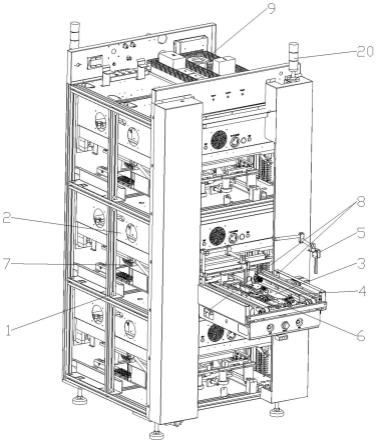
1.本发明应用于工业自动化领域的技术领域,特别涉及一种自动测试设备。
背景技术:2.随着工业4.0的到来,自动化得到迅速发展,在服务器电路主板生产制造过程中,需要对服务器电路主板进行各功能及性能测试,以提高服务器的出厂合格率,然而当前服务器功能测试系统为离线测试,需要人工进行辅助,测试效率不高,如果人工操作对电路主板进行大批量测试,容易因漏检、误检以及情绪化等因素导致不合格品流入到客户处,从而造成投诉,并且人工操作检测生产效率低下,劳动负荷较大。现有的测试生产线大多为流水线结构,流水线排列着多个测试机,每台测试机只能进行单组产品的测试,设备集成度低,每台测试设备均需要设置单独的搬运机构占用空间大,而且成本较高。中国专利cn105314422a公开了一种电路板测试系统,其通过抓取机构沿z向上下运动至电路板组装生产线的高度位置抓取产品且可运动至测试柜某一高度的测试机以取放产品。其中,抓取机构采用风琴形吸盘吸取电路板,以替代真空吸盘或夹爪抓取电路板,有利于降低生产设备的生产成本,有利于简化生产设备的结构,有利于简化控制流程,有利于节能减排,在一定的程度上解决了操作空间大的问题,然而抓取机构无法进入测试机柜的狭窄空间,需要采用抽屉式结构的测试机柜,且每一层都需配置动力源进行伸出和拉回,因此造成设备成本高等问题,不利于产品的精准定位,同时其不具有防压防撞报警模块,容易带来安全隐患,因此有必要提供一种结构紧凑、集成度高且安全性高的自动测试设备。
技术实现要素:3.本发明所要解决的技术问题是克服现有技术的不足,提供了一种结构紧凑、集成度高且安全性高的自动测试设备。
4.本发明所采用的技术方案是:本发明包括机架,所述机架内纵向设置有若干组测试机,所述机架上设有若干个与所述测试机对应配合的出入料口,所述机架的侧面设置有升降机构且所述升降机构位于所述出入料口的一端,所述升降机构上设置有皮带输送模组,所述皮带输送模组的内侧设置有推拉模组;工作时,将装有产品的载具放置在所述皮带输送模组上,所述升降机构驱动所述皮带输送模组移动到对应的所述出入料口,所述皮带输送模组将装有产品的载具输送至所述推拉模组的上方,所述推拉模组将装有产品的载具输送至对应所述测试机的下方。
5.由上述方案可见,至少两组所述测试机在所述机架内纵向排列,分层式布局有鲈鱼将空间利用到最大化,至少两组所述测试机集成至所述机架上,以更低的自动化升级成本提高了ft的使用率,产品通过所述推拉模组的输送作用与所述测试机实现对插,从而导通测试,上料时,外部agv将产品输送至所述皮带输送模组的前端,所述皮带输送模组将产品输送至所述推拉模组的上方,所述推拉模组将产品输送至对应所述测试机的下方,产品与所述测试机对插进行测试,所述升降机构驱动所述推拉模组重复进行上述动作,保证每
一层所述测试机持续工作,减少若干组所述测试机的待机时间,当产品测试完成后,所述推拉模组和所述皮带输送模组配合,取出产品并输送至等待位,以供外部agv进行对接,所述自动测试设备能够精准地自动取送产品,实现扁平化操作,满足多层位供料,具有较好的实用性。
6.一个优选方案是,所述推拉模组包括无杆气缸、凸块以及传动轴,所述无杆气缸的滑块连接有输送架,所述输送架上固定有第一驱动气缸和夹块,所述第一驱动气缸的输出轴传动连接有横向板,所述横向板的两端均连接有纵向板,两个所述纵向板对称设置有斜槽,所述夹块位于两个所述纵向板之间,所述夹块内设有竖直方向的通孔,所述凸块位于所述通孔内,所述传动轴穿过所述凸块且所述传动轴的两端分别与两个所述斜槽配合。
7.由上述方案可见,当所述皮带输送模组将产品输送至所述推拉模组的上方,所述第一驱动气缸驱动所述横向板向后移动,从而带动所述纵向板向后移动,由于所述传动轴穿过所述凸块且所述传动轴的两端分别与两个所述斜槽配合,所述传动轴在所述斜槽内沿着一定的坡度移动,带动所述凸块在所述通孔内进行升降运动,所述夹块用于所述凸块移动的限位,所述凸块与产品底部的限位孔配合,从而卡住产品,保证所述无杆气缸驱动所述输送架时,产品不会发生移位。当所述第一驱动气缸驱动所述纵向板收缩,带动所述传动轴在所述斜槽向上移动,所述凸块向上伸出卡住产品,所述无杆气缸驱动所述输送架至所述测试机的下方,产品与所述测试机对插进行测试,所述升降机构驱动所述推拉模组重复进行上述动作,保证若干组所述测试机持续工作,减少若干组所述测试机的待机时间,当产品测试完成后,所述推拉模组和所述皮带输送模组配合,取出产品并输送至等待位,以供外部agv进行对接,所述凸块通过所述传动轴和所述斜槽的配合卡住产品,传统的限位固定结构通常为设置在产品两侧的气缸,两组气缸向前驱动将产品夹住,采用两组气缸不仅增加设备的成本,而且难以保证联动的一致性,由于两组气缸是对产品移动方向的两侧进行施力,当所述无杆气缸驱动产品快速移动时,产品因惯性的作用发生移位,从而影响所述测试机的对插,另一种限位固定结构为设置在产品的底部且沿竖直方向的气缸,这种限位固定结构不仅占据更多的空间,而且直接驱动凸块会耗费更多的能量,而且产品的固定效果较差,所述推拉模组通过所述夹块与所述传动轴的配合对所述凸块的上下两端进行施力,进而提高产品在所述推拉模组上的稳固性。
8.一个优选方案是,所述测试机包括爬坡顶升模组,所述爬坡顶升模组包括支撑架、支撑板以及两组直线导轨,所述支撑架的内侧设置有第二驱动气缸,所述第二驱动气缸的输出轴传动连接有滑板,所述滑板滑动设置在两组所述直线导轨上,所述滑板上对称设置有四个斜块,所述支撑板的底部设置有与所述斜块对应配合的滚轮。
9.由上述方案可见,所述爬坡顶升模组作为产品的承载体且设置在所述测试机的下方,所述支撑板底部的所述滚轮对应地滑动配合在四个所述斜块上,所述第二驱动气缸驱动所述滑板收缩,带动所述支撑板向上运动,进而将产品顶起,以供所述测试机进行测试,传统的顶升方式是气缸直接驱动顶升板向上运动,由于产品的重量较大,将产品顶起并且保持一段时间需设置大功率的气缸,显然增加气缸的耗能,所述滑板通过第二驱动气缸滑动在两组所述直线导轨上,所述滚轮和所述斜块作为所述支撑板的支撑体,能减少所述自动测试设备的耗能。
10.一个优选方案是,所述自动测试设备还包括触动模组和电控模组,所述电控模组
设置在所述机架的顶部且控制所述自动测试设备的工作,所述触动模组包括若干组上触动模组和若干组下触动模组,所述上触动模组和所述下触动模组均包括导柱和固定块,所述固定块固定在所述皮带输送模组的外侧,所述导柱上套设有压缩弹簧,所述固定块上设置有轴承和槽型光电传感器,所述导柱穿过所述轴承,所述导柱的一端连接有感应片,所述感应片与所述槽型光电传感器配合,所述槽型光电传感器与所述电控模组电信号配合,所述皮带输送模组的外侧和底部分别设置有第一防护板和第二防护板,所述上触动模组的所述导柱与所述第一防护板的顶部配合,所述下触动模组的所述导柱与所述第二防护板的底部配合。
11.由上述方案可见,所述触动模组实现所述升降机构的防圧、防撞、自动报警功能,当所述升降机构向上运动接触到异物时,所述第一防护板对所述上触动模组的所述导柱施加向下方向的力,所述上触动模组的所述感应片进入到所述上触动模组的所述槽型光电传感器的感应范围,所述电控模组将停止所述升降机构的工作,所述压缩弹簧和所述轴承配合用于所述导柱的复位,当所述升降机构向下运动接触到异物时,所述第二防护板对所述下触动模组的所述导柱施加向上方向的力,所述下触动模组的所述感应片进入到所述下触动模组的所述槽型光电传感器的感应范围,所述电控模组将停止所述升降机构的工作,所述触动模组是具有防圧、防撞弹性触发机构,在收到一定的挤压、碰撞后,所述升降机构自动报警停机,能有效保障操作员的安全。
12.一个优选方案是,所述自动测试设备还包括若干把扫码枪,若干把所述扫码枪设置在所述皮带输送模组的上方,所述扫码枪与产品上的二维码配合。
13.由上述方案可见,所述扫码枪用于扫码检测产品,保证产品信息的追溯性。
14.一个优选方案是,所述皮带输送模组的两侧设置有交替连接的固定夹和支柱,最末端的所述固定夹连接有连接片,所述连接片上设有腰型槽,所述扫码枪固定在所述腰型槽上。
15.由上述方案可见,所述扫码枪通过所述固定夹和所述支柱设置在所述皮带输送模组的上方,所述扫码枪固定在所述腰型槽上,满足多角度方向的扫码,实现多行程的自由调节,进而兼容不同产品板的扫码功能。
16.一个优选方案是,所述皮带输送模组的进料端和出料端均设置有第三驱动气缸,所述第三驱动气缸的输出轴传动连接有第一挡块。
17.由上述方案可见,所述第三驱动气缸驱动所述第一挡块向上伸出,从而挡住产品,保证所述皮带输送模组的进料端和出料端能够有序地上料,避免产品发生堆积。
18.一个优选方案是,所述皮带输送模组的两侧分别设置有第四驱动气缸和导正板,所述第四驱动气缸的输出轴传动连接有第二挡块,所述第二挡块与所述导正板配合。
19.由上述方案可见,所述第四驱动气缸驱动所述第二挡块向前伸出,所述第二挡块与所述导正板将产品进行夹持,从而提高产品在输送过程的稳固性。
20.一个优选方案是,所述支撑架的内侧设置有若干条导正柱,所述支撑板的底部设有与所述导正柱配合的限位孔。
21.由上述方案可见,所述导正柱用于所述支撑架的限位导正,避免所述支撑架发生移位。
22.一个优选方案是,所述自动测试设备还包括感应器和警示灯,所述感应器位于所
述纵向板的一侧,所述警示灯设置在所述机架的顶部,所述感应器和所述警示灯均与所述电控模组电信号配合。
23.由上述方案可见,所述感应器位于所述纵向板的一侧,当所述推拉模组对产品进行推拉输送时,所述感应器能够有效识别产品是否脱钩,所述警示灯与所述电控模组电信号配合,当所述触动模组收到一定的挤压、碰撞后,所述升降机构自动报警停机,所述警示灯会发出警报声和亮灯,以便操作员解除异常报警。
附图说明
24.图1是本发明的立体结构示意图;图2是所述升降机构动作端的立体结构示意图;图3是所述推拉模组的剖视图;图4是所述触动模组的立体结构示意图;图5是所述爬坡顶升模组第一角度的立体结构示意图;图6是所述爬坡顶升模组第二角度的立体结构示意图。
具体实施方式
25.如图1至图6所示,在本实施例中,本发明包括机架1,所述机架1内纵向设置有若干组测试机2,所述机架1上设有若干个与所述测试机2对应配合的出入料口,所述机架1的侧面设置有升降机构3且所述升降机构3位于所述出入料口的一端,所述升降机构3上设置有皮带输送模组4,所述皮带输送模组4的内侧设置有推拉模组6,工作时,产品放置在所述皮带输送模组4上,所述升降机构3驱动所述皮带输送模组4移动到对应的所述出入料口,所述皮带输送模组4将产品输送至所述推拉模组6的上方,所述推拉模组6将产品输送至对应所述测试机2的下方。
26.在本实施例中,所述推拉模组6包括无杆气缸61、凸块66以及传动轴67,所述无杆气缸61的滑块连接有输送架62,所述输送架62上固定有第一驱动气缸63和夹块68,所述第一驱动气缸63的输出轴传动连接有横向板,所述横向板的两端均连接有纵向板64,两个所述纵向板64对称设置有斜槽65,所述夹块68位于两个所述纵向板64之间,所述夹块68内设有竖直方向的通孔,所述凸块66位于所述通孔内,所述传动轴67穿过所述凸块66且所述传动轴67的两端分别与两个所述斜槽65配合。
27.在本实施例中,所述测试机2包括爬坡顶升模组7,所述爬坡顶升模组7包括支撑架71、支撑板72以及两组直线导轨73,所述支撑架71的内侧设置有第二驱动气缸74,所述第二驱动气缸74的输出轴传动连接有滑板75,所述滑板75滑动设置在两组所述直线导轨73上,所述滑板75上对称设置有四个斜块76,所述支撑板72的底部设置有与所述斜块76对应配合的滚轮77。
28.在本实施例中,所述自动测试设备还包括触动模组8和电控模组9,所述电控模组9设置在所述机架1的顶部且控制所述自动测试设备的工作,所述触动模组8包括若干组上触动模组和若干组下触动模组,所述上触动模组和所述下触动模组均包括导柱81和固定块82,所述固定块82固定在所述皮带输送模组4的外侧,所述导柱81上套设有压缩弹簧83,所述固定块82上设置有轴承84和槽型光电传感器85,所述导柱81穿过所述轴承84,所述导柱
81的一端连接有感应片86,所述感应片86与所述槽型光电传感器85配合,所述槽型光电传感器85与所述电控模组9电信号配合,所述皮带输送模组4的外侧和底部分别设置有第一防护板87和第二防护板88,所述上触动模组的所述导柱81与所述第一防护板87的顶部配合,所述下触动模组的所述导柱81与所述第二防护板88的底部配合。
29.在本实施例中,所述自动测试设备还包括若干把扫码枪5,若干把所述扫码枪5设置在所述皮带输送模组4的上方,所述扫码枪5与产品上的二维码配合。
30.在本实施例中,所述皮带输送模组4的两侧设置有交替连接的固定夹10和支柱11,最末端的所述固定夹10连接有连接片12,所述连接片12上设有腰型槽,所述扫码枪5固定在所述腰型槽上。
31.在本实施例中,所述皮带输送模组4的进料端和出料端均设置有第三驱动气缸13,所述第三驱动气缸13的输出轴传动连接有第一挡块14。
32.在本实施例中,所述皮带输送模组4的两侧分别设置有第四驱动气缸15和导正板16,所述第四驱动气缸15的输出轴传动连接有第二挡块17,所述第二挡块17与所述导正板16配合。
33.在本实施例中,所述支撑架71的内侧设置有若干条导正柱18,所述支撑板72的底部设有与所述导正柱18配合的限位孔。
34.在本实施例中,所述自动测试设备还包括感应器19和警示灯20,所述感应器19位于所述纵向板64的一侧,所述警示灯20设置在所述机架1的顶部,所述感应器19和所述警示灯20均与所述电控模组9电信号配合。
35.在本实施例中,所述机架1的长度为1020mm,宽度为1540mm,高度为2120mm,所述机架包括钣金和铝合金型材,所述升降机构包括钣金和al6061铝合金。
36.在本实施例中,所述推拉模组6还包括旋转电机和勾块,所述旋转电机固定在所述输送架62上,所述旋转电机的输出轴传动连接有所述勾块,所述勾块与产品底部的限位孔配合,从而卡住产品。通过所述旋转电机与所述勾块的配合有利于提高产品的定位效率。
37.本发明的工作原理:上料时,外部agv将装有产品的载具输送至所述皮带输送模组的前端,产品通过皮带的带动下输送至所述皮带输送模组的二分之一行程,从而到达所述推拉模组的上方,所述第四驱动气缸驱动所述第二挡块向前伸出,所述第一驱动气缸驱动所述纵向板收缩,带动所述传动轴在所述斜槽向上移动,所述凸块向上伸出卡住产品,所述无杆气缸驱动所述输送架至所述爬坡顶升模组的上方,所述第一驱动气缸驱动所述凸块复位,所述无杆气缸驱动所述输送架收缩复位,所述第二驱动气缸驱动所述滑板收缩,带动所述支撑板向上运动,进而将产品顶起,以供所述测试机进行测试,当产品测试完成后,所述爬坡顶升模组、所述推拉模组以及所述皮带输送模组配合,取出产品并输送至等待位,以供外部agv进行对接。
38.实施例二:在本实施例中,所述推拉模组包括第一推拉模组和第二推拉模组,所述第一推拉模组设置在所述皮带输送模组的内侧且靠近所述测试机的一端,所述第一推拉模组与所述测试机配合,将产品输送至测试位,所述第二推拉模组设置在所述皮带输送模组的内侧且靠近外部agv的一端,所述第二推拉模组与外部agv配合,将产品输送至所述皮带输送模组
的输送端,所述第一推拉模组与所述第二推拉模组有序配合,有利于提高产品的上下料速度,进一步提高自动化程度。