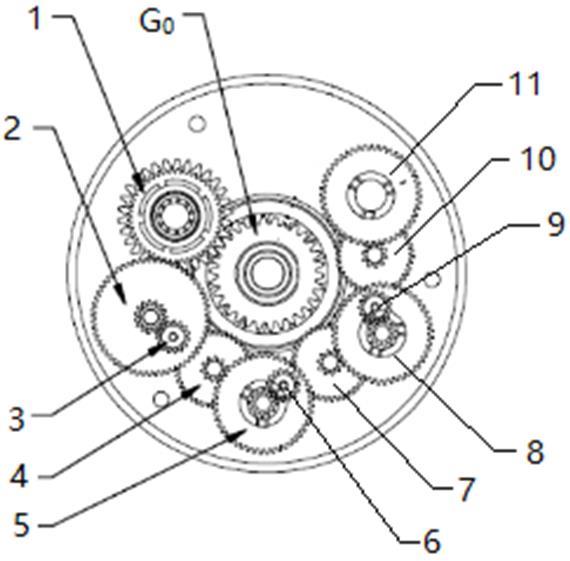
1.本技术涉及磁电领域,具体涉及一种磁电多圈编码装置。
背景技术:2.目前,有许多应用电动机的场合,都需要对电动机的转速进行测量或者对电动机转过的圈数和角度进行测量。当前一般采用光电式编码器对电动机的圈数和角度进行测量,然而光电式编码器由于结构复杂,测量成本高,同时光电式编码器由于自身工作原理,对环境要求较高,这导致光电式编码器的应用受到限制。
技术实现要素:3.针对上述技术问题,本发明实施例提供一种磁电多圈编码装置,能够至少解决上述技术问题之一。
4.本技术采用的技术方案为:本发明实施例提供一种磁电多圈编码装置,包括:壳体、盖板、齿轮传动机构、磁感应装置和数据采集模块;所述盖板用于盖住所述壳体;所述齿轮传动机构设置在所述壳体上,包括啮合连接的主齿轮g0和p个齿轮组g1,g2,
……
,g
p
;其中,所述主齿轮g0通过主轴与电机轴连接,每个齿轮组的齿轮分别通过齿轮轴设置在所述壳体上;在电机轴的转动过程中,通过所述主齿轮带动p个齿轮组的齿轮转动;所述磁感应装置包括p+1个磁柱m0,m1,m2,
……
,m
p
以及对应的p+1个磁芯片c0,c1,c2,
……
,c
p
,其中,磁柱m0设置在主轴上,磁柱m1,m2,
……
,m
p
分别设置在齿轮组g1,g2,
……
,g
p
的最后一个齿轮上并随对应的齿轮转动而转动,p+1个磁芯片设置在所述盖板上,并且每个磁芯片位于对应的磁柱正上方,磁芯片c0,c1,c2,
……
,c
p
的分辨率分别为r0,r1,r2,
……
,r
p
;其中,齿轮组g1和主齿轮g0的最后一个齿轮的传动比为t1,齿轮组gk和齿轮组g
k-1
的最后一个齿轮的传动比为tk,k的取值为2到p;在主齿轮带动齿轮组转动时,每个磁柱产生磁感应信号并由对应的磁芯片接收,所述磁芯片将接收到的磁感应信号转换成编码信号;所述数据采集模块设置在所述盖板上,与p+1个磁芯片连接,用于在每个设定的计算周期内执行如下操作:s100,获取每个磁芯片转换的编码信号;s200,基于当前获取的磁芯片c0的编码信号和分辨率得到电机轴转动的角度;s300,基于当前获取的磁芯片c1,c2,
……
,c
p
的编码信号和分辨率以及传动比得到电机轴转动的圈数;其中,在每个设定的计算周期的初始时刻,电机轴转动的圈数被初始化为0。
5.本技术实施例提供的磁电多圈编码装置,采用齿轮转动带动磁柱产生磁感应信号
以反应电机轴的旋转圈数,通过各级齿轮组之间的传动比来确保编码器的测量精度,与现有的光电式编码器相比,能够降低制造成本和提高环境适用度。
附图说明
6.为了更清楚地说明本技术实施例或相关技术中的技术方案,下面将对实施例或相关技术描述中所需要使用的附图作简单地介绍,显而易见地,下面描述中的附图仅仅是本技术的一些实施例,对于本领域普通技术人员来讲,在不付出创造性劳动性的前提下,还可以根据这些附图获得其他的附图。
7.图1为本技术实施例提供的磁电多圈编码装置的部分主视图;图2为本技术实施例提供的磁电多圈编码装置的部分俯视图。
8.(附图标记说明)1-第一塔轮;2-第二塔轮;3-第一齿轮;4-第三塔轮;5-第四塔轮;6-第二齿轮;7-第五塔轮;8-第六塔轮;9-第三齿轮;10-第七塔轮;11-第八塔轮。
具体实施方式
9.为使本技术要解决的技术问题、技术方案和优点更加清楚,下面将结合本技术实施例中的附图,对本技术实施例中的技术方案进行清楚、完整地描述。
10.图1为本技术实施例提供的磁电多圈编码装置的部分主视图;图2为本技术实施例提供的磁电多圈编码装置的部分俯视图。
11.如图1和图2所示,本技术提供的磁电多圈编码装置,包括:壳体、盖板、齿轮传动机构、磁感应装置和数据采集模块。
12.在本发明实施例中,盖板用于盖住壳体,形成容纳齿轮传动机构、磁感应装置和数据采集模块的容纳空间。
13.其中,所述齿轮传动机构设置在所述壳体上,包括啮合连接的主齿轮g0和p个齿轮组g1,g2,
……
,g
p
,p为大于1的整数。
14.在本发明实施例中,主齿轮g0和p个齿轮组按照设定的啮合关系啮合,输出设定的传动比。如图1所示,主齿轮g0设置在壳体的顶面的中心位置处,通过主轴与测量的电动机的输出端即电机轴连接。各齿轮组通过对应的齿轮轴设置在主齿轮g0的周围,并被布置为能够随主齿轮的转动而转动。每个齿轮轴固定在壳体上,每个齿轮组的齿轮可转动地设置在对应的齿轮轴上,具体地,每个齿轮组的齿轮可通过中心孔可转动地设置在对应的齿轮轴上。
15.在本发明实施例中,齿轮组g1和主齿轮g0的最后一个齿轮的传动比为t1,齿轮组gk和齿轮组g
k-1
的最后一个齿轮的传动比为tk,k的取值为2到p。也就是说,主齿轮g0转动1圈即转动360
°
,齿轮组g1的最后一个齿轮转动1/t1圈;齿轮组gk中的最后一个齿轮转过1圈,g
k-1
中的最后一个齿轮转1/tk圈。
16.进一步地,在本发明实施例中,所述磁感应装置可包括p+1个磁柱m0,m1,m2,
……
,m
p
以及对应的p+1个磁芯片c0,c1,c2,
……
,c
p
,其中,磁柱m0设置在主轴上,磁柱m1,m2,
……
,m
p
分别设置在齿轮组g1,g2,
……
,g
p
的最后一个齿轮上并随着对应的齿轮转动而转动,p+1个磁芯片设置在所述盖板上,并且每个磁芯片位于对应的磁柱上方,磁芯片c0,c1,c2,
……
,cp
的分辨率分别为r0,r1,r2,
……
,r
p
。在本发明实施例中,磁芯片的分辨率是指可以将齿轮旋转一圈分为多少个位置,例如,分辨率为12,则表示在齿轮旋转一圈时,可以得到12个位置。
17.在一个具体实施例中,磁柱m0可通过例如粘接的方式设置在主轴上。每个齿轮组的最后一个齿轮上向上突出形成有固定部。在一个示意性实施例中,固定部可沿对应的齿轮的中心孔的周向方向向上延伸形成,形成有供磁柱插入的固定孔。磁柱m1,m2,
……
,m
p
中的每个磁柱可插入设置在对应的固定孔中。在一个示意性实施例中,固定孔的直径可设置为使得磁柱插入之后不产生晃动,即能够使得磁柱能够与齿轮稳靠连接。在另一个示意性实施例中,固定孔的直径可被设置为略大于磁柱的直径,在磁柱插入到对应的固定孔后,可通过粘接剂等将磁柱粘接在对应的齿轮上。为使得磁柱能够更好的与齿轮相连接,可在固定部上设置多个缺口,缺口用于涂抹粘接剂。优选,可设置沿固定部的圆周方向均匀分布的三个缺口。
18.在本发明实施例中,在主齿轮带动齿轮组转动时,每个磁柱产生磁感应信号并由对应的磁芯片接收,所述磁芯片将接收到的磁感应信号转换成编码信号。在本发明实施例中,磁柱和磁芯片可为现有产品。编码信号为二进制编码信号,将接收到的磁感应信号转换成二进制编码信号的方式属于现有技术。
19.其中,与设置在主轴上的磁柱m0对应的磁芯片c0的分辨率r0可为磁芯片c0自身的分辨率,在一个示意性实施例中,r0=2
12
=4096,即主齿轮g0旋转一圈,磁芯片c0可输出4096个编码信号。
20.在本发明一示意性实施例中,磁芯片c1,c2,
……
,c
p
的分辨率r1,r2,
……
,r
p
可分别与传动比t1,t2,
……
,t
p
不相同,各磁芯片的分辨率可自定义设置例如根据用户需求设置。
21.在本发明另一示意性实施例中,磁芯片c1,c2,
……
,c
p
的分辨率r1,r2,
……
,r
p
可分别与传动比t1,t2,
……
,t
p
相同,即分辨率r1可等于对应的传动比t1,分辨率r
k+1
可等于对应的传动比t
k+1
,即与设置在每个齿轮组的最后一个齿轮上的磁柱对应的磁芯片的分辨率与对应的齿轮组实现的传动比相等。
22.在本发明实施例中,每个磁柱和对应的磁芯片之间的间隔被设置成满足磁芯片能够正常工作的距离。
23.进一步地,在本发明实施例中,所述数据采集模块可设置在所述盖板上并与p+1个磁芯片连接,用于在每个设定的计算周期内执行如下操作:s100,获取每个磁芯片转换的编码信号;s200,基于当前获取的磁芯片c0的编码信号和分辨率得到电机轴转动的角度;s300,基于当前获取的磁芯片c1,c2,
……
,c
p
的编码信号和分辨率以及传动比得到电机轴转动的圈数;其中,在每个设定的计算周期的初始时刻,电机轴转动的圈数被初始化为0,即在每个计算周期,对电机轴的圈数重新进行计数。在本发明实施例中,初始时刻是指基于接收到的编号信号确定的各个齿轮的位置都为初始位置的时刻。初始位置可为自定义位置。
24.在本发明实施例中,设定的计算周期可为,其中,n为电机轴的转速。也
就是说,本发明实施例中,可记录的电机轴的转动圈数最大为。
25.在一具体应用中,可在最后一个齿轮组即g
p
的最后一个齿轮转动一圈时自动进入下一个计算周期。具体地,本发明实施例提供的装置还可包括计数器c,数据采集模块还用于执行如下操作:s10,在当前计算周期的初始时刻,将计数器c的初始化为0。
26.即,在每个计算周期的初始时刻,c=0。
27.s20,在基于接收到c
p
发送的编号信号确定g
p
的最后一个齿轮再一次位于初始位置时,设置c=1,并结束当前计算程序。
28.进一步地,电机轴转动的角度a=(l0/r0)*360
°
,其中,l0为基于磁芯片c0的编码信号确定的主齿轮g0相对于初始位置的位置。基于磁芯片c0的编码信号确定的主齿轮g0相对于初始位置的位置可为现有技术,例如,如果磁芯片r0=2
12
,可采用12位二进制表示位置,例如,编码信号为000000000000表示初始位置(0位置),000000000001表示第1位置等。
29.在本发明实施例中,主齿轮g0转动的圈数即电机轴转动的圈数n可通过每个齿轮组的最后一个齿轮记录的圈数来确定,具体地,n=[l2/r2*t2]*t1+[l3/r3*t3]*t2*t1+
…
+[lp/r
p
*t
p
]*t
p-1
*
…
*t1, l1、l2、
…
、lp分别表示基于磁芯片c1、c2、
…
、cp的编码信号确定的对应的齿轮组的最后一个齿轮相对于初始位置的位置,例如,lj表示基于磁芯片cj的编码信号确定的齿轮组gj的最后一个齿轮相对于初始位置的位置,j的取值为1到p,符号[ ]表示取整的意思。同理,基于磁芯片c1的编码信号确定的齿轮组g1的最后一个齿轮相对于初始位置的位置以及基于磁芯片ci的编码信号确定的齿轮组gi的最后一个齿轮相对于初始位置的位置可为现有技术。
[0030]
本发明实施例中,通过取整后的多级齿轮的转动圈数来获得主齿轮的转动圈数,从而能够使得获取的电机轴的转动圈数更加准确。
[0031]
进一步地,在本发明实施例中,所述数据采集模块还与远程控制端连接,用于将得到的电机轴转动的角度和圈数发送给所述远程控制端。数据采集模块可通过spi协议将得到的电机轴转动的角度和圈数发送给所述远程控制端。
[0032]
在本发明实施例中,盖板上可设置有电路板,数据采集模块可为mcu。磁芯片和mcu可固定在电路板上。
[0033]
在本发明一示意性实施例中,p=3。进一步地,t1=t2=t3。优选地,t1=t2=t3=16。在该实施例中,g3的最后一个齿轮转1圈,则主齿轮转4096圈,即本发明实施例的装置记录的电机轴的转动圈数最大为4096圈。
[0034]
在一个具体实施例中,设定磁芯片c1,c2,c3的分辨率都为64,如果在某个时刻基于磁芯片c1,c2,c3的编码信号分别得到的g1,g2和g3的位置为35,6和8,则当前时刻对应的电机轴的转动圈数n=[35/64*16]+ [6/64*16]*16+[8/64*16]*16*16= 8+16+512=536。
[0035]
在本发明实施例中,每个齿轮的齿数、模数和传动比可基于t1、t2、
…
、t
k+1
以及壳体的面积s确定。具体地,可基于如下步骤确定:步骤一、基于t1、t2、
…
、t
k+1
,得到主齿轮和各齿轮组中的各个齿轮的m个齿数、模数和传动比;步骤二、基于壳体的面积s,从得到的主齿轮和各齿轮组中的各个齿轮的m个齿数、
模数和传动比选择最优的齿数、模数和传动比。这样,由于基于壳体的面积来确定齿轮的参数,能够使得壳体的尺寸可以尽可能的小。
[0036]
在一个示意性实施例中,齿轮组g1包括第一塔轮1、第二塔轮2、第一齿轮3、第三塔轮4和第四塔轮5;齿轮组g2包括第二齿轮6、第五塔轮7和第六塔轮8;齿轮组g3包括第三齿轮9、第七塔轮10和第八塔轮11。其中,第四塔轮5、第六塔轮8和第八塔轮11上设置有磁柱。每个塔轮包括同轴旋转的输入齿轮和输出齿轮。其中,第一塔轮1的输入齿轮与主齿轮啮合,第一塔轮1的输出齿轮与第二塔轮2的输入齿轮啮合,第二塔轮2的输出齿轮通过第一齿轮3与第三塔轮4的输入齿轮连接,即第一齿轮3分别与第二塔轮2的输出齿轮和第三塔轮4的输入齿轮啮合,第三塔轮4的输出齿轮与第四塔轮5的输入齿轮啮合,第四塔轮5的输出齿轮通过第二齿轮6与第五齿轮7的输入齿轮连接,即第二齿轮6分别与第四塔轮5的输出齿轮和第五塔轮7的输入齿轮啮合,第五塔轮7的输出齿轮与第六塔轮8的输入齿轮啮合,第六齿轮8的输出齿轮通过第三齿轮9与第七齿轮10的输入齿轮连接,即第三齿轮9分别与第六塔轮8的输出齿轮和第七塔轮10的输入齿轮啮合,第七塔轮10的输出齿轮与第八塔轮11啮合。其中,第一塔轮1的输入齿轮的直径大于第一塔轮1的输出齿轮的直径,第二塔轮2、第三塔轮4、第五塔轮7、第六塔轮8和第七塔轮10的输入齿轮的直径均大于对应的输出齿轮的直径。
[0037]
在一个具体实施例中,在壳体的直径为46.80mm需满足t1=t2=t3=16的情况下,得到的各齿轮的参数为:(1)主齿轮的齿数为30,第一塔轮1的输入齿轮的齿数为30,第一塔轮1的输出齿轮的齿数为48,第二塔轮2的输入齿轮的齿数为60,第二塔轮2的输出齿轮的齿数为15,第一齿轮3、第二齿6和第三齿轮9的齿数均为15,第三塔轮4、第五塔轮7和第七塔轮10的输入齿轮的齿数为40,输出齿轮的齿数为10,第四塔轮5、第六塔轮8和第八塔轮11的输入齿轮的齿数为48,输出齿轮的齿数为12。
[0038]
(2)主齿轮的分度圆直径为13.5mm,第一塔轮1的输入齿轮的分度圆直径为13.5 mm,第一塔轮1的输出齿轮的分度圆直径为11.52mm,第二塔轮2的输入齿轮的分度圆直径为14.4mm,第二塔轮2的输出齿轮的分度圆直径为3.6mm,第一齿轮3、第二齿6和第三齿轮9的分度圆直径为均为3.6mm,第三塔轮4、第五塔轮7和第七塔轮10的输入齿轮的分度圆直径为9.6mm,输出齿轮的分度圆直径为2.6mm,第四塔轮5、第六塔轮8和第八塔轮11的输入齿轮的分度圆直径为12.48mm,输出齿轮的分度圆直径为2.88mm。
[0039]
(3)主齿轮和第一塔轮的输入齿轮之间的传动比为1:1;第一塔轮的输出齿轮和第二塔轮的输入齿轮之间的传动比为4:5,第二塔轮的输出齿轮和第一齿轮之间的传动比为1:1,第一齿轮和第三塔轮的输入齿轮之间的传动比为3:8,第三塔轮的输出齿轮和第四塔轮的输入齿轮之间的传动比为5:24,第四塔轮的输出齿轮和第二齿轮之间的传动比为4:5,第二齿轮和第五塔轮的输入齿轮之间的传动比为3:8,第五塔轮的输出齿轮和第六塔轮的输入齿轮之间的传动比为5:24,第六塔轮的输出齿轮和第三齿轮之间的传动比为4:5,第三齿轮和第七塔轮的输入齿轮之间的传动比为3:8,第七塔轮的输出齿轮和第八塔轮的输入齿轮之间的传动比为5:24。
[0040]
虽然已经通过示例对本技术的一些特定实施例进行了详细说明,但是本领域的技术人员应该理解,以上示例仅是为了进行说明,而不是为了限制本技术的范围。本领域的技术人员还应理解,可以对实施例进行多种修改而不脱离本技术的范围和精神。本技术公开
的范围由所附权利要求来限定。