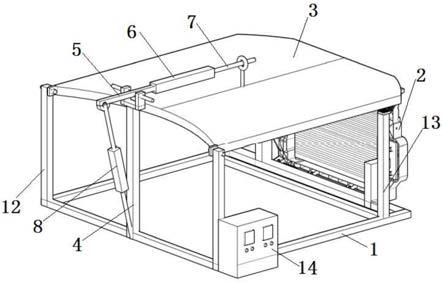
1.本实用新型涉及汽车技术领域,特别是涉及一种汽车前端框架总成疲劳实验设备。
背景技术:2.汽车前端框架总成整体呈矩形框结构设计且通过注塑成型得到。汽车前端框架总成通常通过螺钉呈竖向布置的安装固定在汽车车身前端。汽车前端框架总成上还设有相应的安装结构并用于安装散热器等电器件。
3.汽车前端框架总成作为安装负载构件,需要承各个电器件的重力;并且在操作完成开闭汽车前罩板时,汽车前端框架总成会承受相应的冲击力。这就使得汽车前端框架总成需要具备相应抗疲劳强度以更好的保证在一定次数冲击力内保持完整性。为了能够更好的获得不同塑料材质制得的汽车前端框架总成的抗疲劳强度,需要设计相应的设备模拟完成汽车前端框架总成抗疲劳能力。
4.因此,怎样才能够提供一种结构设计更加简单合理,能够更好的模拟完成汽车前端框架总成抗疲劳能力的汽车前端框架总成疲劳实验设备,成为了本领域技术人员有待解决的技术问题。
技术实现要素:5.有鉴于现有技术的上述缺陷,本实用新型所要解决的技术问题是,怎样提供一种结构设计更加简单合理,能够更好的模拟完成汽车前端框架总成抗疲劳能力的汽车前端框架总成疲劳实验设备。
6.为实现上述目的,本实用新型提供了一种汽车前端框架总成疲劳实验设备,包括架体,其特征在于,架体前端具有竖向的安装工位并用于安装固定待检测汽车前端框架总成,且使得汽车前端框架总成安装在安装工位后呈竖向布置;在架体上方位置且背离安装工位的一侧铰接设置有模拟罩板,在模拟罩板与架体之间设有罩板竖向转动控制结构,罩板竖向转动控制结构具有抓取端并能够与呈水平状态下的模拟罩板上设有的连接端相连,并能够带动模拟罩板竖向旋转至预定位置后,抓取端能够与连接端分离以使得模拟罩板远端朝向安装工位移动并模拟形成罩板冲击力以使得汽车前端框架总成获得冲击。
7.这样,上述的汽车前端框架总成疲劳实验设备在工作时,将待检测汽车前端框架总成安装设置在架体前端的安装工位上,安装工位是呈竖向的,使得汽车前端框架总成安装在安装工位后呈竖向布置。然后,罩板竖向转动控制结构能够带动模拟罩板竖向旋转至预定位置后,抓取端与连接端分离以使得模拟罩板远端朝向安装工位移动并模拟形成罩板冲击力以使得汽车前端框架总成获得冲击,反复的完成对汽车前端框架总成冲击,通过冲击次数得出汽车前端框架总成抗疲劳能力。上述的汽车前端框架总成疲劳实验设备设计简单,通过模拟罩板对汽车前端框架总成的冲击,能够更好的得到汽车前端框架总成抗疲劳能力,并且实验得出的抗疲劳能力具有更好的实用价值,能够更好的为设计制造提供依据。
8.作为优化,所述罩板竖向转动控制结构包括架体后端的竖向向上设置的支撑柱,支撑柱上端向上延伸至模拟罩板上方,在支撑柱上端铰接有水平的支撑杆,支撑杆前端设有水平伸缩机构,水平伸缩机构前端水平设有抓取杆并形成所述抓取端,模拟罩板上具有供抓取杆水平穿过的连接孔以形成所述连接端;且水平伸缩机构能够带动抓取杆水平伸入到连接孔内,在支撑杆后端与架体下端之间还设有倾斜伸缩机构;倾斜伸缩机构带动支撑杆竖向旋转以带动模拟罩板竖向旋转。
9.这样,上述的罩板竖向转动控制结构在工作时,当模拟罩板处于水平状态时,水平伸缩机构带动抓取杆水平伸入到连接孔内,然后,倾斜伸缩机构带动支撑杆竖向旋转以带动模拟罩板竖向旋转至预定高度;最后,水平伸缩机构带动抓取杆从连接孔脱离,模拟罩板失去约束朝向汽车前端框架总成运动并使得汽车前端框架总成获得冲击。
10.作为优化,在模拟罩板上设有竖向的连接柱,连接柱上端连接有连接环,连接环内孔形成所述连接孔。
11.这样, 通过设置连接柱和连接环,连接环内孔形成连接孔,整个结构设计更加简单。
12.作为优化,水平伸缩机构和倾斜伸缩机构均为汽缸。
13.这样,采用汽缸驱动,工作更加稳定可靠。
14.作为优化,在支撑柱上端设有u形结构设计的支撑块,支撑杆通过铰接轴安装设置在支撑块敞口端之间。
15.这样,通过设置支撑块,更加方便支撑杆与支撑柱之间的铰接。
16.作为优化,所述架体包括后端的成对设置的两个立柱,模拟罩板后端两侧各自设有水平向外设置的铰接轴并各自对应的插入到立柱上端具有的铰接孔内。
17.这样,通过设置两个立柱,更加方便模拟罩板与架体之间的铰接连接。
18.作为优化,架体包括前端的成对设置的两个安装柱,两个安装柱之间形成所述安装工位。
19.这样,通过设置两个安装柱,安装柱前侧形成安装工位,更加方便汽车前端框架总成的安装固定。
20.作为优化,在架体的一侧还设置有电控箱。
21.这样,电控箱的布局更加合理。
22.综上所述,上述结构通过设置安装工位更加方便模拟安装汽车前端框架总成,设置模拟罩板,并操作模拟罩板拟形成罩板冲击力以使得汽车前端框架总成获得冲击,能够更好的对汽车前端框架总成进行疲劳实验,并且能够提高实验的准确性和可靠性。
附图说明
23.图1是本实用新型具体实施方式中的结构示意图。
24.图2是图1的主视图。
25.图3是图1的前视图。
具体实施方式
26.下面结合附图和实施例对本实用新型作进一步说明,需注意的是,在本实用新型
的描述中,术语“上”、“下”、“左”、“右”、“内”、“外”等指示的方位或位置关系为基于附图所示的方位或位置关系,仅是为了便于描述本实用新型和简化描述,而不是指示或暗示所指的装置或元件必须具有特定的方位、以特定的方式构造和操作,因此不能理解为对本实用新型的限制。术语“第一”、“第二”、“第三”等仅用于描述目的,而不能理解为指示或暗示相对重要性。
27.如图1至图3所示,一种汽车前端框架总成疲劳实验设备,包括架体1,架体前端具有竖向的安装工位并用于安装固定待检测汽车前端框架总成2,且使得汽车前端框架总成安装在安装工位后呈竖向布置;在架体上方位置且背离安装工位的一侧铰接设置有模拟罩板3,在模拟罩板与架体之间设有罩板竖向转动控制结构,罩板竖向转动控制结构具有抓取端并能够与呈水平状态下的模拟罩板上设有的连接端相连,并能够带动模拟罩板竖向旋转至预定位置后,抓取端能够与连接端分离以使得模拟罩板远端朝向安装工位移动并模拟形成罩板冲击力以使得汽车前端框架总成获得冲击。
28.这样,上述的汽车前端框架总成疲劳实验设备在工作时,将待检测汽车前端框架总成安装设置在架体前端的安装工位上,安装工位是呈竖向的,使得汽车前端框架总成安装在安装工位后呈竖向布置。然后,罩板竖向转动控制结构能够带动模拟罩板竖向旋转至预定位置后,抓取端与连接端分离以使得模拟罩板远端朝向安装工位移动并模拟形成罩板冲击力以使得汽车前端框架总成获得冲击,反复的完成对汽车前端框架总成冲击,通过冲击次数得出汽车前端框架总成抗疲劳能力。上述的汽车前端框架总成疲劳实验设备设计简单,通过模拟罩板对汽车前端框架总成的冲击,能够更好的得到汽车前端框架总成抗疲劳能力,并且实验得出的抗疲劳能力具有更好的实用价值,能够更好的为设计制造提供依据。
29.具体的,模拟罩板的前端下方成对的设有两个橡胶缓冲垫,这样能够更好的模拟前罩板对汽车前端框架总成的冲击。
30.本具体实施方式中,所述罩板竖向转动控制结构包括架体后端的竖向向上设置的支撑柱4,支撑柱上端向上延伸至模拟罩板上方,在支撑柱上端铰接有水平的支撑杆5,支撑杆前端设有水平伸缩机构6,水平伸缩机构前端水平设有抓取杆7并形成所述抓取端,模拟罩板上具有供抓取杆水平穿过的连接孔以形成所述连接端;且水平伸缩机构能够带动抓取杆水平伸入到连接孔内,在支撑杆后端与架体下端之间还设有倾斜伸缩机构8;倾斜伸缩机构带动支撑杆竖向旋转以带动模拟罩板竖向旋转。
31.这样,上述的罩板竖向转动控制结构在工作时,当模拟罩板处于水平状态时,水平伸缩机构带动抓取杆水平伸入到连接孔内,然后,倾斜伸缩机构带动支撑杆竖向旋转以带动模拟罩板竖向旋转至预定高度;最后,水平伸缩机构带动抓取杆从连接孔脱离,模拟罩板失去约束朝向汽车前端框架总成运动并使得汽车前端框架总成获得冲击。
32.本具体实施方式中,在模拟罩板上设有竖向的连接柱9,连接柱上端连接有连接环10,连接环内孔形成所述连接孔。
33.这样, 通过设置连接柱和连接环,连接环内孔形成连接孔,整个结构设计更加简单。
34.本具体实施方式中,水平伸缩机构和倾斜伸缩机构均为汽缸。
35.这样,采用汽缸驱动,工作更加稳定可靠。
36.本具体实施方式中,在支撑柱上端设有u形结构设计的支撑块11,支撑杆通过铰接
轴安装设置在支撑块敞口端之间。
37.这样,通过设置支撑块,更加方便支撑杆与支撑柱之间的铰接。
38.本具体实施方式中,所述架体包括后端的成对设置的两个立柱12,模拟罩板后端两侧各自设有水平向外设置的铰接轴并各自对应的插入到立柱上端具有的铰接孔内。
39.这样,通过设置两个立柱,更加方便模拟罩板与架体之间的铰接连接。
40.本具体实施方式中,架体包括前端的成对设置的两个安装柱13,两个安装柱之间形成所述安装工位。
41.这样,通过设置两个安装柱,安装柱前侧形成安装工位,更加方便汽车前端框架总成的安装固定。
42.本具体实施方式中,在架体的一侧还设置有电控箱14。
43.这样,电控箱的布局更加合理。
44.综上所述,上述结构通过设置安装工位更加方便模拟安装汽车前端框架总成,设置模拟罩板,并操作模拟罩板拟形成罩板冲击力以使得汽车前端框架总成获得冲击,能够更好的对汽车前端框架总成进行疲劳实验,并且能够提高实验的准确性和可靠性。
45.以上详细描述了本实用新型的较佳具体实施例。应当理解,本领域的普通技术人员无需创造性劳动就可以根据本实用新型的构思作出诸多修改和变化。因此,凡本技术领域中技术人员依本实用新型的构思在现有技术的基础上通过逻辑分析、推理或者有限的实验可以得到的技术方案,皆应在由权利要求书所确定的保护范围内。