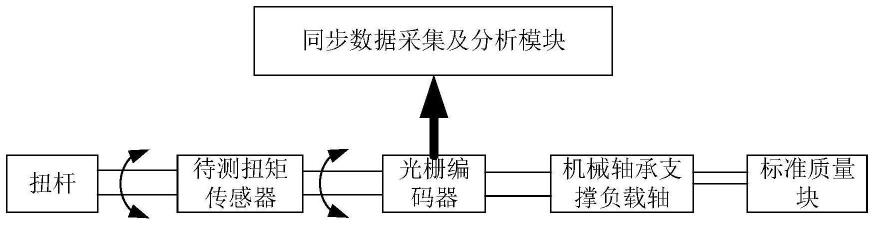
1.本发明属于计量测试领域,特别是涉及一种扭杆驱动的动态扭矩校准装置。
背景技术:2.现今的扭矩校准多为静态校准,存在没有统一的动态校准规范、准确度不高等问题,无法满足各工业领域的扭矩计量需求。除此之外,许多测试系统实际工作状态多为动态加载形式,包括典型的正弦、梯形、锯齿等方式加载,这就需要明确扭矩传感器的动态特性,保证其工作的可靠性。针对上述问题,开展动态扭矩量值溯源技术研究非常必要。
技术实现要素:3.有鉴于此,本发明旨在提出一种扭杆驱动的动态扭矩校准装置,以解决现有的动态扭矩校准无法满足各工业领域的扭矩计量需求的问题。
4.为实现上述目的,本发明采用以下技术方案:一种扭杆驱动的动态扭矩校准装置,所述动态扭矩校准装置设置在底座上,所述底座为l形结构,包括底板和侧壁,底板和侧壁垂直设置,所述动态扭矩校准装置采用卧式布置结构,包括扭杆、待测扭矩传感器、光栅编码器、机械轴承支撑负载轴和标准质量模块,所述待测扭矩传感器包括转子部分和定子部分,所述转子部分和定子部分依靠无线通讯相连,所述扭杆一端安装在底座的侧壁上,另一端与待测扭矩传感器的转子部分一端相连,所述待测扭矩传感器的转子部分另一端与光栅编码器、机械轴承支撑负载轴和标准质量模块依次相连,所述待测扭矩传感器的定子部分与底座的底板相连。
5.更进一步的,所述光栅编码器与同步数据采集及分析模块通讯连接。
6.更进一步的,所述机械轴承支撑负载轴通过机械轴承进行支撑,所述机械轴承与底座的底板相连。
7.更进一步的,所述标准质量模块为圆盘形结构。
8.更进一步的,所述标准质量模块上均布有安装孔,通过安装孔在标准质量模块上均匀设置标准配重。
9.更进一步的,所述扭杆通过扭杆连接件与待测扭矩传感器的转子部分相连。
10.更进一步的,所述扭杆连接件与待测扭矩传感器的转子部分相连之间设置有第一联轴器。
11.更进一步的,所述待测扭矩传感器的转子部分通过第二联轴器与光栅编码器相连。
12.更进一步的,所述扭杆与扭杆连接件、第一联轴器、待测扭矩传感器的转子部分、第二联轴器、光栅编码器、机械轴承支撑负载轴和标准质量模块依次通过高强度螺丝固定锁紧形成旋转轴系。
13.与现有技术相比,本发明的有益效果是:本发明通过研究动态扭矩量值溯源方法,研制出一套大扭矩高精度的通过扭杆驱动的动态扭矩校准装置,实现扭矩传感器的精确动
态校准,提高装备保障能力,增强我国在该领域方面的技术基础支撑与工作保障能力。
14.本发明可实现日常所有量程的扭矩传感器的动态校准,尤其是可以实现 10000nm以上的超大型扭矩传感器的动态校准;还可以通过调整扭杆与标准质量模块,可以实现多频率的动态扭矩校准。而且,相对现有技术,本发明还有结构简单,操作方便、控制鲁棒性好以及实验成本低等优点。
15.与电机驱动的动态扭矩校准系统相比,本发明的驱动部件采用扭杆。因此,由电机带来的机械与控制误差都可以避免,同时,减少了测量数据后期分析的复杂性。
16.本方法所述动态扭矩校准装置只需一次安装,即可以同时测量轴系的转动惯量和动态扭矩。系统的转动惯量可以在线测量得到,而不需要像电机驱动的校准系统一样,还要单独离线测量。减少了因轴系多次拆装而引起的安装误差。
17.通过本发明测转动惯量时,被校扭矩传感器也同时安装在轴系中,因此所测转动惯量反应了轴系的真实转动惯量。而其他离线测量转动惯量的动态扭矩校准系统中,被校扭矩传感器一般不参与轴系转动惯量测量,这样进行动态扭矩校准时,就会产生由被校扭矩传感器自身转动惯量引起的扭矩误差。
18.本发明是根据被校扭矩传感器的量程来选取不同弹性刚度的扭杆和不同转动惯量的标准质量模块,而且,系统自由摆动的初始扭转角也是预先设定好的。这些参数一旦设定之后,实验中的轴系扭矩幅值就一定不会超过被校扭矩传感器的极限值。即使在发生故障情况下,也不会使扭矩幅值变得更大,这是由自由扭摆的基本理论决定的。而电机驱动的动态扭矩校准装置为了节约成本,一般只安装一台激励电机,通过控制电机输出扭矩来实现不同幅值的标准扭矩的加载,那么一旦电机出现故障,极有可能输出最大扭矩,被校扭矩传感器也就存在了被损坏的风险。这种情况在本发明中是不存在的。
19.为了方便测试,本发明特制了标准质量模块,此标准质量模块上均匀分布的安装孔可以用来增加其他小的标准质量模块,从而改变整个轴系的转动惯量,进而改变动态扭矩校准的量程,却不需要拆装轴系中的大标准质量模块。这样就减少了由于安装误差,同时也节省了测试时间。
20.现有的通过电机驱动的动态扭矩校准系统实现大量程动态扭矩校准的前提是需要安装驱动能力比扭矩校准量程还有大的驱动电机。这样,现有电机的驱动能力和制造成本就制约了动态扭矩校准的量程。导致现有的电机驱动的动态扭矩校准量程值最大只有1000n
·
m,而本发明因为不需要电机驱动,也就不会受其制约。本发明的扭矩量程只与扭杆的弹性刚度、转动惯量模块和扭转初始角度有关。这些条件都是较容易实现的。通过扭矩计算公式不难算出,弹性刚度、转动惯量模块和扭转初始角度不需要很大,就可以实现1000n
·
m以上扭矩加载和校准,也很容易实现10000n
·
m以上,甚至能实现目前最高量程——兆牛
·
米的扭矩传感器的动态校准。
附图说明
21.构成本发明的一部分的附图用来提供对本发明的进一步理解,本发明的示意性实施例及其说明用于解释本发明,并不构成对本发明的不当限定。在附图中:
22.图1为本发明所述的一种扭杆驱动的动态扭矩校准装置原理框图;
23.图2为本发明所述的一种扭杆驱动的动态扭矩校准装置结构示意图;
24.图3为本发明所述的标准质量模块主视结构示意图;
25.图4为本发明所述的标准质量模块侧视结构示意图。
26.1-扭杆,2-扭杆连接件,3-第一联轴器,4-待测扭矩传感器,5-第二联轴器, 6-光栅编码器,7-机械轴承支撑负载轴,8-标准质量模块,9-底座。
具体实施方式
27.下面将结合本发明实施例中的附图,对本发明实施例中的技术方案进行清楚、完整地阐述。需要说明的是,在不冲突的情况下,本发明中的实施例及实施例中的特征可以相互组合,所描述的实施例仅仅是本发明一部分实施例,而不是全部的实施例。
28.参见图1-4说明本实施方式,一种扭杆驱动的动态扭矩校准装置,所述动态扭矩校准装置设置在底座9上,所述底座9为l形结构,包括底板和侧壁,底板和侧壁垂直设置,所述动态扭矩校准装置采用卧式布置结构,包括扭杆1、待测扭矩传感器4、光栅编码器6、机械轴承支撑负载轴7和标准质量模块8,所述待测扭矩传感器4包括转子部分和定子部分,所述转子部分和定子部分依靠无线通讯相连,所述扭杆1一端安装在底座9的侧壁上,另一端与待测扭矩传感器4的转子部分一端相连,所述待测扭矩传感器4的转子部分另一端与光栅编码器6、机械轴承支撑负载轴7和标准质量模块8依次相连,所述待测扭矩传感器4的定子部分与底座9的底板相连。
29.光栅编码器6与同步数据采集及分析模块通讯连接。所述机械轴承支撑负载轴7通过机械轴承进行支撑,所述机械轴承与底座9的底板相连。所述标准质量模块8为圆盘形结构,如图3和4所示,所述标准质量模块8上均布有安装孔,通过安装孔在标准质量模块8上均匀设置标准配重。在标准质量模块8 上均匀的增加标准配重,可以方便的改变整个扭摆轴系的转动惯量,而不需要拆装整个轴系,节省了校准时间以及避免了在拆装标准质量模块8过程中带来的误差。
30.所述扭杆1通过扭杆连接件2与待测扭矩传感器4的转子部分相连,所述扭杆连接件2与待测扭矩传感器4的转子部分相连之间设置有第一联轴器3,所述待测扭矩传感器4的转子部分通过第二联轴器5与光栅编码器6相连,所述扭杆1与扭杆连接件2、第一联轴器3、待测扭矩传感器4的转子部分、第二联轴器5、光栅编码器6、机械轴承支撑负载轴7和标准质量模块8依次通过高强度螺丝固定锁紧形成旋转轴系。
31.校准待测扭矩传感器4的动态特性时,调整安装在待测扭矩传感器4外侧的标准质量模块,作为转动惯量已知量;转动标准质量模块8到达设定角度,瞬时释放。由于扭杆1的左端固定在底座9上,因此整个旋转轴系在标准质量模块8带动下自由扭摆。
32.自由扭摆过程中,旋转轴系被待测扭矩传感器4的转子部分分割成两部分,待测扭矩传感器4的转子部分左侧为激励部分,包括扭杆1、扭杆连接件2、第一联轴器3和待测待测扭矩传感器4;待测扭矩传感器4的转子部分右侧为负载部分,包括第二联轴器5、光栅编码器6、机械轴承支撑负载轴7和标准质量模块8等部件。
33.除标准质量模块8以外的负载部分的转动惯量通过扭摆法来获得;标准质量模块8的质量和尺寸为预先计算加工而成,转动惯量为已知量。轴系旋转时,通过光栅编码器6同步测量整体轴系运动的角度,获得角度数据。
34.动态扭矩计算公式为:
[0035][0036]
式中,t(t)动态扭矩校准系统实时动态扭矩,k为扭杆弹性系数,为轴系实时动态扭转角度。
[0037]
计算获得动态扭矩值后,用其与待校扭矩传感器的测量值比较,实现扭矩的动态校准。
[0038]
具体的校准方法包括以下步骤:
[0039]
步骤1:根据待测扭矩传感器4的量程选取相应的扭杆1与标准质量模块8;
[0040]
步骤2:将待测扭矩传感器4与对应的扭杆1安装在动态扭矩校准系统中,组成扭摆轴系;
[0041]
步骤3:将扭摆轴系的一端固定,在另一端依次安装三个不同转动惯量的标准质量模块8,进行三次扭摆实验;
[0042]
步骤4:每次实验时,首先根据待测扭矩传感器4的量程,在扭摆轴系的一端施加相应的扭矩,使得扭摆轴系扭转一定的角度,然后瞬间释放扭矩,扭转轴系进行自由摆动;
[0043]
步骤5:测量扭摆轴系自由摆动时的角度,记录每次测量的角度数据;
[0044]
步骤6:根据三次测量得到的角度数据,计算除标准质量模块8以外扭摆轴系的转动惯量、实际轴系总弹性系数和阻尼比;
[0045]
步骤7:计算扭摆轴系的动态扭矩,并用计算扭摆轴系的动态扭矩与待测扭矩传感器4的测量值比较,实现扭矩的动态校准。
[0046]
所述步骤1中,根据不同量程的待测扭矩传感器4选取相应的扭杆1与标准质量模块8的计算公式为:
[0047][0048]
式中,t0为初始外加扭矩值,j为轴系总转动惯量,为初始角加速度,k 为扭杆弹性系数,为轴系初始扭转角度。
[0049]
所述步骤2中更换不同弹性系数的扭杆1,从而改变扭矩校准时的校准频率。
[0050]
所述步骤3中,通过更换不同的标准质量模块8改变扭矩校准时的校准频率,扭摆轴系的固有角频率计算公式为:
[0051][0052]
式中,ωn为扭摆轴系自由摆动时的固有角频率。
[0053]
所述步骤4中,应用可以瞬间释放的液压推力器在扭摆轴系的一端施加相应的扭矩,使得扭摆轴系扭转一定的角度。
[0054]
所述步骤6中实际轴系总弹性系数包括扭杆1的弹性系数、待测扭矩传感器4的弹性系数以及扭摆轴系其他部分的弹性系数。
[0055]
所述步骤6中,扭摆轴系中存在阻尼因素,扭摆轴系转动惯量计算公式为:
[0056][0057]
式中,j为扭摆轴系总转动惯量,j0为扭摆轴系除标准质量模块8以外的转动惯量,ji为第i次实验时的标准质量模块8的转动惯量,k为扭杆1的弹性系数,ζ为扭摆轴系阻尼
比,τi为第i次实验时的扭摆周期。
[0058]
本实施例的动态校准范围如表1所示。
[0059]
扭矩波形幅值范围频率范围衰减谐波0.01-1000000nm0-100hz
[0060]
表1
[0061]
以上公开的本发明实施例只是用于帮助阐述本发明。实施例并没有详尽叙述所有的细节,也不限制该发明仅为所述的具体实施方式。根据本说明书的内容,可作很多的修改和变化。本说明书选取并具体描述这些实施例,是为了更好地解释本发明的原理和实际应用,从而使所属技术领域技术人员能很好地理解和利用本发明。