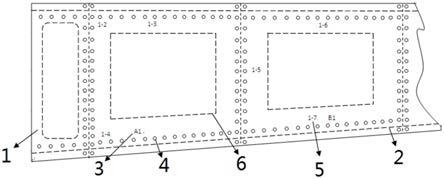
1.本技术属于无损检测超声波测厚技术领域,尤其涉及一种用于机翼盒段件测厚的定位工装。
背景技术:2.复合材料因其诸多优越的性能,在航空航天领域被越来越广泛的使用。很多机型设计制造上都使用大量的复合材料构件,质量合格的复合材料构件,一定是结构稳定的产品,而厚度值是衡量其产品质量的一个极其重要的指标。因此在构件的生产过程中必须要严格地对其厚度进行测量控制,使之达到设计规定的标准范围,以保证产品质量。
3.之前对复合材料件进行厚度检测时采用机械测厚即使用卡尺或千分尺进行测厚,但使用机械测厚时会存在一系列的缺点:受到零件结构和尺寸的限制,当对一个结构比较复杂并且尺寸较大的复合材料件进行机械测厚时,经常会遇到某些复杂区域(如闭合区)的厚度检测不到的问题,并且使用卡尺检测只能对零件开敞区边缘150mm的范围内进行检测,这就使得检测受到了很大的限制。
4.同时,使用机械方法进行测厚读取的数值由于一些人为原因,会导致该数据存在一定的误差,从而影响了检测结果的判定。检测速率也很低,对大的零件进行检测时要花费很多时间。而超声波测厚技术是超声波检测的重要应用之一。超声波测厚技术可以实现从单面对被测工件的厚度进行测量,本发明测厚方法采用超声脉冲回波法来测量被检工件(闭合区)的厚度。
5.机翼盒段作为整个机翼主结构中最重要的框架,其质量安全性对于整个机翼系统结构起着至关重要的作用,从而对于整个飞机的安全使用也具有重要意义。机翼盒段是由前后梁、对接盒段、1~10中段肋及上蒙皮等整体共固化成型复合材料层压件。该构件尺寸较大,长约七八米,宽度0.8米。要求除蜂窝区域外整体测厚,铺层结构复杂多变,厚度变化多,待检测区域数量多、面积大、且分布比较分散,多达二百多个不同的厚度部位,目前针对机翼盒段件采用手动超声脉冲反射法的检测方式进行厚度检测。
6.相对技术为检测人员需要根据零件图纸,先用白色记号笔按照图纸上铺层信息,将各个不同厚度区域边界在零件表面上全部标记出来,然后再结合检测指令上厚度验收值进行比较,逐一判定。这一过程一个检测人员需要几个小时才能检测完一个盒段件。
技术实现要素:7.为解决上述检测过程中遇到的问题,本技术提供了一种用于机翼盒段件测厚的专用定位工装,适用于使用超声脉冲回波法对机翼盒段件各个部位进行厚度检测,提高厚度检测的准确度,并减少人员在检测过程中由于分区失误而造成的错误,保证厚度检测结果的可靠性以及大幅度提高厚度检测效率。
8.本技术提供了一种用于机翼盒段件测厚的定位工装,所述定位工装包括:
9.透明薄膜,用于覆盖在机翼盒段件上;其中,所述透明薄膜的形状与所述机翼盒段
件的外形相同。
10.测厚孔,设置在所述透明薄膜上,用于放置超声测厚仪的检测探头。
11.优选地,所述定位工装还包括:
12.分区线,设置在所述透明薄膜上,用于划分出多个不同厚度的目标区域;其中,所述分区线是基于零件图纸铺层厚度信息标注出来的边界线。
13.优选地,所述目标区域内设置有至少一个测厚孔;其中,所述测厚孔是基于多点测量法扣取的。
14.优选地,所述测厚孔的直径为8mm。
15.优选地,所述透明薄膜的材质是硬质塑料薄膜。
16.优选地,所述定位工装还包括:
17.厚度验收值,设置在所述测厚孔或分区线的附近。
18.本技术具有如下技术效果:
19.本技术采用的透视材质的硬质塑料薄膜,以便于检测过程中观察各个部位的零件表面质量情况,排除可能影响厚度值测量外在干扰因素;同时,定位工装的使用,可准确标记出各个不同厚度区域,区域划分明确,定位准确,大大提高厚度检测的准确度,减少检测人员的劳动强度和检测难度。并最大限度的减少人员由于分区失误而造成的检测错误,保证厚度检测结果的可靠性以及极大幅度提高厚度检测效率;使整个检测过程操作更加方便,简单高效,实际使用效果好。
附图说明
20.图1为本技术实施例提供的机翼盒段件的结构示意图;
21.图2为本技术实施例提供的测厚方法的流程图;
22.图3为本技术实施例提供的一种定位工装的结构示意图;
23.图4为本技术实施例提供的另一种定位工装的结构示意图;
24.其中:1-透明薄膜;2-区域编号;3-分区线;4-测厚孔;5-厚度验收值;6
‑ꢀ
蜂窝区。
具体实施方式
25.下面结合附图1-4与具体实施方式对本技术作进一步详细描述:
26.本技术提出一种用于机翼盒段件测厚的方法和专用定位工装,采用超声脉冲回波法进行超声波测厚,包括以下步骤:
27.先确定被检件需要测厚的部位的全部铺层材料及其理论厚度值,该部位的理论厚度值为每种铺层材料理论厚度与铺层层数乘积之和。
28.制作与被检件材料、固化参数、铺层相同或相近应的对比试片,合格的对比试片应包括三种铺层厚度且无分层、夹杂等影响对比试片厚度检测的缺陷,分别为小于或等于盒段件件最小厚度值对比试片a,中间厚度值对比试片b及大于或等于盒段件最大厚度值对比试片c。
29.在对比试片上选取标记校准点,使用超声测厚仪在对比试片a和对比试片 c的校准点上,确定材料声速,在该声速下对对比试片b的校准点上进行厚度检测,确定出盒段件的声速,并根据此声速对其进行测厚。按超声测厚检测文件规定的30mm多点测量法的要求,
对测量点上逐点进行测量。每个测量点至少测三次,取平均值。对不满足表面要求的测量点,则应在邻近符合要求的位置上进行补充测量。对于厚度测量不显示数值的情况,应对该部位用超声波检测仪检测是否存在分层缺陷。
30.在本技术实施例中,盒段件测厚的专用定位工装包括透明薄膜1,采用的透视材质的硬质塑料薄膜,透明薄膜1尺寸采用与盒段件外表面外形相同的尺寸,分别覆盖于整个盒段件外表面,利用零件边缘定位,与盒段件四个边缘完全重合,并通过胶带固定到零件表面,透视材质以便于检测过程中观察各个部位的零件表面质量情况,如有异常,排除可能影响厚度值测量外在干扰因素。
31.其中,在透明薄膜1上按照零件图纸铺层厚度信息,将所有不同厚度区域边界标识出来,画出分区线3,在透明薄膜1上,按照超声测厚检测文件规定的30mm多点测量法的要求,抠取出测厚孔4,测厚孔4为直径为8mm的圆形孔(略大于探头大小),用于放置检测探头对零件进行测厚,测量点的确定为不同厚度区域内至少有一个测厚孔4,厚度的测量点为距边缘15mm,同一厚度区域每间隔30mm测一点,逐点进行测量。
32.其中,测厚孔4按照铺层厚度信息及30mm多点测量法的要求,分别分散于整个测厚区域的透明薄膜1,在每个相同厚度区域内,在分区线3及测厚孔4 附近,标注出相应的厚度验收值5,用于测量厚度同时,通过各个部位验收值直接进行快速判定,并记录检测结果,所述透明薄膜1上标记出蜂窝区6,不需要进行测厚。
33.需要说明的是,本技术与使用机械测厚方法相比,超声脉冲回波法可以有效的保证对机翼盒段件厚度检测的检测质量,得到的测厚数值更接近真实的数值,人为影响的因素比较少,可在仪器上直接显示出被检部位的厚度值,数字化的显示更加直观。
34.进一步,采用的透视材质的硬质塑料薄膜,以便于检测过程中观察各个部位的零件表面质量情况,排除可能影响厚度值测量外在干扰因素,同时定位工装的使用,可准确标记出各个不同厚度区域,区域划分明确,定位准确,大大提高厚度检测的准确度,减少检测人员的劳动强度和检测难度,并最大限度的减少人员由于分区失误而造成的检测错误,保证厚度检测结果的可靠性以及极大幅度提高厚度检测效率。使整个检测过程操作更加方便,简单高效,实际使用效果好。