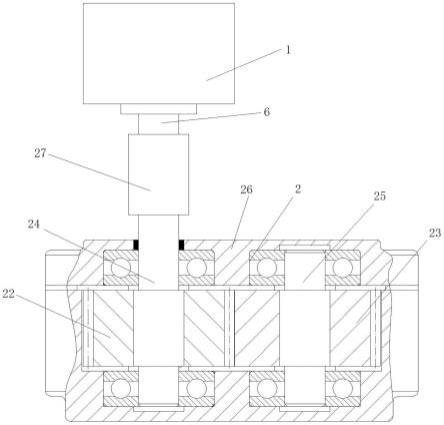
1.本发明涉及测量技术领域,具体涉及一种基于旋转编码器的电子齿轮流量计及测量方法。
背景技术:2.在医药、化工、酿造、能源等行业中,生产原材料很大一部分为流体,包括液体与气体。在生产过程中,原料的精确、稳定供给对反应过程与制品品质具有直接影响。而为了确保流量的稳定准确控制,流量的精密测量是重要前提。当前,流量计种类繁多,其中,齿轮流量计(包含圆齿轮流量计与椭圆齿轮流量计)原理简单、结构紧凑、可测量各种粘度的流体,因而,被广泛应用于石油、化工、食品、医药等领域。传统的齿轮流量计多为机械式,通过传动链可方便地将齿轮转角信息传递出来,并转化为相应的排量数据。
3.为适应自动化生产的需要,各类电子齿轮流量计也被发明出。当前,市场上最为流行的是基于霍尔效应的电子齿轮流量计,其工作原理为:齿轮对每转过一个齿,壳体和齿之间的磁通量变化,从而引起输出电压变化;通过调理电路,流量计每转过一个齿,产生一个电压或电流脉冲。这种电子流量计可很方便地实现流量的实时数显。然而,由于齿轮的齿数相对较少,齿轮旋转一圈输出的脉冲数也较少,这意味着,测量的分辨率较低,精度较差。
技术实现要素:4.本发明的目的是为了克服以上现有技术存在的不足,提供了一种基于旋转编码器的电子齿轮流量计。此基于旋转编码器的电子齿轮流量计的分辨率低,精度差。
5.同时,本发明的另一目的是提供了一种基于旋转编码器的电子齿轮流量计的测量方法。
6.本发明的目的通过以下的技术方案实现:本基于旋转编码器的电子齿轮流量计,包括机械齿轮流量计、旋转编码器、解码器和细分算法模块,所述机械齿轮流量计的输出轴与旋转编码器的码盘连接,所述细分算法模块和解码器均与旋转编码器连接。
7.优选的,所述旋转编码器包括码盘、编码轴、光源、光电转换器和调理电路,所述码盘安装于编码轴,所述光源和光电转换器分别安装于编码盘的两侧,且所述光源和光电转换器正对设置;所述光电转换器与调理电路连接,所述细分算法模块和解码器均与调理电路连接。
8.优选的,所述调整电路和细分算法模块集成成处理电路,所述处理电路包括脉冲计数模块和5个电压比较器,5个电压比较器分别为第一电压比较器、第二电压比较器、第三电压比较器、第四电压比较器和第五电压比较器,所述第一电压比较器、第二电压比较器、第三电压比较器、第四电压比较器和第五电压比较器的输入端均与光电转换器连接,其中,所述第一电压比较器同时连接脉冲计数模块和解码器,所述第三电压比较器的输出端连接于解码器;所述第二电压比较器、第四电压比较器和第五电压比较器均连接于脉冲计数模块。
9.优选的,所述脉冲计数模块包括依次连接的第一与门、计算器和锁存器,所述第一电压比较器、第四电压比较器和第五电压比较器的输出端均与第一与门连接,所述第二电压比较器的输出端与计算器连接。
10.优选的,所述机械齿轮流量计包括第一齿轮、第二齿轮、输出轴和转动轴和外壳,所述第一齿轮和第二齿轮分别通过输出轴和转动轴安装于外内壳内,所述输出轴通过联轴器与编码轴连接;所述第一齿轮和第二齿轮啮合后外壳的内腔分隔形成具有压力差的上游腔和下游腔。
11.基于旋转编码器的电子齿轮流量计的测量方法,采用上述的基于旋转编码器的电子齿轮流量计,包括以下步骤:
12.s1、机械齿轮流量计带动旋转编码器,旋转编码器通过调理电路输出a、b和z这三相正弦波像信号或方波信号,其中a和b相信号的相位差为90
°
;
13.s2、解码器对输出的a、b和z相信号进行解码,以确定机械齿轮流量计的输出轴的旋转圈数和零点位置判定,同时确定机械齿轮流量计的输出轴的累积旋转角位置和旋转方向;
14.s3、细分算法模块对解码器的解码信息进行处理,以计算出流量。
15.优选的,步骤s2中的具体过程包括以下步骤:
16.s21、圈数及零点位置判定:一方面,z相信号提供绝对的零角位置,另一方面,对z相信号进行脉冲计数,以确定流量计输出轴的旋转整圈数n;
17.s22、角位移计算:对a相信号进行脉冲读数,确定输出轴的旋转角度θ:
18.此为式(1);
19.其中,m为码盘上的狭缝条数,m为a相信号的脉冲计数值;
20.基于式(1)得机械齿轮流量计的输出轴的累积旋转角位移θ
total
:
21.,此为式(2);
22.s23、旋转方向判断:对a和b相信号作正交解码以判断a、b相信号的相位:
23.若a相信号超前b相信号,则判定输出轴正转,旋转角位置记为+θ;
24.若a相信号滞后b相信号,则判定编码器(或流量计输出轴)反转,旋转角位移记为-θ。
25.优选的,步骤s3的具体过程包括以下步骤:
26.s31、令a相信号为正弦信号,则ua=sinα,此为式(3),其中ua为旋转编码器a相信号的幅值,α为相位角;
27.s32、令细分倍数为l,则在一个正弦信号周期内,l个细分位置对应的相位角分别为:
28.此为式4),其中,i的取值为0,1,2,
…
,l-1;
29.l个细分位置对应的电压幅值分别为:
30.ui=sinαi,此为式(5),其中,i的取值为0,1,2,
…
,l-1;
31.s33、每经过一个ui,逻辑电路输出一个细分脉冲,对细分脉冲进行计数,其值记为
l,则细分后,流量计输出轴的旋转角位移等于:此为式(6);而转角分辨率为:
32.s34、利用步骤s33中的旋转角位移及转角分辨率计算最终流量q和流量分辩率δq:
[0033][0034][0035]
本发明相对于现有技术具有如下的优点:
[0036]
1、相较基于霍尔效应的电子齿轮流量计(流量分辨率由齿数z决定,等于),本发明所提出的基于旋转编码器的电子齿轮流量计,其流量分辨率由编码器狭缝条数和细分倍数决定,等于同时将机械齿轮流量计的检测结果进行光电转换,于同对光电转换得到的信号进行处理,从而可大幅度提高了齿轮流量计的测量精度。
[0037]
2、本发明利用旋转编码器输出a、b相信号的相位差,可判断流经齿轮流量计的流动方向。
[0038]
3、本发明将流量信息转化为旋转编码器的角位移信息,目前,数控系统几乎都配置有编码器解码器,因此,流量信息可方便地直接反馈给数控系统,这将极大地便利基于数控系统与伺服电机的流量控制系统的开发。
附图说明
[0039]
图1是本发明的基于旋转编码器的电子齿轮流量计的结构示意图。
[0040]
图2是本发明的旋转编码器的示意图。
[0041]
图3是本发明的a、b、z三相信号的示意图。
[0042]
图4是本发明的细分算法模块的细分算法原理图i。
[0043]
图5是本发明的细分算法模块的细分算法原理图ii。
[0044]
图6是本发明的电路图。
[0045]
其中,1为机械齿轮流量计,2为旋转编码器,3为解码器,4为细分算法模块,5为码盘,6为编码轴,7为光源,8为光电转换器,9为调理电路,10为第一电压比较器,11为第二电压比较器,12为第三电压比较器,13为第四电压比较器,14为第五电压比较器,15为脉冲计数模块,16为第一与门,17为计算器,18为锁存器,19为d触发器,20为第二与门,21为示波器,22为第一齿轮,23为第二齿轮,24为输出轴,25为转动轴,26为外壳,27为联轴器。
具体实施方式
[0046]
下面结合附图和实施例对本发明作进一步说明。
[0047]
如图1、图2和图6所示的基于旋转编码器的电子齿轮流量计,包括机械齿轮流量
计、旋转编码器、解码器和细分算法模块,所述机械齿轮流量计的输出轴与旋转编码器的码盘连接,所述细分算法模块和解码器均与旋转编码器连接。
[0048]
具体的,旋转编码器输出的a、b和z这三相正弦波信号,其中其中a、b相信号相位差为90
°
;主码盘每转一圈,z相产生一个脉冲,称为“一转脉冲”。a、b、z三相信号如图3所示。在解码器和细分算法模块分别对a、b和z三相信号进行处理,从而提高电子齿轮流量计的检测精度和检测的准确性,为数控系统提供可靠的保证。
[0049]
如图2所示,所述旋转编码器包括码盘、编码轴、光源、光电转换器和调理电路,所述码盘安装于编码轴,所述光源和光电转换器分别安装于编码盘的两侧,且所述光源和光电转换器正对设置;所述光电转换器与调理电路连接,所述细分算法模块和解码器均与调理电路连接。具体的,编码轴通过联轴器与机械齿轮流量计的输出轴连接,则安装在编码轴的码盘可与和机械齿轮流量计中的齿轮同步转动,从而保证检测的准确性。
[0050]
所述调整电路和细分算法模块集成成处理电路,所述处理电路包括脉冲计数模块和5个电压比较器,5个电压比较器分别为第一电压比较器、第二电压比较器、第三电压比较器、第四电压比较器和第五电压比较器,所述第一电压比较器、第二电压比较器、第三电压比较器、第四电压比较器和第五电压比较器的输入端均与光电转换器连接,其中,所述第一电压比较器同时连接脉冲计数模块和解码器,所述第三电压比较器的输出端连接于解码器;所述第二电压比较器、第四电压比较器和第五电压比较器均连接于脉冲计数模块,具体连接如图6所示。调整电路和细分算法模块优化了电路设计,提升了处理效率。集成的处理电路通过电压比较器实现调理、细分算法功能,分别以a、b、z三相信号作为电压比较器的正相输入端vi,以细分的参考电压作为反向相输入端v
p
,通过两者比较整形输出可以被计数器、d触发器等可识别的高低电平信号;第一电压比较器、第四电压比较器和第五电压比较器分别对参考电压值为sin(0=sin(π)、sin(π/3)=sin(2/3)、sin(4/3)=sin(5/3),可以实现6倍频细分,即将码盘的每条狭缝的正弦信号的信号周期细分6倍,具体原理如图4和图5所示:
[0051]
第一步:ui分别为u1=0、u2=sinpi/3、u3=sin2pi/3、u4=sinpi、u5=sin4pi/3、u6=sin5pi/3,可见u2=u3,u1=u4,u5=u6。
[0052]
第二步:通道c1中,当电压大于u1为高电平,否则为低电平;依次以同理作比较,则通道c2~c6中,当电压大于各通道设置比较电压为高电平,否则为低电平,其结果如图4所示。
[0053]
第三步:识别通道c1~c6中的上升沿与下降沿,赋值为高电平,其他为低电平,识别结果为d1~d6;然后,对d1~d6进行或门运算,则在所有的ui处都将出现一个高电平脉冲,如图5所示。
[0054]
根据需要可以选择更高的倍频,当与排量q为2ml/r齿轮流量计结合时,排量分辨率可达6.7
×
10-5
ml/脉冲,流量分辨率可达6.7
×
10-5
ml/r,相对于齿数为10、排量为2ml/r的基于霍尔效应的电子齿轮流量计,其排量分辨率仅为0.2ml/脉冲,融合旋转编码器后,流量计排量、流量分辨率皆提升2985倍。
[0055]
所述脉冲计数模块包括依次连接的第一与门、计算器和锁存器,所述第一电压比较器、第四电压比较器和第五电压比较器的输出端均与第一与门连接,所述第二电压比较器的输出端与计算器连接。其中第一与门的输入端连接第一电压比较器、第四电压比较器
和第五电压比较器的输出端经细分的a相脉冲信号,第一与门输出信号给计数器u/d接口,比较器2的输出段为z相的调理后的脉冲信号,与计数器的reset接口连接,用于脉冲计数清零,继而传输至锁存器便于数据错误。
[0056]
而解码器包括依次连接d触发器、第二与门和示波器,其中d触发器的d接口与第三电压比较器的输出端连接,而d触发器的clk接口与第一电压比较器的输出端连接,从而实现差别a、b相信号的相位差。
[0057]
所述机械齿轮流量计包括第一齿轮、第二齿轮、输出轴和转动轴和外壳,所述第一齿轮和第二齿轮分别通过输出轴和转动轴安装于外内壳内,所述输出轴通过联轴器与编码轴连接;所述第一齿轮和第二齿轮啮合后外壳的内腔分隔形成具有压力差的上游腔和下游腔。此结构简单,稳定性好,进一步保证检测的精准性。
[0058]
基于旋转编码器的电子齿轮流量计的测量方法,采用上述的基于旋转编码器的电子齿轮流量计,包括以下步骤:
[0059]
s1、机械齿轮流量计带动旋转编码器,旋转编码器通过调理电路输出a、b和z这三相正弦波像信号或方波信号,其中a和b相信号的相位差为90
°
;
[0060]
s2、解码器对输出的a、b和z相信号进行解码,以确定机械齿轮流量计的输出轴的旋转圈数和零点位置判定,同时确定机械齿轮流量计的输出轴的累积旋转角位置和旋转方向;
[0061]
步骤s2中的具体过程包括以下步骤:
[0062]
s21、圈数及零点位置判定:一方面,z相信号提供绝对的零角位置,另一方面,对z相信号进行脉冲计数,以确定流量计输出轴的旋转整圈数n;
[0063]
s22、角位移计算:对a相信号进行脉冲读数,确定输出轴的旋转角度θ:
[0064]
此为式(1);
[0065]
其中,m为码盘上的狭缝条数,m为a相信号的脉冲计数值;
[0066]
基于式(1)得机械齿轮流量计的输出轴的累积旋转角位移θ
total
:
[0067]
,此为式(2);
[0068]
s23、旋转方向判断:对a和b相信号作正交解码以判断a、b相信号的相位:
[0069]
若a相信号超前b相信号,则判定输出轴正转,旋转角位置记为+θ;
[0070]
若a相信号滞后b相信号,则判定编码器(或流量计输出轴)反转,旋转角位移记为-θ。
[0071]
s3、细分算法模块对解码器的解码信息进行处理,以计算出流量。
[0072]
步骤s3的具体过程包括以下步骤:
[0073]
s31、令a相信号为正弦信号,则ua=sinα,此为式(3),其中ua为旋转编码器a相信号的幅值,α为相位角;
[0074]
s32、令细分倍数为l,则在一个正弦信号周期内,l个细分位置对应的相位角分别为:
[0075]
此为式4),其中,i的取值为0,1,2,
…
,l-1;
[0076]
l个细分位置对应的电压幅值分别为:
[0077]
ui=sinαi,此为式(5),其中,i的取值为0,1,2,
…
,l-1;
[0078]
s33、每经过一个ui,逻辑电路输出一个细分脉冲,对细分脉冲进行计数,其值记为l,则细分后,流量计输出轴的旋转角位移等于:此为式(6);而转角分辨率为:
[0079]
s34、利用步骤s33中的旋转角位移及转角分辨率计算最终流量q和流量分辩率δq:
[0080][0081][0082]
上述具体实施方式为本发明的优选实施例,并不能对本发明进行限定,其他的任何未背离本发明的技术方案而所做的改变或其它等效的置换方式,都包含在本发明的保护范围之内。