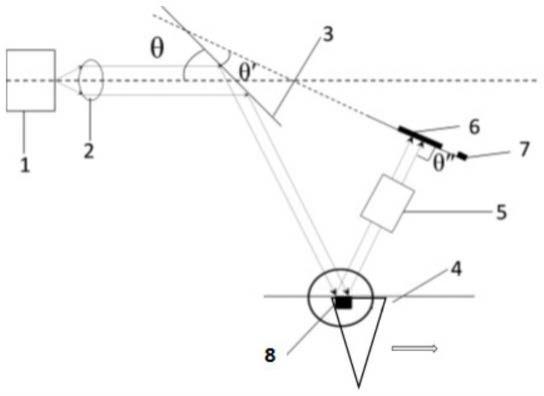
1.本发明涉及结构健康监测领域,具体地,涉及一种用光强度检测焊缝表面细微裂缝的装置与方法。
背景技术:2.金属焊缝属于结构的薄弱环节,在焊接应力、结构应力及运行应力的作用下容易产生裂纹并且扩展裂纹在扩展过程中会降低焊接位置的承载力并且在扩展到达一定程度后对结构造成不可逆转的损伤,造成零件的损坏失效。因此,发现早期微裂纹可尽早的避免焊接件的安全事故,对于系统的可靠性非常重要。目前的检测手段主要有磁粉检测、渗透检测、涡流检测等无损检测手段,但这些手段通常只能检测出有已发展为一定尺寸的宏观裂纹,无法检测出早期产生的细微裂纹。
3.本发明的目的是提供一种金属表面微裂纹的简易检测装置与方法,所述方法基于检测光束的光密度及宽度的调整检测金属焊缝表面细微裂纹及分布,以此可以检测出金属焊缝表面早期产生的细微裂纹,可以及时进行修补,防止造成更大的经济损失。
技术实现要素:4.本发明涉及一种用光强度检测焊缝表面细微裂缝的装置与方法,基于检测光束的光密度及宽度的调整检测金属焊缝表面细微裂纹及分布,以解决现有技术是通常只能检测出有已发展为一定尺寸的宏观裂纹,无法检测出早期产生的细微裂纹的问题。
5.本发明将焊接表面通过打磨和抛光得到比较理想的平面。当检测光束照射到所述平面可认为是平面反射。所述装置包括:激光器、光学整形系统、反射镜、光束扩束器、第一光电探测器、第二光电探测器。
6.图1和图2给出了焊接表面细微裂缝检测的原理示意图。图中的1~6为检测系统的组成部分及结构。其中,1为激光器,所述激光器提供探测光源;2为光学整形系统,所述光学整形系统将激光束转换为线状光源;3为反射镜,所述激光束进一步将线状光源压缩,并控制探测光束的入射方向;4为被检测金属表面;5为光束扩束器,可以放大反馈光束的宽度;6为第一光电探测器,探测金属表面反射后的光束强度信息;7为第二光电探测器;8为光束照射的金属表面区域。被测表面在光束照射时可平移;所述第一光电探测器所在平面与反射镜所在平面的夹角为θ
′
,该夹角为固定值。第一光电探测器的宽度与经所述反射镜反射后的入射光束宽度s一致,且与入射光束垂直。所述第二光电探测器为点光强探测器,且可以在指定范围内来回接收光束。
7.由激光器发出探测光束,通过光学整形系统变为线状光束,再经过反射镜进一步压缩测试光束的宽度,再将线状光束入射到被探测的金属表面;探测光束通过金属表面反射,再入射到扩束器上进行光束展宽,展宽后的光束入射到探测器上进行探测,当第二光电探测器接收不到光束时,通过被测金属表面平移的距离,来确定金属表面的裂纹宽度和深度。
8.根据入射光束在金属表面的反射过程,确定金属裂纹的宽度和深度。具体地,图2为入射光束在金属表面的反射过程,其中h为金属表面的裂纹深度,l为裂纹宽度,ab和ef分别为线光斑的边缘光束。当金属表面理想时,入射光束将全部被第一光电探测器所接收;当金属表面存在裂纹时反射光线入射到探测器上的位置会发生平移,效果如图2所示。
9.根据光束的入射几何关系,可以得到探测器上的强度与裂纹的深度和宽度满足如下关系。当入射光束刚入射到裂纹时,由于裂纹的深度使光束在探测面上平移,因此接收到的光强减少,由此所述金属表面的裂纹深度h的计算方式如下:
10.d
′
g=dg-dd
′
11.s=dd
′
12.s
′
=h/sinθ
13.s
″
=s-h/sinθ
14.h=d
′
g*sinθ
15.具体地,当深度h=l/(2*tg(π/2-θ))时,所述第二光电探测器不能探测到光强,因此该方法能够检测到的最大深度为l/(2*tg(π/2-θ)),因此本方法能检测裂纹的深度范围为0~l/(2*tg(π/2-θ)),可看出检测深度与光束的入射角度有关。
16.当入射光束刚入射到裂纹时,ab光线由b
′
点反射,反射光束将由第二光电探测器接收,控制探测点宽度,可将第二光电探测器看作为点强度测试。当被测金属平面平移至第二光电探测器不能探测到光强时,被测金属平面的距离与裂纹的宽度一致。因此,假设第二光电探测器第一次探测到光强的位置记为j点,第二光电探测器无信号时对应的位置记为k,jk即为裂纹的宽度。
17.本发明基于检测光束的光密度及宽度的调整检测金属焊缝表面细微裂纹及分布,以此可以检测出金属焊缝表面早期产生的细微裂纹,解决了目前技术手段只能检测已有一定尺寸的宏观裂纹而无法尽早检测到细微裂纹的问题,防止造成更大的经济损失,从而避免最终导致零件损坏失效而引发的安全事故。
附图说明
18.为了更清楚地说明本技术实施例中的技术方案,下面将对实施例描述中所需要使用的附图作简单地介绍,显而易见地,下面描述中的附图仅仅是本技术的一些实施例,对于本领域技术人员来讲,在不付出创造性劳动的前提下,还可以根据这些附图获得其他的附图。
19.图1为本发明探测系统结构及检测原理示意图;
20.图2为图1中圈出的部分放大光路图。
具体实施方式
21.下面将结合本发明实施例中的附图,对本发明实施例中的技术方案进行清楚、完整地描述,显然,所描述的实施例仅仅是本发明一部分实施例,而不是全部的实施例。基于本发明中的实施例,本领域普通技术人员在没有做出创造性劳动前提下所获得的所有其他实施例,都属于本发明保护的范围。
22.在下面的描述中阐述了很多具体细节以便于充分理解本发明,但是本发明还可以
采用其他不同于在此描述的其它方式来实施,本领域技术人员可以在不违背本发明内涵的情况下做类似推广,因此本发明不受下面公开的具体实施例的限制。
23.目前的检测焊缝表面技术,只能检测出已发展成一定尺寸的宏观裂纹,因金属焊缝属于结构薄弱的环节,在焊接应力、结构应力及运行应力的作用下容易产生裂纹并扩展,最终造成零件的损坏失效。为了能提早发现焊缝表面的细微裂纹,避免安全事故的发生,本发明提供了一种焊缝表面细微裂缝的检测装置与方法。
24.本实施例所述装置包括:激光器、光学整形系统、反射镜、光束扩束器、第一光电探测器、第二光电探测器;所述检测装置由所述激光器发出探测光束,然后通过光学整形系统变为线状光束,再经过反射镜进一步压缩测试光束的宽度,再将线状光束入射到被探测的金属表面;入射光通过金属表面反射入射到扩束器上进行光束展宽,展宽后的光束入射到探测器上进行探测,根据判断和分析探器上的光束强度确定金属表面的裂纹宽度和深度。
25.所述激光器和光学整形系统的中心在一条水平线上且与所测金属表面平行,所述激光器发出的探测光源由光学整形系统将激光束转为线状光源并射向反射镜;所述反射镜所在平面与所述光学整形系统射出的线状光源锐角夹角为θ;所述光束扩束器垂直于金属表面反射出的光线;所述第一光电探测器和第二光电探测器在同一条直线上并相隔一段距离,且所在平面与反射镜所在平面的夹角为θ
′
,该夹角为固定值。
26.安装好所述装置后,打开所述激光器,光束经光学整形系统变成线性光束后经反射镜反射至金属平面,将金属平面慢慢平移,若入射光束将全部被第一光电探测器所接收,则金属表面理想,没有裂纹;若反射光线入射到探测器上的位置发生平移,则被测金属表面存在裂纹。
27.所述被测金属表面沿预定方向平移,当探测光束刚入射到裂纹时由裂缝射入,在裂缝底部反射,光束由第二光电探测器接收;当平移被测金属平面至第二光电探测器不能探测到光强时,被测金属表面平移的距离等于裂纹的宽度。
28.所述金属表面裂纹的深度为第一光电探测器右端点与第二光电探测器左端点的距离乘sinθ;根据所述金属表面裂纹宽度,确定能检测到的金属表面裂纹的最大深度为裂缝宽度的一半除以tan(π/2-θ)。
29.本装置结构简单,操作方便,能够及时检测出焊缝表面的细微裂纹,避免安全事故的发生。
30.本实施例所述方法具体步骤如下:
31.(1)根据图1所述的结构放置各个元件,具体为:1为激光器,所述激光器提供探测光源;2为光学整形系统,所述光学整形系统将激光束转换为线状光源;3为反射镜,所述激光束进一步将线状光源压缩,并控制探测光束的入射方向;4为被检测金属表面;5为光束扩束器,可以放大反馈光束的宽度;6为第一光电探测器,探测金属表面反射后的光束强度信息;7为第二光电探测器;8为光束照射的金属表面区域。根据激光束的位置将需要探测的表面边缘与所述激光束重合,确定金属表面与第一光电探测器的中心点的距离,如图1所示;
32.具体地,根据由激光器1发出的探测光束,通过光学整形系统2变为线状光束,再经过反射镜3进一步压缩测试光束的宽度,并控制所述入射光束与反射镜锐角夹角的角度为θ,再将线状光束入射到被探测的金属表面;入射光通过金属表面反射入射到扩束器5上进行光束展宽,展宽后的光束入射到探测器上进行探测,根据判断和分析探测面上的光束强
度表征金属表面的裂纹宽度和深度;
33.(3)打开激光器后,根据图1箭头的方向平移金属表面,让激光束沿金属表面逐步照射。同时所述第二光电探测器在规定范围内来回扫描;
34.具体地,根据所述入射光束位置是否发生平移,判断金属表面是否有裂纹;若入射光束将全部被第一光电探测器所接收,则金属表面理想,没有裂纹;若反射光线入射到探测器上的位置发生平移,则金属表面存在裂纹;
35.(4)当所述第二光电探测器接刚收到光强时,读取第二光电探测器的位置g,并固定探测器的位置,当入射光束刚入射到裂纹时,由于裂纹的深度使光束在探测面上平移,因此接收到的光强减少,得到d
′
g的长度,将该长度带入式h=d
′
g sinθ得到深度h。并记录此时探测面位移零点r点;
36.具体地,当深度h≥l/(2*tg(π/2-θ))时,探测器不能探测到光强,因此该方法能够检测到的最大深度为l/(2*tg(π/2-θ)),因此本方法能检测裂纹的深度范围为0~l/(2*tg(π/2-θ));
37.(5)执行上述步骤继续平移被测表面,当所述第二光电探测器没有强度时,记录探测表面位移量u,所述第二探测器表面的位移量u即为缝隙的宽度;
38.(6)当测量到下一个缝隙时又将重复3~5的步骤,直至探测表面平移出激光照射范围。