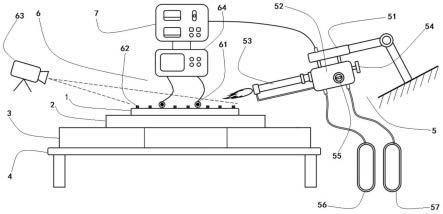
1.本发明涉及飞行器材料测试技术领域,尤其涉及一种用于飞行器部件热环境考核测试的装置及其使用方法。
背景技术:2.飞行器是在大气层内或者大气层外飞行的器械。飞行器分为3类:航空器、航天器、火箭和导弹。在大气层内飞行的称为航空器,如气球、飞艇、飞机等。它们靠空气的静浮力或空气相对运动产生的空气动力升空飞行。在太空飞行的称为航天器,如人造地球卫星、载人飞船、空间探测器、航天飞机等。它们在运载火箭的推动下获得必要的速度进入太空,然后依靠惯性做与天体类似的轨道运动。
3.随着人类对飞行器性能的要求逐步提高,飞行器的速度和航程也进一步提高,而相应的热环境也更加恶劣,因此飞行器的地面高温(大于1750
°
)热环境测试技术的发展也更为关键。而目前能够实现飞行器部件高温加热以及不损坏流场、同步在线监测和原位测量的高温测试技术较少,传统的高温测试技术不能满足目前飞行器服役环境的热环境及高温测量技术需求。
4.中国专利cn102879423b《高超声速飞行器材料1800度有氧环境下单侧面高温试验装置》公开了一种高超声速飞行器材料1800度有氧环境下单侧面高温试验装置,复现有氧环境下的高马赫数飞行器单侧面飞行热环境,测量高超声速飞行器材料在极端有氧高温环境下的隔热特性参数,采用热电偶温度传感器来测量飞行器材料的表面温度,然而热电偶温度传感器尺寸较大,会影响飞行器材料表面的流场,模拟程度不够。
技术实现要素:5.有鉴于此,本发明提出了一种用于飞行器部件热环境考核测试的装置及其使用方法,用于解决传统的高温测试技术不能满足目前飞行器服役环境的热环境及高温测量技术需求的问题。
6.本发明的技术方案是这样实现的:本发明提供了一种用于飞行器部件热环境考核测试的装置,包括飞行器部件、坩埚、耐火砖、试验台;
7.所述试验台设置于地面上,用于承载耐火砖;
8.所述耐火砖设置于试验台上,用于隔绝坩埚和试验台;
9.所述坩埚设置于耐火砖上,用于放置飞行器部件;
10.其特征在于,还包括烧蚀系统、温度测量系统和温度控制系统;
11.所述烧蚀系统设置于飞行器部件上方的一侧,用于提供高温高压的超音速焰流;
12.所述温度测量系统设置于飞行器部件上方的另一侧,用于测量并记录飞行器部件表面的温度;
13.所述温度控制系统与温度测量系统信号连接,用于飞行器部件温度调控。
14.优选的,所述烧蚀系统包括往复运动机构、燃烧室、拉法尔喷管、电磁阀、比例控制
器、航空煤油储罐和液氧储罐;
15.所述往复运动机构固定设置于飞行器部件上方的一侧,用于根据飞行器部件的尺寸进行运动轨迹的模拟;
16.所述燃烧室悬挂于往复运动机构下方,用于燃烧可燃气体;
17.所述拉法尔喷管与燃烧室连接,位于飞行器部件和燃烧室之间,用于喷出高温高压的超音速焰流;
18.所述电磁阀与燃烧室连接,与拉法尔喷管对侧设置,用于开启烧蚀系统;
19.所述比例控制器设置于燃烧室的表面,用于调控航空煤油和氧气的比例;
20.所述航空煤油储罐和液氧储罐与燃烧室连接并位于其下方,用于提供航空煤油和氧气。
21.优选的,所述温度测量系统包括铂铑热电偶、测温晶体、红外热成像仪和温度记录仪;
22.所述铂铑热电偶放置于飞行器部件表面,用于在预处理阶段将温度数据传输给温度记录仪;
23.所述测温晶体放置于飞行器部件表面,用于在飞行器部件服役热环境阶段将温度数据传输至温度记录仪;
24.所述红外热成像仪设置于飞行器部件的另一侧,与拉法尔喷管对侧,用于实时监测飞行器部件表面温度变化情况;
25.所述温度记录仪设置于飞行器部件上方,用于记录飞行器部件表面的温度分布情况。
26.另一方面,本发明还提供一种用于飞行器部件热环境考核测试的装置的使用方法,包括以下步骤:
27.s1,设置试验器材,进行加热环境预处理,对温控系统进行预置;
28.s2,保持温控系统配置,进行服役热环境考核试验;
29.s3,测量飞行器部件表面温度分布情况并记录。
30.优选的,步骤s1具体包括:
31.通过比例控制器调整航空煤油和氧气的比例,氧气将航空煤油充分雾化后形成可燃混合气进入燃烧室,将其点燃后生成高温高压燃气,经拉法尔喷管点火燃烧后形成高温高压的超音速焰流,完成加热环境预处理。
32.更进一步优选的,步骤s1具体包括:
33.在飞行器部件的主要测温点处布置铂铑热电偶,温控系统根据铂铑热电偶反馈的温度信号,调度往复运动机构的运动速度以及电磁阀开度,记录调控好的往复运动机构的运动速度及电磁阀开度的周期性变化情况,完成对温控系统进行预置。
34.优选的,步骤s2具体包括:
35.在进行服役热环境考核试验时,将主要测温点处的铂铑热电偶替换为测温晶体,减少对飞行器部件表面流场的影响,复现飞行器部件的服役热环境。
36.更进一步优选的,步骤s2具体包括:
37.通过红外热成像仪实时监测飞行器部件表面温度变化并记录。
38.更进一步优选的,步骤s2具体包括:
39.所述测温晶体不附加支撑件或引线,布置在飞行器部件表面不影响原温度场,尺寸0.2毫米,最高测温达1800℃,误差小于1.5%。
40.本发明的一种用于飞行器部件热环境考核测试的装置及其使用方法相对于现有技术具有以下有益效果:
41.(1)通过采用加热温度可达1750度以上的高温加热装置,模拟飞行器部件服役的气动加热环境,调控往复运动机构的运行速度来根据飞行器部件的尺寸进行运动轨迹模拟;
42.(2)设置两个工作环境,首先通过加热环境预处理,对温控系统进行预置,然后保持温控系统的配置不变,替换铂铑热电偶为测温晶体,开始服役热环境考核试验,实现了高温加热时不损坏流场和原位测量;
43.(3)配合红外热成像仪,测量飞行器部件表面的温度分布,并使用温度记录仪记录,便于人员对加热环境和服役热环境进行精确调控,实现了同步在线监测。
附图说明
44.为了更清楚地说明本发明实施例或现有技术中的技术方案,下面将对实施例或现有技术描述中所需要使用的附图作简单地介绍,显而易见地,下面描述中的附图仅仅是本发明的一些实施例,对于本领域普通技术人员来讲,在不付出创造性劳动的前提下,还可以根据这些附图获得其他的附图。
45.图1为本发明的一种用于飞行器部件热环境考核测试的装置结构示意图;
46.图2为本发明的一种用于飞行器部件热环境考核测试的装置的使用方法流程图;
47.图3为本发明的一种用于飞行器部件热环境考核测试的装置的考核测试系统组成图;
48.图4为本发明的一种用于飞行器部件热环境考核测试的装置的预置加热环境测试系统组成图;
49.图5为本发明的一种用于飞行器部件热环境考核测试的装置的服役热环境正式测试系统组成图。
具体实施方式
50.下面将结合本发明实施方式,对本发明实施方式中的技术方案进行清楚、完整地描述,显然,所描述的实施方式仅仅是本发明一部分实施方式,而不是全部的实施方式。基于本发明中的实施方式,本领域普通技术人员在没有做出创造性劳动前提下所获得的所有其他实施方式,都属于本发明保护的范围。
51.实施例一
52.提供一种用于飞行器部件热环境考核测试的装置,如图1所示,包括飞行器部件1、坩埚2、耐火砖3、试验台4;
53.所述试验台4设置于地面上,用于承载耐火砖3;
54.所述耐火砖3设置于试验台4上,用于隔绝坩埚2和试验台4;
55.所述坩埚2设置于耐火砖3上,用于放置飞行器部件1;
56.还包括烧蚀系统5、温度测量系统6和温度控制系统7;
57.所述烧蚀系统5设置于飞行器部件1上方的一侧,用于提供高温高压的超音速焰流;
58.所述温度测量系统6设置于飞行器部件1上方的另一侧,用于测量并记录飞行器部件1表面的温度;
59.所述温度控制系统7与温度测量系统6信号连接,用于飞行器部件1温度调控。
60.该用于飞行器部件热环境考核测试的装置可以提供高于1750度的热环境,模拟飞行器部件服役的气动加热环境,在进行热环境试验前将上述器件按照图1所示设置。
61.所述烧蚀系统5包括往复运动机构51、燃烧室52、拉法尔喷管53、电磁阀54、比例控制器55、航空煤油储罐56和液氧储罐57;
62.所述往复运动机构51固定设置于飞行器部件1上方的一侧,用于根据飞行器部件1的尺寸进行运动轨迹的模拟;
63.所述燃烧室52悬挂于往复运动机构51下方,用于燃烧可燃气体;
64.所述拉法尔喷管53与燃烧室52连接,位于飞行器部件1和燃烧室52之间,用于喷出高温高压的超音速焰流;
65.所述电磁阀54与燃烧室52连接,与拉法尔喷管53对侧设置,用于开启烧蚀系统5;
66.所述比例控制器55设置于燃烧室52的表面,用于调控航空煤油和氧气的比例;
67.所述航空煤油储罐56和液氧储罐57与燃烧室52连接并位于其下方,用于提供航空煤油和氧气。
68.烧蚀系统5的工作原理:打开电磁阀54,通过比例控制器55调整航空煤油储罐56和液氧储罐57提供的航空煤油和氧气的比例,氧气通过雾化喷嘴将航空煤油充分雾化后形成可燃混合气进入燃烧室52,点火系统将其点燃后生成高温高压燃气,往复运动机构51模拟飞行器部件1的运动轨迹,经拉法尔喷管53点火燃烧后形成高温高压的超音速焰流。
69.所述温度测量系统6包括铂铑热电偶61、测温晶体62、红外热成像仪63和温度记录仪64;
70.所述铂铑热电偶61放置于飞行器部件1表面,用于在预处理阶段将温度数据传输给温度记录仪64;
71.所述测温晶体62放置于飞行器部件1表面,用于在飞行器部件1服役热环境阶段将温度数据传输至温度记录仪64;
72.所述红外热成像仪63设置于飞行器部件1的另一侧,与拉法尔喷管53对侧,用于实时监测飞行器部件1表面温度变化情况;
73.所述温度记录仪64设置于飞行器部件1上方,用于记录飞行器部件1表面的温度分布情况。
74.温度测量系统6可编写12组工艺曲线,根据需要,可以对不同的飞行器部件1预设不同服役热环境,铂铑热电偶测量温度可达1800℃,测量精度在
±
0.25%以内,测温晶体是晶体传感器,尺寸约0.2mm,测量温度可达1800℃,误差小于1.5%。
75.实施例二
76.提供一种用于飞行器部件热环境考核测试的装置的使用方法,如图2所示,包括以下步骤:
77.s1,设置试验器材,进行加热环境预处理,对温控系统进行预置;
78.s2,保持温控系统配置,进行服役热环境考核试验;
79.s3,测量飞行器部件表面温度分布情况并记录。
80.通过设置两个工作环境,先预设加热环境,然后对飞行器部件复现服役热环境,实现了原位测量和不损换流场测温。
81.步骤s1具体包括:
82.通过比例控制器调整航空煤油和氧气的比例,氧气将航空煤油充分雾化后形成可燃混合气进入燃烧室,将其点燃后生成高温高压燃气,经拉法尔喷管点火燃烧后形成高温高压的超音速焰流,完成加热环境预处理。
83.在飞行器部件的主要测温点处布置铂铑热电偶,温控系统根据铂铑热电偶反馈的温度信号,调度往复运动机构的运动速度以及电磁阀开度,记录调控好的往复运动机构的运动速度及电磁阀开度的周期性变化情况,完成对温控系统进行预置。
84.设置试验器材如图1所示,然后根据飞行器部件的尺寸以及服役热环境,先做加热环境预处理,来完成对温控系统的预置,所述超音速焰流,温度可达2000℃以上,速度可达2000m/s以上。
85.步骤s2具体包括:
86.在进行服役热环境考核试验时,将主要测温点处的铂铑热电偶替换为测温晶体,减少对飞行器部件表面流场的影响,复现飞行器部件的服役热环境。
87.通过红外热成像仪实时监测飞行器部件表面温度变化并记录。
88.所述测温晶体不附加支撑件或引线,布置在飞行器部件表面不影响原温度场,尺寸约0.2毫米,最高测温达1800℃,误差小于1.5%。
89.不损坏流场、同步在线监测和原位测量的高温测量技术实现方法:在温度场测试过程中,将主要测温点处的铂铑热电偶替换为晶体传感器,减少对飞行器部件表面流场的影响同时实现飞行器部件服役热环境的复现,配合红外热成像仪实时监测飞行器部件表面温度变化情况。
90.实施例三
91.模拟飞行器部件服役的气动加热热环境,飞行器部件热环境考核测试装置加热温度可达1750度以上,飞行器部件热环境考核测试装置能够实现高温加热时不损坏流场、同步在线监测和原位测量,飞行器部件热环境考核测试系统组成如图3所示,包括温度测量系统、烧蚀系统和温控系统;
92.所述飞行器部件热环境考核测试装置存在两个工作环节,首先在铂铑热电偶和温度记录仪的配合下,对温控系统进行预置,进而调控燃烧机的电磁阀开度和往复运动机构的运行速度,保证施加热环境的准确,预置加热环境测试系统组成如图4所示;
93.然后保持温控系统的配置不变,移除铂铑热电偶,将测温晶体安装在主要测温点,同时配合红外成像仪,开始服役热环境考核试验及温度测量,服役热环境正式测试系统组成如图5所示;其中所述的温度记录仪用于记录飞行器部件表面的温度分布情况,同时便于人员对服役热环境进行精确调控。
94.所述的飞行器部件热环境考核测试装置中,需要预先通过比例控制器调整好航空煤油和液氧的比例;所述的温控系统预置环节,不部署测温晶体,而在正式服役热环境测试环节部署测温晶体,同时去除铂铑热电偶,保证不对飞行器部件表面流场造成影响。
95.以上所述仅为本发明的较佳实施方式而已,并不用以限制本发明,凡在本发明的精神和原则之内,所作的任何修改、等同替换、改进等,均应包含在本发明的保护范围之内。