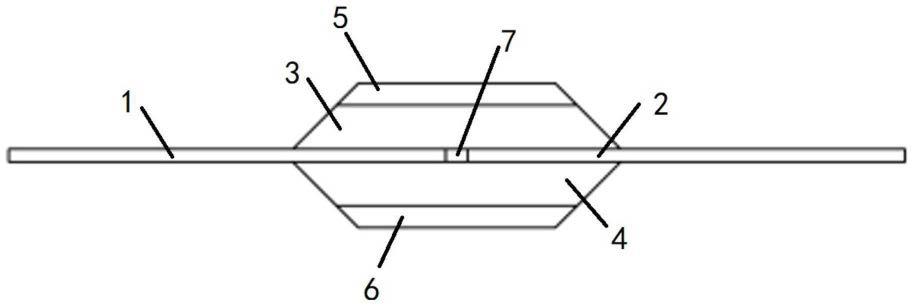
1.本发明属于胶粘剂测试技术领域,具体涉及一种测试胶粘剂粘接界面强度的双搭接试样及测试方法。
背景技术:2.粘接是材料或构件相互连接的最重要方式,粘接的可靠性主要取决于胶粘剂的拉伸剪切性能,要保证粘接的可靠,就须有优良的拉伸剪切性能。国内风电行业快速发展,日趋成熟,大型风机叶片大多采用组装方式制造,叶片壳体分别在两个模具上灌注或手糊成型,之后采用胶粘剂将两个壳体和腹板粘接形成整体叶片,其中所使用的胶粘剂是叶片的重要结构材料,因而准确测试与评价结构胶的界面粘结剪切强度对于结构设计和安全可靠性评价至关重要。
3.目前对于胶粘剂界面拉伸剪切性能的测试方法主要有gb/t7124、iso4587、bs en 1465等国家、国际标准中提出的拉伸剪切强度测试方法,试样采用的是单搭接的形式。对单搭接试验,胶层太厚、太薄其强度都较低。这通常由于随着胶层厚度增加,必然导致胶层内聚强度迅速下降;胶层越厚,由于温度变化引起的内应力也大,这些内应力可造成胶接接头强度损失。胶层太薄,则胶接面上容易缺胶,缺胶处便成为胶粘剂膜的缺陷,在受力时,于缺陷周围容易产生应力集中,从而加速胶膜破裂,导致胶接强度低。因此,对于单搭接试验,为了保证胶接街头具有最高的胶接强度,对胶层厚度应严格控制,通常,胶接刚性制件的大多数胶黏剂,其胶层厚度对有机胶黏剂控制在0.05~0.15mm,无机胶黏剂控制在0.10~0.20mm,在保证不缺胶的前提下,尽量涂薄一些为好。
4.对于风电叶片行业来说,叶片壳体分别在两个模上成型,之后采用胶黏剂将2个壳体、腹板和芯材粘接形成整体叶片。叶片运行中将经受上亿次弯曲振动,粘结部分承受巨大的剪切力,因此风电叶片行业使用结构胶在实际工况中的粘结厚度较厚,大多数超过10mm以上,用单搭接法测试10mm粘接厚度以上的测试时,由于胶层较厚,测试过程中易出现施加的载荷偏离轴向,结果不太理想。且粘结基材为复合材料,由于复合材料在制备过程中,其上下表面采用的工艺不一样,导致基材的上下表面在与结构胶的拉伸剪切强度不一样。现有的测试方法不能测试粘结胶层较厚的情况,不能同时测试复合材料基材的两个粘接表面的拉伸剪切性能。
技术实现要素:5.本发明解决的技术问题是提供一种测试胶粘剂粘接界面强度的双搭接试样及测试方法,通过采用双搭接模式,可以在拉伸剪切试验中,使用更厚的胶粘剂,适用于风电叶片用复合材料的强度测定,同时可以实现两个粘接表面拉伸剪切强度的计算。
6.为了解决上述问题,本发明的一个方面提供一种测试胶粘剂粘接界面强度的双搭接试样,包括:
7.第一中间基材板、第二中间基材板、第一胶粘剂层、第二胶粘剂层、第一外表面基
材板、第二外表面基材板;
8.所述第一中间基材板、所述第二中间基材板的厚度相同;所述第一中间基材板与所述第二中间基材板的上下表面齐平设置,且所述第一中间基材板与所述第二中间基材板之间留有间隙;所述第一中间基材板与所述第二中间基材板的上表面设置所述第一胶粘剂层,所述第一中间基材板与所述第二中间基材板的下表面设置所述第二胶粘剂层;所述第一胶粘剂层的上表面设置所述第一外表面基材板,所述第二胶粘剂层的下表面设置所述第二外表面基材板;所述第一中间基材板和所述第二中间基材板的外端在长度方向上延伸至超出所述第一胶粘剂层、所述第二胶粘剂层,以适于夹具夹持。
9.优选地,所述第一中间基材板与所述第二中间基材板之间的间隙中设有定位块,所述定位块的厚度与所述第一中间基材板相同。
10.优选地,所述第一中间基材板、所述第二中间基材板、所述第一外表面基材板、所述第二外表面基材板为单向纤维复合材料。
11.优选地,所述第一中间基材板、所述第二中间基材板、所述第一外表面基材板、所述第二外表面基材板的厚度不小于5mm;
12.所述第一胶粘剂层、所述第二胶粘剂层的厚度为5-30mm。
13.优选地,所述第一外表面基材板、所述第二外表面基材板的长度为55mm,宽度为25mm;
14.所述第一胶粘剂层与所述第一中间基材板、所述定位块、所述第二中间基材板的整体的粘接面的长度为(55+2*d)mm;
15.所述第一中间基材板与所述第二中间基材板的总长度至少为(155+2*d)mm;所述第一中间基材板、所述第二中间基材板的宽度为25mm;
16.其中,d为所述第一胶粘剂层的厚度;
17.所述定位块的长度为2-5mm,宽度为25mm。
18.优选地,所述第一外表面基材板的两端的端面与所述第一外表面基材板的下表面的夹角为45
°
;
19.所述第二外表面基材板的两端的端面与所述第二外表面基材板的上表面的夹角为45
°
;
20.所述第一胶粘剂层的两端的端面与所述第一中间基材板、所述第二中间基材板上表面的夹角为45
°
;
21.所述第二胶粘剂层的两端的端面与所述第一中间基材板、所述第二中间基材板下表面的夹角为45
°
。
22.本发明的另一方面提供一种上述的测试胶粘剂粘接界面强度的双搭接试样的制备方法,包括以下步骤:
23.s1.制备所述第一中间基材板、所述第二中间基材板、所述第一外表面基材板、所述第二外表面基材板,并对所述第一中间基材板、所述第二中间基材板、所述第一外表面基材板、所述第二外表面基材板的粘接面进行表面处理;
24.s2.将所述第一中间基材板、所述第二中间基材板放置于工作台,所述第一中间基材板与所述第二中间基材板预留间隙;
25.s3.在所述第一中间基材板、所述第二中间基材板的第一粘接面的边缘处设置第
一定位工装,所述第一定位工装用于限定涂抹的胶粘剂的厚度;
26.s4.将胶粘剂涂抹至所述第一中间基材板、所述第二中间基材板的第一粘接面上,达到设定厚度,形成第一胶粘剂层;
27.s5.在所述第一胶粘剂层上设置第一外表面基材板;
28.s6.将所述第一外表面基材板与所述第一中间基材板、所述第二中间基材板固定,然后进行预固化;
29.s7.在所述第一中间基材板、所述第二中间基材板的第二粘接面的边缘处设置第二定位工装,所述第二定位工装用于限定涂抹的胶粘剂的厚度;
30.s8.将胶粘剂涂抹至所述第一中间基材板、所述第二中间基材板的第二粘接面上,达到设定厚度,形成第二胶粘剂层;
31.s9.将所述第二外表面基材板与所述第一中间基材板、所述第二中间基材板固定,然后进行固化;
32.s10.按照设定尺寸,对固化后的制品进行加工,得到所述测试胶粘剂粘接界面强度的双搭接试样。
33.优选地,步骤s2中还包括在所述第一中间基材板与所述第二中间基材板的间隙中设置定位块,并对所述定位块的表面涂覆脱模剂。
34.本发明的再一方面提供一种测试胶粘剂粘接界面强度的方法,包括以下步骤:
35.a1.制备上述的测试胶粘剂粘接界面强度的双搭接试样;
36.a2.将所述双搭接试样的所述第一中间基材板、所述第二中间基材板的端部放入夹具,并保证轴向对中;
37.a3.在所述双搭接试样的轴向施加连续载荷,连续加载直至所述双搭接试样破坏,记录破坏形式,计算外表面基材粘接面拉伸剪切强度和中间基材粘接面拉伸剪切强度。
38.优选地,步骤a3中,外表面基材粘接面拉伸剪切强度τw、中间基材粘接面拉伸剪切强度τn的计算方法为:
[0039][0040][0041]
其中,p为试样破坏时的载荷;aw为所述第一外表面基材板粘接面面积或所述第二外表面基材板粘接面面积;an为所述第一中间基材板的第一粘接面面积与所述第二中间基材板的第一粘接面面积之和或所述第一中间基材板的第二粘接面面积与所述第二中间基材板的第二粘接面面积之和。
[0042]
本发明与现有技术相比,具有以下有益效果:
[0043]
本发明的测试胶粘剂粘接界面强度的双搭接试样,采用了双搭接形式的试样,相比于单搭接形式,可弥补对粘接厚度较厚的拉剪试验的空缺,且双搭接剪切试验的受力比较均衡,从而减小了单搭接试验中的劈裂应力和剥离应力,在试验过程中,也具有更高的失效位移和更好的失效承载能力。此外,当前对于复合材料的制备,其上下表面的制备工艺不同,在实际应用中则需要分开考虑。但由于基材的上下表面在与结构胶的拉伸剪切强度不
一致,而单搭接试样无法分别对两个表面的拉伸剪切强度进行计算,对于双搭接试样,由于试样特性,可通过改变试样中两个外表面基材板来实现分别测试上下表面的拉伸剪切强度,(即试样上的两个中间基材板是一种材料,通过计算公式可测试中间基材板粘接面的强度,两个外表面基材板可以是与中间基材板一样的材料,也可以是不一样的材料,如果采用不同的材料,就可以分别测试上述两种材料的剪切强度),对胶黏剂的性能有着更加充分的了解,对其在实际应用中的性能预测提供了一个良好的参数。在工程应用中,产品的服役时间久,而双搭接接头失效强度明显高于单搭接接头,在一定条件下可以用双搭接连接来代替单搭接连接以获取更大的承载能力,可以提高产品的使用年限,缩减成本。
附图说明
[0044]
图1是本发明实施例1所述的测试胶粘剂粘接界面强度的双搭接试样的主视图;
[0045]
图2是本发明实施例1所述的测试胶粘剂粘接界面强度的双搭接试样的结构示意图;
[0046]
图3是本发明实施例3中测试胶粘剂粘接界面强度的双搭接试样的结构尺寸标注图。
[0047]
其中:1-第一中间基材板;2-第二中间基材板;3-第一胶粘剂层;4-第二胶粘剂层;5-第一外表面基材板;6-第二外表面基材板;7-定位块。
具体实施方式
[0048]
下面将结合本发明的实施例,对本发明的技术方案进行清楚、完整地描述,显然,所描述的实施例仅仅是本发明一部分实施例,而不是全部的实施例。基于本发明中的实施例,本领域普通技术人员在没有做出创造性劳动前提下所获得的所有其他实施例,都属于本发明保护的范围。
[0049]
实施例1
[0050]
如图1、图2所示,本实施例的一种测试胶粘剂粘接界面强度的双搭接试样,包括:
[0051]
第一中间基材板1、第二中间基材板2、第一胶粘剂层3、第二胶粘剂层4、第一外表面基材板5、第二外表面基材板6;
[0052]
第一中间基材板1、第二中间基材板2的厚度相同;第一中间基材板1与第二中间基材板2的上下表面齐平设置,且第一中间基材板1与第二中间基材板2之间留有间隙;第一中间基材板1与第二中间基材板2的上表面设置第一胶粘剂层3,第一中间基材板1与第二中间基材板2的下表面设置第二胶粘剂层4;第一胶粘剂层3的上表面设置第一外表面基材板5,第二胶粘剂层4的下表面设置第二外表面基材板6;第一中间基材板1和第二中间基材板2的外端在长度方向上延伸至超出第一胶粘剂层3、第二胶粘剂层4,以适于夹具夹持。
[0053]
目前胶粘剂界面拉伸剪切性能的测试方法中,试样主要采用单搭接的形式,为了保证胶接街头胶接强度,需要对胶层厚度严格控制,通常,胶接刚性制件的大多数胶黏剂,其胶层厚度对有机胶黏剂控制在0.05~0.15mm,无机胶黏剂控制在0.10~0.20mm。然而对于风电叶片行业,结构胶在实际工况中的粘结厚度较厚,大多数超过10mm以上,单搭接无法实现10mm粘接厚度测试。本实施例中,采用了双搭接形式的试样,可弥补对粘接厚度较厚的拉剪试验的空缺,且双搭接剪切试验的受力比较均衡,从而减小了单搭接试验中的劈裂应
力和剥离应力,在试验过程中,也具有更高的失效位移和更好的失效承载能力。此外,当前对于复合材料的制备,其上下表面的制备工艺不同,在实际应用中则需要分开考虑。但由于基材的上下表面在与结构胶的拉伸剪切强度不一致,而单搭接试样无法分别对上下表面的拉伸剪切强度进行计算,对于双搭接试样,由于试样特性,可通过改变试样中两个外表面基材板来实现分别测试基材两个表面的拉伸剪切强度,即试样上的两个中间基材板是一种材料,通过计算公式可测试中间基材板粘接面的强度,两个外表面基材板可以是与中间基材板一样的材料,也可以是不一样的材料,如果采用不同的材料,就可以分别测试上述两种材料的粘接面的拉伸剪切强度。对胶黏剂的性能有着更加充分的了解,对其在实际应用中的性能预测提供了一个良好的参数。在工程应用中,产品的服役时间久,而双搭接接头失效强度明显高于单搭接接头,在一定条件下可以用双搭接连接来代替单搭接连接以获取更大的承载能力,可以提高产品的使用年限,缩减成本。
[0054]
进一步地,第一中间基材板1与第二中间基材板2之间的间隙中设有定位块7,定位块7的厚度与第一中间基材板1相同。定位块用于两个中间基材板放置粘接时的定位。定位块为硅橡胶材质。
[0055]
进一步地,第一中间基材板1、第二中间基材板2、第一外表面基材板5、第二外表面基材板6为单向纤维复合材料。风电行业中主要采用的是单向纤维复合材料,且单向复合材料的刚度较高,测试时基材不宜产生变形。
[0056]
进一步地,第一中间基材板1、第二中间基材板2、第一外表面基材板5、第二外表面基材板6的厚度大于5mm,为保证基材板的刚度,其厚度至少为5mm。本实施例中,第一中间基材板1、第二中间基材板2、第一外表面基材板5、第二外表面基材板6的厚度为5mm。
[0057]
进一步地,第一胶粘剂层、第二胶粘剂层的厚度为5-30mm。本实施例中,第一胶粘剂层、第二胶粘剂层的厚度为10mm。
[0058]
进一步地,第一外表面基材板、第二外表面基材板的长度为55mm,宽度为25mm。根据前期测试经验,外表面基材板长度选择55mm,测试效果比较好,且制样较为容易。
[0059]
进一步地,第一胶粘剂层与第一中间基材板、定位块、第二中间基材板的整体的粘接面的长度为(55+2*d)mm;第一中间基材板与第二中间基材板的总长度至少为(155+2*d)mm;第一中间基材板、第二中间基材板的宽度为25mm;其中,d为第一胶粘剂层的厚度。中间基材板太短夹持距离不够,太长了基材容易变形,采用该长度,试验的时候方便夹持,且基材不易变形。本实施例中,第一胶粘剂层与第一中间基材板、定位块、第二中间基材板的粘接面的长度分别为35mm、5mm、35mm,整体的粘接面的长度为75mm;第一中间基材板与第二中间基材板的长度均为100mm,总长度为200mm。
[0060]
进一步地,定位块的长度为2-5mm,宽度为25mm。本实施例中,定位块的长度为5mm。
[0061]
进一步地,第一外表面基材板的两端的端面与第一外表面基材板的下表面的夹角为45
°
;第二外表面基材板的两端的端面与第二外表面基材板的上表面的夹角为45
°
;第一胶粘剂层的两端的端面与第一中间基材板、第二中间基材板上表面的夹角为45
°
;第二胶粘剂层的两端的端面与第一中间基材板、第二中间基材板下表面的夹角为45
°
。
[0062]
实施例2
[0063]
本实施例的测试胶粘剂粘接界面强度的双搭接试样的制备方法,包括以下步骤:
[0064]
s1.按照实施例1中要求的长度、宽度、厚度,采用真空袋压成型、拉挤成型、缠绕成
型中的一种方法制备所述第一中间基材板、所述第二中间基材板、所述第一外表面基材板、所述第二外表面基材板,并对所述第一中间基材板、所述第二中间基材板、所述第一外表面基材板、所述第二外表面基材板的粘接面进行打磨;
[0065]
s2.将所述第一中间基材板、所述第二中间基材板放置于平整的粘接工作台上,所述第一中间基材板与所述第二中间基材板中间放置定位块,并对所述定位块的表面涂覆脱模剂;
[0066]
s3.在所述第一中间基材板、所述第二中间基材板的上面粘接面的边缘处设置第一定位工装,所述第一定位工装用于限定涂抹的胶粘剂的厚度;
[0067]
s4.将粘接用的粘结胶进行在脱泡处理,去除粘结胶内部的气泡,脱泡完后用专用喷枪将粘结胶涂抹至所述第一中间基材板、所述第二中间基材板的上面粘接面上,达到设定厚度,形成第一胶粘剂层;
[0068]
s5.在所述第一胶粘剂层上放置第一外表面基材板;
[0069]
s6.用压力夹将所述第一外表面基材板与所述第一中间基材板、所述第二中间基材板固定,然后于常温条件下进行预固化;
[0070]
s7.待粘结胶预固化完成后,在所述第一中间基材板、所述第二中间基材板的下面粘接面的边缘处设置第二定位工装,所述第二定位工装用于限定涂抹的胶粘剂的厚度;
[0071]
s8.将胶粘剂涂抹至所述第一中间基材板、所述第二中间基材板的下面粘接面上,达到设定厚度,形成第二胶粘剂层;
[0072]
s9.用压力夹将所述第二外表面基材板与所述第一中间基材板、所述第二中间基材板固定,然后放入烘箱,按照要求的固化制度进行后固化;
[0073]
s10.固化完成后,按照设定尺寸,对固化后的制品进行加工,得到所述测试胶粘剂粘接界面强度的双搭接试样。
[0074]
实施例3
[0075]
本实施例的测试胶粘剂粘接界面强度的方法,包括以下步骤:
[0076]
a1.采用实施例2的方法制备测试胶粘剂粘接界面强度的双搭接试样;
[0077]
a2.采用万能材料试验机,将所述双搭接试样的所述第一中间基材板、所述第二中间基材板的端部放入夹具,并保证轴向对中;
[0078]
a3.在所述双搭接试样的轴向施加连续载荷,实验速度1~5mm/min,连续加载直至所述双搭接试样破坏,记录破坏形式,计算外表面基材粘接面拉伸剪切强度和中间基材粘接面拉伸剪切强度,外表面基材粘接面拉伸剪切强度τw、中间基材粘接面拉伸剪切强度τn的计算方法为:
[0079][0080][0081]
其中,p为试样破坏时的载荷;aw为第一外表面基材板的粘接面面积,如图3所示,本实施例中,即b1*lo,b1为第一外表面基材板的宽度;an为中间基材板粘接面面积之和,本实施例中,即b2*(li1+li2),b2为中间基材板的宽度,li1为第一中间基材板的上面粘接面的
长度,li2为第二中间基材板的上面粘接面的长度。
[0082]
显然,上述实施例仅仅是为清楚地说明所作的举例,而并非对实施方式的限定。对于所属领域的普通技术人员来说,在上述说明的基础上还可以做出其它不同形式的变化或变动。这里无需也无法对所有的实施方式予以穷举。而由此所引伸出的显而易见的变化或变动仍处于本发明创造的保护范围之中。