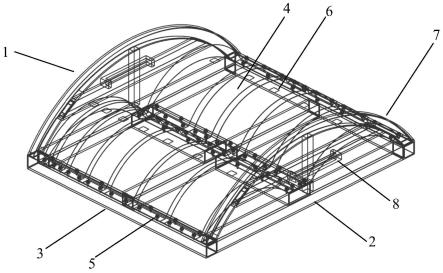
1.本发明涉及车辆领域,尤其涉及一种测量车辆覆盖件刚度的量具及制作和使用量具的方法。
背景技术:2.客户在购买、使用以及清洁保养车辆的过程中,会以指压、掌压、依靠、坐、脚踏等形式接触车辆,这对车辆覆盖件的软硬或者抵抗变形的能力(刚度)提出了要求。
3.本发明提出一种将客户对车辆覆盖件刚度的实际感受与车辆覆盖件的实际刚度相对应的方法和测量量具,即测量车辆覆盖件刚度的量具及制作和使用量具的方法。
技术实现要素:4.基于以上问题,本发明提出一种测量车辆覆盖件刚度的量具及制作和使用量具的方法,通过量具提供不同刚度的感知和不同刚度感知对应的实际刚度值,达到对客户刚度感知度进行量化的效果。
5.本发明提出一种测量车辆覆盖件刚度的量具,包括:
6.框架主体和安装在框架主体上的至少一组覆盖片,每组覆盖片包括多个相邻排列的覆盖片,框架主体包括两条纵梁和两条横梁,框架主体的中间还设置有比覆盖片的组数的数量少一个数量的纵梁;
7.每一个覆盖片对应不同的刚度值,覆盖片的两端分别安装在框架主体的两条相邻的纵梁上,框架主体的两条横梁上各设有一个弧形结构,弧形结构包括一个弧形支架和一个横杆,弧形支架的两端与框架本体的横梁的两端连接,横杆安装在弧形支架上。
8.此外,每一个覆盖片上均设置有按压区域标记。
9.此外,覆盖片的材料为金属、塑料和复合材料其中之一。
10.此外,每个覆盖片的下方还设置有限位片,限位片的两端安装在框架主体的两条相邻的纵梁上。
11.此外,覆盖片的两侧包覆防刮条。
12.此外,防刮条为硅胶条。
13.此外,横杆上安装有把手。
14.本发明还提出一种制作测量车辆覆盖件刚度的量具的方法,包括:
15.采用仿真软件设计不同刚度值的覆盖片;
16.根据设计结果制作不同刚度值的覆盖片;
17.对覆盖片的刚度值进行试验校正;
18.将校正后的覆盖片安装在量具的框架主体上。
19.本发明还提出一种使用覆盖件刚度的量具的方法,包括:
20.按压车辆覆盖件,感知车辆覆盖件的刚度;
21.按压量具上的覆盖片,在量具上找到与车辆覆盖件的刚度相同的覆盖片,查看覆
盖片对应的刚度值;
22.量具包括多个不同刚度值的覆盖片。
23.本发明提出的是一个全新的量具,通过量具提供不同刚度的感知和不同刚度感知对应的实际刚度值,达到对客户刚度感知度进行量化的效果。
附图说明
24.图1为本发明一个实施例提供的测量车辆覆盖件刚度的量具的整体结构示意图;
25.图2为图1的渲染图;
26.图3为图1的左视图的渲染图;
27.图4为图1的左视图;
28.图5为本发明一个实施例提供的制作测量车辆覆盖件刚度的量具的方法的流程图;
29.图6为本发明一个实施例提供的使用覆盖件刚度的量具的方法的流程图。
具体实施方式
30.以下结合具体实施方案和附图对本发明进行进一步的详细描述。其只意在详细阐述本发明的具体实施方案,并不对本发明产生任何限制,本发明的保护范围以权利要求书为准。
31.参照图1-4,本发明提出一种测量车辆覆盖件刚度的量具,包括:
32.框架主体1和安装在框架主体1上的至少一组覆盖片,每组覆盖片包括多个相邻排列的覆盖片4,框架主体1包括两条纵梁3和两条横梁2,框架主体1的中间还设置有比覆盖片的组数的数量少一个数量的纵梁;
33.每一个覆盖片4对应不同的刚度值,覆盖片4的两端分别安装在框架主体1的两条相邻的纵梁3上,框架主体1的两条横梁2上各设有一个弧形结构,弧形结构包括一个弧形支架7和一个横杆,弧形支架的两端与框架本体1的横梁2的两端连接,横杆安装在弧形支架上。
34.可选地,覆盖片4通过紧固件5安装在框架主体1上,只要能便于拆卸更换,不拘泥于螺栓连接的形式。
35.在车辆覆盖件的设计阶段仅能通过cae计算得到设计状态的刚度值,不能将刚度与实际的客户感受对应;在实物阶段虽可以进行客户评审,但不能将具体刚度值与客户评估的任意覆盖件区域的软硬度一一对应。车辆覆盖件刚度的客户体验标尺是一个可以准确量化不同刚度感受的样件,客户可以用来感知是否满足其要求。而本发明提供的量具可以用于客户调研、设定刚度目标、虚拟评审等。
36.使用本量具时,通过按压覆盖片感知覆盖片的软硬度和刚度,对比按压车辆覆盖件的感知刚度,当二者一致时,则根据覆盖片对应的刚度值得到车辆覆盖件的刚度值。
37.本发明提出的是一个全新的量具,通过量具提供不同刚度的感知和不同刚度感知对应的实际刚度值,达到对客户刚度感知度进行量化的效果。
38.参照图3-4,在其中的一个实施例中,每一个覆盖片1上均设置有按压区域标记6。
39.由于对覆盖片上的不同位置施加相同的力,其产生的变形量不同,导致刚度的感
知有误差,所以在每一个覆盖片1上均设置有按压区域标记6,通过设置按压区域标记6,引导客户在此区域按压从而保证得到精确的刚度值。可选地,通过激光印刻的方式,在覆盖片上印刻按压区域标记6,比如按压区域标记的面积为10mm*10mm。
40.在其中的一个实施例中,覆盖片的材料为金属、塑料和复合材料其中之一。
41.参照图3-4,在其中的一个实施例中,每个覆盖片1的下方还设置有限位片9,限位片9的两端安装在框架主体的两条相邻的纵梁上。
42.为了防止客户在测试或使用量具的过程中,操作力过大出现覆盖片变形过大而翻转的问题,在覆盖片的下方设计了限位片9。
43.在其中的一个实施例中,覆盖片的两侧包覆防刮条。
44.考虑按压过程中对人手的保护,可在覆盖片的两侧包覆防刮条,例如硅胶条。尤其当覆盖片采用金属薄板时,覆盖片的两侧尤其需要包覆防刮条。
45.在其中的一个实施例中,防刮条为硅胶条。
46.在其中的一个实施例中,横杆上安装有把手8。把手8用于方便搬运量具。
47.当采用本实施例的量具进行指导汽车设计或客户感知评审时,找到一定数量的客户按压量具的覆盖片,直接进行顾客感知度和刚度的对应。比如将顾客感知度分为十级,让每一个顾客按压后列出对应的十级刚度,顾客数量足够多的话结果就越可靠,即可形成标准感知度与刚度的对应表,这个对应表即可以用于指导汽车设计或顾客感知评审。
48.参照图5,本发明还提出一种制作测量车辆覆盖件刚度的量具的方法,包括:
49.步骤s501,采用仿真软件设计不同刚度值的覆盖片;
50.步骤s502,根据设计结果制作不同刚度值的覆盖片;
51.步骤s503,对覆盖片的刚度值进行试验校正;
52.步骤s504,将校正后的覆盖片安装在量具的框架主体上。
53.本发明步骤s501中采用的仿真软件为optistruct或abaqus,输入参数包括:材料的弹性模量、泊松比、密度等参数,仿真软件根据这些参数进行刚度分析,求得位移。根据外部的输入力除以位移即可得到覆盖片的刚度值。
54.步骤s502中的设计结果包括:材料牌号、覆盖片几何参数(形状、厚度、宽度、长度等)、螺栓点数量。
55.步骤s503中的试验校正过程包括:将通过仿真软件计算设计得到的覆盖片进行物理样件制作。制作完成后,覆盖片紧固在试验台架上,对每一片覆盖片进行力的加载,测得变形量,取线性段结果的加载力和变形量的斜率即为刚度值。将测得的刚度值与仿真软件计算结果进行比对,若不同,则校正。
56.校正时,若刚度值偏差超过5%,需修正仿真软件的计算模型(检查物理模型和仿真软件的计算模型的差异),根据偏差量对覆盖片几何特性进行重新设计计算,最有效的方式是改变覆盖片的宽度和厚度。
57.通过制作的量具提供不同刚度的感知和不同刚度感知对应的实际刚度值,达到对客户刚度感知度进行量化的效果。
58.参照图6,本发明还提出一种使用覆盖件刚度的量具的方法,包括:
59.步骤s601,按压车辆覆盖件,感知车辆覆盖件的刚度;
60.步骤s602,按压量具上的覆盖片,在量具上找到与车辆覆盖件的刚度相同的覆盖
片,查看覆盖片对应的刚度值;
61.步骤s603,量具包括多个不同刚度值的覆盖片。
62.本发明给出了使用覆盖件刚度的量具的方法,通过使用此量具,达到对客户刚度感知度进行量化的效果。
63.以上所述的仅是本发明的原理和较佳的实施例。应当指出,对于本领域的普通技术人员来说,在本发明原理的基础上,还可以做出若干其它变型,也应视为本发明的保护范围。