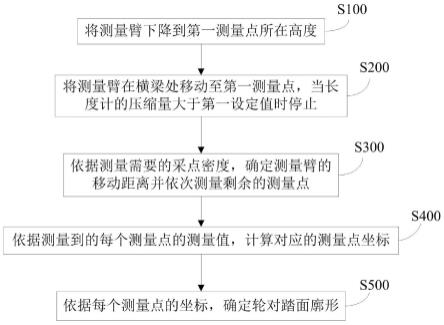
1.本发明涉及曲面零件廓形测量技术领域,具体涉及一种接触式廓形测量方法。
背景技术:2.动车段在检修动车、高铁等车型的轮对时,以往对于鏇修完成后的车轮踏面廓形采用人工手持廓形尺比对的方式来验证其是否合格,即根据被测轮对踏面廓形与标准形状尺的贴合程度判定是否合格。这种方式只能通过操作工直观观察来判断合格与否,而没有实际廓形的数据定量的判定,无法得到实际廓形数据,也无法得到轮辋宽度、轮缘厚度、轮缘高度、qr值等重要指标,是一种粗略的测量方式。同时这种人工手动测量的方式也无法实现自动化测量,不利于车间生产自动化的发展。
3.现有技术虽通过专用装置利用激光非接触测量的方式实现踏面廓形测量,但在测量时仍需专人安装后才可进行,且测量结束后需人工拆卸,不适合在自动化的流水线经行。
4.因此,发明人提供了一种接触式廓形测量方法。
技术实现要素:5.(1)要解决的技术问题
6.本发明实施例提供了一种接触式廓形测量方法,解决了车轮踏面廓形定量测量和自动化测量难度大的技术问题。
7.(2)技术方案
8.本发明提供了一种接触式廓形测量方法,该测量方法使用的测量装置包括横梁、测量臂、旋转机构和长度计,所述测量臂安装于所述横梁上,所述测量臂的一端安装有所述旋转机构,所述长度计连接于对应的所述旋转机构,该方法包括以下步骤:
9.将所述测量臂下降到第一测量点所在高度;
10.将所述测量臂在所述横梁处移动至所述第一测量点,当所述长度计的压缩量大于第一设定值时停止;
11.依据测量需要的采点密度,确定所述测量臂的移动距离并依次测量剩余的测量点;
12.依据测量到的每个测量点的测量值,计算对应的测量点坐标;
13.依据所述每个测量点的坐标,确定轮对踏面廓形。
14.进一步地,所述将所述测量臂下降到第一测量点所在高度,具体为:
15.所述旋转机构带动所述长度计旋转至垂直于轮对踏面的第一立面。
16.进一步地,所述将所述测量臂在所述横梁处移动至所述第一测量点,当所述长度计的压缩量大于第一设定值时停止,具体为:
17.将所述测量臂在所述横梁处移动至所述第一测量点,当所述长度计的压缩量大于所述设定值时停止,并记录此时长度计的压缩量、横梁与测量臂的位置坐标、长度计的旋转角度。
18.进一步地,所述依据测量需要的采点密度,确定所述测量臂的移动距离并依次测量剩余的测量点,具体为:
19.依据前后两次测量中的压缩量差值与第二设定值的大小关系,确定后一次测量中的测量点。
20.进一步地,所述依据前后两次测量中的压缩量的差值与第二设定值的大小关系,确定后一次测量中的测量点,具体为:
21.当所述压缩量差值小于或等于所述第二设定值时,所述长度计仍与立面垂直;或,
22.当所述压缩量差值大于所述第二设定值时,确定该测量点处的长度计压缩量最大的角度,使得长度计与曲面上该测量点处的法线重合。
23.进一步地,所述当所述压缩量差值大于所述第二设定值,确定该测量点处的长度计压缩量最大的角度,使得长度计与曲面上该测量点处的法线重合,具体包括如下步骤:
24.以当前角度为参照点,正向旋转长度计;
25.若长度计压缩量增大,则继续旋转,直至压缩量减小时停止并记录测量过程中的最大压缩量及其对应角度;
26.若长度计压缩量减小,则反向旋转并记录最大压缩量及其对应角度;
27.将长度计旋转至长度计压缩量最大的角度后停止。
28.进一步地,当后一次测量点处长度计的最大压缩量小于第一次测量点处长度计的压缩量的一半时,则在下一测量点时调整测量臂在横梁的位置,使测量臂在横梁方向移动设定距离,并更新下一测量点在横梁方向上的移动距离。
29.进一步地,当所述压缩量差值大于所述第二设定值且所述长度计的旋转角度为0
°
时,确定该测量点为轮对踏面的最高点。
30.进一步地,所述长度计的旋转角度为-90
°
时,确定该测量点为轮对踏面的第二立面。
31.进一步地,所述依据测量到的每个测量点的测量值,计算对应的测量点坐标,具体为:
32.依据长度计在对应的测量点的实际长度、旋转角度及横梁与测量臂的位置坐标,确定该测量点坐标。
33.(3)有益效果
34.综上,本发明通过旋转机构调整长度计在测量过程中角度的方式得到长度计与被测物接触点的坐标值,实现被测件廓形定量测量和自动化测量。提高了车轮检修时的自动化水平和轮对廓形检测的准确性,在列车轮对维修、检测领域具有广阔的市场空间。
附图说明
35.为了更清楚地说明本发明实施例的技术方案,下面将对本发明实施例中所需要使用的附图作简单地介绍,显而易见地,下面所描述的附图仅仅是本发明的一些实施例,对于本领域普通技术人员来讲,在不付出创造性劳动的前提下,还可以根据这些附图获得其他的附图。
36.图1是本发明实施例提供的一种接触式廓形测量方法的流程示意图;
37.图2是本发明实施例提供的一种接触式廓形测量装置的结构示意图;
38.图3是本发明实施例提供的一种接触式廓形测量装置的应用场景图;
39.图4是本发明实施例提供的一种轮对踏面廓形的参数示意图。
40.图中:
41.1-横梁;2-测量臂;3-旋转机构;4-长度计;5-被测轮对踏面廓形;6-被测轮对踏面的左立面;7-被测轮对踏面的右立面。
具体实施方式
42.下面结合附图和实施例对本发明的实施方式作进一步详细描述。以下实施例的详细描述和附图用于示例性地说明本发明的原理,但不能用来限制本发明的范围,即本发明不限于所描述的实施例,在不脱离本发明的精神的前提下覆盖了零件、部件和连接方式的任何修改、替换和改进。
43.需要说明的是,在不冲突的情况下,本技术中的实施例及实施例中的特征可以相互组合。下面将参照附图并结合实施例来详细说明本技术。
44.图1是本发明实施例提供的一种接触式廓形测量方法的流程示意图,如图2所示,其使用的测量装置包括横梁1、测量臂2、旋转机构3和长度计4,测量臂2安装于横梁1上,测量臂2的一端安装有旋转机构3,长度计4连接于对应的旋转机构3,该方法包括以下步骤:
45.s100、将测量臂下降到第一测量点所在高度;
46.s200、将测量臂在横梁处移动至第一测量点,当长度计的压缩量大于第一设定值时停止;
47.s300、依据测量需要的采点密度,确定测量臂的移动距离并依次测量剩余的测量点;
48.s400、依据测量到的每个测量点的测量值,计算对应的测量点坐标;
49.s500、依据每个测量点的坐标,确定轮对踏面廓形。
50.在上述实施方式中,图2中a、b、c、d、e分别为选取的测量过程中具有代表性的点,设长度计4的原长为l,长度计4在各点的压缩量分别δla、δlb、δlc、δld、δle。则当长度计4被压缩后,从接触点到旋转中心的长度如下:
[0051][0052]
长度计4的原长l为已知量,横梁1和测量臂2装有高精度光栅尺,可以精确计算其行走过的距离,分别以x和y表示;旋转机构3处有编码器,能精确记录长度计4转过的角度,以θ表示。
[0053]
通过旋转机构3调整长度计4在测量过程中角度的方式得到长度计4与被测物接触点的坐标值,实现被测件廓形定量测量和自动化测量,进而提高了车轮检修时的自动化水平和轮对廓形检测的准确性。
[0054]
作为一种可选的实施方式,步骤s100中,将测量臂下降到第一测量点所在高度,具体为:
[0055]
旋转机构带动长度计旋转至垂直于轮对踏面的第一立面。
[0056]
如图2-3所示,旋转机构3带动长度计4旋转至与被测轮对踏面的左立面6垂直,即使得θa=90
°
,此时长度计4未与被测面接触。其中,旋转机构具体可选用为步进电机,长度计可以为基恩士压缩量位移传感器。
[0057]
作为一种可选的实施方式,步骤s200中,将测量臂在横梁处移动至第一测量点,当长度计的压缩量大于第一设定值时停止,具体为:
[0058]
将测量臂在横梁处移动至第一测量点,当长度计的压缩量大于设定值时停止,并记录此时长度计的压缩量、横梁与测量臂的位置坐标、长度计的旋转角度。
[0059]
具体地,保存停止时的长度计的压缩量δla,横梁与测量臂位置坐标分别为xa、ya,旋转机构角度θa;以上为方便表示,记为a(xa,ya,θa,δla),此时a点处测量值采集完成。
[0060]
作为一种可选的实施方式,步骤s300中,依据测量需要的采点密度,确定测量臂的移动距离并依次测量剩余的测量点,具体为:
[0061]
依据前后两次测量中的压缩量差值与第二设定值的大小关系,确定后一次测量中的测量点。
[0062]
其中,如图2所示,设提升完成后到达点b,测量臂坐标为yb,长度计压缩量为δlb。
[0063]
作为一种可选的实施方式,依据前后两次测量中的压缩量的差值与第二设定值的大小关系,确定后一次测量中的测量点,具体为:
[0064]
当压缩量差值小于或等于第二设定值时,长度计仍与立面垂直;或,
[0065]
当压缩量差值大于第二设定值时,确定该测量点处的长度计压缩量最大的角度,使得长度计与曲面上该测量点处的法线重合。
[0066]
具体地,若|δl
b-δla|≤ε(其中第二设定值ε为与立面表面粗糙度和长度计精度有关的经验值)则认为当前点仍与初始点a在同一左立面,此时xb=xa+(δl
b-δla),因都在同一立面,此时长度计仍保持与立面垂直不需要旋转,故θb=θa=90
°
。得此时该测量点的测量值为b(xb,yb,θb,δlb)。
[0067]
若|δl
b-δla|>ε则认为b点离开左立面,此时长度计的压缩量为δl
b0
,此时需旋转长度计找出该点长度计压缩量最大时对应的角度,使得长度计与曲面上点b处的法线重合。
[0068]
作为一种可选的实施方式,当压缩量差值大于第二设定值,确定该测量点处的长度计压缩量最大的角度,使得长度计与曲面上该测量点处的法线重合,具体包括如下步骤:
[0069]
以当前角度为参照点,正向旋转长度计;
[0070]
若长度计压缩量增大,则继续旋转直至压缩量开始减小时停止并记录测量过程中的最大压缩量及其对应角度;
[0071]
若长度计压缩量减小,则反向旋转并记录最大压缩量及其对应角度;
[0072]
将长度计旋转至长度计压缩量最大的角度后停止。
[0073]
具体地,以当前角度为参照点,顺时针旋转长度计,(1)若长度计压缩量增大,则继续旋转,直至压缩量减小时停止并记录测过程中最大压缩量δl
bmax
和对应角度θb;(2)若长度计压缩量减小,则停止该方向旋转而变为逆时针旋转,重复(1)过程找出最大压缩量δl
bmax
和对应角度θb。最后,将长度计旋转至最大压缩量的角度θb后停止,此时记δlb=δl
bmax
。此时该测量点b测量值为(xb,yb,θb,δlb)。
[0074]
作为一种可选的实施方式,当后一次测量点处长度计的最大压缩量小于第一次测
量点处长度计的压缩量的一半时认为压缩量过小,则在下一测量点时调整测量臂在横梁的位置,使测量臂在横梁方向移动设定距离,并更新下一测量点在横梁方向上的移动距离。
[0075]
具体地,为保证足够的压缩量,当(即)时,则在下一点时调整测量臂在横梁的位置,使测量臂在横梁方向(x方向)移动距离为即更新下一个测量点在横梁方向上的移动距离为
[0076]
长度计压的缩量范围的选择是为了防止在下一个点长度计的压缩量过小,通过在横梁上横向移动,来增大长度计的压缩量,每次只能下降这么多以避免使长度计的压缩量过大。
[0077]
作为一种可选的实施方式,当压缩量差值大于第二设定值且长度计的旋转角度为0
°
时,确定该测量点为轮对踏面的最高点。
[0078]
具体地,重复步骤s300,若不满足|δl
b-δla|≤ε,则开始执行步骤s300的第二种情况。当重复执行步骤s300第二种情况时则表明b已离开立面,故后续无需再判定条件|δl
b-δla|>ε;执行步骤s300第二种情况的过程中,若θ=0
°
,如c点,则此时测量臂在横梁上的位置x为踏面最高点所在位置,相应的此时c点测量值记为(xc,yc,θc,δlc)。
[0079]
开始测量c点后续的坐标,根据需要的采样密度在横梁方向(x方向)上移动测量臂,如d点,然后找出d点压缩量最大的点,此时d点记为(xd,yd,θd,δld)。为保证足够的压缩量,当(即)时,则在下一点时调整测量臂下降,下降距离即更新下一点
[0080]
作为一种可选的实施方式,长度计的旋转角度为-90
°
时,确定该测量点为轮对踏面的第二立面。
[0081]
具体地,如图2-3所示,当θ=-90
°
时,则说明长度计到达被测轮对踏面的右立面7,如e点,则测量点全部采集完成,记录此时e点测量值为(xe,ye,θe,δle)。测量臂在横梁上x向移动使得长度计与被测面脱离,然后测量臂提升至最高点后回到初始位置并旋转长度计使其旋转角度θ=0
°
,至此测量结束。
[0082]
作为一种可选的实施方式,步骤s400中,依据测量到的每个测量点的测量值,计算对应的测量点坐标,具体为:
[0083]
依据长度计在对应的测量点的实际长度、旋转角度及横梁与测量臂的位置坐标,确定该测量点坐标。
[0084]
以d点为例,设曲面上d点的坐标为(xd,yd),则:
[0085][0086]
其中,xd、yd、θd及ld由测量d点过程中记录值(xd,yd,θd,δld)得到,依次计算所有测量点的坐标,即可得到踏面廓形所有采集的表面点的坐标。
[0087]
步骤s500中,将每个点依次连接起来便得到踏面廓形的轮廓曲线,根据计算结果
所得曲面廓形各处的坐标点,其他相关指标如轮辋宽度、轮缘厚度、qr值及轮缘高度(如图4所示)也可相应的求出。
[0088]
需要明确的是,本说明书中的各个实施例均采用递进的方式描述,各个实施例之间相同或相似的部分互相参见即可,每个实施例重点说明的都是与其他实施例的不同之处。本发明并不局限于上文所描述并在图中示出的特定步骤和结构。并且,为了简明起见,这里省略对已知方法技术的详细描述。
[0089]
以上仅为本技术的实施例而已,并不限制于本技术。在不脱离本发明的范围的情况下对于本领域技术人员来说,本技术可以有各种更改和变化。凡在本技术的精神和原理之内所作的任何修改、等同替换、改进等,均应包含在本技术的权利要求范围内。