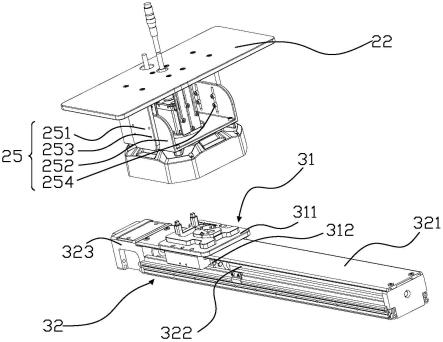
1.本实用新型涉及零部件尺寸检测领域,尤其是一种零部件尺寸测量系统。
背景技术:2.随着技术的发展,设备对零部件尺寸的精度要求越来越高,在生产零部件时,均需要对零部件的尺寸进行测量。进一步地,越来越多的客户要求对产品的尺寸进行联机联控,以对产品进行准确的追溯。在现有技术中,一般需要人工来对零部件的尺寸进行测量,然后对测量结果进行记录,这一方面工作效率较低,另一方面也很难满足用户联机联控的需求。
技术实现要素:3.本实用新型提供了一种零部件尺寸测量系统,该零部件尺寸测量系统能够较为容易地对零部件的尺寸进行测量,且能够实时对零部件尺寸进行联机联控。
4.本实用新型提供了一种零部件尺寸测量系统,包括柜体、ccd视觉检测组件、零部件承载组件及控制主机,所述ccd视觉检测组件及所述零部件承载组件均设置于所述柜体内,所述ccd视觉检测组件设置于所述零部件承载组件的上方,所述零部件承载组件包括承载零部件的零部件固定座及零部件承载座,所述零部件固定座可滑动地设置于所述零部件承载座上,所述ccd视觉检测组件与所述控制主机电性相连,所述控制主机包括控制模块及存储模块,所述ccd视觉检测组件用于对设置于所述零部件承载组件上的零部件的尺寸进行检测,并把检测信号传递至所述控制模块,所述控制模块根据该检测信号计算零部件的尺寸,所述存储模块用于对所述零部件的尺寸信息进行存储。
5.进一步的,所述ccd视觉检测组件包括ccd固定架、ccd承托板、ccd视觉检测镜头及ccd打光灯,所述ccd固定架固定于所述柜体上,所述ccd承托板固定于所述ccd固定架上,所述ccd视觉检测镜头设置于所述ccd承托板上,所述ccd打光灯有多个,多个所述ccd打光灯环设于所述ccd视觉检测镜头的周边。
6.进一步的,所述ccd固定架上设置有ccd调整架,所述ccd调整架包括第一板体及第二板体,所述第一板体与所述ccd固定架相连,所述ccd视觉检测镜头及所述ccd打光灯与所述第二板体相连,在所述第一板体及所述第二板体上沿竖直方向均间隔设置有多个连接孔,连接件穿过所述第一板体及所述第二板体上的连接孔以使所述第一板体与所述第二板体相连,通过调整所述连接件的结合位置,以调整所述ccd视觉检测镜头及所述ccd打光灯的高度。
7.进一步的,所述零部件承载座包括滑轨、第一传动部件及动力源,所述零部件固定座包括固定板及第二传动部件,所述第一传动部件与所述动力源相连,所述动力源与所述滑轨相互固定,所述固定板与所述第二传动部件相互固定,所述固定板可滑动地设置于所述滑轨上,所述第一传动部件与所述第二传动部件动力相连,所述动力源通过所述第一传动部件及所述第二传动部件带动所述固定板沿所述滑轨运动。
8.进一步的,:所述动力源为电机,所述第一传动部件及所述第二传动部件的组合为
蜗轮蜗杆或丝杠螺母。
9.进一步的,所述滑轨呈板状,在所述固定板与所述第二传动部件之间形成有透过孔,板状的所述滑轨穿过所述透过孔,以使所述固定板可滑动地与所述滑轨相连。
10.进一步的,在所述固定板上设置有用于对零部件进行夹持的固定螺栓。
11.进一步地,所述固定板上设置有真空吸板,在所述真空吸板上设置有用于与抽真空装置相连的吸管接头。
12.进一步地,所述柜体上设置有对零部件的尺寸参数进行显示的显示屏,对所述零部件承载组件的运动进行控制的控制按钮,以及对所述零部件尺寸测量系统的工作状态进行显示的指示灯。
13.进一步地,所述控制主机还包括识别码生成模块,所述识别码生成模块与所述存储模块电性相连,所述识别码生成模块用于根据存储模块存储的零部件的尺寸信息生成含有零部件尺寸信息的识别码。
14.综上所述,在本实用新型中,通过ccd视觉检测组件及零部件承载组件的设置,在进行测量时,可以先将零部件设置于零部件固定座上,然后将零部件固定座在零部件承载座上进行移动,以使零部件逐渐滑过ccd视觉检测组件的下方,利用ccd视觉以对零部件的尺寸进行检测,在检测后,控制模块能够根据检测信号计算出零部件的尺寸,并通过存储模块进行存储。通过ccd视觉检测模块进行零部件尺寸的检测,以及进行存储,这能够快速地进行零部件尺寸的检测,并通过对尺寸进行实时的存储,能够实时对零部件尺寸进行联机联控。
15.上述说明仅是本实用新型技术方案的概述,为了能够更清楚了解本实用新型的技术手段,而可依照说明书的内容予以实施,并且为了让本实用新型的上述和其他目的、特征和优点能够更明显易懂,以下特举较佳实施例,并配合附图,详细说明如下。
附图说明
16.图1所示为本实用新型第一实施例提供的零部件尺寸测量系统的结构示意图。
17.图2所示为ccd视觉检测组件与零部件承载组件在箱体内的结构示意图。
18.图3所示为ccd视觉检测组件与零部件承载组件的结构示意图。
19.图4所示为零部件尺寸测量系统的系统框图。
20.图5所示为ccd视觉检测组件的结构示意图。
21.图6所示为零部件承载组件的结构示意图。
22.图7所示为本实用新型第一实施例中零部件固定座的结构示意图。
23.图8所示为本实用新型第二实施例中零部件固定座中固定板的结构示意图。
24.附图标记:10.柜体、20.ccd视觉检测组件、21.ccd固定架、22.ccd承托板、23.ccd视觉检测镜头、24.ccd打光灯、25.ccd调整架、251.第一板体、252.第二板体、253.连接孔、254.连接件、30.零部件承载组件、31.零部件固定座、311、固定板、312.第二传动部件、313.透过孔、315.固定螺栓、316.真空吸板、317.吸管接头、32零部件承载座、321.滑轨、322.第一传动部件、323.动力源、40.控制主机、41.控制模块、42.存储模块、43.识别码生成模块、51.显示屏、52.控制按钮、53指示灯。
具体实施方式
25.为更进一步阐述本实用新型为达成预定实用新型目的所采取的技术手段及功效,以下结合附图及较佳实施例,对本实用新型进行详细说明如下。
26.本实用新型提供了一种零部件尺寸测量系统,该零部件尺寸测量系统能够较为容易地对零部件的尺寸进行测量,且能够实时对零部件尺寸进行联机联控。
27.图1所示为本实用新型第一实施例提供的零部件尺寸测量系统的结构示意图,图2所示为ccd视觉检测组件与零部件承载组件在箱体内的结构示意图,图3所示为ccd视觉检测组件与零部件承载组件的结构示意图,图4所示为零部件尺寸测量系统的系统框图,图5所示为ccd视觉检测组件的结构示意图,图6所示为零部件承载组件的结构示意图,图7所示为本实用新型第一实施例中零部件固定座的结构示意图。如图1至图7所示,本实用新型提供的零部件尺寸测量系统包括柜体10、ccd(charge-coupled device电荷耦合元件)视觉检测组件20、零部件承载组件30及控制主机40,ccd视觉检测组件20及零部件承载组件30均设置于柜体10内,零部件承载组件30包括承载零部件的零部件固定座31及零部件承载座32,ccd视觉检测组件20设置于零部件承载组件30的上方,零部件固定座31可滑动地设置于零部件承载座32上,ccd视觉检测组件20与控制主机40电性相连,控制主机40包括控制模块41及存储模块42,ccd视觉检测组件20用于对固定于零部件承载组件30上的零部件的尺寸进行检测,并把检测信号传递至控制模块41,控制模块41用于根据检测信号计算零部件的尺寸,存储模块42用于对零部件的尺寸进行存储。
28.在本实施例中,通过ccd视觉检测组件20及零部件承载组件30的设置,在进行测量时,可以先将零部件设置于零部件固定座31上,然后将零部件固定座31在零部件承载座32上进行移动,以使零部件逐渐穿过ccd视觉检测组件20的下方,利用ccd视觉以对零部件的尺寸进行检测,在检测后,控制模块41能够根据检测信号计算出零部件的尺寸,并通过存储模块42进行存储。通过ccd视觉检测组件20进行零部件尺寸的检测,以及通过存储模块42进行存储,这能够快速地进行零部件尺寸的检测,并对尺寸进行实时的存储,能够实时对零部件尺寸进行联机联控。
29.需要说明的是,ccd视觉检测组件如何对零部件的尺寸进行检测,控制模块41如何对检测的信号进行分析,以及存储模块如何对数据进行存储其均可以参照现有技术,在此不再赘述。
30.进一步地,请继续参照图3、图5及图6,在图5及图6中省略了ccd固定架21,ccd视觉检测组件20包括ccd固定架21(见图2)、ccd承托板22、ccd视觉检测镜头23及ccd打光灯24。ccd固定架21固定于柜体10上,ccd承托板22固定于ccd固定架21上,ccd视觉检测镜头23设置于ccd承托板22上,ccd打光灯24有多个,多个ccd打光灯24环设于ccd视觉检测镜头23的周边。
31.进一步地,在ccd固定架21上还设置有ccd调整架25,ccd调整架25包括第一板体251及第二板体252,第一板体251与ccd固定架21相连,ccd视觉检测镜头23及ccd打光灯24与第二板体252相连,在第一板体251及第二板体252上沿竖直方向均间隔设置有多个连接孔253,连接件254穿过第一板体251及第二板体252上的连接孔253以使第一板体251与第二板体252相互固定。通过调整连接件254的结合位置,以调整ccd视觉检测镜头23及ccd打光灯24的高度。
32.请继续参照图2、图3、图6及图7,在本实施例中,零部件承载座32包括滑轨321、第一传动部件322及动力源323,零部件固定座31包括固定板311及第二传动部件312,第一传动部件322与动力源323相连,动力源323与滑轨321相互固定,固定板311与第二传动部件312相互固定,固定板311可滑动地设置于滑轨321上,第一传动部件322与第二传动部件312动力相连,动力源323通过第一传动部件322及第二传动部件312带动固定板311沿滑轨321运动。
33.在本实施例中,动力源323可以为电机,第一传动部件322及第二传动部件312的组合可以为涡轮蜗杆、丝杠螺母等。
34.滑轨321呈板状,在固定板311与第二传动部件312之间形成有透过孔313,板状的滑轨321穿过透过孔313,以使固定板311可滑动地与滑轨321相连,通过板状滑轨321与透过孔313的设置,能够保证零部件固定座31运动的平稳。
35.进一步地,在本实施例中,固定板311上设置有固定螺栓315,以对零部件进行夹持,该固定板311适应于具有一定高度的零部件的固定。
36.进一步地,在柜体10上还设置有对零部件的尺寸参数进行显示的显示屏51、对零部件承载组件30的运动进行控制的控制按钮52,以及对零部件尺寸测量系统的工作状态进行显示的指示灯53。
37.进一步地,控制主机40还包括识别码生成模块43,识别码生成模块43与存储模块42电性相连,识别码生成模块43用于根据存储模块42存储的零部件的尺寸信息生成含有零部件尺寸信息的识别码,如条形码,二维码等,以便于零部件的追溯。
38.图8所示为本实用新型第二实施例中零部件固定座中固定板的结构示意图。本实用新型第二实施例提供的零部件尺寸测量系统与第一实施例基本相同,其不同之处在于,在本实施例中,固定板311上设置有真空吸板316,在真空吸板下侧面设置有用于与抽真空装置相连的吸管接头317,通过吸管接头317与抽真空装置相连,并在真空吸板316上产生负压,以对片状的零部件进行吸附固定。
39.综上所述,在本实用新型中,通过ccd视觉检测组件20及零部件承载组件30的设置,在进行测量时,可以先将零部件设置于零部件固定座31上,然后将零部件固定座31在零部件承载座32上进行移动,以使零部件逐渐滑过ccd视觉检测组件20的下方,利用ccd视觉以对零部件的尺寸进行检测,在检测后,控制模块41能够根据检测信号计算出零部件的尺寸,并通过存储模块42进行存储。通过ccd视觉检测模块进行零部件尺寸的检测,以及进行存储,这能够快速地进行零部件尺寸的检测,并通过对尺寸进行实时的存储,能够实时对零部件尺寸进行联机联控。
40.以上所述,仅是本实用新型的较佳实施例而已,并非对本实用新型作任何形式上的限制,虽然本实用新型已以较佳实施例揭露如上,然而并非用以限定本实用新型,任何熟悉本专业的技术人不脱离本实用新型技术方案范围内,当可利用上述揭示的技术内容作出些许更动或修饰为等同变化的等效实施例,但凡是未脱离本实用新型技术方案内容,依据本实用新型的技术实质对以上实施例所作的任何简单修改、等同变化与修饰,均仍属于本实用新型技术方案的范围内。