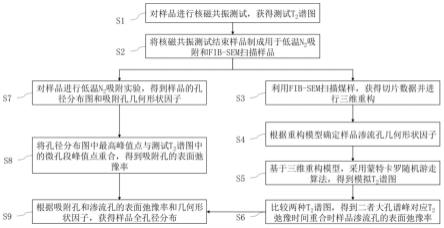
1.本发明涉及一种煤的全孔径分布测试方法,属于煤层孔隙结构测试领域。
背景技术:2.煤炭资源占据我国能源的主体地位,并且在未来一定时间内不会发生变化,目前煤矿生产过程中的安全问题仍较为严峻,尤其是煤矿瓦斯事故,严重威胁煤矿的安全生产。煤作为一种具有双重孔隙结构的多孔介质,其孔隙结构特征是影响其瓦斯吸附能力、渗透特性及力学强度的重要因素。国内外大量专家学者开展煤孔隙结构测试的相关研究,结果表明煤孔径分布范围十分广泛,孔径从纳米级到毫米级不等,并且对煤中的孔隙按照孔径进行了分类,例如iupac的分类、霍多特分类等,也有学者根据孔径是否大于0.1μm将煤的孔隙划分为吸附孔(<0.1μm)和渗流孔(>0.1μm)。不同尺度的孔隙决定着煤层气吸附解吸、扩散和渗流过程。煤孔隙结构的精准表征是研究煤孔渗特性的基础,而煤的孔渗特性是反映煤层气含量及可采性的重要指标。因此,研究煤的孔隙结构并对其进行精准表征极为重要,对于因地制宜采取合适的瓦斯防治措施具有重要意义。
3.目前测试煤孔隙结构的方法主要有压汞法、气体吸附法(n2吸附和co2吸附)、核磁共振、ct扫描、小角散射和聚焦离子束扫描电镜(fib-sem)等。近几年来,核磁共振由于其操作简便、孔径测试范围广泛,被广泛应用于煤孔隙结构的测试中,而核磁共振测试结果很大程度上受限于测试样品的表面弛豫率的测定,煤孔隙表面弛豫率与孔隙表面有机质的含量和分布特征关系密切。通过现有文献调研发现煤的介孔和微孔受控于煤中的脂肪侧链、芳香环片层等大分子结构的堆砌方式,其中大孔的孔隙表面有机质含量占比低于介孔和微孔,这就表明煤中不同孔径的孔隙表面弛豫率不同。但是现有的孔径测试通常认为煤的表面弛豫率是一个固定值,并未区分不同孔径大小的表面弛豫率,由于不同孔径的表面弛豫率按照相同的固定值,这就导致在对煤样进行孔隙结构测试时,大孔的测定出现较大误差,进而影响煤样孔径分布的测试结果。因此,迫切需要一种能够简单、高效的测试不同孔径表面弛豫率的方法,进而根据获得的不同孔径的孔隙对应的表面弛豫率,以精确测得煤的孔径分布信息。
技术实现要素:4.针对上述现有技术存在的问题,本发明提供一种煤的全孔径分布测试方法,能够简单、高效的测试不同孔径表面弛豫率,进而根据获得的不同孔径对应的表面弛豫率能精确得到煤的孔径分布信息。
5.为了实现上述目的,本发明采用的技术方案是:一种煤的全孔径分布测试方法,具体步骤为:
6.s1、先从所需测试区域采集煤岩体,并将煤岩体加工成多个圆柱体作为煤样,选择一个煤样进行核磁共振测试,获得该煤样的测试t2谱图;其中根据测试t2谱图数据、以t2弛豫时间的大小划定大中微孔,将其中t2值小于10ms的为微孔段,位于t2值处于10-100ms的为
中孔段,大于100ms的为大孔段;
7.s2、将核磁共振测试结束后的煤样,分别加工成用于低温n2吸附试验的粉末和用于fib-sem扫描的矩形块体;
8.s3、利用fib-sem(即聚焦离子束扫描电子显微镜)扫描该煤样,获得该煤样的切片图像,然后对切片图像进行阈值分割和三维重构,获得三维重构模型,并由三维重构模型得到孔径分布图;
9.s4、根据三维重构模型,先将渗流孔的孔隙形状分成多类,然后统计模型中每个分类中的渗流孔体积,将体积最大的一类孔隙确定为该煤样的主要孔隙形状,根据主要孔隙形状确定煤样渗流孔几何形状因子f
s1
;
10.s5、基于步骤s4的三维重构模型,采用蒙特卡罗随机游走算法,得到模拟t2谱图;其中根据模拟t2谱图数据,以t2弛豫时间的大小划定大中微孔,将其中t2值小于10ms的为微孔段,位于t2值处于10-100ms的为中孔段,大于100ms的为大孔段;
11.s6、比较步骤s1和步骤s5获得的两个t2谱图,进而根据公式计算得到二者大孔段谱峰对应t2弛豫时间值重合时样品渗流孔的表面弛豫率ρ1;
12.s7、步骤s2加工后的同一煤样进行低温n2吸附实验,得到该煤样的吸附-脱附曲线,然后根据曲线采用bjh法计算获得煤样孔径分布图,并根据曲线获得吸附孔的孔隙形状,具体能分为圆柱形孔、狭缝形孔、楔形孔和墨水瓶形孔,其中圆柱形孔和楔形孔划分类为柱形孔,狭缝形孔划分类为平行板孔,墨水瓶孔分类为球形孔,进而按照步骤s2确定渗流孔几何形状因子f
s1
的过程确定吸附孔的几何形状因子f
s2
;
13.s8、将步骤s3获得的孔径分布图中最高峰值点与步骤s1获得的测试t2谱图中的微孔段峰值点重合,进而根据公式计算得到吸附孔的表面弛豫率ρ2;
14.s9、根据吸附孔和渗流孔各自的表面弛豫率和几何形状因子,得出该煤样的吸附孔分布和渗流孔分布,然后由吸附孔分布和渗流孔分布组成该煤样最终的全孔径分布图,其中在该煤样全孔径分布图内吸附孔和渗流孔两者连接处的孔径为0.1μm,且其对应的表面弛豫率为吸附孔的表面弛豫率ρ2。
15.进一步,所述步骤s4中将渗流孔的孔隙形状进行分类,按照平行板孔、柱形孔和球形孔分成三类。
16.进一步,所述步骤s6中将两种图谱的大孔段谱峰重合时对应的t2值和孔喉半径作为计算渗流孔表面弛豫率的参数值,计算公式为:
[0017][0018]
式中,ρ为孔隙表面弛豫率;fs为孔隙几何形状因子,若分类后为平行板孔取1,柱形孔取2,球形孔取3;r为孔喉半径。
[0019]
进一步,所述步骤s7中将测试t2谱图中微孔段峰值点对应的t2值和煤样孔径分布图中孔径位于2-50nm范围中的最高峰值点对应的孔径作为计算吸附孔表面弛豫率的参数值,然后将参数值代入步骤s6中的计算公式,最终得出吸附孔的表面弛豫率ρ2。
[0020]
进一步,将经过核磁共振测试后的饱水煤样放入干燥箱中,45℃恒温干燥12h,然后取出煤样,分别加工成用于低温n2吸附试验的粉末和用于fib-sem扫描的矩形块体;其中粉末为粒度为200目且质量不超过2g的粉末;矩形块体的体积小于10
×
10
×
5mm。
[0021]
与现有技术相比,本发明考虑到测试煤样中不同孔径的孔隙形状和孔隙表面有机组分的差异,因此通过fib-sem重构模型、蒙特卡罗随机游走算法模拟t2谱图、核磁共振测试t2谱图和低温n2吸附孔径分布曲线相结合进行分析,对煤样中渗流孔和吸附孔的形状进行分类,分别确定两种类型孔隙的几何形状因子和表面弛豫率,然后根据吸附孔和渗流孔各自的表面弛豫率和几何形状因子,得出该煤样的吸附孔分布和渗流孔分布,进而组成煤样的全孔径分布图,从而精准表征煤的孔隙结构;本发明弥补了现有核磁共振测试过程中,使用单一孔隙几何形状因子和表面弛豫率,不能精确求解样品孔径分布的缺陷(即由于煤中不同孔径范围的孔隙表面弛豫率不同会使得对应范围的孔径分布也不同),有效提高了煤样全孔径分布测试的准确性,对于进一步表征煤储层吸附特性提供数据支撑。
附图说明
[0022]
图1为本发明的流程示意图;
[0023]
图2为本发明中煤样的核磁共振测试t2谱图示意图;
[0024]
图3为中煤样的低温n2吸附-脱附曲线示意图;
[0025]
图4为本发明中煤样的低温n2吸附孔径分布示意图。
具体实施方式
[0026]
下面将对本发明作进一步说明。
[0027]
如图1所示,本发明的具体步骤为:
[0028]
s1、先从所需测试区域采集煤岩体,并将煤岩体加工成多个尺寸为φ25
×
50mm的圆柱体作为煤样,选择一个表面无宏观裂隙的煤样进行核磁共振测试,获得该煤样的测试t2谱图;其中根据测试t2谱图数据、以t2弛豫时间的大小划定大中微孔,将其中t2值小于10ms的为微孔段,位于t2值处于10-100ms的为中孔段,大于100ms的为大孔段;具体过程为:将煤样放入真空饱水机内真空饱水12h,然后擦净样品表面水分,放入低场核磁共振分析仪中进行测试,核磁共振测试设备的设置参数如下表;
[0029][0030]
如图2所示,获得该煤样的测试t2谱图;
[0031]
s2、将经过核磁共振测试后的饱水煤样放入干燥箱中,45℃恒温干燥12h,然后取出煤样,分别加工成用于低温n2吸附试验的粉末和用于fib-sem扫描的矩形块体;其中粉末为粒度为200目且质量不超过2g的粉末;矩形块体的体积小于10
×
10
×
5mm;
[0032]
s3、利用fib-sem(即聚焦离子束扫描电子显微镜)扫描该煤样,获得该煤样的切片
0.6之间时存在吸附体积的降低“滞后环”,表面样品中吸附孔主要以墨水瓶形孔为主,即为球形孔,对应的吸附孔几何形状因子f
s2
取值为3;
[0045]
s8、将步骤s3获得的孔径分布图中最高峰值点与步骤s1获得的测试t2谱图中的微孔段峰值点重合,即测试t2谱图中微孔段峰值点对应的t2值和煤样孔径分布图中孔径位于2-50nm范围中的最高峰值点对应的孔径作为计算吸附孔表面弛豫率的参数值,然后将参数值代入步骤s6中的计算公式,最终得出吸附孔的表面弛豫率ρ2;其中孔径小于1μm的为吸附孔,孔径大于1μm的为渗流孔;
[0046]
s9、根据吸附孔和渗流孔各自的表面弛豫率和几何形状因子,得出该煤样的吸附孔分布和渗流孔分布,然后由吸附孔分布和渗流孔分布组成该煤样最终的全孔径分布图,其中在该煤样全孔径分布图内吸附孔和渗流孔两者连接处的孔径为0.1μm,且其对应的表面弛豫率为吸附孔的表面弛豫率ρ2。
[0047]
以上所述仅是本发明的优选实施方式,应当指出:对于本技术领域的普通技术人员来说,在不脱离本发明原理的前提下,还可以做出若干改进和润饰,这些改进和润饰也应视为本发明的保护范围。