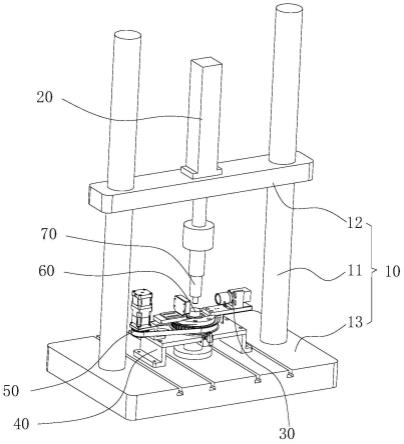
1.本发明属于塑料管道检测领域,特别是一种聚乙烯管材试样裂纹检测装置及检测方法。
背景技术:2.20世纪30年代以来,塑料管道作为生命线工程中的一种重要承压设备,市场应用越来越广泛。聚乙烯管材作为塑料管材中最重要的一种,以其优异的耐腐蚀性、高柔韧性、易维护性等特点,在生命线工程中以塑代钢得到广泛应用。欧洲的燃气管网中,聚乙烯管占90%以上;美国的的燃气管网中,聚乙烯管占95%以上。高密度聚乙烯管材的市场预计将以每年5%的速度增长,到2025年将达到265亿美元。城镇燃气管道一直贯穿人口密集地区,聚乙烯燃气管道作为承压类特种设备,一旦发生燃气泄漏,容易引发爆炸事故,给城市公共安全造成严重隐患。因此,聚乙烯管材的失效和寿命研究必然是材料生产厂家和燃气公司重点关注的问题。
3.聚乙烯管材的寿命与材料、环境和载荷等要素相关,其中材料包括树脂、添加剂、制造工艺等;环境包括气体、液体、紫外线辐射、放射性辐射、温度、白蚁、微生物等;载荷包括内部压力、外部静态/动态载荷、缺口、划痕等。现有疲劳裂纹扩展的试验方法中,如采用接触式引伸计方法通过测量张口位移间接测量裂纹扩展的速率,或者采用裂纹扩展的平均速率。前者成本比较高且采集数据量不多,后者精确度不高,都无法低成本的直接检测疲劳裂纹扩展的情况。
技术实现要素:4.本发明的目的在于改善现有技术的缺点,提供一种塑料试样裂纹检测装置和试样裂纹检测方法,通过试样的疲劳裂纹扩展测量,评估试样对应管道的剩余使用寿命。
5.实现上述目的包括如下技术方案。
6.试样裂纹检测装置包括支撑座、动力件、第一夹具、第二夹具和检测组件,所述动力件固定安装在所述支撑座上,所述第一夹具安装在所述支撑座上,所述第二夹具安装在所述动力件的动力输出部分,所述检测组件安装在支撑座上,所述检测组件的检测部分朝向所述第一夹具和所述第二夹具的连线。
7.在其中一些实施例中,所述检测组件包括第一检测件和第二检测件,所述第一检测件和所述第二检测件相对,且所述第一检测件和所述第二检测件的检测部分连线,穿过所述第一夹具和所述第二夹具的连线。
8.在其中一些实施例中,所述第一检测件为激光发射器,所述第二检测件为激光接收器,所述激光发射器发射区域对着所述激光接收器的接收区域。
9.在其中一些实施例中,所述第一检测件为可见光发射器,所述第二检测件为工业照相机,所述可见光发射器发射区域对着所述工业照相机的接收区域。
10.在其中一些实施例中,所述激光发射器发射的光源为面光源。
11.在其中一些实施例中,试样裂纹检测装置还包括安装座,所述安装座固定安装在所述支撑座上,所述检测组件安装在所述安装座上。
12.在其中一些实施例中,试样裂纹检测装置还包括旋转组件,所述旋转组件包括旋转座和旋转电机,所述旋转座转动安装在所述安装座上,且所述第一夹具或第二夹具在所述旋转座内部,所述检测组件安装在所述旋转座上,所述旋转电机驱动所述旋转座转动。
13.在其中一些实施例中,所述旋转组件包括第一驱动轮和第二驱动轮,所述第一驱动轮安装在所述旋转电机的动力输出位置,所述第二驱动轮安装在所述旋转座上,且所述第二驱动轮与所述旋转座转动轴同轴,所述第一驱动轮带动所述第二驱动轮转动。
14.在其中一些实施例中,所述旋转组件还包括架体,所述架体固定安装在所述旋转座上,所述检测组件安装在所述架体上。
15.在其中一些实施例中,所述支撑座包括座板、第一支撑杆和第二支撑杆,所述第一支撑杆固定安装在所述座板上,所述第二支撑杆固定连接在所述第一支撑杆上,所述动力件安装在所述第二支撑杆上。
16.试样裂纹检测方法,包括如下步骤:
17.试样安装在第一夹具和第二夹具上,并夹持好;
18.第一动力件启动,带动第二夹具运动,第二夹具运动带动试样动作;
19.检测组件启动,检测部分对着位于第一夹具和第二夹具上的试样,并对试样采集数据;
20.检测组件采集试样裂纹数据。
21.本发明所提供的技术方案具有以下的优点及效果:
22.使用时,将预备好的试样夹持在第一夹具和第二夹具之间,然后动力件启动,带动第二夹具往复移动,此时的试样在第二夹具的带动下做往复拉伸动作,此处的拉伸并非是距离为截止值,而是拉伸力值为截止值,试样在拉伸时达到设定的力值才停止一个拉伸动作,如此反复,检测试样的拉伸拉断的疲劳值。在循环载荷的试验过程中,通过检测组件检测试样在拉伸过程中裂纹的扩展,通过记录不同时间下的裂纹深度,计算出裂纹的扩展速率,用于预测试样的剩余使用寿命。比传统的试验方法节省了大量时间。
附图说明
23.图1是本发明实施例一的检测组件转动在第一状态立体结构示意图;
24.图2是本发明实施例一的检测组件转动在第二状态立体结构示意图;
25.图3是本发明实施例一的检测组件、旋转组件和安装座的拆分结构示意图;
26.图4是本发明实施例一的检测组件转动在第一状态的剖视结构示意图;
27.图5是本发明实施例一的图4中a处放大结构示意图;
28.图6是本发明实施例二检测组件转动在第一状态立体结构示意图;
29.图7是本发明实施例二检测组件转动在第二状态立体结构示意图。
30.附图标记说明:
31.10、支撑座;11、第一支撑杆;12、第二支撑杆;13、座板;20、动力件;30、检测组件;31、第一检测件;32、第二检测件;40、安装座;41、导轨;50、旋转组件;51、旋转座;511、导槽;52、旋转电机;53、第一驱动轮;54、第二驱动轮;55、架体;551、套筒;552、套杆;60、第一夹
具;70、第二夹具。
具体实施方式
32.为了便于理解本发明,下面将参照说明书附图对本发明的具体实施例进行更详细的描述。
33.除非特别说明或另有定义,本文所使用的“第一、第二
…”
仅仅是用于对名称的区分,不代表具体的数量或顺序。
34.除非特别说明或另有定义,本文所使用的术语“和/或”包括一个或多个相关的所列项目的任意的和所有的组合。
35.需要说明的是,当元件被认为“固定于”另一个元件,它可以是直接固定在另一个元件上,也可以是存在居中的元件。
36.实施例一:
37.如图1至图3所示,试样裂纹检测装置包括支撑座10、动力件20、第一夹具60、第二夹具70和检测组件30,所述动力件20固定安装在所述支撑座10上,所述第一夹具60安装在所述支撑座10上,所述第二夹具70安装在所述动力件20的动力输出部分,所述检测组件30安装在支撑座10上,所述检测组件30的检测部分朝向所述第一夹具60和所述第二夹具70的连线。
38.使用时,将预备好的试样夹持在第一夹具60和第二夹具70之间,然后动力件20启动,带动第二夹具70往复移动,此时的试样在第二夹具70的带动下做往复拉伸动作,此处的拉伸并非是距离为截止值,而是拉伸力值为截止值,试样在拉伸时达到设定的力值才停止一个拉伸动作,如此反复,检测试样的拉伸拉断的疲劳值。在循环载荷的试验过程中,通过检测组件30检测试样在拉伸过程中裂纹的扩展,通过记录不同时间下的裂纹深度,计算出裂纹的扩展速率,用于预测试样的剩余使用寿命。比传统的试验方法节省了大量时间。
39.此处为了实时获取拉力数值,在第一夹具60或者第二夹具70上安装力传感器,获取拉力大小,用于反馈控制动力件20的动作,如本实施例中,在第二夹具70上安装有力传感器。而第一夹具60和所述第二夹具70的连线即为试样夹取时所在位置。
40.如图3所示,所述检测组件30包括第一检测件31和第二检测件32,所述第一检测件31和所述第二检测件32相对,且所述第一检测件31和所述第二检测件32的检测部分连线,穿过所述第一夹具60和所述第二夹具70的连线。第一检测件31和第二检测件32相对,用于检测第一检测件31和第二检测件32之间的试样。
41.具体地,所述第一检测件31为可见光发射器,所述第二检测件32为工业照相机接收器,所述可见光发射器发射区域对着所述工业照相机接收器的接收区域。更进一步的,所述第一检测件31为激光发射器,所述第二检测件32为激光接收器,所述激光发射器发射区域对着所述激光接收器的接收区域。通过激光发生器发射激光,如果激光被阻挡,激光接收器的接收区域无法接收到该部分的光源,就记录下来,显示出此处的试样状态,如果试样此处有裂纹,光线就可以通过,最终根据激光接收的情况,还原出试样的裂纹情况。
42.因为试样在拉伸过程中,存在位移,所以即使产生了裂纹,裂纹也跟随试样的移动而移动,普通的线光源的激光捕获试样在移动过程中的裂纹扩展比较困难,此处所述激光发射器发射的光源为面光源,即产生的裂纹移动的幅度不大,可以通过激光发射器的面光
源捕获。无论试样怎么移动,只要裂纹是在激光面所覆盖的区域内移动,均可以捕获裂纹扩展的实时情况。
43.如图1和图2所示,试样裂纹检测装置还包括安装座40,所述安装座40固定安装在所述支撑座10上,所述检测组件30安装在所述安装座40上。安装座40可以独立安装在支撑座10上,然后将检测组件30安装好,提供给检测组件30一个合适的安装位置。
44.如图1至图3所示,试样裂纹检测装置还包括旋转组件50,所述旋转组件50包括旋转座51和旋转电机52,所述旋转座51转动安装在所述安装座40上,且所述第一夹具60或第二夹具70在所述旋转座51内部,所述检测组件30安装在所述旋转座51上,所述旋转电机52驱动所述旋转座51转动。具体将检测组件30安装在旋转座51上,通过旋转电机52的转动,带动旋转座51的转动,此时的检测组件30也跟随转动。因为检测组件30在检测裂纹时,通过检测激光的接收情况,确定是否有裂纹,此处检测为一个位置。由于试样裂纹的扩展是不确定的,所以在旋转座51的转动下,带动检测组件30转动,多角度检测裂纹扩展的位置,找到裂纹扩展最快的位置,此时就是需要记录的裂纹扩展位置,将检测组件30停留在该位置检测。此时通过旋转组件50带动检测组件30对着裂纹扩展最快的位置持续实时检测。
45.旋转座51上有避让的位置,避让旋转座51,而旋转电机52固定安装在安装座40上。
46.具体地,如图1所示,所述支撑座10包括座板13、第一支撑杆11和第二支撑杆12,所述第一支撑杆11固定安装在所述座板13上,所述第二支撑杆12固定连接在所述第一支撑杆11上,所述动力件20安装在所述第二支撑杆12上。此处第一支撑柱设置有两根,竖直安装在底板的两侧,第二支撑柱架设在两个第一支撑柱上。
47.此处的动力件20可以采用电机,如直线电机,也可以采用气缸驱动,具体在本实施例中,将采用直线电机。
48.如图3所示,所述旋转组件50还包括架体55,所述架体55固定安装在所述旋转座51上,所述检测组件30安装在所述架体55上。此处的架体55有两个,每个架体55呈180度角度安装在旋转座51上,第一检测件31和第二检测件32分别安装在两个架体55上。所以保证了第一检测件31和第二检测件32之间的位置关系。
49.如图3至图5所示,所述旋转组件50包括第一驱动轮53和第二驱动轮54,所述第一驱动轮53安装在所述旋转电机52的动力输出位置,所述第二驱动轮54安装在所述旋转座51上,且所述第二驱动轮54与所述旋转座51转动轴同轴,所述第一驱动轮53带动所述第二驱动轮54转动。此处的第一驱动轮53和第二驱动轮54均为皮带轮,第一驱动轮53和第二驱动轮54之间通过皮带关联,通过旋转电机52带动第一驱动轮53转动,进而带动第二驱动轮54转动,第二驱动轮54与旋转座51固定,所以旋转座51也跟随转动。此处的第一驱动轮53安装在旋转电机52的转动轴上。
50.如图3至图5所示,旋转座51包括内座和外座,外座与内座之间安装有轴承,内座套设在第一夹具60上。
51.根据高聚物材料线弹性断裂力学理论,裂纹发生稳定慢速裂纹扩展时,满足paris和erdogan提出幂律关系:
[0052][0053]
其中da/dt为缺口试样裂纹扩展速率;ki为应力强度因子;a,m为材料参数。
[0054]
通过采用循环载荷裂纹圆棒(crb)试验,裂纹圆棒即塑料试样,测量聚乙烯材料在
不同载荷比条件下,缺口圆柱棒试样的疲劳失效周期nf与初始裂纹深度a
ini
的对应关系,然后通过计算得到慢速裂纹扩展速率da/dt与应强度因子ki的对应关系,通过外推法,得到静载(r=1)条件下,聚乙烯材料的固有参数a和m,最后通过公式(1),可以得到含初始裂纹缺陷的pe管材的使用寿命tf的表达式为:
[0055][0056]
式中,a
ini
和af为含缺陷管道的初始裂纹和最终裂纹深度;k
pipe
管材为裂纹尖端的应力强度因子(由缺陷类型、管内压σ
hoop
和裂纹深度a共同决定)。
[0057]
试样裂纹检测方法包括如下步骤:试样安装在第一夹具60和第二夹具70上,并夹持好;第一动力件20启动,带动第二夹具70运动,第二夹具70运动带动试样动作;检测组件30启动,检测部分对着位于第一夹具60和第二夹具70上的试样,并对试样采集数据;检测组件30采集试样裂纹数据。
[0058]
实施例二:
[0059]
如图6和图7所示,安装座40上设置有导轨41,旋转座51上对应位置设置有导槽511,利用导轨41导槽511配合,旋转座51的转动时的转动轨迹固定。本实施例中,将第二驱动轮54的作用合成在旋转座51上,旋转座51的外侧边缘设置齿牙,第一驱动轮53为齿轮,固定安装在旋转电机52转动轴上,此处的旋转电机52与旋转座51之间的动力传递通过齿轮的齿牙啮合,采用直接啮合的方式,可以提高动力传递的精度。
[0060]
在本实施例中,架体55包括套筒551和套杆552,将套筒551固定在旋转座51上,套杆552顶部固定第一检测件31或第二检测件32,此处可以通过上下移动套杆552控制第一检测件31和第二检测件32的上下位置,可以针对不同的试样检测,而且还能调节第一检测件31和第二检测件32之间的相对高度。当然此处也可以将套杆552固定在旋转座51上,套筒551用于固定第一检测件31或第二检测件32。
[0061]
引用图纸说明时,是对出现的新特征进行说明;为了避免重复引用图纸导致描述不够简洁,在表述清楚的情况下已描述的特征,图纸不再一一引用。
[0062]
以上实施例也并非是基于本发明的穷尽性列举,在此之外,还可以存在多个未列出的其他实施方式。在不违反本发明构思的基础上所作的任何替换与改进,均属本发明的保护范围。