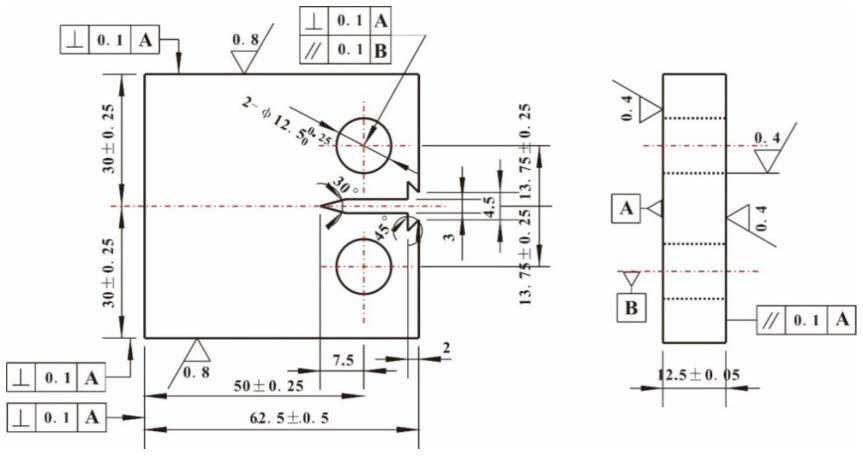
1.本发明涉及金属材料疲劳裂纹扩展速率试验技术领域,具体涉及一种疲劳裂纹扩展门槛值测试方法。
背景技术:2.结构材料在实际服役工况下的受力状况是循环加载的,因此疲劳破坏是工程构件失效破坏的主要方式之一。据相关研究部门统计由疲劳破坏导致的工程构件失效破坏在所有构件失效破坏中约占80%。疲劳断裂往往表现出无征兆性,突然性和灾难性的特征,导致的损失一般也比较巨大。因此材料的疲劳问题是构件实际应用之前不可避免的一个主要环节,要想保证构件的服役安全性就必须能够准确、安全、快速的测量出材料的疲劳性能。因此准确的获得材料的疲劳数据是材料在实际应用之前必不可少的环节。
3.损伤容限设计法是飞机、高铁和船舶等重大装备进行结构安全性设计的主要方法,该方法允许结构件存在一定的裂纹等缺陷,但是裂纹等缺陷的存在又不能影响结构件在规定服役时间内的安全性。通过该方法可以使得飞机等装备结构更强、重量更轻,从而表现出更优异的综合性能和运载力,同时油耗更低。疲劳裂纹扩展门槛值作为疲劳断裂力学中的重要参数,是结构材料进行损伤容限设计的重要指标。疲劳裂纹扩展门槛值数据的准确性直接决定了重型装备的服役可靠性。因此,在飞行器等重要结构件进行结构设计前需要准确获得材料的疲劳裂纹扩展门槛值。
4.疲劳裂纹扩展门槛值
△kth
的定义为:疲劳裂纹扩展速率等于10-7
mm/cycle所对应的应力强度因子范围值,其中,疲劳裂纹扩展速率用da/dn表示,a为裂纹长度,n为应力循环次数。疲劳裂纹扩展门槛值试验是一个专业而且所需时间比较漫长的试验过程。整个试验过程以疲劳裂纹长度为试验终止条件,疲劳裂纹长度可通过目测法或柔度法等方式进行计算,目测法需要测试人员反复测量,比较繁琐,误差较大。柔度法可以通过使用电脑自动记录存储,不需要人工操作,计算公式按(1)和(2)所示。
[0005][0006]
a/w=co+c1u
x
+c2u
x2
+c3u
x3
+c4u
x4
+c5u
x5
ꢀꢀ
(2);
[0007]
式中:a表示疲劳裂纹长度,b表示试样厚度,w表示加载孔中心到试样端部的距离,e表示弹性模量,vx表示形变变化量,f表示载荷;c0~c5表示计算常数。
[0008]
在gb/t6398-2017金属材料疲劳裂纹扩展速率试验方法中详细规定了疲劳裂纹扩展门槛值试验的测试方法为:
[0009]
在裂纹扩展速率(da/dn)介于10-7
mm/cycle~10-6
mm/cycle范围内选取至少5对da/dn
‑△
k(应力强度因子)数据点,将这些数据点在双对数坐标系下用线性回归的方法进行拟合,推荐使用的拟合公式如公式(3)所示:
[0010]
da/dn=c(
△
k)mꢀꢀ
(3);
[0011]
公式(3)中:c和m分别为最佳拟合直线的截距和斜率。
[0012]
根据公式(3)拟合获得的结果,计算获取da/dn=10-7
mm/cycle时对应的
△
k值作为疲劳裂纹扩展门槛值
△kth
。
[0013]
现在疲劳裂纹扩展门槛值试验中主要使用的是柔度法+恒载法。恒载法是指在疲劳试验过程中选择恒定载荷使得裂纹扩展速率介于10-7
mm/cycle~10-6
mm/cycle之间,疲劳裂纹扩展0.2~0.5mm裂纹长度后停止试验,获得一对da/dn
‑△
k数据点,然后继续降低试验载荷,载荷改变范围不超过10%,扩展0.2~0.5mm裂纹长度后,裂纹扩展速率接近10-7
mm/cycle后再逐步增加载荷,载荷增加范围不超过10%,每次裂纹扩展0.2~0.5mm,直到裂纹扩展速率超过10-6
mm/cycle后停止试验。
[0014]
该试验过程由于需要疲劳试验机反复启/停,改变试验载荷后再继续试验,当试验停止时,试样裂纹尖端会产生裂纹闭合效应,使得柔度法计算裂纹长度误差较大,获得da/dn
‑△
k数据点分散,导致数据拟合误差大,计算获得的门槛值
△kth
误差也较大,最大误差范围可达到40%。而且需要试验人员反复更改试验载荷,采集记录裂纹长度,试验人员劳动强度大。测试数据不稳定,测试结果误差大,从而增加了材料研发和使用的难度,严重阻碍了飞重大装备的研发和装备。
技术实现要素:[0015]
针对现有测试方法中存在的上述不足之处,本发明提供一种疲劳裂纹扩展门槛值测试方法,该方法通过使用柔度法和降k法,将整个疲劳裂纹扩展门槛值试验在一个试验程序中完成,避免了试验机的频繁启/停,因而也不会发生裂纹闭合效应,获得满足标准要求的数据点,数据连续、稳定、准确。
[0016]
降k法是指试验过程中采用应力强度因子k控制,应力强度因子k与试验载荷线性对应,因此试验载荷会在计算机的控制下以恒定的速率逐步缓慢降低,但是整个过程试样两端始终被施加试验载荷,直到连续获得裂纹扩展速率(da/dn)介于10-7
mm/cycle~10-6
mm/cycle范围内至少5对da/dn
‑△
k数据点,停止试验。整个试验过程疲劳试验机不会停机更换试验载荷,试验裂纹尖端始终受一个拉力,因此试验裂纹尖端不会发生闭合效应。从而获得的da/dn
‑△
k数据点连续稳定,数据线性度好,数据拟合精度高,误差不超过10%,计算获得的门槛值
△kth
准确,能够大幅度提高疲劳裂纹扩展门槛值测试的效率和准确性,降低材料研发的试验费用,为后续的结构件材料的设计和使用提供可靠参考,保证重大装备的服役可靠性。
[0017]
为实现上述目的,本发明所采用的技术方案如下:
[0018]
一种疲劳裂纹扩展门槛值测试方法,该测试方法使用的试样为紧凑拉伸(ct)试样,计算机计算裂纹长度的方法为柔度法,疲劳裂纹扩展门槛值试验过程采用的控制方式为恒力控制的降k法。
[0019]
该测试方法具体包括如下步骤:
[0020]
(1)制备金属材料紧凑拉伸(ct)试样并测量试样尺寸;
[0021]
(2)在疲劳试验机上安装试样及cod规,输入试样尺寸、材质等参数;试样刀口处安装cod规;
[0022]
(3)进行疲劳预加载,通过修改弹性模量使柔度法计算获得的裂纹长度与实际裂纹长度一致,确认裂纹长度计算准确;
[0023]
(4)设置控制方式为柔度法和降k法:根据公式(5)和公式(6)计算获得对应的应力强度因子范围
△
k和试样疲劳裂纹扩展速率da/dn数据,使用降k法,按照公式(4)连续逐级缓慢降低试验疲劳裂纹尖端的应力强度因子;其中输入k梯度值c,c介于-0.05~-0.15之间;
[0024]
(5)设置较大的终止疲劳裂纹长度,使其等于w,并按照步骤(4)设置的控制方式开始试验,向试样两端施加试验载荷,直到连续获得裂纹扩展速率(da/dn)介于10-7
mm/cycle~10-6
mm/cycle范围内至少5对da/dn
‑△
k数据点,停止试验;
[0025]
(6)将步骤(5)获得的数据点在双对数坐标系下依据公式(3)用线性回归的方法进行拟合,根据拟合结果,计算获取da/dn=10-7
mm/cycle对应的
△
k值作为疲劳裂纹扩展门槛值
△kth
。
[0026]
上述步骤(5)试验过程中,试验载荷采用应力强度因子
△
k控制,应力强度因子
△
k与试验载荷线性对应,通过计算机控制应力强度因子
△
k使试验载荷以恒定的速率(即k梯度值c)逐级缓慢降低。
[0027]
所述应力强度因子
△
k根据公式(5)计算:
[0028][0029]
公式(5)中:
△
k表示试样裂纹尖端所受的应力强度因子范围,与试样尺寸、裂纹长度和载荷有关;f表示试验载荷,b表示试样厚度,α表示疲劳裂纹长度a与w的比值;通过cod规测量试样裂纹尖端张开位移的变化量,使用柔度法计算试样的实时裂纹长度。
[0030]
上述步骤(5)试验过程中,疲劳试验机不会停机更换试验载荷,试验裂纹尖端始终受一个拉力,因此试验裂纹尖端不会发生闭合效应。
[0031]
上述步骤(4)中,疲劳裂纹扩展速率da/dn表示循环一次的疲劳裂纹扩展量,计算公式为公式(6):
[0032]
da/dn=
△
a/nfꢀꢀ
(6);
[0033]
公式(6)中:
△
a表示疲劳裂纹扩展量(表示循环一次疲劳裂纹增加的长度),nf表示疲劳裂纹扩展量所需的循环寿命。
[0034]
上述步骤(4)中,应力强度因子逐级缓慢降低按如公式(4)计算;
[0035]
δk
i(j)
=δk
i(j-1)ecδa(j-1)
ꢀꢀ
(4);
[0036]
公式(4)中:
△ki(j)
表示第j级初始应力强度因子范围;
△ki(j-1)
表示第j-1级初始应力强度因子范围;
△a(j-1)
表示前一级恒定载荷对应的裂纹扩展量,一般为0.05~0.15mm;c表示
△
k梯度值,c=-0.05~-0.15(当c>0,表示增k法,当c<0,表示降k法)。
[0037]
本发明原理及有益效果如下:
[0038]
1、本发明疲劳裂纹扩展门槛值测试方法有效地解决了现阶段疲劳试验机测量疲劳裂纹扩展门槛值
△kth
使用方法导致试验周期长,试验费用高,试验数据不稳定,测试结果误差大的难题,新的测试方法使用柔度法+降k法的方式,避免了试验过程中试验机反复启停的问题,在计算机的控制下使得应力强度因子k以恒定的速率逐步缓慢下降(c=-0.1,c表示k梯度值),从而获得连续稳定的da/dn
‑△
k数据点,数据拟合精度高,计算获得的门槛值
△kth
准确。整个试验过程试验机一直对试样施加载荷,不会发生停机。避免了因试验机频繁停机引起试样裂纹尖端闭合进而导致的数据分散,最终使得试验结果不准确的问题。经
过实践证明:使用该方法后能够将测试结果误差由原先的40%提高到10%以内,极大的提高了测试准确性,保证了重大装备设计的结构设计安全和服役可靠性。
[0039]
2、本发明主要利用柔度法+降k法满足测试标准要求,通过获得裂纹扩展速率(da/dn)介于10-7
mm/cycle~10-6
mm/cycle范围内选取至少5对dadn
‑△
k(应力强度因子范围)数据点,将这些数据点在双对数坐标系下用线性回归的方法进行拟合,获得da/dn=10-7
mm/cycle时对应的疲劳裂纹扩展门槛值
△kth
。能够在保证测试结果准确的前提下,大幅度的降低试验所需时间,提高试验效率,降低材料的研发和使用周期,从而加快了重型装备的生产和使用。
附图说明
[0040]
图1为紧凑拉伸试样尺寸图。
[0041]
图2为恒力控制的降k法示意图。
[0042]
图3为降k法试样裂纹尖端受力示意图。
具体实施方式
[0043]
为了进一步理解本发明,以下结合实例对本发明进行描述,但实例仅为对本实用发明的特点和优点做进一步阐述,而不是对本发明权利要求的限制。
[0044]
实施例1:
[0045]
本实施例为测试疲劳裂纹扩展门槛值,所述测试方法用于测量金属材料疲劳裂纹扩展门槛值。所述测试方法使用的试样为紧凑拉伸(ct)试样,不同尺寸的紧凑拉伸试验对本测试方法均通用,试样形状及尺寸如图1所示。
[0046]
该测试方法具体执行过程如下:
[0047]
(1)按图1所示制备金属材料紧凑拉伸(ct)试样并测量试样尺寸;
[0048]
(2)在疲劳试验机上安装试样及cod规,输入试样尺寸、材质参数;试样刀口处安装cod规;不同cod规安装位置对应的柔度法计算参数也不同;
[0049]
(3)进行疲劳预加载,通过修改弹性模量使采用柔度法和恒载法计算获得的裂纹长度与实际裂纹长度一致,确认裂纹长度计算准确;
[0050]
(4)设置控制方式为柔度法和降k法:根据公式(5)和公式(6)计算获得对应的应力强度因子范围
△
k和试样疲劳裂纹扩展速率da/dn数据,使用降k法,按照公式(4)连续逐级缓慢降低试验疲劳裂纹尖端的应力强度因子;其中输入k梯度值c,c为-0.1;如图2所示。
[0051]
(5)设置较大的终止疲劳裂纹长度,使其等于w,并按照步骤(4)设置的控制方式开始试验,向试样两端施加试验载荷,直到连续获得裂纹扩展速率(da/dn)介于10-7
mm/cycle~10-6
mm/cycle范围内至少5对da/dn
‑△
k数据点,停止试验;
[0052]
步骤(5)试验过程中,试验载荷采用应力强度因子
△
k控制,应力强度因子
△
k与试验载荷线性对应,通过计算机控制应力强度因子
△
k使试验载荷以恒定的速率(即k梯度值c)逐级缓慢降低。所述应力强度因子
△
k根据公式(5)计算:
[0053][0054]
公式(5)中:
△
k表示试样裂纹尖端所受的应力强度因子范围,与试样尺寸、裂纹长
度和载荷有关;f表示试验载荷,b表示试样厚度,α表示疲劳裂纹长度a与w的比值;通过cod规测量试样裂纹尖端张开位移的变化量,使用柔度法计算试样的实时裂纹长度。
[0055]
步骤(5)试验过程中,疲劳试验机不会停机更换试验载荷,试验裂纹尖端始终受一个拉力,因此试验裂纹尖端不会发生闭合效应。
[0056]
疲劳裂纹扩展速率da/dn表示循环一次的疲劳裂纹扩展量,计算公式为公式(6):
[0057]
da/dn=
△
a/nfꢀꢀ
(6);
[0058]
公式(6)中:
△
a表示疲劳裂纹扩展量(表示循环一次疲劳裂纹增加的长度),nf表示疲劳裂纹扩展量所需的循环寿命。
[0059]
(6)将步骤(5)获得的数据点在双对数坐标系下依据公式(3)用线性回归的方法进行拟合,根据拟合结果,计算获取da/dn=10-7
mm/cycle对应的
△
k值作为疲劳裂纹扩展门槛值
△kth
。应力强度因子逐级缓慢降低按如公式(4)计算;
[0060]
δk
i(j)
=δk
i(j-1)ecδa(j-1)
ꢀꢀ
(4);
[0061]
公式(4)中:
△ki(j)
表示第j级初始应力强度因子范围;
△ki(j-1)
表示第j-1级初始应力强度因子范围;
△a(j-1)
表示前一级恒定载荷对应的裂纹扩展量,一般为0.05~0.15mm;c表示
△
k梯度值,c=-0.1。
[0062]
采用本实施例测试,没有发生裂纹闭合效应,经过计算处理拟合获得准确的疲劳裂纹扩展速率门槛值结果,测试数据连续、稳定、准确性高。如图3所示。
[0063]
该测试方法使用时,要求使用经过第三方检定合格的cod规,疲劳试验机的载荷精度满足试验需求。试样形状为紧凑拉伸(ct)试样,试样尺寸满足标准要求,试验过程中途不能停止。该测试方法不能用于腐蚀环境中。
[0064]
该测试方法满足gb/t6398-2017金属材料疲劳试验疲劳裂纹扩展方法中疲劳裂纹扩展门槛值测试的要求。
[0065]
该测试方法以裂纹扩展速率测试软件为基础,能够节约试验时间,提高测试效率,降低试验成本。