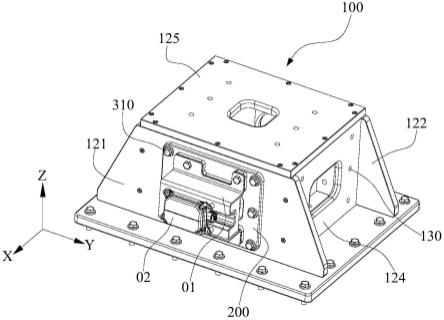
1.本实用新型涉及汽车零部件测试技术领域,特别是涉及一种车载雷达振动测试工装。
背景技术:2.自动驾驶辅助系统在汽车上的应用越来越广泛,在自动驾驶辅助系统中,毫米波雷达为重要的组成部分之一,其精确性至关重要。
3.在毫米波雷达生产完成后,需要模拟整车的振动环境对其进行振动试验,以使其满足应用需求。其他车载雷达也有相同的需求。
4.一般,雷达通过转接支架安装在车身上。在对雷达进行振动测试时,将雷达安装在转接支架上,转接支架再通过工装安装在振动试验台上,以进行振动测试;但是车型不同,雷达的安装环境不同,即对应的转接支架不同,这就需要设计不同的工装以对应不同的转接支架,成本高,也增加了试验的繁琐程度。
技术实现要素:5.本实用新型的目的是提供一种车载雷达测试工装,通过对测试工装的结构优化,使得该测试工装可以与多种不同类型的转接支架相匹配,无需对工装本体进行更换,测试过程相对简化,且降低了测试成本。
6.为解决上述技术问题,本实用新型提供一种车载雷达振动测试工装,包括:
7.工装本体,其具有至少三个安装面部,其中,三个所述安装面部的法线方向相互垂直;每个所述安装面部均具有固定结构;
8.固定部,用于安装转接支架,所述转接支架安装有待测雷达,所述固定部具有安装结构,所述安装结构能够与每个所述安装面部的所述固定结构固定连接。
9.本实施新型提供的车载雷达振动测试工装,包括工装本体和固定部,在工装本体设有至少三个安装面部,三个安装面部的法线方向相互垂直,每个安装面部都设有固定结构,固定部具有安装结构,固定部的安装结构能够与每个安装面部的固定结构固定连接,这样,安装有待测雷达的固定部可根据试验需求安装在三个安装面部中的任一个上,方便不同振动方向的测试;其中,待测雷达通过转接支架安装在固定部上,车型不同,转接支架的类型也不同,但不管转接支架的类型如何,安装转接支架的固定部都能通过其安装结构固定在任一安装面部上,实际测试时,只需根据转接支架的类型变换固定部即可,无需对应设计工装本体,也无需更换工装本体,测试过程相对简单,同时也提高了测试工装的通用性,节约了成本。
10.如上所述的车载雷达振动测试工装,所述固定结构包括多个固定孔,各所述安装面部的至少部分所述固定孔的尺寸以及排布方式均相同;
11.所述安装结构包括多个安装孔,所述安装结构的至少部分所述安装孔与所述固定结构的至少部分所述固定孔一一匹配;
12.所述固定部通过穿过相互匹配的所述固定孔和所述安装孔的紧固件与所述安装面部固定。
13.如上所述的车载雷达振动测试工装,所述工装本体包括底座和至少三个安装板,所述安装板与所述底座相对固定,每个所述安装板具有一个所述安装面部。
14.如上所述的车载雷达振动测试工装,所述工装本体包括五个所述安装板,五个所述安装板和所述底座围合形成箱型结构,各所述安装板朝向外侧的板面形成所述安装面部;
15.其中,第一安装板和第二安装板相对,第三安装板和第四安装板相对,所述第一安装板的两端分别与所述第三安装板和所述第四安装板固接,所述第二安装板的两端分别与所述第三安装板和所述第四安装板固接,第五安装板与所述第一安装板、所述第二安装板、所述第三安装板和所述第四安装板的顶壁固接。
16.如上所述的车载雷达振动测试工装,所述安装板与所述底座通过可拆卸的连接方式相对固定。
17.如上所述的车载雷达振动测试工装,所述安装板具有减重孔。
18.如上所述的车载雷达振动测试工装,所述底座为铝合金底座,和/或,所述安装板为铝合金板。
19.如上所述的车载雷达振动测试工装,所述底座的周边具有多个用于与振动试验台可拆卸连接的连接孔。
20.如上所述的车载雷达振动测试工装,所述工装本体的固有频率大于设定频率。
21.如上所述的车载雷达振动测试工装,所述设定频率为900~1100hz。
附图说明
22.图1为本实用新型提供一种实施方式中车载雷达振动测试工装的工装本体的结构示意图;
23.图2为图1所示工装本体的俯视图;
24.图3为图1中工装本体安装有一个待测雷达的结构示意图;
25.图4为具体实施方式中待测雷达、转接支架和固定部组装后的结构示意图。
26.附图标记说明:
27.转接支架01,待测雷达02;
28.工装本体100,底座110,第一安装板121,第二安装板122,第三安装板123,第四安装板124,第五安装板125,固定孔130,减重孔140;
29.固定部200,安装孔210;
30.第一紧固件310,第二紧固件320。
具体实施方式
31.为了使本技术领域的人员更好地理解本实用新型方案,下面结合附图和具体实施方式对本实用新型作进一步的详细说明。
32.请参考图1至图4,图1为本实用新型提供一种实施方式中车载雷达振动测试工装的工装本体的结构示意图;图2为图1所示工装本体的俯视图;图3为图1中工装本体安装有
一个待测雷达的结构示意图;图4为具体实施方式中待测雷达、转接支架和固定部组装后的结构示意图。
33.本实施方式中,车载雷达振动测试工装包括工装本体100和固定部200,两者可拆卸连接。
34.工装本体100具有至少三个安装面部,其中,三个安装面部的法线方向相互垂直,以图示中的空间坐标系来说,三个安装面部的法线方向分别为x轴所在方向、y轴所在方向和z轴所在方向。
35.工装本体100包括底座110和至少三个与底座110相对固定的安装板,一个安装板形成有一个安装面部,各安装面部具有固定结构。
36.固定部200用于安装转接支架01,转接支架01上安装有待测雷达02,可以理解,转接支架01根据车型匹配设置;固定部200具有安装结构,固定部200的安装结构能够与每个安装面部的固定结构固定连接。
37.这样,安装有待测雷达02的固定部200可以根据试验需求安装在需要的安装面部上,以方便不同振动方向的测试,在一个工装上就可以实现三个方向的振动测试。车辆在正常行驶过程中,其振动都可分解为x轴所在方向、y轴所在方向和z轴所在方向三个方向的振动,通过前述至少三个安装面部的设置,能够较为全面地对待测雷达02进行测试。
38.因固定部200的安装结构能够与每个安装面部的固定结构相连接,所以针对不同车型测试时,只需要匹配与对应车型的转接支架01可安装的固定部200即可,无需更换工装本体100,也就是说,虽然转接支架01的类型不同,其与固定部200的连接结构也不同,但固定部200与安装面部连接的安装结构是一致的,这样就无需变更工装本体100,只需变换固定部200,可提高工装本体100的通用性,避免来回更换工装本体100导致的高成本和繁琐的测试过程。可以理解,固定部200的数量根据需要测试的车型或者说需要匹配的转接支架01来定,多个固定部200与一个工装本体100相配合。
39.综上分析,该测试工装的结构设计通用性高,测试过程相对简化,且成本相对较低。
40.本实施方式中,工装本体100设有五个安装板,为方便描述,下面将五个安装板分别称之为第一安装板121、第二安装板122、第三安装板123、第四安装板124和第五安装板125,这五个安装板与底座110围合形成箱型结构,也可理解为盒型结构。
41.其中,第一安装板121和第二安装板122相对设置,并沿x轴所在方向排布,第三安装板123和第四安装板124相对设置,并沿y轴方向排布,第一安装板121的两端分别与第三安装板123和第四安装板124固接,第二安装板122的两端分别与第三安装板123和第四安装板124固接,第五安装板125与第一安装板121、第二安装板122、第三安装板123和第四安装板124的顶壁固接。
42.上述五个安装板朝向外侧的板面均形成安装面部,这里的外侧指的是相对远离工装本体100的中心的方向,可以理解,第一安装板121的安装面部和第二安装板122的安装面部均与x轴方向垂直,第三安装板123的安装面部和第四安装板124的安装面部均与y轴方向垂直,第五安装板125的安装面部与z轴方向垂直。也就是说,本实施方式中,工装本体100具有五个安装面部。
43.这样,实际测试时,利用该工装可以一次性对五个待测雷达02进行测试,之后再变
换待测雷达02的安装位置,实现三个振动方向的测试,测试效率高。当然,也可一次仅针对一个待测雷达02在一个振动方向进行测试。
44.图3示例性地示出了只在工装本体100的第一安装板121上安装有待测雷达02的结构。
45.为方便更换待测雷达02的安装位置,固定部200与各安装板的安装面部可通过可拆卸方式连接,具体的,前述各安装面部的固定结构可包括多个固定孔,各安装面部的至少部分固定孔的尺寸以及排布方式均相同,固定部200的安装结构包括多个安装孔210,其安装结构的至少部分安装孔210与每个固定结构的至少部分固定孔一一匹配,每组相互匹配的固定孔和安装孔210可通过第一紧固件310实现固定连接。
46.图示方案中,各安装板的安装面部的固定孔的数量、尺寸以及排布方式均相同,结合图1至图3,图中示例性地示出了每个安装板上设有六个固定孔的结构,这六个固定孔排成两列,固定部200上设有与这六个固定孔一一匹配的六个安装孔210。
47.在其他实施方式中,固定孔的数目和排布方式不限于图中所示,安装孔210匹配设置。
48.这里需要说明的是,实际应用中,各安装板根据各自的应用需求可以设有不同的孔结构,图中仅示意了固定孔和安装板与其他结构连接的连接孔,以便于理解固定孔的设置。
49.在其他实施方式中,各安装板的固定孔的数量可以不同,但至少各安装板至少有部分固定孔的尺寸和位置相同,以便于固定部200能够与每个安装板都实现连接,不再一一说明。
50.在其他实施方式中,与底座110相对固定的安装板的数目不限于图中的五个,但至少需要有三个,以形成分别与x轴、y轴、z轴垂直的三个安装面部。
51.本实施方式中,各安装板与底座110通过可拆卸的连接方式相对固定,这样,方便根据需要维护安装板,也方便拆卸后应用于其他试验;具体的,相邻的两个安装板之间可通过螺钉等紧固件固定连接。
52.本实施方式中,在不影响试验的基础上,各安装板均设有减重孔140,以节约材料,减轻工装的整体重量。
53.本实施方式中,工装本体100的底座110和各安装板均可采用铝合金材质,有利于轻量化,同时,铝合金材质的表面可与空气反应,形成一层致密的氧化膜,可以防锈蚀。
54.本实施方式中,在工装本体100的底座110的周边设有多个连接孔,以方便通过第二紧固件320将工装本体100可拆卸地固定在振动试验台上。
55.具体设置时,该振动测试工装的固定频率大于设定频率设置,设定频率可以在900~1100hz范围内,以避免在进行振动试验时,工装因共振而影响对待测雷达02的测试结果,有利于提高测试精确度。
56.实际应用中,设定频率的范围具体可根据振动试验的相关要求来设定,只要能够避免工装共振即可。
57.以上对本实用新型所提供的一种车载雷达振动测试工装进行了详细介绍。本文中应用了具体个例对本实用新型的原理及实施方式进行了阐述,以上实施例的说明只是用于帮助理解本实用新型的方法及其核心思想。应当指出,对于本技术领域的普通技术人员来
说,在不脱离本实用新型原理的前提下,还可以对本实用新型进行若干改进和修饰,这些改进和修饰也落入本实用新型权利要求的保护范围内。