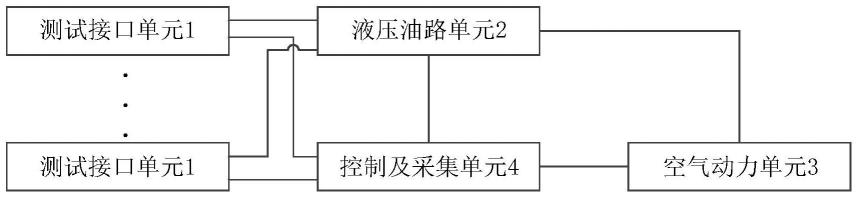
1.本发明涉及核电厂设备测试技术领域,尤其涉及一种电磁阀自动测试装置。
背景技术:2.在核电厂中,二回路系统vvp/are分别配有主蒸汽隔离阀(msiv)、主给水隔离阀(mfiv),每台隔离阀上配有多台高压力主电磁阀和试验电磁阀,核电厂运行、试验及检修过程中对电磁阀失磁和励磁密封性均有严格的要求。
3.该类电磁阀在每次大修时,需要使用专用的检测装置对其密封性能、启停动作特性等进行检测。而现有技术中,检测电磁阀的装置存在以下缺陷:自动化程度度较低,测试需要试验人员手动控制阀门,无法实现自动操作电磁阀动作试验;可测试电磁阀数量及种类较少,效率偏低,且存在人因操作失误风险。
技术实现要素:4.本发明要解决的技术问题在于,提供一种电磁阀自动测试装置。
5.本发明解决其技术问题所采用的技术方案是:构造一种电磁阀自动测试装置,其特征在于,包括:
6.至少一个测试接口单元,用于连接待测电磁阀;
7.液压油路单元,与各所述测试接口单元连接,用于为所述待测电磁阀提供测试油压;
8.空气动力单元,与所述液压油路单元,用于控制所述液压油路单元的油路启闭;
9.控制及采集单元,与所述液压油路单元、空气动力单元和各所述测试接口单元连接,用于控制所述待测电磁阀进行密封性及电气性能测试,并采集所述待测电磁阀的测试数据,进而根据所述测试数据出具测试结果。
10.优选地,所述液压油路单元包括:
11.背压回路单元,与所述控制及采集单元和各测试接口单元连接,用于根据述控制及采集单元输出的背压控制指令为所述待测电磁阀提供背压;
12.液压主油路单元,与所述控制及采集单元、背压回路单元和各测试接口单元连接,用于根据述控制及采集单元输出的主油路控制指令为所述待测电磁阀提供主油路油压,以及为所述背压回路单元供油。
13.优选地,所述液压主油路单元包括:储油单元、进油阀、第一过滤阀、气动油泵、比例阀、过滤器、第一隔离阀、废油收集单元和卸荷阀;
14.所述储油单元的输出端连接经所述进油阀和第一过滤阀连接至所述气动油泵的输入端,所述气动油泵的进气端连接所述空气动力单元,所述气动油泵的控制端经所述比例阀连接至所述控制及采集单元,所述气动油泵的输出端连接所述背压回路单元的输入端和过滤器的输入端,所述过滤器的输出端连接所述第一隔离阀的输入端,所述第一隔离阀的输出端连接各所述测试接口单元的主油路输入端,所述废油收集单元连接各所述测试接
口单元,所述气动油泵的输出端经所述卸荷阀连接至所述废油收集单元。
15.优选地,所述背压回路单元包括第二过滤阀、第一气动隔离阀和第一调压阀;
16.所述第二过滤阀的输入端为所述背压回路单元的输入端,所述第二过滤阀的输出端经所述第一气动隔离阀连接至所述第一调压阀的输入端,所述第一气动隔离阀的进气端连接所述空气动力单元,所述第一气动隔离阀的控制端连接所述控制及采集单元,所述第一调压阀的输出端作为所述背压回路单元的输出端连接各所述测试接口单元的背压输入端。
17.优选地,每一个所述测试接口单元包括第二气动隔离阀、第一排气阀、被测电磁阀底座、第三气动隔离阀、第一电磁阀、第二排气阀和第四气动隔离阀;
18.所述第二气动隔离阀的输入端为所述测试接口单元的主油路输入端,所述第二气动隔离阀的进气端连接所述空气动力单元,所述第二气动隔离阀的控制端连接所述控制及采集单元,所述第二气动隔离阀的输出端连接所述第一排气阀的输入端和被测电磁阀底座的主油输入端,所述第一排气阀的输出端连接所述废油收集单元;
19.所述第三气动隔离阀的输入端为所述测试接口单元的背压输入端连接所述第一电磁阀的输入端,所述第一电磁阀的控制端连接所述控制及采集单元,所述第一电磁阀的输出端连接所述废油收集单元,所述第三气动隔离阀的进气端连接所述空气动力单元,所述第三气动隔离阀的控制端连接所述控制及采集单元,所述第三气动隔离阀的输出端连接所述被测电磁阀底座的背压输入端,所述第三气动隔离阀的输出端还经所述第二排气阀连接至所述废油收集单元;
20.所述被测电磁阀底座的输出端经所述第四气动隔离阀连接至所述废油收集单元,所述第四气动隔离阀的进气端连接所述空气动力单元,所述第四气动隔离阀的控制端连接所述控制及采集单元,所述被测电磁阀底座的排油输出端连接所述废油收集单元。
21.优选地,所述空气动力单元包括空气压缩机、气源隔离阀、空气电磁阀、第一过滤减压阀、第二过滤减压阀和消音器;
22.所述空气压缩机的输出端连接所述气源隔离阀的输入端,所述气源隔离阀的输出端经所述空气电磁阀、第一过滤减压阀和消音器连接至所述气动油泵的进气端,所述气源隔离阀的输出端还连接所述第二过滤减压阀的输入端,所述第二过滤减压阀的输出端连接各所述第一气动隔离阀、第二气动隔离阀、第三气动隔离阀和第四气动隔离阀的进气端,所述空气电磁阀的控制端连接所述控制及采集单元。
23.优选地,所述控制及采集单元包括:
24.采集单元,与所述第一隔离阀的输出端和各被测电磁阀底座连接,用于采集主油路油压,每一个所述待测电磁阀的背压、输入电压和输入电流;
25.控制单元,与所述采集单元、所述空气电磁阀的控制端和各第一电磁阀的控制端连接,用于控制所述待测电磁阀进行密封性及电气性能测试,并根据所述主油路油压、背压、输入电压和输入电流出具测试结果;其中,所述密封性及电气性能测试包括失磁密封试验、励磁密封试验、保压试验、电流特性试验和启动释放电压试验中的至少一种。
26.优选地,所述采集单元包括:
27.电压传感器,与各所述被测电磁阀底座的供电端连接,用于采集每一个所述待测电磁阀的输入电压;
28.两个气压传感器,分别与所述第一过滤减压阀和第二过滤减压阀的输出端一一连接,以采集输入至气动设备的气压;
29.若干与所述至少一个测试接口单元相对应的电流测试单元,与各所述被测电磁阀底座一一对应连接,以采集每一个所述待测电磁阀的输入电流;
30.若干压力传感器,与所述第一隔离阀的输出端和各被测电磁阀底座的背压输入端一一对应连接,以采集所述主油路油压和每一个所述待测电磁阀的背压;
31.所述电压传感器、各气压传感器、各电流测试单元和各压力传感器还与所述控制单元连接。
32.优选地,所述控制单元包括上位机、控制器、电压采集卡、电压输出卡、继电器模块和电流输出卡;
33.所述上位机连接所述控制器,所述控制器连接所述电压采集卡、电压输出卡和电流输出卡,所述电压采集卡连接所述电压传感器、各电流测试单元和压力传感器,所述电压输出卡连接所述继电器模块、第一气动隔离阀、第二气动隔离阀、第三气动隔离阀和第四气动隔离阀的控制端,所述继电器模块连接所述气动油泵的供电端和各被测电磁阀底座的供电端,所述电流输出卡连接所述比例阀的调节端。
34.优选地,所述电磁阀自动测试装置还包括供电单元和急停开关;
35.其中,所述供电单元包括用于为所述待测电磁阀提供输入电压的可调直流电源、用于提供模拟电压的第一直流电源和用于提供数字电压的第二直流电源;
36.所述可调直流电源连接所述急停开关的第一常闭回路的第一端,所述急停开关的第一常闭回路的第二端连接各所述测试接口单元的供电端,所述第一直流电源的输出端经所述急停开关的第二常闭回路连接至所述控制及采集单元,所述第二直流电源的输出端连接所述控制及采集单元。
37.本发明具有以下有益效果:提供一种电磁阀自动测试装置;利用测试接口单元可以同时测试多个待测电磁阀的效果,通过控制及采集单元控制液压油路单元和空气动力单元工作,从而控制待测电磁阀工作在对应工况下,并自动或手动进行密封性及电气性能测试,控制及采集单元还根据试验过程采集到的测试数据出具测试结果;本发明装置不仅操作简单,减少测试人员工作量,还提高主电磁阀和试验电磁阀的测试效率,降低人因操作失误风险,而且测试项目完整及全面,测试结果准确、直观。
附图说明
38.下面将结合附图及实施例对本发明作进一步说明,附图中:
39.图1是本发明提供的电磁阀自动测试装置的结构图;
40.图2是本发明提供的电磁阀自动测试装置中的液压主油路单元的结构图;
41.图3是本发明提供的电磁阀自动测试装置中的背压回路单元的结构图;
42.图4是本发明提供的电磁阀自动测试装置中的测试接口单元的结构图;
43.图5是本发明提供的电磁阀自动测试装置中的空气动力单元的结构图;
44.图6和图7是本发明提供的电磁阀自动测试装置中的控制及采集单元的电路图;
45.图8是本发明提供的电磁阀自动测试装置中的供电单元的电路图;
46.图9是本发明提供的电磁阀自动测试装置中的操作台的结构图;
47.图10是本发明提供的电流特性曲线的示例图。
具体实施方式
48.为了对本发明的技术特征、目的和效果有更加清楚的理解,现对照附图详细说明本发明的具体实施方式。
49.参考图1,本发明提供了一种电磁阀自动测试装置,用于自动测试核电厂二回路电磁阀的性能,该装置包括:液压油路单元2、空气动力单元3、控制及采集单元4和至少一个测试接口单元1。
50.测试接口单元1用于连接待测电磁阀;液压油路单元2与各测试接口单元1连接,用于为待测电磁阀提供测试油压;空气动力单元3与液压油路单元2,用于控制液压油路单元2的油路启闭;控制及采集单元4与液压油路单元2、空气动力单元3和各测试接口单元1连接,用于控制待测电磁阀进行密封性及电气性能测试,并采集待测电磁阀的测试数据,进而根据测试数据出具测试结果。
51.一些实施例中,如图2和图3所示,液压油路单元2包括:背压回路单元21和液压主油路单元22。
52.背压回路单元21与控制及采集单元4和各测试接口单元1连接,用于根据述控制及采集单元4输出的背压控制指令为待测电磁阀提供背压;液压主油路单元22与控制及采集单元4、背压回路单元21和各测试接口单元1连接,用于根据述控制及采集单元4输出的主油路控制指令为待测电磁阀提供主油路油压,以及为背压回路单元21供油。
53.一些实施例中,如图2所示,液压主油路单元22包括:储油单元221、进油阀222、第一过滤阀223、气动油泵224、比例阀225、过滤器226、第一隔离阀227、废油收集单元228和卸荷阀229。
54.储油单元221的输出端连接经进油阀222和第一过滤阀223连接至气动油泵224的输入端,气动油泵224的进气端连接空气动力单元3,气动油泵224的控制端经比例阀225连接至控制及采集单元4,气动油泵224的输出端连接背压回路单元21的输入端和过滤器226的输入端,过滤器226的输出端连接第一隔离阀227的输入端,第一隔离阀227的输出端连接各测试接口单元1的主油路输入端,废油收集单元228连接各测试接口单元1,气动油泵224的输出端经卸荷阀229连接至废油收集单元228。
55.具体的,进油阀222用于控制储油单元221是否向后级管道输出液压油。第一过滤阀223用于对液压油进行过滤,以避免存在杂质而导致阻碍液压油传输及管道堵塞。气动油泵224用于为后级管道的液压油提供传输动力,其型号可以为sc hydraulic engineering公司的d50vab105空气动力油泵。比例阀225用于对输入到气动油泵224的气源压力进行按比例放大,进而控制气动油泵224的功率,而比例阀225的输出受控于控制及采集单元4。过滤器226对输入至主油路的液压油进行进一步的杂质过滤,其型号可以为epf1102qivm3kg081。第一隔离阀227用于控制输入至主油路的液压油油压。废油收集单元228用于回收待测电磁阀输出的液压油以及排出的废油。卸荷阀229用于防止气动油泵224输出的油压超限,其型号可以为ss-4r3a,安全卸荷压力整定值可以为400bar。液压主油路单元22在工作时,进油阀222打开,气动油泵224启动,进而为背压回路单元21供油;第一隔离阀227开启时,则为各测试接口单元1提供主油路油压。
56.一些实施例中,如图2所示,储油单元221包括储油箱2211、第一液位计2212、第一排油阀2213。储油箱2211的输出端对应为储油单元221的输出端,储油箱2211用于提供测试用的液压油。第一液位计2212设有储液箱2211上,以检测储液箱2211的液位。第一排油阀2213连接储油箱2211的排油端,以在储液箱2211液位过高时进行排油。
57.一些实施例中,如图2所示,废油收集单元228包括回油槽2281、废油收集箱2282、第二液位计2283和第三排油阀2284。回油槽2281的输入端连接各测试接口单元1,以收集待测电磁阀输出的液压油以及排出的废油;其输出端连接废油收集箱2282,以将收集到废油导入至废油收集箱2282。废油收集箱2282连接卸荷阀229,以收集卸荷阀229开启时输出的液压油。第二液位计2283设于废油收集箱2282上,以检测废油收集箱2282的液位。废油收集箱2282还连接第三排油阀2284,以在废油收集箱2282液位过高时进行排油。
58.需要说明的是,,在液压主油路单元22中,各个部件通过液压油传输管道进行连接的。进一步地,管道可以为1/2英寸的不锈钢仪表管。
59.一些实施例中,如图3所示,背压回路单元21包括第二过滤阀211、第一气动隔离阀212和第一调压阀213。
60.第二过滤阀211的输入端为背压回路单元21的输入端,第二过滤阀211的输出端经第一气动隔离阀212连接至第一调压阀213的输入端,第一气动隔离阀212的进气端连接空气动力单元3,第一气动隔离阀212的控制端连接控制及采集单元4,第一调压阀213的输出端作为背压回路单元21的输出端连接各测试接口单元1的背压输入端。
61.具体的,第二过滤阀211用于对输入至背压回路单元21的液压油进行进一步杂质过滤。第一气动隔离阀212用于控制输入至背压回路单元21的液压油的开闭,并受控于控制及采集单元4,其型号可以为vap6pbvc9d9。第一调压阀213用于控制背压回路单元21输入至各测试接口单元1的背压大小,其型号可以为kpr1fwa425a60000(自带压力表,并可手动调节)。
62.需要说明的是,在背压回路单元21中,各个部件通过液压油传输管道进行连接的。进一步地,管道可以为3/8英寸的不锈钢仪表管。
63.一些实施例中,如图4所示,每一个测试接口单元1包括第二气动隔离阀11、第一排气阀12、被测电磁阀底座13、第三气动隔离阀14、第一电磁阀15、第二排气阀16和第四气动隔离阀17。
64.第二气动隔离阀11的输入端为测试接口单元1的主油路输入端,第二气动隔离阀11的进气端连接空气动力单元3,第二气动隔离阀11的控制端连接控制及采集单元4,第二气动隔离阀11的输出端连接第一排气阀12的输入端和被测电磁阀底座13的主油输入端,第一排气阀12的输出端连接废油收集单元228(回油槽2281);
65.第三气动隔离阀14的输入端为测试接口单元1的背压输入端连接第一电磁阀15的输入端,第一电磁阀15的控制端连接控制及采集单元4,第一电磁阀15的输出端连接废油收集单元228(回油槽2281),第三气动隔离阀14的进气端连接空气动力单元3,第三气动隔离阀14的控制端连接控制及采集单元4,第三气动隔离阀14的输出端连接被测电磁阀底座13的背压输入端,第三气动隔离阀14的输出端还经第二排气阀16连接至废油收集单元228(回油槽2281);
66.被测电磁阀底座13的输出端经第四气动隔离阀17连接至废油收集单元228(回油
槽2281),第四气动隔离阀17的进气端连接空气动力单元3,第四气动隔离阀17的控制端连接控制及采集单元4,被测电磁阀底座13的排油输出端连接废油收集单元228(回油槽2281)。
67.具体的,第二气动隔离阀11、第三气动隔离阀14和第四气动隔离阀17用于控制相应管道上的液压油的开闭,并受控于控制及采集单元4,其型号可以为vap6pbvc9d9。第一排气阀12和第二排气阀16用于对相应管道内的空气进行排放,以避免管道中存在空气,其型号可以为swagelok公司的ss-6nbs6-blp,用户可以手动控制其开闭。被测电磁阀底座13用于连接待测电磁阀,使待测电磁阀与相应液压油传输管道进行连接。第一电磁阀15用于控制背压回路单元21的输出端与回油槽2281之间的开闭,以降低背压,其受控于控制及采集单元4,可以为两位两通电磁阀。
68.需要说明的是,在每一个测试接口单元1中,各个部件通过液压油传输管道进行连接的。进一步地,管道可以为3/8英寸的不锈钢仪表管。
69.一些实施例中,如图5所示,空气动力单元3包括空气压缩机31、气源隔离阀32、空气电磁阀33、第一过滤减压阀34、第二过滤减压阀35和消音器36。
70.空气压缩机31的输出端连接气源隔离阀32的输入端,气源隔离阀32的输出端经空气电磁阀33、第一过滤减压阀34和消音器36连接至气动油泵224的进气端,气源隔离阀32的输出端还连接第二过滤减压阀35的输入端,第二过滤减压阀35的输出端连接各第一气动隔离阀212、第二气动隔离阀11、第三气动隔离阀14和第四气动隔离阀17的进气端,空气电磁阀33的控制端连接控制及采集单元4。空气电磁阀33
71.具体的,空气压缩机31用于为各气动隔离阀提供驱动气源,其型号可以为捷豹空压机ev-51。气源隔离阀32用于控制空气压缩机31的输出端是否对后级管道的开闭。空气电磁阀33用于控制输入至气动油泵224的气源开闭,其型号可以为cpe18-m1h-3gl-qs-10。第一过滤减压阀34、第二过滤减压阀35用于调节相应管道上的气压大小,其型号可以为ms4-lfr-1/4-d6-c-u-v(自带压力表,并可手动调节)。
72.需要说明的是,在空气动力单元3中,各个部件通过气管进行连接的。进一步地,气管的尺寸可以为3/8英寸。
73.一些实施例中,如图6和图7所示,控制及采集单元4包括:采集单元和控制单元。
74.采集单元连接第一隔离阀227的输出端和各被测电磁阀底座13,采集单元用于采集主油路油压,每一个待测电磁阀的背压、输入电压和输入电流(主油路油压、背压、输入电压和输入电流组成测试数据)。控制单元连接采集单元、空气电磁阀33的控制端和各第一电磁阀15的控制端,控制单元用于控制待测电磁阀进行密封性及电气性能测试,并根据主油路油压、背压、输入电压和输入电流出具测试结果;其中,密封性及电气性能测试包括失磁密封试验、励磁密封试验、保压试验、电流特性试验和启动释放电压试验中的至少一种。
75.一些实施例中,如图6所示,采集单元包括:电压传感器411、两个气压传感器417、若干与至少一个测试接口单元1相对应的电流测试单元412和若干压力传感器413。
76.电压传感器411与各被测电磁阀底座13的供电端连接,用于采集每一个待测电磁阀的输入电压。具体的,各被测电磁阀底座13的供电端是并联连接的,在被测电磁阀底座13接入待测电磁阀后,可以通过电压传感器411待测电磁阀的输入电压大小,为保压试验、电流特性试验和启动释放电压试验提供分析所需的数据。
77.各气压传感器417分别与第一过滤减压阀34和第二过滤减压阀35的输出端一一连接,以采集输入至气动设备(包括气动油泵224,以及第一至第四气动隔离阀)的气压。
78.各电流测试单元412分别与各被测电磁阀底座13一一对应连接,以采集每一个待测电磁阀的输入电流。具体的,电流测试单元412可以为电流互感器或者现有技术中常用的电阻式电流采样装置或设备(使用取样电阻串联在相应测试接口单元1的供电端或接地端上,通过采集取样电阻的电压,结合欧姆定律得到对应待测电磁阀的输入电流大小)。
79.各压力传感器413分别与第一隔离阀227的输出端和各被测电磁阀底座13的背压输入端一一对应连接,以采集主油路油压和每一个待测电磁阀的背压。具体的,压力传感器413可以为型号是acd-201的数字压力表。
80.电压传感器411、各气压传感器417、各电流测试单元412和各压力传感器413还与控制单元连接(图6未完全示出),以将相应的采集数据发送至控制单元。
81.一些实施例中,如图6所示,采集单元还包括两个用于测量主电磁阀的开关位置的限位开关测试模块416。各限位开关测试模块416分别与控制单元一一连接,各限位开关测试模块416还分别与两个被测电磁阀底座13连接。
82.一些实施例中,如图6和图7所示,控制单元包括上位机421、控制器422、电压采集卡423、电压输出卡424、继电器模块425和电流输出卡426。
83.上位机421连接控制器422,以向控制器422发送相关的控制指令,包括控制比例阀工作,以及相应气动隔离阀和电磁阀(包含第一电磁阀15、空气电磁阀33和各待测电磁阀)的开闭等,进而使待测电磁阀进行密封性及电气性能测试;并通过控制器422获取测试时,采集单元采集到的测试数据,并根据测试数据出具测试结果。进一步地,上位机421可以为电脑,与控制器422通过网口实现信息交互。
84.控制器422连接电压采集卡423、电压输出卡424和电流输出卡426,电压采集卡423连接电压传感器411、各电流测试单元412和压力传感器413;控制器422通过电压采集卡423可以获取测试数据,还可以控制电压输出卡424和电流输出卡426的工作。进一步地,控制器422的型号可以为crio 9023(美国国家仪器公司生产)。
85.电压输出卡424连接继电器模块425、第一气动隔离阀212、第二气动隔离阀11、第三气动隔离阀14和第四气动隔离阀17的控制端,以控制相关气动隔离阀和继电器模块的开闭。进一步地,电压输出卡424的型号可以为crio9474(美国国家仪器公司生产)。
86.继电器模块425连接气动油泵224的供电端和各被测电磁阀底座13的供电端,以使电压输出卡424通过继电器模块425控制第一电磁阀15、空气电磁阀33和各待测电磁阀是否通电。进一步地,继电器模块425由若干继电器组成,每个继电器的励磁线圈与电压输出卡424的输出端口一一对应连接,每个继电器的常闭或常开回路则分别一一串联在第一电磁阀15、空气电磁阀33和各待测电磁阀的供电端与相应电源之间,使电压输出卡424可以通过控制相应励磁线圈是否励磁,进而控制第一电磁阀15、空气电磁阀33和各待测电磁阀是否通电。
87.电流输出卡426连接比例阀225的调节端,以根据控制器422输出的调节指令输出相应电流,以控制比例阀225的输出,进而控制气动油泵224的输出动力。进一步地,电流输出卡426的型号可以为crio 9265(美国国家仪器公司生产)。
88.一些实施例中,如图6和图8所示,电磁阀自动测试装置还包括供电单元和急停开
关6。
89.其中,供电单元包括用于为待测电磁阀提供输入电压的可调直流电源51、用于提供模拟电压的第一直流电源52和用于提供数字电压的第二直流电源53。可调直流电源51连接急停开关6的第一常闭回路的第一端,急停开关6的第一常闭回路的第二端连接各测试接口单元1的供电端,第一直流电源52的输出端经急停开关6的第二常闭回路连接至控制及采集单元4,第二直流电源53的输出端连接控制及采集单元4。
90.具体的,第一直流电源52用于为电压采集卡423、电压输出卡424、电流输出卡426、电压传感器411、各限位开关测试模块416、各气压传感器417、各电流测试单元412和各压力传感器413供电,可以为西门子sitop smart 24v电源。第二直流电源53用于为控制器422供电,可以为西门子sitop smart 24v电源。对于急停开关6,如图6和图8所示,其第一常闭回路(第三触点和第四触点)串接在可调直流电源51的输出端,按下可以急停开关6断开各待测电磁阀的输入电源;其第二常闭回路(第一触点和第二触点)则串接在控制气动油泵224供电的继电器的励磁线圈输入端,按下可以急停开关6断开气动油泵224的输入电源。
91.一些实施例中,如图8所示,可调直流电源51包括可调电源511、电阻器512和数字电压表513。可调电源511与电阻器512和数字电压表513连接。具体的,可调电源511为输出电压可调直流电源,以应对不同输入电压的待测电磁阀,其型号可以为4nic-k60/g。电阻器可以为可调电阻,通过调节电阻可以实现对可调电源511输出电压调节。数字电压表513用于显示可调电源511的输出电压(端口v+与端口dc20-200+的电压相等,端口v-与端口gnd/-的电压相等)。
92.一些实施例中,如图8所示,供电单元还包括电源总开关54和空气开关55。电源总开关54的输入端连接市电,电源总开关54的输出端连接空气开关55的输入端,空气开关55的输出端连接可调直流电源51、第一直流电源52和第二直流电源53的供电端。
93.优选地,测试接口单元1的数量为4个,可以同时测量核电厂二回路的2个主电磁阀和两个实验电磁阀;其中,主电磁阀的型号可以为flowserve edward公司的48v dc-0-1,实验电磁阀的型号可以为flowserve edward公司的48v dc-0-0。对应地,压力传感器413的数量为5个,电流测试单元412的数量为4个。
94.一些实施例中,电磁阀自动测试装置还包括由于收纳液压油路单元2、空气动力单元3、控制及采集单元4和各测试接口单元1的壳体。如图9所示,壳体包括设于顶面的操作台71,气源隔离阀32、第一过滤减压阀34、第二过滤减压阀35、第一调压阀213、各被测电磁阀底座(13)、各压力传感器413、各第一排气阀12和各第二排气阀16设于操作台上,以便用户对数据进行观察,进行手动调节,以及接入待测电磁阀。
95.进一步地,如图9所示,操作台71的一侧还延伸出用于放置上位机421的承载板。
96.一些实施例中,如图8所示,供电单元还包括第一散热风扇fan1和第二散热风扇fan2。第一散热风扇fan1和第二散热风扇fan2连接第一直流电源52,并设于壳体内,从而为测试装置散热内的发热部件散热。
97.电磁阀自动测试装置的测试过程如下:
98.失磁密封试验:自动或手动载入失磁密封试验的试验设定时间(一般为10分钟)、比例阀参数、空气电磁阀额定参数、待测电磁阀额定电压,开启空气电磁阀33和各隔离阀,使待测电磁阀的主油输入端(p侧)根据载入参数保持压力基本不变,待测电磁阀的背压输
入端(t侧)的背压也保持在一定范围内(如5-10bar),使待测电磁阀失磁,并持续试验设定时间,在试验过程中,采集并记录失磁前以及失磁持续时间结束后的主油路油压和背压,若失磁前的主油路油压和背压与相应的试验完成后的主油路油压和背压的差值小于报警阈值,则判定待测电磁阀失磁密封试验合格;
99.励磁密封试验:励磁密封试验的工作过程与失磁密封试验类似,区别在于测试过程中待测电磁阀的失磁状态转变为励磁状态,是否合格判断原理也与失磁密封试验相仿,在次不再叙述;
100.保压试验:保压试验是在待测电磁阀处于失磁状态下,长时间在高压力环境下,测试电磁阀失磁面密封性能,该试验与失磁密封试验相仿,区别在于其保压时间相对试验设定时间较长(一般为15分钟),可以手动设置试验时间及压力阈值,可同时对4个待测电磁阀进行保压测试;持续采集并记录保压试验过程中的主油路油压和背压,并可以曲线形式呈现,还对主油路油压和背压的采集数据进行分析,根据保压试验起始时及结束后的主油路油压和背压判断相应待测电磁阀的保压试验是否合格;
101.电流特性试验:使待测电磁阀处于运行状态,并持续采集试验设定时间内的待测电磁阀的工作电流(使用电流测试单元41采集),以此生成电流特性曲线,结合核电厂标准电磁阀电流特性标准,分析电流特性曲线,以判断电流特性是否合格;进一步地,参考图10,若待测电磁阀在刚开启时刻(a点)到进入稳定开启状时刻(c点)后的电流比值(ia/ic)在预设范围内(一般为60%-80%),则判定待测电磁阀的电流特性合格。
102.启动释放电压试验:采集待测电磁阀开启及失磁时的开启及释放电流和开启及释放电压(使用电流测试单元412和电压传感器411采集),通过分析开启及释放电流和开启及释放电压判断启动释放电压试验是否合格;
103.各项测试的判断结果组成测试结果。
104.可以理解的,本发明装置不仅操作简单,减少测试人员工作量,还提高主电磁阀和试验电磁阀的测试效率,降低人因操作失误风险,而且测试项目完整及全面,测试结果准确、直观。
105.可以理解的,以上实施例仅表达了本发明的优选实施方式,其描述较为具体和详细,但并不能因此而理解为对本发明专利范围的限制;应当指出的是,对于本领域的普通技术人员来说,在不脱离本发明构思的前提下,可以对上述技术特点进行自由组合,还可以做出若干变形和改进,这些都属于本发明的保护范围;因此,凡跟本发明权利要求范围所做的等同变换与修饰,均应属于本发明权利要求的涵盖范围。