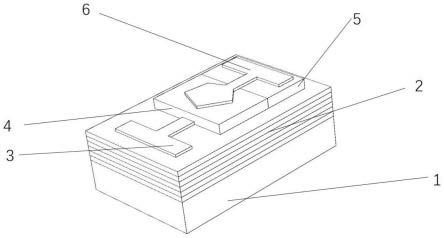
1.本实用新型涉及一种全金属结构的固态装配型微质量传感器,属于微质量传感器技术领域。
背景技术:2.传统的质量传感器大致分为两种,一种传感器基于石英晶体厚度剪切波模式工作,受限于石英晶体的工艺水平,不能把晶片做的很薄,导致其传感器灵敏度不高。另一种传感器基于声表面波工作,利用电压基底上的叉指换能器来接收待测信号并将其转换为器件谐振频率的变化量,质量灵敏度主要取决于叉指电极宽度,尽管精度高,但复杂的工艺让人望而却步,并且这种传感器的感应面积大,不适用于微小区域的质量变化。
3.受其他工艺技术以及制备难度等限制,如何制备拥有高精度、高灵敏度、适用于多种环境的质量传感器成为目前迫切需要解决的问题。
技术实现要素:4.本实用新型提供了一种全金属结构的固态装配型微质量传感器,以用于通过合理的构成及连接构建全金属结构的固态装配型微质量传感器。
5.本实用新型的技术方案是:一种全金属结构的固态装配型微质量传感器,包括衬底1、布拉格反射层2、下电极层3、压电层4、绝缘层5、上电极层6;其中,布拉格反射层2设置在衬底1上,布拉格反射层2上设置下电极层3、压电层4、绝缘层5,且下电极层3位于布拉格反射层2与压电层4之间,绝缘层5紧靠在压电层4远离下电极层3一侧并与压电层 4同高,上电极层6设置于压电层4和绝缘层5之上,上电极层6与下电极层3未在同一图层。
6.所述布拉格反射层2为全金属布拉格反射层,是由3-4个反射组构成,每个反射组由一个高声阻抗层和一个低声阻抗层构成。
7.所述下电极层3与上电极层6结构相同,均由依次连接的五边形的有效压电区域、引线区域、pad区域三部分构成。
8.所述压电层4沉积在下电极层3之上,下电极层3的有效压电区域与一部分引线区域被压电层4覆盖。
9.所述衬底1的材料为si,用于沉积布拉格反射层2的表面粗糙度小于10nm;所述布拉格反射层2中高声阻抗层的材料为w,每层高声阻抗层的厚度为530
±
2nm,低声阻抗层的材料为al,每层低声阻抗层的厚度为628
±
2nm;所述下电极层3、上电极层6的材料为al,两者五边形的有效压电区域面积为20150um2,下电极层3的厚度为150
±
2nm,上电极层6 的厚度为150-200nm;所述压电层4的材料为aln;厚度在2.18
±
0.002um;所述绝缘层5 的材料为绝缘材料,厚度与压电层4相同。
10.本实用新型的有益效果是:本实用新型采用六或八层布拉格反射层构建全金属固态装配型微质量传感器,通过改变上电极厚度模拟质量负载变化发现该传感器可工作在频域变化在 2.28ghz~2.25ghz之间的微质量检测;同时,本实用新型的结构设计整体工序简
单,绝缘层与压电层、上电极层的巧妙配合,不仅可以防止沉积时因坡度落差而出现断层或因厚度变化影响特性阻抗值使电压驻波比增加、并防止上下电极发生短接影响测量,还可以降低质量缺陷,且可以避免压电层过大产生寄生效应(寄生效应会导致传感器性能下降,严重情况甚至无法工作),对于微质量传感器领域提高传感器的精度和灵敏度是至关重要的。
附图说明
11.图1为本实用新型的结构示意图;
12.图2为本实用新型的结构透视示意图;
13.图3为本实用新型的俯视图;
14.图4为有效谐振区域展示示意图;
15.图5为本实用新型的剖视图;
16.图6为4层布拉格反射层层数能量泄露谱图;
17.图7为6层布拉格反射层层数能量泄露谱图;
18.图8为8层布拉格反射层层数能量泄露谱图;
19.图9为10层布拉格反射层层数能量泄露谱图;
20.图10为上电极层的掩模板设计示意图;
21.图11为绝缘层的掩模板设计示意图;
22.图12为压电层的掩模板设计示意图;
23.图13为下电极层的掩模板设计示意图;
24.图14为光刻对准标记分布及对准示意图;
25.图15为本实用新型制备流程图;
26.图16为通过有限元仿真计算的阻抗频率响应曲线图;
27.图17为谐振频率随质量(上电极厚度)变化曲线图;
28.图中各标号为:1-衬底,2-布拉格反射层,3-下电极层,4-压电层,5-绝缘层,6-上电极层,7-三寸掩模版,8-下电极层对准标记,9-压电层光刻对准标记,10-下电极+压电层对准标记,11-绝缘层光刻对准标记,12-下电极+压电层+绝缘层对准标记,13-上电极层光刻对准标记,14-下电极+压电层+绝缘层+上电极层对准标记。
具体实施方式
29.下面结合附图和实施例,对实用新型做进一步的说明,但本实用新型的内容并不限于所述范围。
30.实施例1:如图1-17所示,一种全金属结构的固态装配型微质量传感器,包括衬底1、布拉格反射层2、下电极层3、压电层4、绝缘层5、上电极层6;其中,布拉格反射层2设置在衬底1上,布拉格反射层2上设置下电极层3、压电层4、绝缘层5,且下电极层3位于布拉格反射层2与压电层4之间,绝缘层5紧靠在压电层4远离下电极层3一侧并与压电层 4同高,上电极层6设置于压电层4和绝缘层5之上,上电极层6与下电极层3未在同一图层。
31.可选地,所述布拉格反射层2为全金属布拉格反射层,是由3-4个反射组构成,每个反射组由一个高声阻抗层和一个低声阻抗层构成。
32.可选地,所述下电极层3由依次连接的五边形的有效压电区域、引线区域、pad区域三部分构成;其中,引线区域、pad区域呈t形;下电极层的有效压电区域大小、形状与上电极相同且位置上呈上下对应(上下电极的中心在一条垂直线上附图3),下电极层的pad区域大小、形状与上电极层一致,下电极层的引线区域与上电极的引线区域宽度相同、上电极引线区域长度大于下电极层的引线区域长度。
33.可选地,所述压电层4沉积在下电极层3之上,下电极层3的有效压电区域与一部分引线区域被压电层4覆盖。
34.可选地,所述衬底1的材料为si,用于沉积布拉格反射层2的表面粗糙度小于10nm;所述布拉格反射层2中高声阻抗层的材料为w,每层高声阻抗层的厚度为530
±
2nm,低声阻抗层的材料为al,每层低声阻抗层的厚度为628
±
2nm;所述下电极层3、上电极层6的材料为al,两者五边形的有效压电区域面积为20150um2,下电极层3的厚度为150
±
2nm,上电极层6的厚度为150-200nm;所述压电层4的材料为aln;厚度在2.18
±
0.002um;所述绝缘层5的材料为绝缘材料,厚度与压电层4相同。可选地,所述压电层4是一个长300um,宽200um,厚度在2.18
±
0.002um的矩形,为微质量传感器的核心层;绝缘层5是一个长 300um,宽150um的矩形。
35.具体而言,压电层4沉积在下电极层3之上,下电极层的有效压电区域与一部分引线被压电层4覆盖,绝缘层5紧靠在压电层4远离下电极层3一侧设计,上电极层6设置于绝缘层5、压电层4上,上下电极层与压电层4的重叠区域配合形成谐振区(即传感器的工作区);该结构采用图形化的设计能够有效减少寄生效应提高测量精度和灵敏度,在一定程度上也减小了工艺的复杂程度;可以防止沉积时因坡度落差而出现断层或因厚度变化影响特性阻抗值使电压驻波比(vswr)增加、防止上下电极发生短接影响测量,且可以降低质量缺陷(比如,可以避免上电极层在压电层那块直接断开造成的结构缺陷),还可以避免压电层过大导致横波被激发的概率增加(即可以降低横波被激发的概率,从而减少寄生效应,提升传感器性能)。本实用新型的固态装配型微质量传感器,可以使用1mm宽距的gs型双头射频探针来测量质量变化带来微小电信号的变化,大宽距的测量能够避免测量时影响有效谐振区域的正常工作。
36.对于一种全金属结构的固态装配型微质量传感器的制备步骤,包括:在衬底1上沉积全金属布拉格反射层2;在布拉格反射层2上沉积下电极层3;在下电极层3和布拉格反射层2 上沉积压电层4;在紧靠压电层4远离下电极层3一侧沉积绝缘层5;在压电层4和绝缘层5 上沉积上电极层6。
37.可选地,所述衬底1制备为:衬底1选用单面抛光的n型(100)单晶硅(也可以采用单面抛光的p型(110)),电阻率为1~10ω
·
cm,n型单晶硅抛光面的表面粗糙度小于10nm(优选地,取值为6≤粗糙度<10,避免后期加工时材料缺陷对传感器性能造成影响);使用标准rca 清洗n型单晶硅,清洗掉硅片表面的杂质,避免杂质影响传感器性能;使用氮气吹干清洗后 n型单晶硅表面水分后,在烘烤室中从室温加热至100℃烘烤使n型单晶硅完全干燥;其中,烘烤分为两个阶段:升温阶段、恒温阶段;升温阶段与恒温阶段所用时间比值为5:1,升温阶段指从室温升至100℃的阶段,恒温阶段指保持100℃的阶段;烘烤共计用时20min-30min。 (比如,烘烤用时30min,则升温阶段控制在25min,即从室温至100℃用时25min,剩下的 5min在100℃下烘干;烘烤用时也可以是20min、25min等),通过逐步升温再恒温,可以
避免温度升高过快导致材料应力增加产生肉眼不可见的结构损伤。
38.可选地,全金属布拉格反射层2制备为:使用物理磁控溅射系统(磁控溅射系统的腔室真空背景为≤5
×
10-4
pa,靶基距为6cm,本实用新型中所有磁控溅射基本参数设置均为此参数)在干燥后的单晶硅抛光面上先沉积一层厚度为530
±
2nm的高声阻抗薄膜w,选用纯度为 99.95%的纯w靶材,设置射频功率为60w,溅射压强为1.2pa,基底温度设置室温水冷,氩气流量为20sccm。沉积完毕后,再在高声阻抗薄膜w表面上沉积厚度为628
±
2nm的低声阻抗薄膜al,选用纯度为99.99%的纯al靶材,设置射频功率为300w,溅射压强为0.5pa,基底温度设置室温水冷,氩气流量为20sccm;重复以上步骤制备反射组为3组的布拉格反射层(通过上述方式获得的布拉格反射层,确保在降低工艺难度的情况下,依旧拥有良好的反射能力)。可选地,所述反射组为3-4个。具体而言,所述的布拉格反射层由al(低声阻抗) 和w(高声阻抗)两种金属构成的全金属结构,反射组为3-4组,采用λ/2模式固态装配型质量传感器,由此布拉格反射层2靠近下电极层一层为低阻抗层,厚度为每层628
±
2nm,靠近衬底的为高声阻抗层,厚度为每层530
±
2nm。即图1、5中所示为3组,从上到下的结构为低-高-低-高-低-高。
39.给出布拉格反射层数的选择过程:
40.布拉格反射层数越多对能量的封闭性越好,但是层数增多会增加工艺的复杂性和器件成本,选择适当的布拉格反射层数不仅可以较少能量泄露,还便于器件的加工制作。下面将对布拉格反射层数为:4、6、8、10进行仿真分析,获得不同布拉格反射层层数能量泄露谱如图6-9所示。谐振时能量的峰峰值之比作为能量效率η,,η越小,能量封闭的越好。取泄露谱中横向最大峰值和最小峰值,计算能量效率如表1所示。
41.比较发现,4层与6层能量效率差值为:η
4-η6=2.07%,6层与8层能量效率差值为:η
6-η8=2.83%,8层与10层能量效率差值为:η
8-η
10
=0.74%。由于器件布拉格反射层数不同,起振时的波长不同,所以对比si中能量大小绝对值是没有意义的,应该用该器件si中峰值能量绝对值比上薄膜中峰值能量的绝对值,才能真实反映能量效率。能量效率越小,能量封闭性越好。表中可知,当层数为6层时,能量效率已经达到3.78%,小于5%,随着布拉格反射层不断增加所带来的效益呈断崖式下跌。从工艺成本和复杂度来看6层在降低工艺难度的情况下仍能保证能量泄露尽可能小,所以本技术选择6层是作为综合性能最佳器件,即反射组数为3。
42.表1能量效率的计算
[0043][0044]
可选地,所述下电极层3制备为:先对制备好布拉格反射层2上表面使用hmds液进行增粘处理,在整个布拉格反射层上表面均匀的旋涂一层厚度为1um的光刻胶az600,设置
匀胶机转速为4000rpm,匀胶40s;匀胶结束后进行前烘处理,设置热板温度100℃烘烤光刻胶,烘烤时间60s,使光刻胶蒸发失去流动,去除胶膜中残余的溶剂,消除胶膜的机械应力,增强胶层的粘附性,提高和稳定胶层的感光敏感度,以便后续进行曝光处理;在对应的下电极掩模版(附图13)的图案下进行曝光,使用紫外线进行曝光,能量为g线,时间为2s;使用显影液az300mif显影60s得到需要的下电极图案;在磁控溅射之前,通过电子显微镜观察显影后的图形是否存在缺陷:若存在缺陷(比如存在显影不足或显影过度等缺陷),清洗样板上的光刻胶,重复上述步骤,直至合格。显影合格后进行坚膜,使用去离子水清洗30s,将清洗后的样片放入烘烤室烘烤,烘烤时间120s,烘烤温度为100℃;烘烤结束后,使用物理磁控溅射系统沉积厚度为150
±
2nm下电极薄膜,设置磁控溅射系统的射频功率为300w,溅射压强为0.5pa,靶材纯度为99.99%的纯al,氩气流量为20sccm,基底温度设置室温水冷;在正式溅射之前先预溅射,保证腔体纯净,溅射完成后使用az剥离液剥离光刻胶形成图形化下电极层3。
[0045]
所述五边形的有效压电区域面积为20150um2(即上下电极的重叠区域面积,如图4所示;五边形的有效压电区域是电极的核心部分。pad区域的设计是为了让探针尖端更有效的接触电极,其长为180um,宽为90um;引线区域的设计是在不影响有效压电区域的前提下更好的进行测量并加长测量长度契合射频探针。当纵波在压电层被激发时,也会激发横波,横波在压电层来回震荡被上下电极捕捉到,形成寄生谐振,若传感器的边缘上的任意两个边界所产生的横波谐振频率相同,那寄生会被明显增强,使用五边形可以明显减少寄生的产生。
[0046]
可选地,所述压电层4制备为;图形化过程与下电极层3制备过程基本相同,不同之处在于:使用磁控溅射系统射频功率设置在400w,氩气与氮气的流量比为3:1(具体可以为:氩气流量为48sccm,氮气流量设置在16sccm),溅射压强为0.23pa,基底为100℃,利用纯度99.99%的纯al靶材和氮气在100℃高温下进行反应制备厚度为2.18um的压电层薄膜,并进行图形化(压电层掩模版示意图见附图12),形成图形化压电层4,aln是传感器的核心。压电层厚度为2.18
±
0.002um,所需光刻胶的厚度在2.2um以上,一次旋涂无法达到所需厚度,需要进行二次旋涂,在二次旋涂中不进行前烘操作;压电层在曝光之前进行光刻对准。光刻胶旋涂的具体操作如下:先滴一滴光刻胶,设置匀胶转速为3000rpm,时间设置40s,成胶厚度为1.3um,在一次匀胶完成后不进行烘干操作,再在上面滴一滴光刻胶,依旧设置匀胶转速为3000rpm,时间设置40s,这样就可以得到厚度>2.2um的胶层(光刻胶的厚度与转速是有直接关系,而时间设置是为了获得厚度均匀的光刻胶,一般设置时间均为40s,是个默认时间),两次滴胶连续进行,虽然厚度小于两个单次滴胶的厚度之和,但是可以在不影响光刻胶的性质的基础上使得厚度仍然大于2.2um。
[0047]
可选地,所述绝缘层5制备为;图形化过程与压电层4制备过程基本相同,不同之在于:采用磁控溅射系统射频功率设置在100w,溅射压强为1.2pa,氩气与氧气的流量比为5:3(具体可以为:氩气流量50sccm,氧气为30sccm),基底温度设置为室温水冷,使用纯度为99.9%的纯si靶材,在氩气和氧气混合给气体环境下制备氧化硅薄膜并进行图形化,形成绝缘层5 (绝缘层掩模版示意图见附图11)。
[0048]
可选地,所述上电极层6制备为:上电极的制备过程是固态装配型微质量传感器制备的最后阶段,同时,考虑到微质量传感器的质量灵敏度极高,拟改变上电极厚度来模拟负
载质量的变化,选择密度较小的al作为上电极材料;由于上电极的制备是在电极图形化下电极层、压电层、绝缘层制备完成后进行的。图形化过程与下电极层3制备过程基本相同,不同之在于:设置磁控溅射系统的射频功率为300w,溅射压强为0.5pa,氩气流量为20sccm,基底温度设置室温水冷,靶材纯度为99.99%的al沉积厚度为150-200nm上电极并图形化处理。 (上电极掩模版示意图见附图10)。上电极层要在曝光之前进行光刻对准,通过下述介绍对准的方式进行,可以有效地确保上下电极的中心在同一位置。
[0049]
所述下电极层、上电极层选用al靶材,本技术中对mo、al、w、au、pt这几种电极材料进行仿真。在有限元仿真中发现,相同厚度下不同材料的谐振频率由低到高分别为pt、au、 mo、al。从表2可知,本实用新型选用的al具备高品质因子和高阻抗特性的优良特性外,还具有密度低的优点,相同体积下al的质量变化最小,可以通过改变厚度来模拟质量负载的变化。
[0050]
表2谐振点和品质因子
[0051][0052]
此外,压电层、绝缘层、上电极层对准的过程如下,如图14所示:
[0053]
在压电层制备过程中,曝光之前需要通过显微镜观察电极图形,调整压电层掩模版位置使压电层掩模版上的压电层光刻对准标记9与下电极层对准标记8对准后进行磁控溅射;在布拉格反射层上形成下电极+压电层对准标记10;
[0054]
在绝缘层制备过程中,曝光之前需要通过显微镜观察电极图形,调整绝缘层掩模版位置使绝缘层掩模版上的绝缘层光刻对准标记11与下电极+压电层对准标记10对准后进行磁控溅射;在布拉格反射层上形成下电极+压电层+绝缘层对准标记12;
[0055]
在上电极层制备过程中,曝光之前需要通过显微镜观察电极图形,调整上电极层掩模版位置使上电极层光刻对准标记13与下电极+压电层+绝缘层对准标记12对准后进行磁控溅射;在布拉格反射层上形成下电极+压电层+绝缘层+上电极层对准标记14。
[0056]
所述压电层光刻对准标记9、绝缘层光刻对准标记11、上电极层光刻对准标记13采用镂空结构(如镂空十字结构);压电层光刻对准标记9的镂空形状、大小与下电极层对准标记8 形状、大小相同,两者适配;绝缘层光刻对准标记11的镂空形状、大小与压电层光刻对准标记9形状、大小相同,两者适配;上电极层光刻对准标记13的镂空形状、大小与绝缘层光刻对准标记11形状、大小相同,两者适配。具体而言,下电极层3、压电层4、绝缘层5、上电极层6掩模版均设有“+”字对准标记便于套刻对准,如三寸掩模版7中所示,把掩模版划分成四
个区域的中线中附有16个光刻对准标记,每个掩膜板中也设计着“l”型的方向对准标记15,位于掩膜版正上方,避免无法识别方向;图下电极层对准标记8、压电层光刻对准标记9、绝缘层光刻对准标记11、上电极层光刻对准标记13形状相同,均可以采用十字结构,压电层光刻对准标记9、绝缘层光刻对准标记11、上电极层光刻对准标记13采用镂空十字结构;压电层光刻对准标记9的镂空形状、大小与下电极层对准标记8形状、大小相同,两者适配,形如下电极+压电层对准标记10;其它同理。
[0057]
采用上述的对准方式参与压电层、绝缘层、上电极层的制备过程,能够有效保证层与层之间的误差在允许范围内,减少因为工艺误差等因素降低传感器性能。
[0058]
为验证本技术的微质量传感器的可行性,通过有限元仿真分析软件,计算实例的谐振特性曲线其串联谐振频率为2.28ghz,并联谐振频率为2.33ghz(图16),通过改变上电极厚度发现该传感器可工作在频域变化在2.28ghz~2.25ghz之间的微质量检测(此处指串联谐振点的频率变化范围,上电极的厚度变化范围为150nm-200nm,厚度越大,谐振频率向左偏移(变小),如表3所示)。仿真得出,al厚度与频率的变化呈线性关系,也说明了质量负载与频率的变化呈线性关系,本实用新型的传感器是可行且有效的,本实用新型的仿真实验是基于三维的多物理场仿真,更加贴合实际;从图17中可知上电极厚度每增加10nm,上电极质量负载变化0.544ng,谐振频率向左偏移7mhz(图17中,横坐标取值0表示为初始的上电极层厚度,即150nm,按照步长10进行递增);根据薛伯瑞方程可计算得出该微质量传感器的质量灵敏度为s=2.5926
×
103hz
·
cm2/ng,即质量改变1ng,单位面积(cm2)下谐振频率下降2.5926
ꢀ×
103hz。
[0059]
表3上电极厚度对应的谐振频率表
[0060][0061]
上面结合附图对本实用新型的具体实施方式作了详细说明,但是本实用新型并不限于上述实施方式,在本领域普通技术人员所具备的知识范围内,还可以在不脱离本实用新型宗旨的前提下做出各种变化。