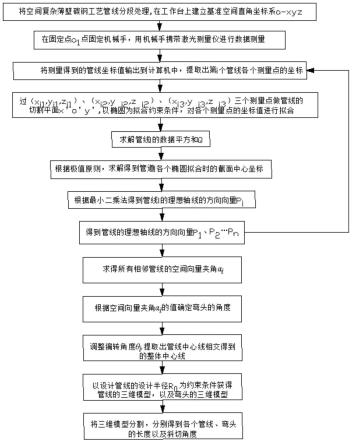
1.本发明主要涉及管线结构焊接领域,具体涉及一种空间复杂薄壁碳钢工艺管线姿态测量方法。
背景技术:2.薄壁管线是管线焊接过程中非常重要的一部分,薄壁管线通常应用在空间管线部分的焊接,在空间薄壁管线的焊接过程中,薄壁管线的空间姿态以及弯头的角度测量是非常关键的问题,如果不能精准的测量出薄壁管线的空间姿态以及弯头的角度在焊接完成后就会造成焊接后的管线产生错位的现象,且极易产生焊接变形,这对薄壁管线的对接精度产生非常大的影响,无法保证管线对接过程中的精度。现阶段对于空间薄壁管线仍然需要采用人工测量的方式,在很大的程度上需要依靠工人的测量经验,这很容易造成空间薄壁管线对接过程中出现误差,进行需要重新切割重新焊接或者重新矫正,造成空间薄壁管线使用性能变差。
技术实现要素:3.本发明的目的在于克服已有技术的缺点,提供一种空间复杂薄壁碳钢工艺管线姿态测量方法,通过对空间薄壁管线的对接模型的测量与求解,实现对空间薄壁管线的弯头的正确选用,实现了空间薄壁管线的精准对接,减少焊接变形,提高了焊接效率,保证了操作安全。
4.实现本发明的目的技术方案如下:
5.本发明的一种空间复杂薄壁碳钢工艺管线姿态测量方法,包括以下步骤:
6.步骤一、将待检测的空间复杂薄壁碳钢工艺管线夹持在工作台上,将空间复杂薄壁碳钢工艺管线分段处理,标记为l1、l2…
ln,在工作台上建立基准空间直角坐标系o-xyz,以工作台的垂直方向为y轴,水平向右为x轴,水平向前为z轴;
7.步骤二、在工作台上选择空间直角坐标系o-xyz的固定点o1点为零点坐标固定机械手,用机械手携带激光测量仪,沿着管线的平行线对薄壁碳钢工艺管线进行测量;
8.步骤三、对薄壁碳钢工艺管线测量完成后,将测量得到的管线坐标值输出到计算机中,提取出第i个管线各个测量点的坐标(x
i1
,y
i1
,z
i1
)、(x
i2
,y
i2
,z
i2
)
…
(x
in
,y
in
,z
in
);
9.步骤四、过(x
i1
,y
i1
,z
i1
)、(x
i2
,y
i2
,z
i2
)、(x
i3
,y
i3
,z
i3
)三个测量点做管线的切割平面x’o’y’,将提取出第i个管线各个测量点投影到x’o’y’平面上,得到测量点的平面坐标值,(x
i1’,y
i1’)、(x
i2’,y
i2’)
…
(x
in’,y
in’),以椭圆为拟合约束条件,对步骤三得到的各个测量点的坐标值进行拟合;
10.步骤五、将步骤四管线i的平面坐标值(x
i1’,y
i1’)、(x
i2’,y
i2’)
…
(x
in’,y
in’)带入步骤四椭圆公式中,求解管线i的数据平方和q;
11.步骤六、根据极值原则,对管线i的数据平方和q的各参数{a、b、c、d、e、f}进行求导并令求导后的值等于零,得到各个参数的最优解,再根据椭圆的标准式求解得到管道i各个
椭圆拟合时的截面中心坐标;
12.步骤七、根据最小二乘法对管道i各个椭圆拟合时的截面中心坐标进行空间直线拟合,得到管线i的理想轴线的方向向量pi;
13.步骤八、分别做管线l
i+1
、l
i+2
的切割面x’o’z’、y’o’z’,重复步骤三至步骤七,得到所有管线的理想轴线的方向向量p1、p2…
pn;
14.步骤九、根据相邻管线的方向向量pi(ai,bi,ci),p
i+1
(a
i+1
,b
i+1
,c
i+1
)求得所有相邻管线的空间向量夹角αi;
15.步骤十、根据空间向量夹角αi的值确定弯头的角度,选用夹角αi的弯头,将选用的弯头的拐角处中心点放置在方向向量pi,p
i+1
与pi,p
i+1
的公垂向量m的中心点处或者方向向量pi,p
i+1
延伸线的交叉点处;
16.步骤十一、以弯头的拐角处中心点为中心,调整偏转角度θi,当弯头两侧的中心线的延长线与管线pi,p
i+1
的中心线或者延长线相交时,停止调整偏转角度θi,提取出管线中心线相交得到的整体中心线;
17.步骤十二、根据步骤十一得到的整体中心线,以设计管线的设计半径r0为约束条件获得管线的三维模型,以及弯头的三维模型;
18.步骤十三、以管线以及弯头的三维模型中心线的相交点为分割点,将三维模型分割,分别得到各个管线、弯头的长度以及斜切角度。
19.本发明的有益效果是:采用本方法能够对空间薄壁管线实现精准对接,选用正确的对接弯头,从而提高了焊接效率,并且能够保证空间薄壁管线的焊接质量,提升薄壁管线制造加工效率,减少焊接变形。
附图说明
20.图1是本发明的一种空间复杂薄壁碳钢管线姿态测量方法流程示意图;
21.图2为本发明的一种空间复杂薄壁碳钢工艺管线姿态测量方法示意图;
22.图3为本发明切割平面x’o’y’示意图;
23.图4为本发明管线li的测量数据拟合示意图;
24.图5为本发明管线li+1的测量数据拟合示意图;
25.图6为本发明空间管线弯头布置原理示意图。
具体实施方式
26.下面结合具体实施方式对本发明作进一步说明。
27.本发明的一种空间复杂薄壁碳钢管线姿态测量方法,包括以下步骤:
28.步骤一、将待检测的空间复杂薄壁碳钢工艺管线夹持在工作台上,将空间复杂薄壁碳钢工艺管线分段处理,标记为l1、l2…
ln,在工作台上建立基准空间直角坐标系o-xyz,以工作台的垂直方向为y轴,水平向右为x轴,水平向前为z轴;
29.步骤二、在工作台上选择空间直角坐标系o-xyz的固定点o1点为零点坐标固定机械手,用机械手携带激光测量仪,沿着管线的平行线对薄壁碳钢工艺管线进行测量;
30.步骤三、对薄壁碳钢工艺管线测量完成后,将测量得到的管线坐标值输出到计算机中,提取出第i个管线各个测量点的坐标(x
i1
,y
i1
,z
i1
)、(x
i2
,y
i2
,z
i2
)
…
(x
in
,y
in
,z
in
);
31.步骤四、过(x
i1
,y
i1
,z
i1
)、(x
i2
,y
i2
,z
i2
)、(x
i3
,y
i3
,z
i3
)三个测量点做管线的切割平面x’o’y’,将提取出第i个管线各个测量点投影到x’o’y’平面上,得到测量点的平面坐标值,(x
i1’,y
i1’)、(x
i2’,y
i2’)
…
(x
in’,y
in’),以椭圆为拟合约束条件,对步骤三得到的各个测量点的坐标值进行拟合,椭圆参数方程可以表示为:
32.f(x,y)=ax2+bxy+cy2+dx+ey+f
33.式中:{a、b、c、d、e、f}为椭圆的待求参数值;(x,y)为x’o’y’平面的椭圆坐标。
34.步骤五、将步骤四管线i的平面坐标值(x
i1’,y
i1’)、(x
i2’,y
i2’)
…
(x
in’,y
in’)带入步骤四椭圆公式中,求解管线i的数据平方和q,计算公式如下:
[0035][0036]
式中:q为管线i的数据平方和,n为数据采集数量,i为管线号。
[0037]
步骤六、根据极值原则,对管线i的数据平方和q的各参数{a、b、c、d、e、f}进行求导并令求导后的值等于零,得到各个参数的最优解,在根据椭圆的标准式求解得到管道i各个椭圆拟合时的截面中心坐标;
[0038][0039]
式中:a、b为椭圆的长短轴的值。
[0040]
步骤七、根据最小二乘法对管道i各个椭圆拟合时的截面中心坐标进行空间直线拟合,得到管线i的理想轴线的方向向量。具体步骤如下
[0041]
第一步、设空间直线li方程为:
[0042][0043]
式中:{g、m、n}为空间直线li的参数值;(xi,yi,zi)空间直线li的空间测量点坐标值;(x0,y0,z0)空间直线li的空间坐标起始值,设定为(1,1,1)。
[0044]
第二步、根据最小二乘法得到空间直线li参数方程,公式如下:
[0045][0046]
式中:(xi,yi,zi)为空间直线li第i个测量点坐标值;n为测量点个数;{g、m、n}为空间直线li的参数值。
[0047]
第三步、根据极值原理对参数{g、m、n}求导,并并令求导后的值等于零,得到参数{g、m、n}的值,得到管道i的空间直线方程li方向向量pi。
[0048]
步骤八、分别做管线l
i+1
、l
i+2
的切割面x’o’z’、y’o’z’,重复步骤三至步骤七,得到所有管线的理想轴线的方向向量p1、p2…
pn;
[0049]
步骤九、根据相邻管线的方向向量pi(ai,bi,ci),p
i+1
(a
i+1
,b
i+1
,c
i+1
)求得所有相邻管线的空间向量夹角αi,根据计算公式如下:
[0050][0051]
式中:αi为相邻向量的夹角;(ai,bi,ci)为管线i的方向向量;(a
i+1
,b
i+1
,c
i+1
)为管线i+1的方向向量。
[0052]
步骤十、根据空间向量夹角αi的值确定弯头的角度,选用夹角αi的弯头,将选用的弯头的拐角处中心点放置在方向向量pi,p
i+1
与pi,p
i+1
的公垂向量m的中心点处或者方向向量pi,p
i+1
延伸线的交叉点处;
[0053]
步骤十一、以弯头的拐角处中心点为中心,调整偏转角度θi,当弯头两侧的中心线的延长线与管线pi,p
i+1
的中心线或者延长线相交时,停止调整偏转角度θi,提取出管线中心线相交得到的整体中心线;
[0054]
步骤十二、根据步骤十一得到的整体中心线,以设计管线的设计半径r0为约束条件获得管线的三维模型,以及弯头的三维模型;
[0055]
步骤十三、以管线以及弯头的三维模型中心线的相交点为分割点,将三维模型分割,分别得到各个管线、弯头的长度以及斜切角度。