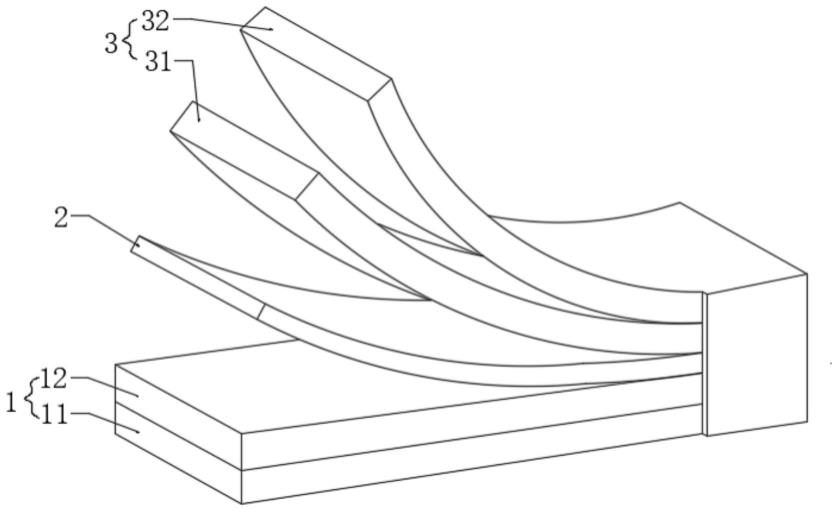
1.本发明属于柔性电子器件领域,具体涉及一种微裂纹应变传感器及其制备方法,特别是涉及一种基于柔性基底层-脆性导电层的微裂纹应变传感器及其制备方法。
背景技术:2.在可穿戴智能设备领域、植入式电子器件领域以及智能机器人领域,柔性应变传感器均是至关重要的器件之一;它可以将应变转化为电学信号,并进一步转化为数字信号输出。相比于由金属或半导体制备得到的传统硬质传感器,柔性应变传感器可以任意变换形状,贴合在皮肤表面或智能机器人表面的任意位置,因此柔性应变传感器的适用环境更广。另外,柔性应变传感器的应变响应范围,以及gf值(单位应变下的电阻变化率,常作为评价应变传感性能的标准之一)均要优于传统硬质传感器,因此近年来关于柔性应变传感器的研究络绎不绝。其中,制备柔性应变传感器最常见的方法是将柔性聚合物基体与导电填料共混均匀,导电填料在柔性聚合物基体中构成导电通路。当复合材料被施加应变后导电通路被破坏,复合材料的电阻急剧上升,因此具有较好的应变传感性能。然而,此种方式制备的柔性应变传感器通常需要在较大的应变下(》100%)才有较高的gf值(5~500)。
3.专利cn 113930037 a对纳米金属/石墨烯进行改性,在其表面接枝氨基,而氨基与基体改性聚乙烯醇中的羧基发生缩合反应。这一方法改善了纳米金属/石墨烯在改性聚乙烯醇基体中的分散程度,分散均匀的导电填料网络更易在应变中被破坏,因此复合材料具有良好的应变传感性能(在80%应变下的gf值为7左右)。同时,导电填料与聚合物基体间的化学键合使得复合材料在循环拉伸过程中具有良好的稳定性和抗疲劳性。然而,在实际应用过程中常常需要应变传感器对更细微的应变产生足够大的信号,这是导电复合材料类型的应变传感器所无法达到的。
4.从蜘蛛腿可以感应到蛛网传来的微弱信号获取灵感,近年来科学家设计了微裂纹结构的应变传感器,即在柔性基层表面溅射或喷涂一层纳米级的金属薄膜,并采用弯曲或拉伸的方式,使金属薄膜表面形成均匀的微裂纹。在拉伸过程中,金属薄膜微裂纹的扩展会导致裂纹处的金属薄膜厚度减小,进而使得应变传感器的电阻急剧升高。在极低应变下(《5%)的gf值即可高达(2000~80000)。专利cn 113310395 a将带有相应镂空形状的镀膜模板放置于基底层上,并将两种金属沉积在模板中。在未沉积金属的部分采用模板涂敷一层保护层。这种方式制备的微裂纹应变传感器具有更高精度的裂纹,且不会影响裂纹在应变过程中的使用寿命。然而,现有的微裂纹应变传感器具有一个本质的缺陷,即在大应变下微裂纹结构会遭到不可逆破坏,因此难以应用于复杂的实际应用环境。
技术实现要素:5.为此,本发明的目的是针对现有技术存在的问题,提供一种在较低应变下具有更加优异应变传感性能,且具有良好环境适应性的新型微裂纹应变传感器。
6.本发明是通过以下技术方案来实现的:
7.一种微裂纹应变传感器,包括柔性基底层、脆性导电薄膜裂纹层和柔性封装层;按质量份数计,其原料配方组成包括:柔性基底材料50~90份;弹性体交联剂0~5份;弹性体交联助剂0~10份;脆性薄膜材料1~5份;导电填料0.01~0.5份;界面改性剂0~3份;所述的柔性基底材料为热固性弹性体、热塑性弹性体、柔性薄膜中的一种或多种;所述的脆性薄膜材料为羧甲基壳聚糖、羧甲基纤维素、羧甲基纤维素钠、聚乙烯醇、乙烯-醋酸乙烯共聚物、醋酸纤维素、乙基纤维素、聚丙烯酰胺、聚甲基丙烯酸甲酯、聚氯乙烯和聚碳酸脂中的一种或多种;所述的导电填料为碳纳米管、石墨烯、导电炭黑、纳米银线、聚(3,4-亚乙二氧基噻吩)、聚乙炔、聚苯胺中的一种或多种。
8.进一步优选的,所述的热固性弹性体为天然橡胶、天然橡胶胶乳、环氧化天然橡胶、环氧化天然橡胶胶乳、乙丙橡胶、硅橡胶、氟橡胶、丁腈橡胶、丁腈橡胶胶乳、羧基丁腈橡胶胶乳、丁苯橡胶、丁苯橡胶胶乳、羧基丁苯橡胶胶乳、杜仲胶乳和蒲公英胶乳中的一种或多种,所述的热塑性弹性体为苯乙烯-丁二烯嵌段共聚物、乙烯-辛烯共聚物、聚氨酯弹性体和聚酰胺弹性体中的一种或多种。
9.进一步优选的,所述的柔性薄膜材料为聚酰亚胺、聚酯、环烯烃聚合物和液晶聚合物中的一种或多种。
10.进一步优选的,所述弹性体交联剂为硫黄硫化剂、过氧化物硫化剂、硅氢加成交联剂、胺类硫化剂和双酚类硫化剂中的一种或多种。
11.进一步优选的,所述的弹性体交联助剂为氧化锌、噻唑类促进剂、次硫酰胺类促进剂、秋兰姆类促进剂、硫代甲酸盐类促进剂、胍类促进剂、双酚类促进剂、季铵盐促进剂、季磷盐促进剂、氰脲酸酯类促进剂和过渡金属配位类促进剂中的一种或多种。
12.进一步优选的,所述的碳纳米管为单壁碳纳米管和多壁碳纳米管中的一种或多种;所述的导电炭黑为油炉法导电炭黑、重油复产导电炭黑和电石乙炔导电炭黑中的一种或多种。
13.进一步优选的,所述的界面改性剂为硅烷偶联剂、钛酸酯偶联剂、铝酸酯偶联剂、铝钛复合偶联剂、阴离子表面活性剂、阳离子表面活性剂和非离子表面活性剂中的一种或多种。
14.本发明还提供所述微裂纹应变传感器的制备方法,包括如下步骤:
15.a)获得柔性基底层,所述柔性基底层为柔性薄膜或弹性体薄膜、或为柔性薄膜-弹性体薄膜复合柔性基底层;所述弹性体薄膜的制备方法为:在热固性弹性体胶乳或热固性弹性体溶液或热塑性弹性体溶液中依次加入弹性体交联剂、或弹性体交联剂与弹性体交联助剂、或弹性体交联剂与弹性体交联助剂及界面改性剂,混合均匀后,进行成型得到所述弹性体薄膜。
16.b)脆性导电薄膜裂纹层的制备,方法如下:
17.i)将脆性薄膜材料溶解在溶剂中,得到脆性薄膜材料的溶液。
18.ii)将导电填料或导电填料及界面改性剂在超声作用下分散于脆性薄膜材料的溶液中,得到导电填料-脆性薄膜材料悬浮液。
19.iii)将步骤ii)得到导电填料-脆性薄膜材料悬浮液分次涂敷在柔性基底层表面,并加热烘干,在柔性基底层表面形成一层脆性导电薄膜层。
20.iv)采用预弯曲或拉伸的方式,使得步骤iii)制得的脆性导电薄膜层形成均匀的
裂纹,得到脆性导电薄膜裂纹层。
21.c)重复步骤a),得到柔性基底层并将其覆盖在导电薄膜裂纹层表面作为柔性封装层封闭导电薄膜裂纹层,得到所述微裂纹应变传感器。
22.进一步优选的,步骤a)与步骤b)之间还包括对所述柔性基底层进行表面处理,表面处理方法为电镀、化学镀、电泳、化学热处理、臭氧、等离子和激光表面处理中的一种或多种。步骤iv)后还包括将导电铜片引入脆性导电薄膜裂纹层作为输出电极,步骤c)后还包括将输出电极引出所述柔性封装层。
23.进一步优选的,步骤ii)所述的超声作用时间为0.1~2小时,超声作用功率为100~10000w;步骤iv)所述的弯曲曲率半径为1~5mm,拉伸速率为50~2000cm/min。
24.进一步优选的,上述制备的微裂纹应变传感器对拉伸或压缩造成的平面内的应变最为敏感。对于按压等垂直或一定角度倾斜于微裂纹应变传感器的应变,所述微裂纹应变传感器的制备方法还可以增加步骤d):将步骤c)制备得到的微裂纹应变传感器两端固定,中间悬空,得到弧型结构的弧状微裂纹应变传感器,这一结构能使得微裂纹应变传感器垂直或一定角度倾斜方向的应变转化为水平面内的应变,使弧状微裂纹应变传感器对垂直或一定角度倾斜方向的应变具有高敏感性。
25.有益效果:
26.本发明的基于柔性基底层-脆性导电层的微裂纹应变传感器,其gf值最高可达400000以上。且微裂纹应变传感器的应变响应范围可调(最小响应应变低至1%,最大响应应变高达100%),以适应不同的应用场景。
27.本发明的基于柔性基底层-脆性导电层的微裂纹应变传感器,在经受大应变或循环应变后,仍能保持较佳的应变传感性能,具有良好的稳定性。
28.本发明的基于柔性基底层-脆性导电层的微裂纹应变传感器,制备过程简单,便于大规模生产。且制备所得的微裂纹应变传感器体积小质量轻,适用于可穿戴智能设备。
29.本发明的基于柔性基底层-脆性导电层的微裂纹应变传感器具有极高的gf值和可调控的应变响应范围。即使在很低的电压下,仍能输出极大的电流变化信号(工作电压为1.5v时,即可检测电流的显著变化),因此适用于低压环境,提高了应变传感器的安全性,降低了应变传感器的能耗。适用于低电压环境的可穿戴智能设备、航空航天等领域。
附图说明
30.图1为实施例10提供的微裂纹应变传感器的结构示意图;
31.图2为本发明提供的弧状微裂纹传感器的结构及工作原理示意图;
32.图3为本发明的微裂纹应变传感器的工作原理图;
33.图4a)为实施例2提供的微裂纹应变传感器的脆性导电薄膜裂纹层初始状态时的扫描电镜图片;
34.图4b)为实施例2提供的微裂纹应变传感器的脆性导电薄膜裂纹层在50%应变时的扫描电镜图片;
35.图5为实施例4的微裂纹应变传感器在不同应变下的3维扫描截面曲线:a)0%应变;b)5%应变;c)50%应变;d)图c)的放大图;
36.图6为实施例4的微裂纹应变传感器在不同应变下的3维扫描图;
37.图7为实施例9的微裂纹应变传感器的电阻变化率-应变曲线图;
38.图8a)与图8b)分别为实施例5的微裂纹应变传感器在50%与100%循环应变下的电阻率变化曲线。
具体实施方式
39.为更好地理解本发明,下面结合附图和实施例对本发明做进一步的描述,但需要说明的是,实施例并不构成对本发明要求保护范围的限定。
40.本发明提供一种微裂纹应变传感器,包括柔性基底层、脆性导电薄膜裂纹层和柔性封装层;按质量份数计,其原料配方组成包括:柔性基底材料50~90份,弹性体交联剂0~5份;弹性体交联助剂0~10份;脆性薄膜材料1~5份;导电填料0.01~0.5份;界面改性剂0~3份。
41.所述的柔性基底材料为热固性弹性体、热塑性弹性体、柔性薄膜中的一种或多种;所述的脆性薄膜材料为羧甲基壳聚糖、羧甲基纤维素、羧甲基纤维素钠、聚乙烯醇、乙烯-醋酸乙烯共聚物、醋酸纤维素、乙基纤维素、聚丙烯酰胺、聚甲基丙烯酸甲酯、聚氯乙烯和聚碳酸脂中的一种或多种;所述的导电填料为碳纳米管、石墨烯、导电炭黑、纳米银线、聚(3,4-亚乙二氧基噻吩)、聚乙炔、聚苯胺中的一种或多种;所述的热固性弹性体为天然橡胶、天然橡胶胶乳、环氧化天然橡胶、环氧化天然橡胶胶乳、乙丙橡胶、硅橡胶、氟橡胶、丁腈橡胶、丁腈橡胶胶乳、羧基丁腈橡胶胶乳、丁苯橡胶、丁苯橡胶胶乳、羧基丁苯橡胶胶乳、杜仲胶乳和蒲公英胶乳中的一种或多种,所述的热塑性弹性体为苯乙烯-丁二烯嵌段共聚物、乙烯-辛烯共聚物、聚氨酯弹性体和聚酰胺弹性体中的一种或多种。
42.所述的柔性薄膜的材料为聚酰亚胺、聚酯、环烯烃聚合物和液晶聚合物中的一种或多种。
43.所述弹性体交联剂为硫黄硫化剂、过氧化物硫化剂、硅氢加成交联剂、胺类硫化剂和双酚类硫化剂中的一种或多种。
44.所述的弹性体交联助剂为氧化锌、噻唑类促进剂、次硫酰胺类促进剂、秋兰姆类促进剂、硫代甲酸盐类促进剂、胍类促进剂、双酚类促进剂、季铵盐促进剂、季磷盐促进剂、氰脲酸酯类促进剂和过渡金属配位类促进剂中的一种或多种。
45.所述的碳纳米管为单壁碳纳米管和多壁碳纳米管中的一种或多种;所述的导电炭黑为油炉法导电炭黑、重油复产导电炭黑和电石乙炔导电炭黑中的一种或多种。
46.所述的界面改性剂为硅烷偶联剂、钛酸酯偶联剂、铝酸酯偶联剂、铝钛复合偶联剂、阴离子表面活性剂、阳离子表面活性剂和非离子表面活性剂中的一种或多种。
47.本发明还提供所述微裂纹应变传感器的制备方法,包括如下步骤:
48.a)获得柔性基底层,所述柔性基底层为柔性薄膜或弹性体薄膜、或为柔性薄膜-弹性体薄膜复合柔性基底层;所述弹性体薄膜的制备方法为:在热固性弹性体胶乳或热固性弹性体溶液或热塑性弹性体溶液中依次加入弹性体交联剂、或弹性体交联剂与弹性体交联助剂、或弹性体交联剂与弹性体交联助剂及界面改性剂,混合均匀后,进行成型得到所述弹性体薄膜。即在一些实施例中以市面上的柔性薄膜为柔性基底层,也可以弹性体薄膜为柔性基底层,也可以层叠的柔性薄膜和弹性体薄膜构成柔性薄膜-弹性体薄膜复合柔性基底层为柔性基底层。
49.b)脆性导电薄膜裂纹层的制备,方法如下:
50.i)将脆性薄膜材料溶解在溶剂中,得到脆性薄膜材料的溶液。
51.ii)将导电填料或导电填料及界面改性剂在超声作用下分散于脆性薄膜材料的溶液中,得到导电填料-脆性薄膜材料悬浮液。
52.iii)将ii)中的溶液分次涂敷在柔性基底层表面,并加热烘干,在柔性基底层表面形成一层脆性导电薄膜层。
53.iv)采用弯曲或拉伸的方式,使得iii)中的脆性导电薄膜层上形成均匀的裂纹,得到脆性导电薄膜裂纹层。
54.c)重复步骤a),得到柔性基底层并将其覆盖在导电薄膜裂纹层表面作为柔性封装层封闭导电薄膜裂纹层,得到所述微裂纹应变传感器。
55.在一些实施例中,步骤a)与步骤b)之间还包括对所述柔性基底层进行表面处理,表面处理方法为电/化学镀、电泳、化学热处理、臭氧、等离子和激光表面处理中的一种或多种。步骤iv)后还包括将导电铜片引入脆性导电薄膜裂纹层作为输出电极,步骤c)后还包括将输出电极引出所述柔性封装层。
56.进一步优选的,步骤ii)所述的超声作用时间为0.1~2小时,超声作用功率为100~10000w;步骤iv)所述的弯曲曲率半径为1~5mm,拉伸速率为50~2000cm/min。
57.上述制备的微裂纹应变传感器可为层叠的条状传感器,其对任一方向的应变均可响应,尤其对拉伸或压缩造成的水平面内的应变最为敏感,但对于按压等垂直或一定角度倾斜于微裂纹应变传感器的应变的敏感度相对较低。因此进一步的,对于垂直方向按压微裂纹应变传感器等的应变,所述微裂纹应变传感器的制备方法还可以增加步骤d):将步骤c)制备得到的微裂纹应变传感器两端固定,中间悬空,制得弧型结构的微裂纹应变传感器,这一结构能将对弧状微裂纹应变传感器垂直或一定倾斜角度的应变转化为水平面内的应变,从而提高微裂纹应变传感器对垂直或一定倾斜角度应变的敏感度。所述弧状微裂纹应变传感器受到按压等垂直方向应变时的工作原理如图2所示。同理,还可以的,以一定倾斜角按压弧状微裂纹应变传感器时,所述弧型微裂纹应变传感器同样能将倾斜方向的应变转化为水平面内的应变,因此弧型微裂纹应变传感器同样可以提高对倾斜方向应变的敏感度。
58.实施例1
59.本实施例提供一种微裂纹应变传感器,包括从下至上依次层叠的柔性基底层、脆性导电薄膜裂纹层和柔性封装层,其制备方法如下:
60.选取环氧度为30%的环氧化天然橡胶胶乳为柔性基底材料,弹性体交联剂为硫黄,弹性体交联助剂为氧化锌和二乙基二硫代氨基甲酸锌(zdec),脆性薄膜材料为羧甲基壳聚糖,导电填料为单壁碳纳米管。向环氧化天然橡胶胶乳中加入2phr的硫黄,1phr的zdec,0.5phr的氧化锌,采用超声设备对胶乳超声处理0.5h,使硫化体系均匀分散在胶乳中得到含硫化体系的环氧化天然橡胶胶乳。将2g含硫化体系的环氧化天然橡胶胶乳加入30cm*30cm*2cm的聚四氟乙烯模具中,使其铺展均匀。将模具放入80℃烘箱中干燥、硫化2h制得柔性基底层。将0.1g羧甲基壳聚糖溶解在10ml去离子水中,并加入0.001g单壁碳纳米管(单壁碳纳米管为羧甲基壳聚糖质量的1%),超声处理0.5h得到均匀分散的单壁碳纳米管悬浮液。将悬浮液分4次加入聚四氟乙烯模具中,在烘箱中60℃干燥8h制得脆性导电薄膜
层。采用预弯曲(曲率半径为1mm)的方式制造微裂纹,得到脆性导电薄膜裂纹层,并将导电铜片引入脆性导电薄膜裂纹层作为输出电极。将1g含硫化体系的环氧化天然橡胶胶乳加入模具中80℃干燥、硫化2h作为柔性封装层封闭导电薄膜裂纹层,将输出电极引出所述柔性封装层。
61.实施例2
62.本实施例提供一种微裂纹应变传感器,包括从下至上依次层叠的柔性基底层、脆性导电薄膜裂纹层和柔性封装层,其制备方法如下:
63.选取环氧度为10%的环氧化天然橡胶胶乳为柔性基底材料,弹性体交联剂为硫黄,弹性体交联助剂为氧化锌和二乙基二硫代氨基甲酸锌(zdec),脆性薄膜材料为羧甲基壳聚糖,导电填料为单壁碳纳米管。向环氧化天然橡胶胶乳中加入2phr的硫黄,1phr的zdec,0.5phr的氧化锌,采用超声设备对胶乳超声处理0.5h,使硫化体系均匀分散在胶乳中得到含硫化体系的环氧化天然橡胶胶乳。将2g含硫化体系的环氧化天然橡胶胶乳加入20cm*20cm*2cm的聚四氟乙烯模具中,使其铺展均匀。将模具放入80℃烘箱中干燥、硫化2h制得柔性基底层。将0.1g羧甲基壳聚糖溶解在10ml去离子水中,并加入0.001g单壁碳纳米管(单壁碳纳米管为羧甲基壳聚糖质量的1%),超声处理0.5h得到均匀分散的单壁碳纳米管悬浮液。将悬浮液分4次加入模具中,在烘箱中60℃干燥8h制得脆性导电薄膜层。采用预弯曲(曲率半径为1mm)的方式制造微裂纹,得到脆性导电薄膜裂纹层,并将导电铜片引入脆性导电薄膜裂纹层作为输出电极。将1g含硫化体系的环氧化天然橡胶胶乳加入模具中80℃干燥、硫化2h作为柔性封装层封闭导电薄膜裂纹层,将输出电极引出所述柔性封装层。
64.实施例3
65.本实施例提供一种微裂纹应变传感器,包括从下至上依次层叠的柔性基底层、脆性导电薄膜裂纹层和柔性封装层,其制备方法如下:
66.选取羧基含量为1%的羧基丁苯橡胶胶乳为柔性基底材料,弹性体交联剂为硫黄,弹性体交联助剂为氧化锌和二乙基二硫代氨基甲酸锌(zdec),脆性薄膜材料为羧甲基壳聚糖,导电填料为单壁碳纳米管。向羧基丁苯橡胶胶乳中加入2phr的硫黄,1phr的zdec,0.5phr的氧化锌,采用超声设备对胶乳超声处理0.5h,使硫化体系均匀分散在胶乳中得到含硫化体系的羧基丁苯橡胶胶乳。将2g含硫化体系的羧基丁苯橡胶胶乳加入30cm*30cm*2cm的聚四氟乙烯模具中,使其铺展均匀。将模具放入80℃烘箱中干燥、硫化2h制得柔性基底层。将0.1g羧甲基壳聚糖溶解在10ml去离子水中,并加入0.001g单壁碳纳米管(单壁碳纳米管为羧甲基壳聚糖质量的1%),超声处理0.5h得到均匀分散的单壁碳纳米管悬浮液。将悬浮液分4次加入模具中,在烘箱中60℃干燥8h制得脆性导电薄膜层。采用预弯曲(曲率半径为1mm)的方式制造微裂纹,得到脆性导电薄膜裂纹层,并将导电铜片引入脆性导电薄膜裂纹层作为输出电极。将1g含硫化体系的羧基丁苯橡胶胶乳加入模具中80℃干燥、硫化2h作为柔性封装层封闭导电薄膜裂纹层,将输出电极引出所述柔性封装层。
67.实施例4
68.本实施例提供一种微裂纹应变传感器,包括从下至上依次层叠的柔性基底层、脆性导电薄膜裂纹层和柔性封装层,其制备方法如下:
69.选取环氧度为30%的环氧化天然橡胶胶乳为柔性基底材料,弹性体交联剂为硫黄,弹性体交联助剂为氧化锌和二乙基二硫代氨基甲酸锌(zdec),脆性薄膜材料为羧甲基
纤维素钠,导电填料为单壁碳纳米管。向环氧化天然橡胶胶乳中加入2phr的硫黄,1phr的zdec,0.5phr的氧化锌,采用超声设备对胶乳超声处理0.5h,使硫化体系均匀分散在胶乳中得到含硫化体系的环氧化天然橡胶胶乳。将2g含硫化体系的环氧化天然橡胶胶乳加入10cm*10cm*2cm的聚四氟乙烯模具中,使其铺展均匀。将模具放入80℃烘箱中干燥、硫化2h制得柔性基底层。将0.1g羧甲基纤维素钠溶解在10ml去离子水中,并加入0.001g单壁碳纳米管(单壁碳纳米管为羧甲基纤维素钠质量的1%),超声处理0.5h得到均匀分散的单壁碳纳米管悬浮液。将悬浮液分4次加入模具中,在烘箱中60℃干燥8h制得脆性导电薄膜层。采用预弯曲(曲率半径为1mm)的方式制造微裂纹,得到脆性导电薄膜裂纹层,并将导电铜片引入脆性导电薄膜裂纹层作为输出电极。将1g含硫化体系的环氧化天然橡胶胶乳加入模具中80℃干燥、硫化2h作为柔性封装层封闭导电薄膜裂纹层,将输出电极引出所述柔性封装层。
70.实施例5
71.本实施例提供一种微裂纹应变传感器,包括从下至上依次层叠的柔性基底层、脆性导电薄膜裂纹层和柔性封装层,其制备方法如下:
72.选取环氧度为30%的环氧化天然橡胶胶乳为柔性基底材料,弹性体交联剂为硫黄,弹性体交联助剂为氧化锌和二乙基二硫代氨基甲酸锌(zdec),脆性薄膜材料为羧甲基壳聚糖,导电填料为单壁碳纳米管。向环氧化天然橡胶胶乳中加入2phr的硫黄,1phr的zdec,0.5phr的氧化锌,采用超声设备对胶乳超声处理0.5h,使硫化体系均匀分散在胶乳中得到含硫化体系的环氧化天然橡胶胶乳。将2g含硫化体系的环氧化天然橡胶胶乳加入6cm*6cm*2cm的聚四氟乙烯模具中,使其铺展均匀。将模具放入80℃烘箱中干燥、硫化2h制得柔性基底层。将0.1g羧甲基壳聚糖溶解在10ml去离子水中,并加入0.01g聚(3,4-亚乙二氧基噻吩)(聚(3,4-亚乙二氧基噻吩)为羧甲基壳聚糖质量的10%),超声处理0.5h得到均匀分散的聚(3,4-亚乙二氧基噻吩)悬浮液。将悬浮液分4次加入模具中,在烘箱中60℃干燥8h制得脆性导电薄膜层。采用预弯曲(曲率半径为1mm)的方式制造微裂纹,得到脆性导电薄膜裂纹层,并将导电铜片引入脆性导电薄膜裂纹层作为输出电极。将1g含硫化体系的环氧化天然橡胶胶乳加入模具中80℃干燥、硫化2h作为柔性封装层封闭导电薄膜裂纹层,将输出电极引出所述柔性封装层。
73.实施例6
74.本实施例提供一种微裂纹应变传感器,包括从下至上依次层叠的柔性基底层、脆性导电薄膜裂纹层和柔性封装层,其制备方法如下:
75.选取硅橡胶为柔性基底材料,弹性体交联剂为过氧化二异丙苯,脆性薄膜材料为羧甲基壳聚糖,导电填料为纳米银线。将硅橡胶溶解在二氯甲烷溶剂中,加入2phr弹性体交联剂过氧化二异丙苯使其均匀分散在硅橡胶溶液中得到含硫化体系的硅橡胶溶液。将2g含硫化体系的硅橡胶溶液加入6cm*6cm*2cm的聚四氟乙烯模具中,使其铺展均匀。将模具放入160℃烘箱中干燥、硫化2h制得柔性基底层。将0.1g羧甲基壳聚糖溶解在10ml去离子水中,并加入0.001g纳米银线(纳米银线为羧甲基壳聚糖质量的1%),超声处理0.5h得到均匀分散的纳米银线悬浮液。将悬浮液分4次加入模具中,在烘箱中60℃干燥8h制得脆性导电薄膜层。采用预弯曲(曲率半径为1mm)的方式制造微裂纹,得到脆性导电薄膜裂纹层,并将导电铜片引入脆性导电薄膜裂纹层作为输出电极。将1g含硫化体系的硅橡胶溶液加入模具中160℃干燥、硫化2h作为柔性封装层封闭导电薄膜裂纹层,将输出电极引出所述柔性封装
层。
76.实施例7
77.本实施例提供一种微裂纹应变传感器,包括从下至上依次层叠的柔性基底层、脆性导电薄膜裂纹层和柔性封装层,其制备方法如下:
78.选取羧基丁腈橡胶为柔性基底材料,弹性体交联剂为过氧化二异丙苯,脆性薄膜材料为羧甲基壳聚糖,导电填料为聚苯胺,界面改性剂为硅烷偶联剂双-[3-(三乙氧基硅)丙基]-四硫化物(tespt)。将羧基丁腈橡胶溶解在溶剂中,并加入2phr的过氧化二异丙苯,采用超声设备对溶液超声处理0.5h,使硫化体系均匀分散在羧基丁腈橡胶溶液中得到含硫化体系的羧基丁腈橡胶溶液。将2g含硫化体系的羧基丁腈橡胶溶液加入6cm*6cm*2cm的聚四氟乙烯模具中,使其铺展均匀。将模具放入160℃烘箱中干燥、硫化2h制得柔性基底层。采用tespt对柔性基底层进行表面处理。将0.1g羧甲基壳聚糖溶解在100ml的二甲基甲酰胺(dmf)中,并加入0.01g聚苯胺(聚苯胺为羧甲基壳聚糖质量的10%),超声处理0.5h得到聚苯胺-羧甲基壳聚糖溶液。将溶液分4次加入模具中,在烘箱中60℃干燥8h制得脆性导电薄膜层。采用预弯曲(曲率半径为1mm)的方式制造微裂纹,得到脆性导电薄膜裂纹层,并将导电铜片引入脆性导电薄膜裂纹层作为输出电极。将1g含硫化体系的羧基丁腈橡胶溶液加入模具中160℃干燥、硫化2h作为柔性封装层封闭导电薄膜裂纹层,将输出电极引出所述柔性封装层。
[0079]
实施例8
[0080]
本实施例提供一种微裂纹应变传感器,包括从下至上依次层叠的柔性基底层、脆性导电薄膜裂纹层和柔性封装层,其制备方法如下:
[0081]
选取商业化聚酯薄膜为柔性基底层,脆性薄膜材料为聚丙烯酰胺,导电填料为单壁碳纳米管。将0.1g聚丙烯酰胺溶解在10ml去离子水中,并加入0.001g单壁碳纳米管(单壁碳纳米管为聚丙烯酰胺质量的1%),超声处理0.5h得到均匀分散的单壁碳纳米管悬浮液。将悬浮液分4次喷涂在聚酯薄膜表面,在烘箱中60℃干燥8h制得脆性导电薄膜层。采用预拉伸(拉伸速率为500mm/min)的方式制造微裂纹,得到脆性导电薄膜裂纹层,并将导电铜片引入脆性导电薄膜裂纹层作为输出电极。将聚酯薄膜覆盖在脆性导电薄膜裂纹层表面作为柔性封装层封闭导电薄膜裂纹层,将输出电极引出所述柔性封装层。
[0082]
实施例9
[0083]
本实施例提供一种微裂纹应变传感器,包括从下至上依次层叠的柔性基底层、脆性导电薄膜裂纹层和柔性封装层,其制备方法如下:
[0084]
选用商业化聚酰亚胺薄膜为柔性基底层,脆性薄膜材料为醋酸纤维素,导电填料为多壁碳纳米管,界面改性剂为阴离子表面活性剂十二烷基苯磺酸钠。首先采用十二烷基苯磺酸钠对聚酰亚胺薄膜进行表面处理。将0.1g醋酸纤维素溶解在10ml去离子水中,并加入0.002g多壁碳纳米管(多壁碳纳米管为聚丙烯酰胺质量的2%),超声处理0.5h得到均匀分散的多壁碳纳米管悬浮液。将悬浮液分4次喷涂在聚酯薄膜表面,在烘箱中60℃干燥8h制得脆性导电薄膜层。采用预拉伸(拉伸速率为500mm/min)的方式制造微裂纹,得到脆性导电薄膜裂纹层,并将导电铜片引入脆性导电薄膜裂纹层作为输出电极。将表面处理过的聚酯薄膜覆盖在脆性导电薄膜裂纹层表面作为柔性封装层封闭导电薄膜裂纹层,将输出电极引出所述柔性封装层。
[0085]
实施例10
[0086]
本实施例提供一种微裂纹应变传感器,如图1所示,包括从下至上依次层叠的柔性基底层1、脆性导电薄膜裂纹层2和柔性封装层3,柔性基底层1包括从下至上层叠的柔性薄膜层11和弹性体薄膜层12,如图3所示,所述脆性导电薄膜裂纹层包括本体层21和过渡层22,所述柔性封装层3包括从下至上层叠的弹性体薄膜封装层31和柔性薄膜封装层32,所述微裂纹应变传感器制备方法如下:
[0087]
选取环氧度为30%的环氧化天然橡胶胶乳和聚酰亚胺薄膜作为柔性基底材料,弹性体交联剂为硫黄,弹性体交联助剂为氧化锌和二乙基二硫代氨基甲酸锌(zdec),脆性薄膜材料为羧甲基壳聚糖,导电填料为单壁碳纳米管,界面改性剂为硅烷偶联剂γ-甲基丙烯酰氧基丙基三甲氧基硅烷(kh570)。向环氧化天然橡胶胶乳中加入2phr的硫黄,1phr的zdec,0.5phr的氧化锌,2phr的kh570。采用超声设备对胶乳超声处理0.5h,使硫化体系和界面改性剂均匀分散在胶乳中得到含硫化体系和界面改性剂的环氧化天然橡胶胶乳。将2g含硫化体系和界面改性剂的环氧化天然橡胶胶乳涂敷在聚酰亚胺薄膜表面并将其放入80℃烘箱中干燥、硫化2h制得从下至上层叠的柔性薄膜层11和弹性体薄膜层12,作为柔性基底层1。对柔性基底层上表面进行电镀处理。将0.1g羧甲基壳聚糖溶解在10ml去离子水中,并加入0.001g单壁碳纳米管(单壁碳纳米管为羧甲基壳聚糖质量的1%)和1phr的kh570,超声处理0.5h得到均匀分散的单壁碳纳米管悬浮液。将悬浮液分4次加入模具中,在烘箱中60℃干燥8h制得脆性导电薄膜层。采用预弯曲(曲率半径为1mm)的方式制造微裂纹,得到脆性导电薄膜裂纹层2,并将导电铜片引入脆性导电薄膜裂纹层2作为输出电极(图未示)。并将1g含硫化体系和界面改性剂的环氧化天然橡胶胶乳涂敷在聚酰亚胺薄膜表面并置于烘箱中80℃干燥、硫化2h得到聚酰亚胺薄膜-环氧化天然橡胶胶乳薄膜复合层,将聚酰亚胺薄膜-环氧化天然橡胶胶乳薄膜复合层覆盖在所述覆盖在脆性导电薄膜裂纹层2作为柔性封装层3封闭导电薄膜裂纹层,环氧化天然橡胶胶乳薄膜层与所述脆性导电薄膜裂纹层贴合,将输出电极引出所述柔性封装层。
[0088]
实施例11
[0089]
本实施例提供一种微裂纹应变传感器,包括从下至上依次层叠的柔性基底层、脆性导电薄膜裂纹层和柔性封装层,其制备方法如下:
[0090]
选取环氧度为30%的环氧化天然橡胶胶乳和聚酰亚胺薄膜作为柔性基底材料,弹性体交联剂为硫黄,弹性体交联助剂为氧化锌和二乙基二硫代氨基甲酸锌(zdec),脆性薄膜材料为羧甲基壳聚糖和聚碳酸酯,导电填料为单壁碳纳米管,界面改性剂为硅烷偶联剂γ-甲基丙烯酰氧基丙基三甲氧基硅烷(kh570)。向环氧化天然橡胶胶乳中加入2phr的硫黄,1phr的zdec,0.5phr的氧化锌,2phr的kh570。采用超声设备对胶乳超声处理0.5h,使硫化体系和界面改性剂均匀分散在胶乳中得到含硫化体系和界面改性剂的环氧化天然橡胶胶乳。将2g含硫化体系和界面改性剂的环氧化天然橡胶胶乳涂敷在聚酰亚胺薄膜表面并将其放入80℃烘箱中干燥、硫化2h制得柔性基底层。对柔性基底层表面进行电镀处理。将0.05g羧甲基壳聚糖溶解在10ml去离子水中,并加入0.0005g单壁碳纳米管(单壁碳纳米管为羧甲基壳聚糖质量的1%)和1phr的kh570,超声处理0.5h得到均匀分散的单壁碳纳米管悬浮液,将悬浮液分2次加入模具中烘干。将0.05g聚碳酸酯溶解20ml二氯甲烷中,并加入0.0005g单壁碳纳米管(单壁碳纳米管为聚碳酸酯质量的1%)和1phr的kh570,超声处理
0.5h得到均匀分散的单壁碳纳米管悬浮液,将悬浮液分2次加入模具中烘干。烘箱温度为60℃,干燥8h制得复合脆性导电薄膜层。采用预弯曲(曲率半径为1mm)的方式制造微裂纹,得到脆性导电薄膜裂纹层,并将导电铜片引入脆性导电薄膜裂纹层作为输出电极。并将1g含硫化体系和界面改性剂的环氧化天然橡胶胶乳涂敷在聚酰亚胺薄膜表面并置于烘箱中80℃干燥、硫化2h得到聚酰亚胺薄膜-环氧化天然橡胶胶乳薄膜复合层,将聚酰亚胺薄膜-环氧化天然橡胶胶乳薄膜复合层覆盖在所述覆盖在脆性导电薄膜裂纹层作为柔性封装层封闭导电薄膜裂纹层,环氧化天然橡胶胶乳薄膜层与所述脆性导电薄膜裂纹层贴合,将输出电极引出所述柔性封装层。
[0091]
实施例12
[0092]
本实施例提供一种微裂纹应变传感器,包括从下至上依次层叠的柔性基底层、脆性导电薄膜裂纹层和柔性封装层,其制备方法如下:
[0093]
选取环氧度为30%的环氧化天然橡胶胶乳和聚酰亚胺薄膜作为柔性基底材料,弹性体交联剂为硫黄,弹性体交联助剂为氧化锌和二乙基二硫代氨基甲酸锌(zdec),脆性薄膜材料为羧甲基壳聚糖,导电填料为单壁碳纳米管和聚(3,4-亚乙二氧基噻吩),界面改性剂为硅烷偶联剂γ-甲基丙烯酰氧基丙基三甲氧基硅烷(kh570)。向环氧化天然橡胶胶乳中加入2phr的硫黄,1phr的zdec,0.5phr的氧化锌,2phr的kh570。采用超声设备对胶乳超声处理0.5h,使硫化体系和界面改性剂均匀分散在胶乳中得到含硫化体系和界面改性剂的环氧化天然橡胶胶乳。将2g含硫化体系和界面改性剂的环氧化天然橡胶胶乳涂敷在聚酰亚胺薄膜表面并将其放入80℃烘箱中干燥、硫化2h制得柔性基底层。对柔性基底层表面进行电镀处理。将0.1g羧甲基壳聚糖溶解在10ml去离子水中,并加入0.001g单壁碳纳米管和0.001g聚(3,4-亚乙二氧基噻吩)(单壁碳纳米管和聚(3,4-亚乙二氧基噻吩)均为羧甲基壳聚糖质量的1%)和1phr的kh570,超声处理0.5h得到均匀分散的悬浮液。将悬浮液分4次加入模具中,在烘箱中60℃干燥8h制得脆性导电薄膜层。采用预弯曲(曲率半径为1mm)的方式制造微裂纹,得到脆性导电薄膜裂纹层,并将导电铜片引入脆性导电薄膜裂纹层作为输出电极。将1g含硫化体系和界面改性剂的环氧化天然橡胶胶乳涂敷在聚酰亚胺薄膜表面并置于烘箱中80℃干燥、硫化2h得到聚酰亚胺薄膜-环氧化天然橡胶胶乳薄膜复合层,将聚酰亚胺薄膜-环氧化天然橡胶胶乳薄膜复合层覆盖在所述覆盖在脆性导电薄膜裂纹层作为柔性封装层封闭导电薄膜裂纹层,环氧化天然橡胶胶乳薄膜层与所述脆性导电薄膜裂纹层贴合,将输出电极引出所述柔性封装层。
[0094]
对比例1
[0095]
选取环氧度为30%的环氧化天然橡胶胶乳为基体,弹性体交联剂为硫黄,弹性体交联助剂为氧化锌和二乙基二硫代氨基甲酸锌(zdec),导电填料为单壁碳纳米管。将0.05g单壁碳纳米管加入100ml去离子水中;采用超声设备对单壁碳纳米管悬浮液进行超声处理0.5h,得到均匀分散的单壁碳纳米管悬浮液;将其加入5g环氧化天然橡胶胶乳中,超声处理0.5h使单壁碳纳米管均匀分散在胶乳粒子间;将所得悬浮液置于烘箱中60℃干燥硫化24h得到隔离结构的环氧化天然橡胶/单壁碳纳米管复合材料。
[0096]
以下对实施例1~12的微裂纹应变传感器和对比例1的环氧化天然橡胶/单壁碳纳米管复合材料进行一系列的性能测试,性能测试方法如下:
[0097]
首先,将制得的样品用裁刀裁成哑铃状样条。然后,在橡胶拉力机上用夹具将样条
固定。最后,将样条两端的电极与万用表连接。在样条拉伸过程中测量其电阻变化。
[0098]
拉伸测试中,样条的拉伸速率为10mm/min;循环拉伸测试中,样条的拉伸速率和回复速率均为10mm/min,最大应变分别为50%和100%。万用表选择双线电阻模式,电阻测量的频率为40次/秒。
[0099]
实施例1~12的微裂纹应变传感器和对比例1的环氧化天然橡胶/单壁碳纳米管复合材料的性能数据如表1所示。
[0100]
表1实施例1~12的微裂纹应变传感器和对比例1的环氧化天然橡胶/单壁碳纳米管复合材料的性能数据
[0101] gf值应变响应范围(%)对比例12050-200实施例14500005-30实施例22600005-50实施例313000020-100实施例412000010-50实施例54000050-100实施例65000020-50实施例72000005-20实施例81000001-5实施例91200001-5实施例101500002-10实施例112000002-20实施例121800005-10
[0102]
实施例1~12的性能见表1所示。表中的实施例编号对应上述实施例。
[0103]
比较对比例1和实施例1,本发明的基于柔性基底层-脆性导电层的微裂纹应变传感器相比于传统导电复合材料类应变传感器具有更高的gf值,更低的应变响应范围。
[0104]
比较实例1和实施例2,采用不同环氧度的环氧化天然橡胶胶乳作为柔性基底层,对柔性基底层与脆性导电薄膜裂纹层之间的相互作用大小有明显影响,进而影响了gf值的大小与应变响应范围。
[0105]
对比实施例1和实施例3,选取不同的弹性体薄膜作为柔性基底层;对比实施例1和实施例4,选取不同脆性薄膜材料;对比实施例1和实施例5,选取不同的导电填料;对比实施例1和实施例6,选取不同的弹性体薄膜作为柔性基底层以及不同的导电填料,均可得到较好的应变传感性能。
[0106]
对比实施例1和实施例8,选取不同的柔性基底材料作为基底层,应变传感器的应变响应范围有明显不同——柔性基底层为弹性体薄膜时,需要较大的应变实现电阻突变;柔性基底层为商业化柔性薄膜时,在较小应变即可实现电阻突变。在实际应用过程中,可根据适用环境灵活选择基底层。
[0107]
对比实施例8和实施例9,对商业化柔性薄膜表面进行表面处理后,柔性基底层和脆性导电薄膜裂纹层之间的界面相互作用提高,过渡层厚度增加,进而提高了gf值。
[0108]
对比实施例10和实施例1,选取柔性薄膜-弹性体薄膜复合作为柔性基底层,应变
传感器具有较好的应变传感性能,可应用于可触控式屏幕等领域。
[0109]
对比实施例10和实施例11,选取不同脆性导电薄膜复合构成多层脆性导电薄膜裂纹层,可有效扩展应变响应范围。
[0110]
对比实施例10和实施例12,选取不同类型导电填料复合,可以有效降低突变前电阻,进而有效提高gf值。
[0111]
图1为实施例10所得微裂纹应变传感器结构示意图,其由柔性基底层、脆性导电薄膜裂纹层、柔性封装层三部分构成,引入电极即可实现电学信号输出。
[0112]
图2为本发明提供的弧型微裂纹应变传感器在垂直方向应变下的工作原理示意图。垂直按压弧状微裂纹应变传感器时,对弧状微裂纹应变传感器垂直方向的应变转化为水平面内的应变。
[0113]
图3为本发明的微裂纹应变传感器的工作原理图,对于拉伸应变,初始状态时,脆性导电薄膜裂纹层的裂纹基本处于闭合状态;当对微裂纹应变传感器施加拉伸应变时,脆性导电薄膜裂纹层的裂纹逐渐扩展,电阻急剧增加;当应变撤去后,裂纹逐渐消失,电阻降低。对于按压应变,初始状态时,微裂纹应变传感器为预拉伸状态,脆性导电薄膜裂纹层的裂纹处于扩展状态;当对微裂纹应变传感器施加一定的按压应变时,脆性导电薄膜裂纹层的裂纹逐渐闭合,电阻急剧降低;当应变撤去后,裂纹逐渐恢复,电阻提高。
[0114]
图4a)为实施例2所得微裂纹应变传感器的脆性导电薄膜裂纹层初始状态时的扫描电镜图片,相比于平整光滑的导电薄膜表面,裂纹处有明显皱褶;图4b)为实施例2中脆性导电薄膜裂纹层在50%应变时的扫描电镜图片,可以明显看到脆性导电薄膜裂纹层的本体层21与过渡层22的裂纹扩展方式明显不同。
[0115]
图5a)为实施例4所得微裂纹应变传感器初始状态的3维扫描截面曲线,微裂纹的宽度为9.1μm,深度为5.6μm;图5b)为基于柔性基底层-脆性导电层的微裂纹应变传感器的应变提高至5%时的3维扫描截面曲线,微裂纹的宽度和深度分别提高至23.9μm和15.7μm;图5c)为基于柔性基底层-脆性导电层的微裂纹应变传感器的应变提高至50%时的3维扫描截面曲线,微裂纹的宽度和深度分别提高至188.1μm和24.6μm,并且此时过渡层出现裂纹,图5d显示过渡层度的裂纹深度约为1.5μm(即为过渡层22的深度)。
[0116]
图6为实施例4所得微裂纹应变传感器在不同应变下的3维扫面图,随着应变增加,裂纹宽度和深度均增加。
[0117]
图7为实施例9所得微裂纹应变传感器的电阻变化率-应变曲线图,随着应变增加,电阻变化率急剧提高。当应变为5%时,电阻变化率高达40000。
[0118]
图8a)与图8b)分别为实施例5所得微裂纹应变传感器在50%与100%循环应变下的电阻率变化曲线,电阻率变化与应变基本同步,且并未随循环次数增加而衰减,说明基于柔性基底层-脆性导电层的微裂纹应变传感器具有良好的耐久性。
[0119]
以上所揭露的仅为本发明几种较佳实施例而已,当然不能以此来限定本发明之权利范围,因此依本发明申请专利范围所作的等同变化,仍属本发明所涵盖的范围。