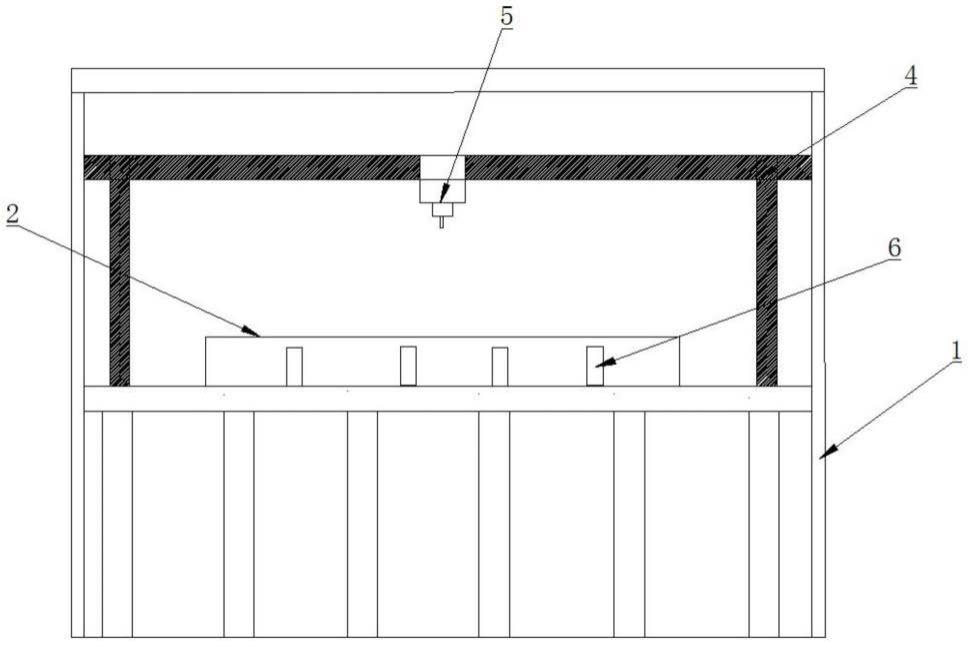
1.本发明涉及超薄柔性玻璃加工技术领域,具体涉及一种用于超薄柔性玻璃的标记装置、尺寸检测方法及叠片方法。
背景技术:2.超薄柔性玻璃(ultra thin glass)以下简称utg,泛指0.02毫米-0.1毫米厚度的钠铝硅酸盐玻璃。主要应用于柔性显示行业,当前最广泛的应用产品为折叠手机,是一种制造加工难度高、经济效益强的高科技产品。
3.utg加工工序简易分为裁切、叠片、精加工、边部处理、强化、修复、检查等工序。现有utg加工生产中utg裁切采用激光设备进行直接切割,将utg原片放置在激光切割设备工作台上,吸附定位在裁切台后激光探头进行产品裁切,裁切后采用设备或人工进行分片处理。在裁切之后叠片之前,通过还会对utg单片进行尺寸、线轮廓度的抽检:人工取片放置在离线抽检设备3d测量仪和轮廓仪上,采取20%产品抽检、首件抽检形式进行检查。检查品质参数要求为尺寸公差、线轮廓度
±
0.1mm。叠片作为玻璃基板边部加工重要工序,其主要作用为将裁切完成后的0.05-0.07mm厚度的utg玻璃用胶水等材质叠加起来使其厚度达到1.0mm以上,然后采用cnc等设备对utg玻璃的边部进行研磨以消除切割应力与裁切裂纹,以此解决单片utg无法进行边部加工的问题。现有的叠片采用工装夹具对utg单片产品进行限位,在每片产品中间点胶,然后通过uv灯照射胶使其固化的生产方式进行叠片作业,一般叠加片数为20片utg产品(单片utg产品厚度0.05mm,叠加后总厚度为1.0mm)。边部加工:采用金刚石磨砂轮对叠片后的边部进行研磨,释放切割应力与改善边部光滑面增加边部受力强度。
4.上述现有工序操作过程存在以下难以避免的问题,会导致产品加工受损、良率下降:
5.(1)现有utg切割设备一般采用激光切割,过程中无法检测产品尺寸、直角度等外观形貌参数。采用抽检的方式进行检测,在后续产品叠片、膜层贴合、显示屏贴合等工序中难免存在一些未抽检到的产品质量不合格导致匹配不良等问题;另一方面采用离线抽检设备3d测量仪和轮廓仪进行检测,需要将产品拿到离线设备上进行检查,涉及到产品搬运与摆放,这个过程增加了单片生产时间与搬运摆放碰撞风险,因此亟需一种能快速检测utg产品形貌尺寸的设备和方法。
6.(2)现有叠片装置都是采用两侧机械或治具辅助定位,对于厚度达到50μm左右的utg产品而言采用这样的定位方式难免会因为其柔性特性导致叠片存在位置偏差,造成研磨后的产品尺寸公差与破片数量较多。
技术实现要素:7.本发明要解决的技术问题是:克服现有技术的不足,提供一种用于超薄柔性玻璃的标记装置、尺寸检测方法及叠片方法,解决了utg产品生产过程中难以检测尺寸、直角度
等形貌参数的问题;在叠片工序中以utg产品上的四角定位标记点为基准点精准定位,无需在产品两侧设置物理定位,提高叠片精度,大大降低了后续cnc边部研磨工序中破片与尺寸不合格的现象,极大提高了产品产出与最终良率。
8.本发明的技术方案为:
9.第一方面,本发明提供了一种用于超薄柔性玻璃的标记装置,包括支架,支架上设置有承载平台,承载平台上设置有定位标识和玻璃固定装置;承载平台的上方安装有十字滑架,十字滑架上安装有打印喷头;十字滑架的驱动装置以及打印喷头分别与控制系统电连接。
10.优选地,所述玻璃固定装置包括抽真空管道,抽真空管道与抽真空装置连接,抽真空装置与控制系统电连接;承载平台为中空结构且承载平台表面设置有若干个真空吸附孔,抽真空管道安装在承载平台内。
11.第二方面,本发明提供了一种利用上述用于超薄柔性玻璃的标记装置检测超薄柔性玻璃尺寸的方法,包括以下步骤:
12.s1玻璃标记:以承载平台的定位标识为原点在控制系统上绘制玻璃的模拟裁切图,在模拟裁切图上每片玻璃靠近四个端点处各预设一个标记点,通过打印喷头在每片玻璃的四个标记点的位置处绘制标记,标记点直径为50-100μm,标记点的颜色为黑色;
13.s2尺寸检测:玻璃裁切后,通过utg自动检测设备对每片玻璃进行拍照并测量照片中每个标记点到相近两条玻璃侧边的距离,将测量的距离与理论距离对比,若对比结果的偏差符合预设标准一,则判定玻璃尺寸合格,可进入下一工序,否则判定玻璃尺寸不合格。
14.优选地,步骤s1中,标记点位于玻璃一角45
°
线上且距相近两侧边500μm处。
15.优选地,步骤s2中,预设标准一为相邻两个标记点距相对两条侧边的距离偏差之和不超过100μm。
16.优选地,还包括步骤s3直角度检测:以四个标记点为基点,分别作水平线和垂直线,四个标记点的水平线与垂直线与玻璃的四条侧边产生八个交点,以该八个交点绘制玻璃的四条边,得到重新绘制的玻璃图形;将绘制的玻璃图形与理论玻璃图形对比,若最大直角度符合预设标准二,则判定玻璃合格,可进入下一工序,否则判定玻璃不合格。
17.优选地,步骤s3中,预设标准二为直角度不超过100μm。
18.第三方面,本发明还提供了一种用于超薄柔性玻璃的叠片方法,包括以下步骤:
19.s1喷涂叠层胶水:将一片通过如权利要求3-7任一项所述的方法检测合格后的玻璃采用抓片叠片装置放置于叠片平台上,采用点胶喷头在第一片玻璃上喷涂叠层胶水;
20.s2叠片:抓片叠片装置四侧边上安装ccd图像传感器,通过抓片叠片装置抓取第二片玻璃,利用ccd图像传感器使第二片玻璃上的标记点与第一片玻璃上的标记点对齐,将第二片玻璃叠放在第一片玻璃上;
21.s3叠层胶水固化:打开uv灯源照射叠层胶水使其固化;
22.s4重复叠片:重复步骤s2和s3的操作至完成15-20片玻璃的叠片。
23.本发明与现有技术相比,具有以下有益效果:
24.本发明通过在产品裁切前对未裁切的整版原片绘图并在每片utg产品四角处设定标记点,该标记点在后续边部研磨或膜层、显示屏等贴合过程中会被消除或覆盖掉,不影响产品正常使用。并且设定标记点的工序可以与裁切工序在一个生产线上进行,不用搬运产
品,也避免了搬运摆放碰撞风险。在utg裁片工序后,通过四角定位标记点配合utg自动检测设备快速检查出utg产品尺寸、直角度等形貌参数,以快速判断产品是否合格,以便进入下一道工序。在叠片工序依据四角定位标记点采用ccd图像传感器与抓片叠片装置配合控制系统实现utg产品的叠片精准定位(误差<20μm),降低了后续边部研磨工序的破片率及尺寸不良率。因此本发明解决了utg产品生产过程中难以检测尺寸、直角度等形貌参数的问题;在叠片工序中以utg产品上的四角定位标记点为基准点精准定位,无需在产品两侧设置物理定位,提高叠片精度,大大降低了后续cnc边部研磨工序中破片与尺寸不合格的现象,极大提高了产品产出与最终良率。
附图说明
25.为了更清楚地说明本发明实施例或现有技术中的技术方案,下面将对实施例或现有技术描述中所需要使用的附图作简单地介绍,显而易见地,对于本领域普通技术人员而言,在不付出创造性劳动的前提下,还可以根据这些附图获得其他的附图。
26.图1是本发明的标记装置的结构示意图。
27.图2是本发明的标记装置承载平台的俯视图。
28.图3是utg玻璃的模拟裁切图。
29.图4是标记点在utg玻璃上的位置示意图。
30.图5是尺寸偏差计算示意图。
31.图6是直角度计算示意图。
32.图7是本发明的叠片装置的结构示意图。
33.图中,1-支架、2-承载平台、3-定位标识、4-十字滑架、5-打印喷头、6-抽真空管道、7-真空吸附孔、8-标记点、9-叠片平台、10-抓片叠片装置、11-点胶喷头、12-ccd图像传感器、13-utg玻璃。
具体实施方式
34.为了使本技术领域的人员更好地理解本发明中的技术方案,下面将结合本发明实施例中的附图,对本发明实施例中的技术方案进行清楚、完整地描述,显然,所描述的实施例仅仅是本发明一部分实施例,而不是全部的实施例。基于本发明中的实施例,本领域普通技术人员在没有做出创造性劳动前提下所获得的所有其他实施例,都应当属于本发明保护的范围。
35.实施例1
36.如图1-2所示,本实施例提供了一种适用于超薄柔性玻璃的标记装置,包括支架1,支架1上设置有承载平台2,承载平台2上设置有定位标识3和玻璃固定装置;承载平台2的上方安装有十字滑架4,十字滑架4上安装有打印喷头5;十字滑架4的驱动装置以及打印喷头5分别与控制系统电连接。
37.其中玻璃固定装置可采用现有的装置,本发明中所述玻璃固定装置包括抽真空管道6,抽真空管道6与抽真空装置连接,抽真空装置与控制系统电连接;承载平台2为中空结构且承载平台2表面设置有若干个真空吸附孔7,抽真空管道6安装在承载平台2内。打印喷头可采用现有的能实现在玻璃上绘制标记点的市购产品,如武汉三工光电设备制造有限公
司的sdm3;十字滑架的作用是带动打印喷头在多个区域绘制标记点,可采用能实现上述功能的市购产品,如飞创直线模组(苏州)有限公司的fcl200-r5。
38.实施例2
39.利用实施例1的用于超薄柔性玻璃的标记装置检测超薄柔性玻璃尺寸的方法,包括以下步骤:
40.s1玻璃标记
41.s11:将utg原片玻璃按照承载平台2上的定位标识3对位放置,真空吸附定位在承载平台2上;
42.s12:以承载平台2的定位标识3为原点在控制系统上采用cad或类似软件绘制出玻璃的模拟裁切图(如图3所示);
43.s13:在模拟裁切图上每片utg玻璃13靠近四个端点处、位于玻璃四个角45
°
线上且距相近两侧边500μm处预设四个标记点8;
44.s14:控制系统通过控制十字滑架4使打印喷头5在每片玻璃的四个标记点8的位置处绘制标记,标记点8尺寸为50-100μm,颜色为黑色(如图4所示)。标记点的颜色规定为黑色是因为黑色是最常见的标记颜色,生产工艺简便,且utg自动检测设备采用线性相机作为图像收集单元,线性相机成型由灰阶成像,黑色标记与utg产品其余区域成像灰阶对比明显更容易识别,最后utg产品与手机贴合时黑色标记位置对应显示屏黑边区域更容易做隐藏处理。
45.s2尺寸检测
46.s21:通过utg自动检测设备的高精度摄像头完成utg玻璃的整体拍照,并找到照片上玻璃的标记点8。其中utg自动检测设备通常用于检测玻璃内部缺陷,每个玻璃加工厂所用utg自动检测设备稍有差异,但都能实现本发明的目的。本发明的utg自动检测设备由中科慧远视觉技术(洛阳)有限公司提供。
47.s22:以标记点8为基点测量标记点8到相近两条玻璃侧边的距离,将测量的距离与理论距离对比,若对比结果的偏差符合预设标准一,则判定玻璃尺寸合格,可进入下一工序,否则判定玻璃尺寸不合格。其中,预设标准一可根据实际需要而设定,优选地,本发明步骤s2中,预设标准一为相邻两个标记点8距相对两条侧边的距离偏差之和不超过100μm,如图5所示,a点距其理论位置的距离加上d点距其理论位置的距离之和不可超过100μm。
48.实施例3
49.在实施例2的基础上,本实施例还包括步骤s3直角度检测:以四个标记点8为基点,分别作水平线和垂直线,四个标记点8的水平线与垂直线与玻璃的四条侧边产生八个交点(如图5所示的a-h点),以该八个交点绘制玻璃的四条边,得到重新绘制的玻璃图形;将绘制的玻璃图形与理论玻璃图形对比,若最大直角度(如图6所示,倾斜侧边与理论侧边的一端重叠,而倾斜侧边另一端至理论侧边另一端的距离d即为直角度)符合预设标准二,则判定玻璃合格,可进入下一工序,否则判定玻璃不合格。其中,预设标准二可根据实际需要而设定,优选地,本发明步骤s3中,预设标准二为直角度不超过100μm。
50.以200万片utg玻璃年产量工厂为例,采用该检测方法,可省略原有生产采用3d测量仪进行20%抽检的检测过程,提升了生产效率5%,每天可提升275片utg玻璃的产出。现有生产过程中,尺寸不良或直角度批量不良发生率为2%,采用本发明的检测方法可提前半
小时检测出产品不良,能够及时拦截并及时调整产线设备工艺以改善产品质量,可将尺寸不良或直角度批量不良发生率降低至0.5%,每日提升83片良品产出,年产出多达3.03万片。
51.实施例4
52.每个玻璃加工厂所用叠片装置稍有差异,但都能实现本发明的目的。本发明的叠片装置由坤轮机械有限公司提供,如图7所示,包括叠片平台9、抓片叠片装置10、点胶喷头11、取出装置和控制系统,并在抓片叠片装置10的四个侧边上安装ccd图像传感器12。
53.用于超薄柔性玻璃的叠片方法,包括以下步骤:
54.s1喷涂叠层胶水:将一片通过实施例2和3的方法检测合格后的玻璃利用ccd图像传感器12使其以叠片平台9上的定位标识为基点采用抓片叠片装置10放置于叠片平台9上,然后通过点胶喷头11在第一片玻璃上喷涂叠层胶水(叠层胶水透光率>80%);
55.s2叠片:通过抓片叠片装置10抓取第二片玻璃,利用ccd图像传感器12使第二片玻璃上的标记点8与第一片玻璃上的标记点8对齐,将第二片玻璃叠放在第一片玻璃上;
56.s3叠层胶水固化:打开uv灯源照射叠层胶水使其固化;
57.s4重复叠片:重复步骤s2和s3的操作至完成15-20片玻璃的叠片。
58.叠片完成后,叠片平台9解除对玻璃的真空吸附,再通过取出装置将完成品拿走送往下一工序。
59.以200万片utg玻璃年产量工厂为例,原有工装夹具叠片方法的偏差一般为
±
50μm(即两片玻璃叠片后,上下两片玻璃边部的错位距离),导致后续边部研磨工序产出的破片率与尺寸不良率共计5%,而采用本实施例的标记定位叠片方法,偏差为
±
20μm,在后续边部研磨工序的破片与尺寸不良率降低至2%,每日提升良品产出165片,年产出多达6.03万片。
60.尽管通过参考附图并结合优选实施例的方式对本发明进行了详细描述,但本发明并不限于此。在不脱离本发明的精神和实质的前提下,本领域普通技术人员可以对本发明的实施例进行各种等效的修改或替换,而这些修改或替换都应在本发明的涵盖范围内/任何熟悉本技术领域的技术人员在本发明揭露的技术范围内,可轻易想到变化或替换,都应涵盖在本发明的保护范围之内。因此,本发明的保护范围应所述以权利要求的保护范围为准。