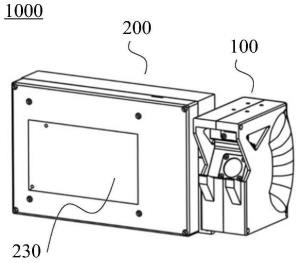
1.本技术涉及数字化检测技术领域,具体涉及一种用于飞机表面连接孔的检测装置及检测方法。
背景技术:2.飞机装配是飞机制造过程中的重要环节,直接关系到飞机最终的整体稳定性和可靠性。在飞机装配过程中,由于机械连接性能可靠、承载能力强等特点,其依然是飞机装配中的主要连接手段之一。例如,整机及相关部件的连接方式主要有铆接、焊接、胶接和螺栓连接等。在铆接和螺栓连接结构中都需要连接孔来进行连接。据统计,一架某型战斗机机翼上需要加工1.4万个连接孔;一架某型商用飞机上需要加工300多万个连接孔;一架某型商用飞机的机身段需要加工1万个连接孔,每对机翼上需要0.8万个连接孔。
3.随着科学技术的发展,现代飞机的安全使用寿命要求日益增加,飞机结构长寿命是大型民用客机适应未来发展的重要需求。在众多飞机事故中,结构疲劳是机体破坏的主要原因。据统计,疲劳失效事故的70%以上源于结构件连接部位,其中80%的疲劳裂纹发生在连接孔处。因此,连接孔的加工质量是保证飞机高质量装配的基础与关键。
技术实现要素:4.为了解决现有检测装置无法快速便捷地对连接孔进行检测的问题,本技术提供了一种便携式的飞机表面连接孔的检测装置和检测方法。
5.根据本技术的第一方面,提供一种飞机表面连接孔的检测装置,包括:
6.采集模块,包括,:
7.第一壳体,
8.线激光传感器,设置于所述第一壳体内,通过发射线激光采集连接孔信息;
9.支撑部,突出于所述第一壳体,通过三点支撑结构与所述飞机表面贴合,使所述线激光垂直射向所述连接孔;
10.处理模块,与所述采集模块相连,包括:
11.第二壳体;
12.信息处理单元,设置于所述第二壳体内,接收所述线激光传感器采集的所述连接孔信息并进行处理后,获得所述连接孔的几何特征。
13.根据本技术的一些实施例,所述三点支撑结构沿检测方向的长度位于所述线激光传感器的检测范围的中部。
14.根据本技术的一些实施例,所述信息处理单元包括:
15.距离测量子单元,用于对所述连接孔信息进行处理并获得所述连接孔的深度特征;和/或
16.角度测量子单元,用于对所述连接孔信息进行处理并获得所述连接孔的孔径特征。
17.根据本技术的一些实施例,所述处理模块还包括:
18.显示单元,设置于所述第一壳体上,用于显示采集的所述连接孔信息。
19.根据本技术的一些实施例,所述显示单元包括:触摸显示屏,还用于接收用户对距离测量功能和/或角度测量功能的交互。
20.根据本技术的一些实施例,所述采集模块还包括:握持部,设置于所述第一壳体上,其表面设置防滑橡胶。
21.根据本技术的一些实施例,所述采集模块还包括:观察窗,设置于所述第一壳体上。
22.根据本技术的一些实施例,所述支撑部还包括一组橡胶件,分别设置于所述三点支撑结构的支撑端。
23.根据本技术的一些实施例,所述检测装置还包括:电源模块,设置于所述第一壳体内,用于向所述采集模块和所述处理模块供电。
24.根据本技术的另一方面,还提供一种飞机表面连接孔的检测方法,包括:
25.将检测装置的支撑部与所述连接孔周围的飞机表面贴合,所述检测装置的线激光传感器向所述连接孔垂直发射线激光;
26.所述线激光传感器通过发射的线激光采集所述连接孔的信息,并将其传输至所述检测装置的信息处理单元;
27.信息处理单元根据用户选择的测量功能,对所述连接孔的信息进行处理后获取所述连接孔的几何特征。
28.本技术提供的飞机表面连接孔的检测装置,通过手持线激光传感器快速采集连接孔的点云信息,简化飞机表面连接孔检测的操作;通过突出的支撑部使得线激光传感器直接对准连接孔向其垂直发射线激光,无需进行人工调整;通过信息处理单元利用智能算法准确计算出连接孔的几何特征,从而提高了检测效率和精度。
附图说明
29.为了更清楚地说明本技术实施例中的技术方案,下面将对实施例描述中所需要使用的附图作简单地介绍,显而易见地,下面描述中的附图仅仅是本技术的一些实施例,对于本领域普通技术人员来讲,还可以根据这些附图获得其他的附图,而并不超出本技术要求保护的范围。
30.图1a示出了根据本技术示例实施例的检测装置外观示意图;
31.图1b示出了根据本技术示例实施例的检测装置内部结构示意图。
32.图2示出了根据本技术示例实施例的处理模块结构示意图;
33.图3示出了根据本技术示例实施例的采集模块结构示意图;
34.图4示出了根据本技术示例实施例的采集模块与飞机表面配合示意图;
35.图5示出了根据本技术示例实施例的线激光发射示意图;
36.图6示出了根据本技术示例实施例的检测方法流程图;
37.图7示出了根据本技术示例实施例的孔深检测原理示意图;
38.图8示出了根据本技术示例实施例的检测过程示意图。
具体实施方式
39.下面将结合本技术实施例中的附图,对本技术实施例中的技术方案进行清楚、完整地描述,显然,所描述的实施例是本技术一部分实施例,而不是全部的实施例。基于本技术中的实施例,本领域技术人员在没有做出创造性劳动前提下所获得的所有其他实施例,都属于本技术保护的范围。
40.本技术的术语“第一”、“第二”、“上部”、“下部”、“左部”、“右部”等是用于区别不同对象,而不是用于描述预定顺序。此外,术语“包括”和“具有”以及它们任何变形,意图在于覆盖不排他的包含。例如包含了一系列步骤或单元的过程、方法、系统、产品或设备没有限定于已列出的步骤或单元,而是可选地还包括没有列出的步骤或单元,或可选地还包括对于这些过程、方法、产品或设备固有的其它步骤或单元。
41.在本文中提及“实施例”意味着,结合实施例描述的预定特征、结构或特性可以包含在本技术的至少一个实施例中。在说明书中的各个位置出现该短语并不一定均是指相同的实施例,也不是与其它实施例互斥的独立的或备选的实施例。本领域技术人员显式地和隐式地理解的是,本文所描述的实施例可以与其它实施例相结合。
42.飞机表面连接孔的加工质量直接影响着飞机结构件的装配质量和整机性能。以铆接为例,飞机表面锪窝孔的质量直接影响铆接过程中的钉孔变形及制造缺陷的产生。其中,飞机表面锪窝孔的深度不仅影响飞机气动表面的平整度进而影响飞机的隐身性能,而且还会影响连接结构处的疲劳性能。目前,锪窝孔的加工存在锪窝深度不稳定等问题。每架飞机上都存在部分锪窝孔超差、需要人工补锪的现象。此类问题严重影响连接的质量,进而影响批产质量的稳定性。因此,在飞机装配过程中对锪窝孔进行快速、准确的测量,是保证飞机铆接质量的重要因素。
43.对于锪窝孔的深度测量,通常采用卡尺进行测量。例如,通过选取合适大小的光滑圆柱塞规插入锪窝孔,并用卡尺尾部测量露出部分的长度,进而可以根据以下公式间接计算出锪窝孔深度:孔深=塞规长度-塞规插入后剩余的长度。上述测量过程中,由于卡尺尾部容易晃动,导致测量结果容易出现偏差;测量一个锪窝孔深度需要3~4分钟时间,效率低,无法满足大批量生产的要求;锪窝孔处厚度尺寸公差要求较高时,数显游标卡尺精度无法满足要求。
44.为此,本技术旨在提供一种用于飞机表面连接孔的便携式检测装置及方法。该检测装置可以简化检测操作、缩小体积便于手持操作、可以在飞机装配型架上操作、能够检测不同飞机结构件上的表面连接孔的窝深或孔径,提高检测的便捷性和效率。
45.下面将结合附图,详细介绍本技术的技术方案。
46.图1a示出了根据本技术示例实施例的检测装置外观示意图;图1b示出了根据本技术示例实施例的检测装置内部结构示意图。
47.如图1a和1b所示,本技术提供的用于飞机表面连接孔的检测装置1000为手持便携式检测设备,其包括采集模块100和处理模块200。采集模块100用于通过线激光传感器向连接孔发射线激光,从而获取连接孔的信息。处理模块200用于对连接孔的信息进行处理,从而快速获取连接孔的几何特征,例如孔深、孔径等。
48.根据本技术的一些实施例,采集模块100用于以手持的方式对连接孔进行数据测量,其可以包括第一壳体110和线激光传感器120。线激光传感器120固定设置于所述第一壳
体110内,通过发射线激光采集飞机表面连接孔的点云信息。处理模块200包括第二壳体210和信息处理单元220。信息处理单元220固定设置于所述第二壳体内210内,与线激光传感器120相连,获取采集模块100采集的连接孔信息。
49.根据本技术的一些实施例,为了方便使用者进行手持检测,采集模块100与处理模块200采用分体结构。同时,为了检测装置整体的便携性,采集模块100的第一壳体110与处理模块200的第二壳体210之间可以通过连接结构组装在一起。例如,第一壳体110可以通过第二壳体上设置的滑轨挂置在第二壳体上。由此,使用者在进行操作时,可从处理模块200的第二壳体210上取下采集模块100,仅手持采集模块100进行检测,从而提高了检测装置的便携性。
50.根据本技术的一些实施例,处理模块还可以包括显示单元230,设置于所述第二壳体210上,用于显示采集的连接孔信息,例如获取的连接孔几何特征。根据本技术的一些实施例,显示单元230可以是触摸显示屏,既可以用于显示连接孔信息,还可以接收使用者的交互信息。根据本技术的一些实施例,信息处理单元220可以内置不同的测量子单元,用于根据采集的连接孔信息、通过不同的处理算法来获得连接孔的不同几何特征。例如,信息处理单元220可以内置距离测量子单元,用于对采集的连接孔信息进行处理后获取所述连接孔的深度特征;信息处理单元220还可以内置角度测量子单元,用于对采集的连接孔信息进行处理后获取所述连接孔的孔径特征,本技术不限于此。根据本技术的一些实施例,触摸显示屏可以显示信息处理单元220内置的测量子单元并提供交互界面,以供使用者选择相应的测量功能,从而获得不同的连接孔几何特征。根据本技术的一些实施例,信息处理单元220可以实施为集成处理器、电路板和固态硬盘组成的集成单元。固态硬盘和集成处理器安装在电路板上;固态硬盘用于存储处理程序和测量数据;集成处理器用于程序算法的执行。电路板可以通过串口与触摸显示屏相连,进行数据交互。
51.根据本技术的一些实施例,检测装置1000还可以包括电源模块300,用于向所述采集模块100和所述处理模块200供电。根据本技术的一些实施例,电源模块可以设置于处理模块200的第二壳体210内,从而保证采集模块100的重量最小、便于手持检测。根据本技术的一些实施例,电源模块300可以包括锂电池、变压器、电源开关;锂电池和变压器设置在第二壳体210内,电源开关可以固定在第二壳体210表面。
52.例如,采集模块100和处理模块200之间可以通过网线电源综合线(未示出)相连,既能够保证两者的分体结构,又能实现数据传输和供电。网线电源综合线连接至采集模块100中的线激光传感器的一端是综合性插口,另一端具有lan端口和电源端口。lan端口与处理模块200的信息处理单元相连,实现数据传输;电源端口与电源模块300相连,为线激光传感器供电。
53.图2示出了根据本技术示例实施例的处理模块结构示意图。
54.根据本技术的一些实施例,处理模块200的第二壳体210可以是由两部分组成的中空结构,信息处理单元和电源模块(图中未示出)容纳在其中。例如,第二壳体210可以包括第二壳体上部211和第二壳体下部212;所述第二壳体上部211与所述第二壳体下部212可以通过螺栓连接固定为一体;第二壳体下部212的外侧可以设置滑轨213,用于挂置采集单元的壳体。显示单元230(例如触摸显示屏),可以通过两个挡板214固定在第二壳体上部211。组成信息处理单元的集成处理器、电路板和固态硬盘等可以容置于第二壳体210内,例如电
路板可以通过螺栓固定在第二壳体下部212内。集成处理器可以与触摸显示屏以及采集模块的线激光传感器进行数据传输,对线激光传感器采集的连接孔信息进行处理,并将处理结果在触摸显示屏上进行显示。
55.图3示出了根据本技术示例实施例的采集模块结构示意图。
56.根据本技术的一些实施例,采集模块100的第一壳体110可以是由两部分组成的中空结构,线性激光传感器(图中未示出)容纳在其中。例如,第一壳体110可以包括第一壳体左部111和第一壳体右部112。第一壳体左部111和第一壳体右部112通过螺栓固定连接。根据本技术的一些实施例,采集模块100还可以包括支撑部130,突出于所述第一壳体110。支撑部130用于测量时对采集模块100的支撑和线激光检测范围的确定。
57.根据本技术的一些实施例,支撑部130可以为三点支撑结构。在检测过程中,通过三个支撑端131与飞机表面贴合,使线性激光传感器发射的线激光垂直射向连接孔。根据本技术的一些实施例,所述支撑部130还包括一组橡胶件,分别设置于三点支撑结构的支撑端131,用于保护被测工件表面。根据本技术的一些实施例,采集模块100还可以包括观察窗140,设置于所述第一壳体上110上,以便于使用者在检测时观察激光状态和孔径位置。根据本技术的一些实施例,所述采集模块100还可以包括握持部150,设置于所述第一壳体110上;握持部150采用符合人体工程学的设计,并且表面设置防滑橡胶,在保证握持安全的同时,减少使用者的手部压力。
58.图4示出了根据本技术示例实施例的采集模块与飞机表面配合示意图。对于具有较小曲率的飞机表面,在进行连接孔测量时,通过采集模块100的支撑部轻压工件,使三点支撑结构的支撑端131完全贴合在待测工件表面,由于三点支撑结构沿检测方向的长度位于线激光检测范围中部,可以确保工件在线激光的检测范围内,从而无需人工进行调整。在检测过程中,使用者可以通过观察窗140,观察连接孔2000的位置。
59.根据本技术的一些实施例,线激光传感器通过螺栓(例如三个不共线的螺栓)固定在采集模块的第一壳体内。线激光传感器可以由线激光发射器、ccd线性相机和微处理器等组成。图5示出了根据本技术示例实施例的线激光发射示意图。激光发射器通过镜头将可见红色激光射向被测物体表面,经物体反射的激光通过接收器镜头,被内部的ccd线性相机接收。根据不同的距离,ccd线性相机可以在不同的角度下“看到”被测物体表面的各个光点。根据角度及已知的激光和激光传感器之间的距离,微处理器可以计算出线激光传感器和被测物体之间的距离,从而形成被测物体表面的点云信息。点云信息经过处理模块处理后,便可以获得被测连接孔的几何特征。
60.图6示出了根据本技术示例实施例的检测方法流程图。
61.根据本技术的另一方面,还提供一种飞机表面连接孔的检测方法,使用上述检测装置对连接孔进行深度检测或孔径检测。该检测方法包括以下步骤。
62.s610,将检测装置的支撑部与所述连接孔周围的飞机表面贴合,检测装置的线激光传感器向所述连接孔垂直发射线激光。对于有曲率的飞机表面,则可以将支撑部轻压在工件表面,从而实现线激光的垂直入射。
63.s620,线激光传感器通过发射的线激光采集连接孔的信息,并将其传输至所述检测装置的信息处理单元。
64.在采集过程中,线激光传感器发射一排红色激光至飞机工件表面,经飞机表面反
射的激光通过接收器镜头被内部的ccd线性相机接收。根据不同的距离,ccd线性相机会在不同的角度下接收到这个光点;该将光点传递到信息处理单元,经过三角测量法进行计算便可以得到待测点到传感器的距离;将检测装置的支撑部沿着图4所示方向进行移动,使线激光遍历连接孔,便可以得到各个测量截面在深度方向上的点云信息。
65.s630,信息处理单元根据用户选择的测量功能,对所述连接孔的信息进行处理后获取所述连接孔的相应几何特征。以连接孔深度测量为例,在进行检测操作之前,可以通过显示单元选择距离测量工具(例如距离测量子单元),则在检测过程中可以利用基于opencv的计算机视觉算法(例如split-and-merge算法)识别线激光传感器到被测连接孔截面(例如,锪窝孔截面)端部的距离h2,和线激光传感器到被测连接孔截面顶部的距离h1。如图7所示,利用距离h2减去距离h1,则可以计算出所测连接孔的各截面的深度。对于铆接用的锪窝孔而言,其截面为斜面,因此计算出的最大截面深度为目标深度。
66.图8示出了根据本技术示例实施例的检测过程示意图。
67.以锪窝孔的深度测量为例,本技术提供的检测方法在检测过程中可以按照以下步骤来执行。
68.步骤s810:打开线激光发射器,使线激光处于工作状态,发射一排线激光。
69.步骤s820:使用检测装置的采集模块支撑部贴合在待测工件表面上,实现待测平面的定位,且突出壳体的支撑部可以保证待测平面在线激光的检测范围内。线激光传感器接收经物体反射的激光,将接收的激光信息实时传输至处理模块的信息处理单元。
70.步骤s830:信息处理单元接收激光信息后,根据三角测量算法获得锪窝孔的二维点云信息。
71.步骤s840:根据选择的距离测量子单元,自动识别点云信息中线激光传感器到锪窝孔截面端部的距离h2和线激光传感器到锪窝孔截面顶部的距离h1;利用距离h2减去距离h1,可以计算出测量截面处的窝深。
72.步骤s850:沿直线方向移动采集模块,遍历锪窝孔,距离测量子单元同时进行数据处理,可以得出各个截面的锪窝孔深度;对数据进行对比后,最大值即为所测的锪窝孔深度。
73.步骤s860:若使用结束,则关闭线性激光发射器(s870);若继续使用,则回到步骤s820。
74.本技术提供的检测装置,通过采集模块上的突出支撑部可以直接定位到线激光检测的有效范围,无需工人调整线激光与工件之间的距离进行找寻,便捷定位,操作简单;该检测装置整体采用分体式设计,减轻手持采集模块重量的同时,便于操作人员查看检测结果,且内置电池,检测不受工件尺寸限制,可以在装配型架上进行,体积小,便于手持或携带;对操作人员的熟练度要求较低,通过该检测装置可以实现快速检测;采用线激光传感器,在保证检测精度的同时不受作业场所灯光环境的限制,具有检测精度高、对环境要求低等特点。
75.以上对本技术实施例进行了详细介绍,本文中应用了具体个例对本技术的原理及实施方式进行了阐述,以上实施例的说明仅用于帮助理解本技术的方法及其核心思想。同时,本领域技术人员依据本技术的思想,基于本技术的具体实施方式及应用范围上做出的改变或变形之处,都属于本技术保护的范围。综上所述,本说明书内容不应理解为对本技术
的限制。