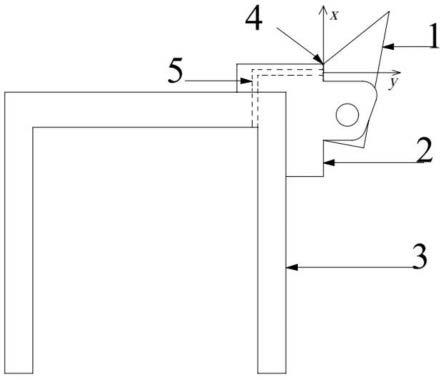
1.本发明涉及隧道掘进机检测,特别是一种全断面隧道掘进机刮刀磨损检测方法。
背景技术:2.全断面隧道掘进机目前普遍应用于各大隧道施工工程中。在泥水混合和江海隧道施工中,全断面隧道掘进机的刮刀磨损是影响施工过程的重要因素。在盾构施工过程中,刮刀的损耗在整个施工阶段耗资占比较大,且刮刀的检查、维修及刮刀更换都十分复杂,单凭工人靠经验判断刮刀的磨损并开仓换刀,常因判断不准出现两种情况:一是刮刀尚未磨损至极限就提前换刀,造成浪费;二是刮刀磨损超过极限而未及时换刀,影响整个施工效果。因此,刮刀磨损检测的精准对于节约施工成本和提高施工效率具有重要意义。全断面隧道掘进机刀盘向前推进时,刀具以刀盘旋转对开挖面产生沿隧道前进方向的进给力(轴向力)和刀盘前进方向的切削力实现对开挖面岩土的切削。掘进机靠刀盘的转动实现岩土切削与分离,在刀盘推力的作用下,刮刀切入岩土实现对切削厚度的改变。当岩土受到的剪切力到达应力极限时发生剪切变形、破碎,形成土屑脱离开挖面,实现隧道的开挖。
3.刮刀磨损目前有多种检测方法,包括液压回路检测法、异味惰性气体检测法、超声波磨损检测法和参数分析法等。其中参数分析法以cn1818640a号专利申请文件公开的一种隧道掘进机掘进过程中刀具磨损的检测方法为例,该方法通过采集掘进机的掘进速度、总推力、刀盘总扭矩、刀盘转速等技术参数,分析计算出掘进速度或刀盘总扭矩的理论值,通过计算该理论值与实测值间的偏差值来判断刀具的磨损状况。该参数分析法在实际应用中发现有如下缺陷:采集参数数量较多,容易造成误差累计,导致判断刀具的磨损值不够准确;利用掘进速度或者刀盘总扭矩的理论值间接判断刀具的磨损,在复杂的全断面隧道施工环境中易造成数值偏差,导致判断错误。
技术实现要素:4.为克服上述掘进机掘进过程中刀具磨损检测参数分析法的缺陷,本发明提供一种全断面隧道掘进机刮刀磨损检测方法。
5.该刮刀磨损检测方法包括以下步骤:
6.步骤1
7.安装刮刀,并在每个刮刀与刀座之间安装压力传感器,压力传感器安装在刮刀与刀座接触面的前端部中心位置;压力传感器的引线通过无线传输装置与设在中央控制室中的报警装置相接,对刀盘上不同位置的刮刀的报警装置进行编号;
8.步骤2
9.以压力传感器的压力采集中心点为原点,以垂直于刮刀与刀座的接触面的直线为y轴,以与刮刀后端面侧边平行的直线为x轴建立直角坐标系和受力分析图(受力分析图根据吉林大学崔国华等《全断面隧道掘进机切削刀具的计算力学模型求解》绘制);由受力分析图分别测得刮刀切削力f
t
与y轴的夹角θ1和刮刀轴向力fn与y轴的夹角θ2;
10.步骤3
11.按以下方法分别计算刮刀在未磨损的初始状态与刀座间的作用力f1和刮刀磨损至极限位置与刀座间的作用力f2的理论值:
12.f1的计算方法:
13.按以下计算公式分别求得刮刀在未磨损的初始状态刮刀切削力f
t1
和刮刀轴向力f
n1
的具体值
[0014][0015][0016]
式中:
[0017]
α为刮刀的切削角,
[0018]
为土体内摩擦角,
[0019]
ph为朗肯被动土压力,具体值通过下式计算得出:
[0020]
非粘性土(隧道地质条件为非粘土性质):
[0021][0022]
粘性土(隧道地质条件为粘土性质):
[0023][0024]
式中:
[0025]
h为刮刀贯入度,λ为土体容量,c为土体内聚力,h为地表面到盾构中轴的深度,d为刮刀宽度,k
p
为被动土压力系数,k0为侧向土压力系数,α为刮刀的切削角,为土体内摩擦角,
[0026]
pf为土体对刮刀前刃面的摩擦阻力,pf=μp
h sinα,μ为岩土与钢的摩擦系数,
[0027]
p
τ
为刮刀侧面土体抗剪阻力,具体值通过下式计算得出:
[0028]
非粘性土:
[0029]
粘性土:
[0030]
进而求得刮刀在未磨损的初始状态f
t1
和f
n1
在y轴的合力
[0031]fy1
=|f
t1
cosθ
1-f
n1 cosθ2|
[0032]
将f
y1
设定为刮刀在未磨损的初始状态与刀座间的作用力f1;
[0033]
f2的计算方法:
[0034]
按以下计算公式分别求得刮刀磨损至极限位置刮刀切削力f
t2
和轴向力f
n2
的具体值
[0035][0036][0037]
式中:
[0038]
α为刮刀的切削角,
[0039]
为土体内摩擦角,
[0040]
δ为刮刀的后角,
[0041]
γ为为刮刀的前角,
[0042]
pz为在刀刃面上土体对刮刀的阻力,pz=p0ad,p0为磨损后刀刃处的切削阻力(一般取土体的无侧限抗压强度),d为刮刀宽度,a为刮刀磨损至极限时刀刃宽度(刮刀刀刃磨损后变为一半径为r的圆弧,近似的a=r)
[0043]
ph为朗肯被动土压力,具体值通过下式计算得出:
[0044]
非粘性土:
[0045][0046]
粘性土:
[0047][0048]
式中:h为刮刀贯入度;λ为土体容量;c为土体内聚力;h为地表面到盾构中轴的深度;d为刮刀宽度;k
p
为被动土压力系数,k0为侧向土压力系数;α为刮刀的切削角;为土体内摩擦角,
[0049]
p
τ
为刮刀侧面土体抗剪阻力,具体值通过下式计算得出:
[0050]
非粘性土:
[0051][0052]
粘性土:
[0053][0054]
pf为土体对刮刀前刃面的摩擦阻力,pf=μphsinα,μ为岩土与钢的摩擦系数,
[0055]
进而求得刮刀磨损至极限位置切削力f
t2
和轴向力f
n2
在y轴的合力
[0056]fy2
=|f
t2 cosθ
1-f
n2 cosθ2|
[0057]
将f
y2
设定为刮刀磨损至极限与刀盘的作用力f2;
[0058]
步骤4
[0059]
在全断面隧道掘进机运行过程中,通过压力传感器不间断地采集刮刀与刀座间的作用力fn,,为确保压力采集的精确,避免由压力单一值的突变(突然变大或突然变小,甚至
为零)对压力检测结果的影响,采取每间隔1s采集一次压力传感器的压力信息,从刮刀开始运行第一秒开始采集,依次获取100次数据设为第一组,并计算第一组数据的平均值f
n1
,作为压力判断值;第二组数据从刮刀开始运行第二秒开始采集,依相同方式获取100次数据,将该组数据设为第二组,并计算第二组数据的平均值fn2
……
,依次类推获取n组数据,当平均值
[0060][0061]
不在f1~f2数值范围内时,判定刮刀磨损达到极限,通过中央控制室中的报警装置报警判断磨损到极限、需要更换的刮刀位置。
[0062]
作为优选,所述压力传感器为薄膜压力传感器。
[0063]
本发明中所述刮刀在未磨损的初始状态与刀座间的作用力f1和刮刀磨损至极限位置时与刀座间的作用力f2理论值的计算公式是基于以下原理得出的:
[0064]
依据《土力学地基基础》并根据吉林大学学报(工学版)2008年9月第38卷(增刊2)登载的崔国华等《全断面隧道掘进机切削刀具的计算力学模型求解》可知,刮刀切削进入岩土后,岩土基体受到剪切破坏,刮刀与岩土接触时其主要受到的力包括朗肯被动土压力ph(在切削软土地层时,ph还包含粘聚力pb)、摩擦阻力pf、刀具侧面土体抗剪阻力p
τ
,刮刀切削土体后,其作用力主要作用在刮刀的前刃面,在全断面隧道掘进机刮刀工作过程中,刮刀的切削速度较慢,切削的土体体积较小,流动速度较慢,因此,在计算时可忽略土体重力和惯性力的影响,忽略刀盘运动时刮刀动力的影响,刮刀工作过程中通过刀盘以及刀座给予刮刀上的力为轴向力和扭矩,分别定义为fz和tv,设根据不同的刮刀安装位置可以分别计算出fz以及扭矩在此处的作用力fv=f
t
,fz=fn,f
t
为刮刀所受到的切削力,fn是刮刀受到的轴向力,由二力平衡原理
[0065]
∑xi=0,∑yi=0,∑zi=0
[0066]
∑m
x
(fi)=0,∑my(fi)=0,∑mz(fi)=0
[0067]
根据刀具受力平衡条件和掌子面施工环境得到刮刀未磨损的初始状态切削力和轴向力的理论值分别为
[0068][0069][0070]
当刮刀刀刃磨损为圆弧结构时,切削力与轴向力都将增大,将圆弧刀刃近似为刀刃宽度为a的楔形块,根据刮刀材料特性以及全断面隧道掘进机施工环境,确定刮刀磨损至极限位置时a的最大值,在刀刃面上土体对刮刀的阻力为p
f1
,土体内摩擦角保持不变。此时,刮刀产生的切削力和轴向力的理论值分别为
[0071][0072][0073]
通过计算刮刀切削力和轴向力在y轴的合力即可得出刮刀在未磨损的初始状态与
刀座间的作用力f1和刮刀磨损至极限位置时与刀座间的作用力f2理论值的计算公式。
[0074]
与cn1818640a的专利申请文件公开的隧道掘进机掘进过程中刀具磨损的检测方法相比较,本发明的有益效果是:
[0075]
1、通过在刮刀与刀座之间直接安装压力传感器,根据刮刀磨损引起的刮刀与刀座之间压力的变化,使用单一变量判断刮刀磨损量,误差较小,判断准确;采用间隔时间段内平均压力值作为判断值,可避免在某个瞬间由于不定因素造成的数值突变导致的判断失误。
[0076]
2、本发明在刀盘上每个刮刀与刀座之间均安装压力传感器,通过在中央控制室中将刀盘上不同安装位置刮刀的报警装置进行编号,可准确判断磨损至极限的刮刀,不需开仓检查即可及时进行更换,有利于降低检测成本,提高掘进效率。
附图说明
[0077]
图1为本发明中刮刀及压力传感器的安装示意图;
[0078]
图2为刮刀的侧视图;
[0079]
图3为本发明中建立的直角坐标系和受力分析图。
[0080]
图中:1-刮刀,2-刀座,3-刀盘,4-压力传感器,5-压力传感器引线。
具体实施方式
[0081]
以下结合附图和实施例对本发明作进一步说明。
[0082]
本实施例为采用全断面隧道掘进机对某隧道进行开凿。
[0083]
该隧道的地质条件为粘土性,刮刀贯入度h=5mm,土体容量λ=18kn/m3,土体内聚力c=12kpa,地表面到盾构中轴的深度h=15m,被动土压力系k
p
=3.25,侧向土压力系数k0=0.46,土体内摩擦角岩土与钢的摩擦系数μ=0.3,土体的无侧限抗压强度p0=125kpa。
[0084]
全断面隧道掘进机采用的刮刀如图2所示,为楔形结构,刮刀长度l=150mm,刮刀宽度d=100mm,刮刀磨损至极限刀刃宽度a=3mm,刮刀切削角α=75
°
,刮刀刃角β=60
°
,刮刀后角δ=15
°
,刮刀前角γ=15
°
(α=β+δ、α+γ=90
°
)。
[0085]
掘进机开凿过程中对刮刀磨损采用本发明方法进行检测,具体操作步骤是:
[0086]
步骤1
[0087]
参照图1,在刀盘3上通过刀座2安装刮刀1,在每个刮刀与刀座之间安装压力传感器4,压力传感器4为厚度0.25mm左右、工作电压为5v、额定电流为5ma的柔性薄膜压力传感器,将压力传感器安装在刮刀与刀座接触面的前端部中心位置,使压力传感器与刮刀和刀座紧密贴合,确保能够准确采集压力信息;压力传感器安装好后用密封剂对接触面边缘进行密封,避免刮刀工作过程中渗入泥水和石渣,影响传感器正常工作;最后将压力传感器引线5穿过预先开设在刀座中的引线孔引到刀盘3上,与安装在刀盘上的无线信号发射器(未图示)相连,设在中央控制室中的无线信号接收器(未图示)与报警装置(未图示)相接,对刀盘上不同位置刮刀的报警装置进行编号。
[0088]
步骤2
[0089]
如图1所示,以压力传感器的压力采集中心点为原点,以垂直于刮刀与刀座的接触
面的直线为y轴,以与刮刀后端面侧边平行的直线为x轴建立直角坐标系;如图3所示,利用建立的直角坐标系绘制受力分析图;由受力分析图分别测得刮刀切削力f
t
与y轴的夹角θ1为35
°
,刮刀轴向力fn与y轴的夹角θ2为55
°
。
[0090]
步骤3
[0091]
(1)根据刮刀在未磨损的初始状态与刀座间的作用力f1的计算公式求得
[0092][0093]
pf=μp
h sinα=52.431n
[0094][0095][0096][0097]fy1
=|f
t1 cosθ
1-f
n1 cosθ2|=93.966n
[0098]
初始状态刮刀与刀座间的作用力f1=f
y1
=93.966n;
[0099]
(2)根据刮刀磨损至极限位置时刮刀与刀座间的作用力f2的计算公式求得
[0100][0101]
pz=p0ad=37.500n
[0102][0103][0104][0105]fy2
=|f
t2 cosθ
1-f
n2 cosθ2|=118.048n
[0106]
刮刀磨损至极限位置与刀盘的作用力f2=f
y2
=118.048n。
[0107]
步骤4
[0108]
在全断面隧道掘进机运行过程中,通过压力传感器不间断地采集刮刀与刀座间的作用力fn,,为确保压力采集的精确,避免由压力单一值的突变(突然变大或突然变小,甚至为零)对压力检测结果的影响,采取每间隔1s采集一次压力传感器的压力信息,从刮刀开始运行第一秒开始采集,依次获取100次数据设为第一组,并计算第一组数据的平均值f
n1
,作为压力判断值;第二组数据从刮刀开始运行第二秒开始采集,依相同方式获取100次数据,将该组数据设为第二组,并计算第二组数据的平均值fn2
……
,依次类推获取n组数据,当平均值
[0109][0110]
不在f1~f2数值范围内(93.966n—118.048n)时,判定刮刀达到磨损极限,通过无线信号发射器发射信号,设在中央控制室中的无线信号接收器接收信号,通过报警装置报警判断磨损至极限、需要更换的刮刀位置。