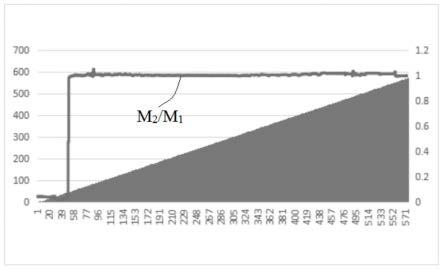
1.本发明属于轧钢大型测量仪表技术领域,更具体地说,涉及一种判断热轧多功能测厚仪表射线管状态变化趋势的方法。
背景技术:2.热轧带钢生产过程中,多功能测厚仪表是一台非常重要的厚度测量仪表,可以测量成品带钢的横向轮廓厚度,其测量原理是通过射线管电离空气产生x射线,让x射线定向向下照射,x射线穿透带钢后到达带钢下方的探头接收端,探头接收端由五百多个小的闪烁晶体晶体组成,构成垂直于带钢运行方向的并覆盖带钢整个宽度方向的接受端。探头通过接收到的x射线能量计算出带钢的厚度等数据。
3.随着使用时间的推移,设备会发生系统漂移,可能导致测量数据出现误差,为了保证设备的精度,需要对测厚仪表进行年度校验,称之为全标工作,全标采用设备自带的各规格标准样片(称之为外部标准样片)进行设备离线外部样片测量校验,并同时校验调整仪表参数,其工作量很大,全标调整后的射线管能量是最优状态。此外,为确保每块钢测量之前消除环境干扰误差,仪表会自动在每块带钢进入精轧机架前时再进行一个简单的内部样片校准工作(其样片装在设备内部),称之为零标工作。
4.测厚仪表的准确性是一个重要的参数,而射线管的状态好坏是左右测厚仪测量准确性的关键因素。实际生产中受现场振动环境的影响射线管的安装位置会发生微变,以及电气设备自身老化会造成放射能力的减弱,导致了射线管的能量变动是客观存在的。
5.为了判断仪表设备及射线管的能量是否满足测量要求,在现实中技术人员通过安装标定架,放置各种规格实际轧制的钢板,先用仪表测量这些钢板厚度并记录,同时人工用千分尺测量同样钢板并记录,从仪表测量结果于千分尺的手动测量结果相比较,从侧面推断多功能仪表射线管的能量是否满足测量要求。此类操作耗时,费力,影响周围环境,以及人员的测量误差,导致判断结果不确定性增加,如何去用简单的方法量化评价测厚仪表射线管状态好坏的变化趋势是一个技术人员不得不面临的问题。
技术实现要素:6.1、要解决的问题
7.针对现有技术中存在的问题,本发明拟提供一种判断热轧多功能测厚仪表射线管状态变化趋势的判断方法,通过对多功能测厚仪所用射线管能量数据进行分析,能够简便、客观地反应测厚仪表射线管能量状态的变化情况,方便对轧钢现场仪表测厚设备关键元件进行及时维护,有效预防和降低设备的故障概率。
8.2、技术方案
9.为解决上述问题,本发明采用如下的技术方案。
10.本发明的一种判断热轧多功能测厚仪表射线管状态变化趋势的方法,包括零标数据图表整理分析:以多功能测厚仪表内的射线管s1作为研究对象,采用多功能测厚仪表设
备自带的某一规格标准样片进行设备离线外部样片测量,并采集某个时间点射线管s1测量的该规格标准样片的能量数据,称之为零标数据,以一个月时间为间隔顺序,采集一段时间内的一组射线管s1的零标数据后对其进行整理,利用数据软件的导出数据功能选项,对采集到的每组射线管s1的零标数据生成相应的图表,当图表在某一时间点出现突变时,则表明多功能测厚仪表内的射线管s1的能量状态发生了变化,需要点检人员重点关注。
11.作为本发明更进一步的改进,当上述零标数据图表在某一时间点出现突变时,此时则需要用全标数据的能量曲线进行全面核算,其中采用多功能测厚仪表设备自带的各个规格标准样片进行设备离线外部样片测量,并采集某个时间点射线管s1测量的各个规格标准样片的一组能量数据,称之为全标数据,通过数据软件导出的不同时间点的射线管s1的全标数据,并对不同时间点的每组全标数据进行编辑整理,形成单独的射线管s1能量曲线,当某个时间点的射线管s1能量曲线与其他时间点的射线管s1能量曲线趋势明显不一致时,则说明射线管s1的状态发生变化,需要点检重点关注。
12.作为本发明更进一步的改进,当某个时间点的射线管s1能量曲线趋势出现明显变化时,通过计算射线管s1的能量比值来判断射线管状态变化情况,其中以上一年度的全标数据作为初始全标数据,初始全标数据所对应的能量数值为q0,通过数据软件导出的不同时间点的射线管s1的全标数据所对应的能量数值为qn,不同时间点的射线管s1的能量比值为mn,mn=qn/q
n-1
,当发现某个时间点的能量比值mn出现突变点时,则认为是射线管s1状态变化的临界点,此时需要调整射线管s1的位置或者更换射线管s1。
13.作为本发明更进一步的改进,当mn《0.8m
n-1
时,则射线管s1状态异常,此时需要调整射线管s1的位置或者更换射线管s1。
14.3、有益效果
15.相比于现有技术,本发明的有益效果为:
16.(1)本发明的一种判断热轧多功能测厚仪表射线管状态变化趋势的方法,当点检人员直观识别出来图表这一时间点的零标数据出现问题时,可采取进一步的措施进行更详细的判断,进而能够初步直观地判定射线管s1的能量状态是否发生变化,避免了传统的人工手动测量的误差,能够用简单的方法量化评价测厚仪表射线管状态好坏,大大减轻了工作人员的工作量,同时提高了检测效率。
17.(2)本发明的一种判断热轧多功能测厚仪表射线管状态变化趋势的方法,当某个时间点的射线管s1能量曲线与其他时间点的射线管s1能量曲线趋势明显不一致时,则说明射线管s1的状态发生变化,需要点检重点关注,此时则说明该射线管s1的状态确实发生了相应的改变,工作人员则需要进一步核查该射线管s1是否需要进行位置调整或者相应的配件更换。通过对多功能测厚仪所用射线管能量数据进行分析,能够简便、客观地反应测厚仪表射线管能量状态的变化情况,方便对轧钢现场仪表测厚设备关键元件进行及时维护,有效预防和降低设备的故障概率。
18.(3)本发明的一种判断热轧多功能测厚仪表射线管状态变化趋势的方法,一方面节省了人力,物力,提高了工作效率和工作质量,另一方面及时发现关键元件劣化趋势,有效避免故障发生,能够在轧钢工业现场大型测厚仪表领域发挥较好的作用;同时弥补轧钢现场高精度测厚仪表射线管检测维护的空白,方法简单可靠,从适用范围来看,本发明的判断方法能够在所有使用类似射线管的大型仪表维护中进行推广应用,其应用前景广阔。
附图说明
19.图1为射线管s1的第一次全标数据q1的能量曲线图;
20.图2为射线管s1的第二次全标数据q2的能量曲线图;
21.图3为射线管s1的第二次全标数据q3的能量曲线图;
22.图4为第二次全标能量比值m1的曲线图;
23.图5为第三次全标能量比值m1的曲线图;
24.图6为射线管s1的状态变化趋势图。
具体实施方式
25.为进一步了解本发明的内容,结合附图对本发明作详细描述。
26.在本发明的描述中,需要说明的是,术语“中心”、“上”、“下”、“左”、“右”、“竖直”、“水平”、“内”、“外”等指示的方位或位置关系为基于附图所示的方位或位置关系,仅是为了便于描述本发明和简化描述,而不是指示或暗示所指的装置或元件必须具有特定的方位、以特定的方位构造和操作,因此不能理解为对本发明的限制。此外,术语“第一”、“第二”、“第三”仅用于描述目的,而不能理解为指示或暗示相对重要性。
27.下面结合实施例对本发明作进一步的描述。
28.实施例1
29.本实施例的一种判断热轧多功能测厚仪表射线管状态变化趋势的方法,包括零标数据图表整理分析:多功能测厚仪表包括左右两个射线管,分别为s1及s2,我们仅仅以多功能测厚仪表内的射线管s1作为研究对象,采用多功能测厚仪表设备自带的某一规格标准样片进行设备离线外部样片测量,并采集某个时间点射线管s1测量的该规格标准样片的能量数据,称之为零标数据。以一个月时间为间隔顺序,采集一段时间内的一组射线管s1的零标数据后对其进行整理,利用数据软件的导出数据功能选项,将采集到的每组射线管s1的零标数据生成相应的图表,当图表在某一时间点出现突变时,则表明多功能测厚仪表内的射线管s1的能量状态发生了变化,此时则需要点检人员重点关注,当点检人员直观识别出来图表这一时间点的零标数据出现问题时,可采取进一步的措施进行更详细的判断,进而能够初步直观地判定射线管s1的能量状态是否发生变化,避免了传统的人工手动测量的误差,能够用简单的方法量化评价测厚仪表射线管状态好坏,大大减轻了工作人员的工作量,同时提高了检测效率。
30.当上述零标数据图表在某一时间点出现突变时,此时则需要用全标数据的能量曲线进行全面核算,或者需要对多功能测厚仪表进行全面检测时,通常也需要用全标数据的能量曲线进行全面核算,保证对多功能测厚仪表射线管能量状态的全面检测,能够更加精准的探知线管能量状态的变化情况。其中采用多功能测厚仪表设备自带的各个规格标准样片进行设备离线外部样片测量,并采集某个时间点射线管s1测量的各个规格标准样片的一组能量数据,称之为全标数据。通过数据软件导出的不同时间点的射线管s1的全标数据,并对不同时间点的每组全标数据进行编辑整理,形成单独的射线管s1能量曲线。假设现场环境影响均匀分布,设备老化状态相同,则其不同时间点的能量曲线趋势应该相同,当某个时间点的射线管s1能量曲线与其他时间点的射线管s1能量曲线趋势明显不一致时,则说明射线管s1的状态发生变化,需要点检重点关注,此时则说明该射线管s1的状态确实发生了相
应的改变,工作人员则需要进一步核查该射线管s1是否需要进行位置调整或者相应的配件更换。通过对多功能测厚仪所用射线管能量数据进行分析,能够简便、客观地反应测厚仪表射线管能量状态的变化情况,方便对轧钢现场仪表测厚设备关键元件进行及时维护,有效预防和降低设备的故障概率。
31.当某个时间点的射线管s1能量曲线趋势出现明显变化时,通过计算射线管s1的能量比值来判断射线管状态变化情况,其中以上一年度的全标数据作为初始全标数据,初始全标数据所对应的能量数值为q0,通过数据软件导出的不同时间点的射线管s1的全标数据所对应的能量数值为qn,不同时间点的射线管s1的能量比值为mn,mn=qn/q
n-1
,当发现某个时间点的能量比值mn出现突变点时,则认为是射线管s1状态变化的临界点,此时需要调整射线管s1的位置或者更换射线管s1。当若mn≈mn-1,则表明射线管s1状态正常;mn《0.8m
n-1
时,则表明射线管s1状态异常,此时需要调整射线管s1的位置或者更换射线管s1。
32.在原有的条件下对测厚仪表的射线管状态进行判断维护,操作时间受限,工作量大,程序繁琐,其中人为操作容易出现误差,影响工作效率,整体工作精度不能有效保证;通过本发明的判断方法,一方面节省了人力,物力,提高了工作效率和工作质量,另一方面及时发现关键元件劣化趋势,有效避免故障发生,能够在轧钢工业现场大型测厚仪表领域发挥较好的作用;同时弥补轧钢现场高精度测厚仪表射线管检测维护的空白,方法简单可靠,从适用范围来看,本发明的判断方法能够在所有使用类似射线管的大型仪表维护中进行推广应用,其应用前景广阔。
33.本发明所述实例仅仅是对本发明的优选实施方式进行描述,并非对本发明构思和范围进行限定,在不脱离本发明设计思想的前提下,本领域工程技术人员对本发明的技术方案作出的各种变形和改进,均应落入本发明的保护范围。