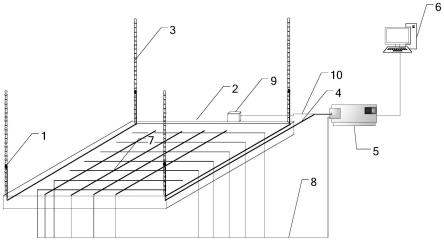
1.本发明属于立体车库状态检测技术领域,尤其涉及一种智能立体车库安全状态检测方法及系统。
背景技术:2.本部分的陈述仅仅是提供了与本发明相关的背景技术信息,不必然构成在先技术。
3.随着经济的发展和人们生活水平的提高,国内私家车的拥有量呈快速上升趋势,车辆猛增和与之配套停车设施滞后的矛盾由此产生,城市泊车压力越来越大。在这样的背景下,一种既能合理利用城市空间,又能有效缓解城市停车难的智能立体车库便应运而生。立体车库属于特种设备,虽然定期会有专业的工程人员对车库进行检修,但是立体车库使用频繁,在长期运营过程中,其升降载车系统是最容易出现问题的地方,因升降载车设备故障导致的翻车或挂碰事故时常出现。立体车库翻车或挂碰事故主要原因是升降载车平板倾斜与载车板承载能力不足引起的载车板脱落导致的,引起升降载车平板倾斜和承载能力不足的主要原因是与之相连的链条发生故障,导致支撑升降载车平板的四根链条变形不均或承载能力下降。
4.同时,随着投入运营的立体车库的服役时间增长,载车板逐渐老化而产生超限形变甚至裂缝,造成严重的安全隐患,处理不及时极易发生财产损失甚至对使用者生命安全造成威胁。目前对于立体车库升降系统安全问题主要侧重于电机、链条检修、保养等工作,在设备服役期的安全状态检测的实时性和设备安全隐患预报的超前性方面略有不足,同时在大型立体车库的巡检任务中,巡检员常常需要进行高空作业,稍有不慎将会引起安全事故。
技术实现要素:5.为克服上述现有技术的不足,本发明提供了一种智能立体车库关键设备安全状态检测方法及系统。能够重构出直观的载车板状态,对载车板及其传动结构进行安全诊断。
6.为实现上述目的,本发明的一个或多个实施例提供了如下技术方案:
7.一种智能立体车库安全状态检测方法,所述立体车库载车板的底部表面设有光纤光栅阵列传感器,包括交错布置的多条光纤;所述方法包括以下步骤:
8.获取沿光纤方向的多个中心波长变化率,对所述载车板的表面形状进行重构;
9.根据所述载车板的表面形状,对所述载车板的状态进行评价。
10.进一步地,根据所述多条光纤交点处的中心波长变化率,计算各个交点的空间坐标;
11.根据所述载车板形状和各个交点的空间坐标,对所述载车板的三维应变场进行重建。
12.进一步地,对所述载车板的表面形状进行重构包括:
13.对所述多个中心波长变化率进行采样;
14.将采样点的中心波长变化量转化为该点的应变信息,将各采样点的应变信息转换为位移信息;
15.基于各采样点的位移信息,对所述载车板的表面形状进行初步重构。
16.进一步地,对所述载车板的表面形状进行初步重构后,还进行修正:
17.基于极限学习机分类器,对初步重构的载车板形状进行修正,得到修正后的载车板形状。
18.进一步地,对所述载车板的三维应变场进行重建包括:
19.根据所述多条光纤交点处的中心波长变化率,计算各交点的正交曲率信息;
20.将所述光纤光栅正交阵列传感器的每根光纤看作一条三维空间曲线,针对每根光纤上的各个交点,依次根据相应正交曲率信息进行空间坐标求解。
21.一个或多个实施例提供了一种智能立体车库安全状态检测系统,其特征在于,包括设于所述立体车库载车板的底部表面的光纤光栅阵列传感器、光纤解调仪和上位机;所述光纤光栅阵列传感器包括交错布置的多条光纤;所述光纤光栅阵列传感器用于采集沿光纤方向的多个中心波长变化率,经由光纤解调仪传输至上位机;所述上位机被配置为:
22.获取沿光纤方向的多个中心波长变化率,对所述载车板的表面形状进行重构;
23.根据所述载车板的表面形状,对所述载车板的状态进行评价。
24.进一步地,根据所述多条光纤交点处的中心波长变化率,计算各个交点的空间坐标;
25.根据所述载车板形状和各个交点的空间坐标,对所述载车板的三维应变场进行重建。
26.进一步地,所述系统还包括多个光纤光栅温度补偿应变传感器,分别设置于载车板的多个传动链条上,用于采集传动链条的应力信息,经由光纤解调仪传输至上位机。
27.进一步地,所述系统还包括光纤光栅倾角仪,设置于载车板上,用于采集载车板的倾角信息,经由光纤解调仪传输至上位机。
28.进一步地,所述上位机对所述载车板的表面形状、三维应变场、链条应力信息以及载车板的倾角信息中的一个或多个进行可视化,并对运行状态进行显示。
29.以上一个或多个技术方案存在以下有益效果:
30.基于利用光纤光栅传感器采集应变信息从而对立体车库关键设备进行状态检测,监测传动链条应力情况、载车板倾角情况,并且重构载车板应变场,能够直观反应载车板及其传动系统的安全状态,并根据其状态对可能出现的安全隐患进行超前预报,对立体车库进行全寿命周期的安全诊断。
附图说明
31.构成本发明的一部分的说明书附图用来提供对本发明的进一步理解,本发明的示意性实施例及其说明用于解释本发明,并不构成对本发明的不当限定。
32.图1为本发明的智能立体车库关键设备安全状态检测系统结构示意图;
33.图2为本发明的载车板应变场重构方法流程图;
34.图3为本发明的光纤光栅正交阵列传感器单根光纤重构应变场算法的计算示意
图。
35.图中,1——光纤光栅温度补偿应变传感器,2——载车板,3——载车板传动链条,4、8、10——光纤传输线,5——光纤解调仪,6——上位机,7——光纤光栅正交阵列传感器,8——光纤光栅倾角仪。
具体实施方式
36.应该指出,以下详细说明都是示例性的,旨在对本发明提供进一步的说明。除非另有指明,本文使用的所有技术和科学术语具有与本发明所属技术领域的普通技术人员通常理解的相同含义。
37.需要注意的是,这里所使用的术语仅是为了描述具体实施方式,而非意图限制根据本发明的示例性实施方式。如在这里所使用的,除非上下文另外明确指出,否则单数形式也意图包括复数形式,此外,还应当理解的是,当在本说明书中使用术语“包含”和/或“包括”时,其指明存在特征、步骤、操作、器件、组件和/或它们的组合。
38.在不冲突的情况下,本发明中的实施例及实施例中的特征可以相互组合。
39.实施例一
40.本实施例公开了一种智能立体车库关键设备安全状态检测系统,多个光纤光栅温度补偿应变传感器1、光纤光栅正交阵列传感器4、光纤光栅倾角仪9、光纤解调仪5和上位机6。所述多个光纤光栅温度补偿应变传感器1、光纤光栅正交阵列传感器4和光纤光栅倾角仪9分别通过光纤传输线与所述光纤解调仪5连接,所述光纤解调仪5连接至所述上位机。光纤解调仪实时采集温度补偿光纤光栅传感器,光纤光栅正交阵列和光纤光栅倾角仪的中心波长,通过工业互联网传给数据处理单元,数据处理单元分析中心波长得到载车板传动链条与载车板的应变分布以及载车板的倾角,并进行相关计算重构出载车板及其传动系统状态,包括倾角,变形场以及裂纹状态,并给出安全诊断及危险预警。
41.其中,所述多个光纤光栅温度补偿应变传感器1分别设置于载车板的多个传动链条3上,本实施例光纤光栅温度补偿应变传感器1数量为四个,分别通过粘贴的方式固定与四根载车板传动链条3上。所述四个温度补偿光纤光栅应变传感器布置于一根光纤上,通过粘贴的方式固定于所述载车板传动链条上,用于检测载车板传动链条应变分布。所述光纤光栅倾角仪9设置于载车板2上,具体为设置与载车板2后方,用于检测载车板各个方向的倾角信息。所述光纤光栅正交铺设形成光纤光栅正交阵列传感器,具体地,所述光纤光栅正交阵列传感器由四条纵肋七条横肋正交等间距铺设组成,通过环氧树脂固定于载车板底部,用于检测载车板应变分布。
42.在载车状态时,载车板传动链条3受力产生应变,载车板2倾角状态发生变化,所述光纤光栅温度补偿应变传感器1获取应变信息,所述光纤光栅倾角仪9获取倾角信息,所述光纤光栅正交阵列传感器4获取载车板应变场分布,三者均以中心波长变化量的形式通过光纤传输线接入光纤解调仪5,光纤解调仪5通过工业互联网将中心波长数据传给上位机6,上位机处理中心波长信息,分析并计算出载车板传动链条的拉力和载车板倾角。
43.如图1所示,光纤光栅正交阵列传感器7由4条纵肋光纤和7条横肋光栅正交排列,通过环氧树脂涂覆固定于载车板底部,当载车板发生形变时,光纤光栅正交阵列传感器4的每根光纤同载车板协同形变,采集到应变信息,传入光纤解调仪5,光纤解调仪5将数据通过
工业互联网传给上位机6,上位机6接收测点中心波长,根据相关公式计算各个测点曲率,根据曲率信息初步重构出载车板的应变状态,再根据算法进行智能修正,最后输出应变场的分布,并给出安全评定。具体过程如下:
44.步骤1:获取所述光纤光栅正交阵列传感器7采集的沿光纤方向的多个中心波长变化率,对载车板形状进行重构。
45.所述步骤1具体包括:
46.步骤1.1:获取所述光纤光栅正交阵列传感器7采集的沿光纤方向的多个中心波长变化率,并对其进行采样,以有限点来描述整条光纤光栅的感测数据;
47.步骤1.2:将采样点的中心波长变化量转化为该点的应变信息,将各采样点的应变信息转换为位移信息;从而能够反映载车板上各个位置的相对变形,便于后续载车板表面形状的重构;
48.步骤1.3:基于各采样点的位移信息,对所述载车板的表面形状进行初步重构;
49.步骤1.4:基于极限学习机分类器,对初步重构的载车板形状进行修正,得到修正后的载车板形状。
50.光纤解调仪采集测点处的中心波长,把测点的波长变化量转化为测点附近区域的曲率,基于变形传感重构算法对光纤光栅正交阵列传感器的弯曲形状进行初次重构。
51.将各个测点位移数据作为输入,输入训练好的极限学习机分类器(智能修正算法),对初次重构的弯曲形状进行分类,并采用相应的最优系数进行修正,得到准确的弯曲形状,流程如图2所示。
52.步骤2:获取所述光纤光栅正交阵列传感器7交点处的中心波长变化率,换算为正交曲率信息,计算各个交点在空间坐标系中的位置坐标。
53.所述步骤2具体包括:
54.步骤2.1:获取所述光纤光栅正交阵列传感器7交点处的中心波长变化率,换算为正交曲率信息;
55.步骤2.2:将所述光纤光栅正交阵列传感器的每根光纤看作一条三维空间曲线,针对每根光纤上的各个交点依次进行空间坐标求解。
56.步骤3:根据所述载车板形状,结合各个交点在空间坐标系中的位置坐标,对所述载车板的三维应变场进行重建。
57.将光纤光栅正交阵列传感器的每根光纤看作一条典型的三维空间曲线,因此其位移变形重构问题可以转化为三维空间曲线重构问题。由微分几何知识可知,三维空间曲线可以由曲线的挠率和曲率来衡量确定,基于测点处的正交曲率信息,利用三维重建拟合算法计算出结构的三维应变场。以下给出三维拟合方法的计算步骤。
58.图3为本发明的光纤光栅正交阵列传感器弯曲形状重构算法计算示意图,坐标系o
0 x0y0z0为绝对坐标系,其中z0方向沿第一段圆弧的切线方向,x0、y0分别为第一段圆弧初始点曲率的两个正交分量。以每个微段圆弧的初始点建立运动坐标系o
1-xiyizi。
59.假设绝对坐标系为(a),其中{si}分别为第i点处的运动坐标系和两个正交的曲率分量。第i+1点在绝对坐标系中的坐标为{xi,yi,zi},第i+1点在运动坐标系{si}中的坐标计算如下:
60.当ki≠0时:
[0061][0062]
当ki=0时:
[0063][0064]
接下来计算第i+1点在绝对坐标系{a}中的坐标值。假设第i点在绝对坐标系{a}中的坐标值转换到运动坐标系{si}中坐标值的齐次转化矩阵为[hi]。则有{si}=[hi]{a}。假设第i-1点到第i点已经计算出4
×
4齐次变换矩阵[hi]-1
,所以第i+1点在绝对坐标系(a)中的坐标可以表示为:
[0065][0066]
假设运动坐标系{si}转换到坐标系{m
i+1
}的齐次变换矩阵为[h
t+1
],所以:{si}=[h
i+1
](mi)可以得出[h
i+1
]=[h
i+1
][ti]。因此可计算i+1点在绝对坐标系的位置坐标,以此类推能够求出每个微段圆弧末端点在绝对坐标系的位置坐标。
[0067]
根据光纤光栅阵列传感器每个测点在绝对坐标系的位置坐标,进行插值,即可重构出载车板的应变场分布。
[0068]
根据载车板的应变分布可以直观看出载车板的运行状态,如有无超限形变等。
[0069]
上位机根据通过上述计算得到传动链条的拉力,载车板倾角,载车板应变分布后通过图形界面直观显示其载车板状态,并通过内置安全评价算法给出当前立体车库运行状态的安全评价,并对可能到来的危险工况进行预警。
[0070]
实施例二
[0071]
基于实施例一提供的方法,本实施例提供了一种智能立体车库安全状态检测系统,包括设于所述立体车库载车板的底部表面的光纤光栅阵列传感器、光纤解调仪和上位机;所述光纤光栅阵列传感器包括交错布置的多条光纤;所述光纤光栅阵列传感器用于采集沿光纤方向的多个中心波长变化率,经由光纤解调仪传输至上位机;
[0072]
所述上位机被配置为:
[0073]
步骤1:获取所述光纤光栅正交阵列传感器7采集的沿光纤方向的多个中心波长变化率,对载车板形状进行重构。
[0074]
步骤2:获取所述光纤光栅正交阵列传感器7交点处的中心波长变化率,换算为正交曲率信息,计算各个交点在空间坐标系中的位置坐标。
[0075]
步骤3:根据所述载车板形状,结合各个交点在空间坐标系中的位置坐标,对所述载车板的三维应变场进行重建。
[0076]
所述系统还包括多个光纤光栅温度补偿应变传感器,分别设置于载车板的多个传动链条上,用于采集传动链条的应力信息,经由光纤解调仪传输至上位机。
[0077]
所述系统还包括光纤光栅倾角仪,设置于载车板上,用于采集载车板的倾角信息,经由光纤解调仪传输至上位机。
[0078]
所述上位机对所述载车板的表面形状、三维应变场、链条应力信息以及载车板的倾角信息中的一个或多个进行可视化,并对运行状态进行显示。
[0079]
基于以上一个或多个实施例,能够重构出载车板及其传动系统状态,包括倾角,变形场以及裂纹状态,并给出安全诊断及危险预警,能有效的避免因长期使用,设备耐受力弱或者违规使用立体车库导致的载车板老化引起的财产损失或者生命安全事故。
[0080]
上述虽然结合附图对本发明的具体实施方式进行了描述,但并非对本发明保护范围的限制,所属领域技术人员应该明白,在本发明的技术方案的基础上,本领域技术人员不需要付出创造性劳动即可做出的各种修改或变形仍在本发明的保护范围以内。