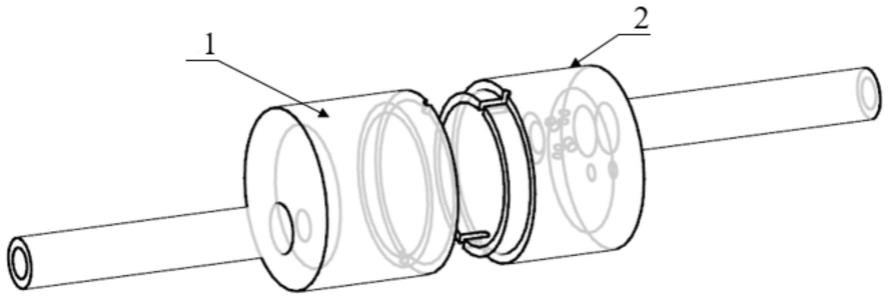
1.本发明属于超高温湿氧环境下力学试验领域,具体涉及超高温湿氧气氛与载荷协同作用的试验装置及方法。
背景技术:2.航空航天技术的腾飞离不开高性能复合材料的发展。碳化硅纤维增强碳化硅基体复合材料(sic/sic)凭借其耐高温、强度高、质量轻等优点,已经被锁定为航空发动机热端部件的最佳候选材料。在航空发动机运行过程中,复合材料部件不仅要承受1200℃左右的超高温,还要承受气动载荷或叶片转动产生的离心载荷;此外,航空燃料燃烧产生的水蒸气和未来得及消耗的氧气的氧化作用也要考虑在内。
3.目前,在该领域中,大部分现有的研究方法只考虑高温湿氧气氛或载荷单一因素对材料性能的影响,无法真实反映实际工况中材料在超高温湿氧环境中氧化与载荷的协同作用对材料力学性能的退化作用,而这对于部件的长期安全可靠地运行具有重要的理论意义和工程应用价值。还有一部分的研究方法是先将材料浸泡在液态水中,然后进行高温环境下的力学试验,这种研究方法不能真实反映实际工况中材料所处的超高温-湿氧气氛-载荷互相耦合的环境。
技术实现要素:4.为了解决现有技术中的问题,本发明提供了超高温湿氧气氛与载荷协同作用的试验装置及方法,能同时实现超高温湿氧环境下应力-氧化的协同作用,综合评估高温湿氧氧化和应力对材料性能的影响,研究材料在超高温湿氧环境下的力学性能退化规律。
5.为了试下上述目的,本发明采用技术方案:一种超高温湿氧气氛与载荷协同作用的试验装置,包括前腔和后腔,所述前腔包括位于前端的出气管道和位于后端的前主腔体,所述后腔包括前端的后主腔体和位于后端的进气管道,所述前主腔体的后端设置有向前凹陷的凹槽,所述凹槽的后端设置有一对前缺口,所述后主腔体的前端设置有向前凸出的凸台,所述凸台的前端设置有一对后缺口,所述凹槽与凸台相匹配,所述前缺口和后缺口相匹配,当前腔和后腔闭合时,位于后主腔体前端的凸台卡入位于前主腔体后端的凹槽内,前主腔体与后主腔体之间形成密闭空间,且前缺口和后缺口相匹配形成一对通孔,位于前主腔体前端的出气管道与位于后主腔体后端的进气管道均与密闭空间连通。
6.进一步的,所述前缺口为c形缺口,所述后缺口为u形缺口,当位于后主腔体前端的凸台卡入位于前主腔体后端的凹槽内时,所述c形缺口与u形缺口形成的一对o形通孔的连线垂直于前主腔体和后主腔体的轴心,所述o形通孔的尺寸略大于试件的尺寸(方形试件的宽度或柱形试件的直径),以确保试件穿过o形通孔时与边界无接触摩擦。
7.进一步的,所述后主腔体的后端还设置有温度采集孔,热电偶自温度采集孔插入后主腔体内部,所述温度采集孔的直径略大于热电偶的直径,以保证热电偶无障碍穿过。
8.进一步的,所述前主腔体和后主腔体闭合状态下置于超高温炉内,且所述前主腔体和后主腔体闭合状态时形成的圆柱外形与超高温炉的炉膛内壁相匹配,超高温炉炉壁的对应位置加工有圆柱孔供进气管道、出气管道和热电偶穿过。
9.进一步的,所述凸台为阶梯型凸台,所述凹槽为阶梯型凹槽,阶梯型凸台和阶梯型凹槽相匹配,以保证前主腔体和后主腔体闭合时内部的气氛不会沿接触边界泄露。
10.进一步的,所述进气管道自后端向前端伸入后主腔体内,位于后主腔体内的进气管道前端设置有分流器,所述分流器引导进气管道内的气体向前主腔体和后主腔体形成的密闭空间内四周发散,以确保气体分布和温度的均匀性。
11.进一步的,所述进气管道与湿氧气氛生成设备相连接,所述出气管道与冷凝器相连接。
12.进一步的,所述进气管道与后主腔体不同轴,所述出气管道与前主腔体也不同轴。
13.进一步的,所述前腔和后腔在试验前相互分离,在试验过程中闭合;所述前腔和后腔均采用一体化成型工艺。
14.进一步的,所述前腔与后腔的材质具有耐高温、导热性好、抗氧化、无金属离子杂质的特性。
15.一种超高温湿氧环境氧化与载荷协同作用的试验方法,其特征在于,包括以下步骤:步骤1、将前腔与后腔分离,将试件的上下两端分别固定于上夹具和下夹具;步骤2、将前腔与后腔关闭,使试件正好竖直穿过c形缺口与u形缺口形成的o形通孔;步骤3、向进气管道通入惰性气体,并操作超高温炉升温至目标温度,以保证升温过程中试件不会受到空气的氧化而影响最终性能的评估;步骤4、温度达到目标温度后,向进气管道通入湿氧气体,同时停止通入惰性气体;步骤5、操作力学试验机对试件加载,超高温湿氧气氛与载荷协同作用。
16.进一步的,所述步骤5的加载程序停止后,应立即降温,同时再次将通入的气体切换为惰性气体,以确保降温过程中试件不会受到空气的氧化而影响最终性能的评估。
17.与现有技术相比,本发明具有以下有益效果:(1)、本发明提供了超高温湿氧气氛与载荷协同作用的试验装置及方法,该装置及方法克服了对材料的高温湿氧气氛或载荷单一因素研究的不全面性,通过将湿氧气氛均匀散布在耐高温无杂质腔体内与试样标距段充分接触实现超高温湿氧氧化环境,配合力学试验机,可用于研究载荷和超高温湿氧氧化的协同作用对材料性能的影响,还可以研究应力与超高温湿氧氧化之间的耦合机理,从而准确揭示材料在服役阶段的高温力学-化学性能演化规律,对航空部件的长期安全可靠地运行具有重要的理论意义和工程应用价值。
18.(2)、本发明具有很强的通用性,可搭配万能试验机开展超高温湿氧环境下的单调拉伸试验以研究材料在超高温湿氧环境下的强度退化;也可搭配蠕变持久或疲劳试验机开展超高温湿氧环境下的蠕变或疲劳试验以研究材料在超高温湿氧环境下的寿命衰减。
19.(3)、本发明适用于任意横截面形状的细长航空材料,如棒状的单纤维束增强复合材料试件,或纤细柔软的陶瓷纤维束。
20.(4)、本发明的试验装置结构简单,加工精度要求较低,所用材质容易获取,因此加
工成本较低。
附图说明
21.图1为本发明的三维透视图;图2为本发明的结构示意图;图3为本发明的剖面图;图4为本发明的截面图;图5为超高温湿氧气氛与载荷协同作用示意图;图6为本发明实施例2中试件的结构示意图;图7为实施例2和对比例1中获取的蠕变曲线;图中,1-前腔,2-后腔,3-前主腔体,4-出气管道,5-前缺口,6-后主腔体,7-进气管道,8-后缺口,9-温度采集孔,10-分流器,11-凸台,12-凹槽,13-上夹具,14-下夹具,15-冷凝器,16-热电偶,17-超高温炉,18-试件。
具体实施方式
22.下面结合说明书附图对本发明作进一步详细描述。
23.实施例1如图1-5所示,一种超高温湿氧气氛与载荷协同作用的试验装置,包括前腔1和后腔2,所述前腔1和后腔2在试验前相互分离,在试验过程中闭合;所述前腔1和后腔2均采用一体化成型工艺,所述前腔1包括位于前端的出气管道4和位于后端的前主腔体3,所述后腔2包括前端的后主腔体6和位于后端的进气管道7,所述前主腔体3的后端设置有向前凹陷的凹槽,所述凹槽的后端设置有一对c形缺口5,所述后主腔体6的前端设置有向前凸出的凸台11,所述凸台11的前端设置有一对后缺口8,所述凹槽12与凸台11相匹配,所述前缺口5和后缺口8相匹配,当前腔1和后腔2闭合时,位于后主腔体6前端的凸台11卡入位于前主腔体3后端的凹槽12内,前主腔体3与后主腔体6之间形成密闭空间,且前缺口5和后缺口8相匹配形成一对通孔,位于前主腔体3前端的出气管道4与位于后主腔体6后端的进气管道7均与密闭空间连通,所述后主腔体6的后端还设置有温度采集孔9,热电偶16自温度采集孔9插入后主腔体6内部,所述温度采集孔9的直径略大于热电偶16的直径,以保证热电偶无障碍穿过。所述前主腔体3和后主腔体6闭合状态下置于超高温炉17内,且所述前主腔体3和后主腔体6闭合状态时形成的圆柱外形与超高温炉17的炉膛内壁相匹配,超高温炉17炉壁的对应位置加工有圆柱孔供进气管道7、出气管道4和热电偶16穿过。所述进气管道7与湿氧气氛生成设备相连接,所述出气管道4与冷凝器15相连接。
24.作为一个优选方案,所述前缺口5为c形缺口,所述后缺口8为u形缺口,当位于后主腔体6前端的凸台卡入位于前主腔体3后端的凹槽内时,所述c形缺口与u形缺口形成的一对o形通孔的连线垂直于前主腔体3和后主腔体6的轴心,所述o形通孔的尺寸略大于试件18的尺寸(方形试件的宽度或柱形试件的直径),以确保试件18穿过o形通孔时与边界无接触摩擦。
25.作为一个优选方案,所述凸台11为阶梯型凸台,所述凹槽12为阶梯型凹槽,阶梯型凸台和阶梯型凹槽相匹配,以保证前主腔体3和后主腔体6闭合时内部的气氛不会沿接触边
界泄露。
26.作为一个优选方案,所述进气管道7自后端向前端伸入后主腔体6内,位于后主腔体6内的进气管道7前端设置有分流器10,所述分流器10引导进气管道7内的气体向前主腔体3和后主腔体6形成的密闭空间内四周发散,以确保气体分布和温度的均匀性。
27.作为一个优选方案,所述进气管道7与后主腔体6不同轴,所述出气管道4与前主腔体3也不同轴。
28.作为一个优选方案,所述前腔1与后腔2的材质具有耐高温、导热性好、抗氧化、无金属离子杂质的特性。
29.一种超高温湿氧气氛与载荷协同作用的试验方法,包括以下步骤:步骤1、将前腔1与后腔2分离,将试件18的上下两端分别固定于上夹具13和下夹具14;步骤2、将前腔1与后腔2关闭,使试件18正好穿过c形缺口与u形缺口形成的o形通孔;步骤3、向进气管道7通入惰性气体,并操作超高温炉17升温至目标温度,以保证升温过程中试件18不会受到空气的氧化而影响最终性能的评估;步骤4、温度达到目标温度后,向进气管道7通入湿氧气体,同时停止通入惰性气体;步骤5、操作力学试验机对试件18加载,超高温湿氧气氛与载荷协同作用;作为一个优选方案,所述步骤5的加载程序停止后,应立即降温,同时再次将通入的气体切换为惰性气体,以确保降温过程中试件18不会受到空气的氧化而影响最终性能的评估。
30.实施例2试验装置:超高温湿氧环境下的蠕变试验,试验温度为1200℃,湿氧气氛采用50%h2o和50%o2的混合气体。被测材料是国产高性能三代sic纤维束cansas 3301,单根纤维的半径为6μm,单束纤维共包含500根纤维,总横截面积约5.655e-8m2。由于纤维本身的脆性特征,一般不能通过夹具直接夹持。
31.将sic纤维束切割成250mm的小段,并采用高温胶将sic纤维束的两端粘在铝制金属管内,所述铝制金属管的长度为25mm,最终制备好的试件18总长185mm,如图6所示。
32.选用高纯度熔融石英材料制备前腔1与后腔2,所述前主腔体3和后主腔体6的外径为38mm,壁厚4mm,长度30mm。
33.所述进气管道7和出气管道4长度为60mm,外径10.5mm,内径6.5mm。
34.所述c形缺口与u形缺口相互匹配形成的o形通孔半径为1mm。
35.所述温度采集孔9的直径为3.5mm。
36.试验方法:步骤1、将前腔1与后腔2分离,将试件18两端的铝制金属管分别固定于上夹具13和下夹具14。
37.步骤2、将前腔1与后腔2关闭,使试件18正好竖直穿过c形缺口与u形缺口相互匹配形成的o形通孔。
38.步骤3、操作超高温炉17升温至1200℃,升温速率1.5℃/s,同时向进气管道7通入氩气,流速为1l/min,以保证升温过程中试件18不会受到空气的氧化而影响最终性能的评估。
39.步骤4、温度达到1200℃后,向进气管道7通入50%h2o和50% o2组成的混合气体,流速为1l/min,同时停止通入氩气。
40.步骤5、操作蠕变试验机设置蠕变载荷为2n,超高温湿氧气氛与载荷协同作用。试验得到的蠕变曲线in wet oxygen如图7所示。蠕变加载程序停止后,应立即降温,同时再次将通入的气体切换为氩气,以确保降温过程中试件18不会受到空气的氧化而影响最终性能的评估。
41.对比例1超高温无湿氧环境下的蠕变试验,试验温度为1200℃,采用氩气作为蠕变试验过程中的填充保护气。被测材料是国产高性能三代sic纤维束cansas 3301,单根纤维的半径为6μm,单束纤维共包含500根纤维,总横截面积约5.655e-8m2。纤维由于本身的脆性特征,一般不能通过夹具直接夹持。
42.将sic纤维束切割成250mm的小段,并采用高温胶将sic纤维束的两端粘在铝制金属管内,所述铝制金属管的长度为25mm,最终制备好的试件18总长185mm,如图6所示。
43.步骤1、将前腔1与后腔2分离,将试件18两端的铝制金属管分别固定于上夹具13和下夹具14。
44.步骤2、将前腔1与后腔2关闭,使试件18正好穿过c形缺口与u形缺口相互匹配形成的o形通孔。
45.步骤3、操作超高温炉17升温至1200℃,升温速率1.5℃/s,升温和保温过程中向进气管道7通入氩气,流速为1l/min,以保证升温和保温过程中试件18不会受到空气的氧化而影响最终性能的评估。
46.步骤4、温度达到1200℃后,操作蠕变试验机设置蠕变载荷为2n,进行正常的蠕变试验。试验得到的蠕变曲线in ar如图7所示。蠕变加载程序停止后,应立即降温,并继续通入氩气,以确保降温过程中试件18不会受到空气的氧化而影响最终性能的评估。
47.在本次超高温湿氧环境下的蠕变试验过程中,通过气体源源不断地流动使腔体内部始终出于微正压地状态,成功避免了外界环境的干扰,准确测量了试件在超高温湿氧环境下的蠕变变形。图7给出了实施例2的湿氧环境下和对比例1的无湿氧环境下的蠕变曲线图,曲线光滑,趋势明显,通过对比无湿氧环境下的蠕变实验,可以看出试样在50%h2o和50% o2组成的试样环境下,由于氧化和载荷的协同作用使其在1个小时内的蠕变变形增大了0.07mm,蠕变速率也明显加快。
48.实验结果表明,该装置及方法可以准确模拟并揭示材料在服役阶段的超高温力学-化学性能的演变规律,对航空部件的长期安全可靠地运行具有重要的理论意义和工程应用价值。
49.以上所述仅是本发明的优选实施方式,应当指出:对于本技术领域的普通技术人员来说,在不脱离本发明原理的前提下,还可以做出若干改进和润饰,这些改进和润饰也应视为本发明的保护范围。