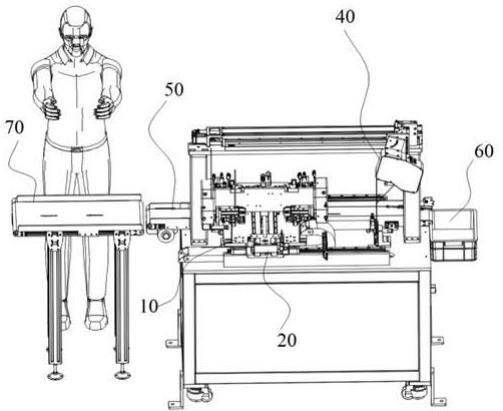
1.本实用新型涉及检测领域,更具体地,涉及一种汽车零部件检测装置。
背景技术:2.随着生活水平的提高和科技的快速发展,汽车已经成为人们出行不可或缺的交通工具,而为了保证汽车的整体质量和行车安全,通常需要严格把控汽车各零部件的加工精度和加工质量。传统的厂商在生产汽车零部件时,往往安排员工通过肉眼识别零部件合格与否,不仅工作强度大,效率低,人工成本高,并且容易出现误判,出错率高,导致不良产品流入市场,影响车辆装配或整车质量。
技术实现要素:3.本实用新型旨在克服上述现有技术的至少一种缺陷(不足),提供一种汽车零部件检测装置,用于解决传统的厂商在生产汽车零部件时,往往安排员工通过肉眼识别零部件合格与否,不仅工作强度大,效率低,人工成本高,并且容易出现误判,出错率高,导致不良产品流入市场,影响车辆装配或整车质量的问题。
4.本实用新型采取的技术方案如下:
5.一种汽车零部件检测装置,包括:底座;
6.上料台,滑动设于底座上,用于接收工件;
7.夹具模组,滑动设于所述底座上且设于所述上料台侧方,用于夹取工件;所述夹具模组包括夹爪组件,驱动夹爪组件升降的升降机构,以及驱动夹爪组件旋转的旋转机构;
8.相机组件,滑动设于夹具模组上方,用于检测工件;
9.下料台,设于底座一侧且与所述夹具模组配合,用于接收检测完成的工件;
10.控制器,至少与上料台、夹具模组和相机组件电连接,用于控制上料台、夹具模组和相机组件的动作。
11.在其中一个实施例中,所述夹爪组件包括第一夹爪和第二夹爪,所述第一夹爪和第二夹爪分别设于所述上料台的两相对侧;所述旋转机构包括分别驱动第一夹爪和第二夹爪旋转的第一旋转电机和第二旋转电机。
12.在其中一个实施例中,所述第一旋转电机与第二旋转电机通过连接板连接,且所述升降机构驱动所述连接板升降。
13.在其中一个实施例中,还包括设于所述底座上且用于对工件进行吹气的吹气机构,所述吹气机构与所述控制器电连接。
14.在其中一个实施例中,所述吹气机构包括第一吹气组件和第二吹气组件,所述第一吹气组件和第二吹气组件分别设于所述上料台两侧。
15.在其中一个实施例中,所述底座上还设有用于对夹具模组的滑动进行缓冲的第一缓冲件;和/或所述底座上还设有用于对上料台的滑动进行缓冲的第二缓冲件。
16.在其中一个实施例中,所述底座上设有用于对夹具模组的极限位置进行感应的第
一传感器,所述第一传感器与所述控制器电连接;和/或所述底座上还设有用于对上料台的极限位置进行感应的第二传感器,所述第二传感器与所述控制器电连接;和/或所述上料台上设有用于感应工件的第三传感器,所述第三传感器与控制器电连接。
17.在其中一个实施例中,所述上料台包括与所述底座滑动配合的滑动块,以及设于所述滑动块上的定位台,所述定位台上设有定位销钉。
18.在其中一个实施例中,还包括与底座滑动配合的滑轨,以及驱动底座在所述滑轨上位移的驱动件;所述底座的滑动方向与所述相机组件的滑动方向匹配。
19.在其中一个实施例中,所述下料台包括用于接收检测完成的工件的传动带,以及驱动所述传动带正反转运动的正反转电机,所述正反转电机与所述控制器电连接。
20.与现有技术相比,本实用新型的有益效果至少包括:
21.本技术方案的汽车零部件检测装置采用人工智能装配对汽车零部件的加工质量和加工高精度进行检测,有效降低人力劳动强度,降低人工成本,同时避免了因人为主观因素以及疲劳检测造成的误判,有效降低出错率,提高产品良率,保障整车装配和整车质量。具体地,本技术方案通过上料台滑动到上料工位接收工件,随后上料台滑动至夹取工位,夹具模组下降至夹取工位以夹取工件,夹取稳定后夹具模组上升至检测工位,相机组件此时滑动至检测工位上方对工件进行获取并传送获取到的图片和点位等信息至控制器,通过控制器内的预设程序对获取的图片信息进行自动化检测,并且通过旋转机构驱动夹爪组件旋转,使工件的各个面均能够被相机组件获取,以完成工件的全方位检测;当工件检测完成后,夹具模组滑动至下料台的下料工位处,将工件松开,使工件落于下料台上。
附图说明
22.图1为本实用新型的实施例所述的汽车零部件检测装置的结构示意图;
23.图2为本实用新型的实施例所述的汽车零部件检测装置的局部示意图;
24.图3为图2中a的局部放大示意图;
25.图4为本实用新型的实施例所述的汽车零部件检测装置的局部工作状态图;
26.图5为本实用新型的实施例所述的汽车零部件检测装置的侧视图;
27.图6为图5中b的局部放大示意图。
28.附图标记:10、底座;20、上料台;21、滑动块;22、定位台;23、定位销钉;30、夹具模组;31、第一夹爪;32、第二夹爪;33、第一旋转电机;34、第二旋转电机;35、连接板;40、相机组件;50、下料台;60、回收篓;70、传输带;80、吹气机构;90、第一缓冲件;100、滑轨;110、工件;120、导向板。
具体实施方式
29.本实用新型附图仅用于示例性说明,不能理解为对本实用新型的限制。为了更好说明以下实施例,附图某些部件会有省略、放大或缩小,并不代表实际产品的尺寸;对于本领域技术人员来说,附图中某些公知结构及其说明可能省略是可以理解的。
30.如图1-图4所示的一种汽车零部件检测装置,包括:底座10;
31.上料台20,滑动设于底座10上,用于接收工件;
32.夹具模组30,滑动设于所述底座10上且设于所述上料台20侧方,用于夹取工件;所
述夹具模组30包括夹爪组件,驱动夹爪组件升降的升降机构,以及驱动夹爪组件旋转的旋转机构;
33.相机组件40,滑动设于夹具模组30上方,用于检测工件;
34.下料台50,设于底座10一侧且与所述夹具模组30配合,用于接收检测完成的工件;
35.控制器(图中未示出),至少与上料台20、夹具模组30和相机组件40电连接,用于控制上料台20、夹具模组30和相机组件40的动作。
36.本实施方式的汽车零部件检测装置采用人工智能装配对汽车零部件的加工质量和加工高精度进行检测,有效降低人力劳动强度,降低人工成本,同时避免了因人为主观因素以及疲劳检测造成的误判,有效降低出错率,提高产品良率,保障整车装配和整车质量。具体地,本实施方式通过上料台20滑动到上料工位接收工件,随后上料台20滑动至夹取工位,夹具模组30下降至夹取工位以夹取工件,夹取稳定后夹具模组30上升至检测工位,相机组件40此时滑动至检测工位上方对工件进行获取并传送获取到的图片和点位等信息至控制器,通过控制器内的预设程序对获取的图片信息进行自动化检测,并且通过旋转机构驱动夹爪组件旋转,使工件的各个面均能够被相机组件40获取,以完成工件的全方位检测;当工件检测完成后,夹具模组30滑动至下料台50的下料工位处,将工件松开,使工件落于下料台50上。
37.本实施方式中的升降机构为气缸升降机构,旋转机构为旋转电机。所述底座10上设有与夹具模组30滑动配合的夹具滑轨,夹具模组30可通过气动的方式在夹具滑轨上滑移。同理,底座10上设有与上料台20滑动配合的上料滑轨,上料台20通过气动的方式在上料滑轨上滑移。
38.本实施方式上料滑轨与夹具滑轨平行设置或呈一字型对接设置。
39.所述相机组件40包括设于夹具模组30上方的相机滑轨,以及与相机滑轨滑动配合的相机,所述相机滑轨可为滚珠丝杠式的滑轨,也可为气动式滑轨;所述相机为二维相机和/或三维相机。
40.本实施方式所述下料台50包括用于接收检测完成的工件的传动带,以及驱动所述传动带正反转运动的正反转电机,所述正反转电机与所述控制器电连接。具体地,本实施方式的下料台50的第一端设有用于收集不合格工件的回收篓60,下料台50的第二端设有用于传输合格工件的传输带70,所述下料台50的第二端为与所述下料台50的第一端相对的一端。当工件经过控制器判断为合格品后,控制器控制正反转电机正转,此时传送带的传动方向朝向第二端,将合格工件传送至传输带70经工人封装后出厂;当工件经过控制器判断为不合格品后,控制器控制正反转电机反转,此时传动带的传动方向朝向第一端,将不合格工件传送至回收篓60内进行回收。通过此设置,提升了本检测装置的自动化程度,无需通过人工根据控制器的提示对检测完成后的工件进行分拣,进一步降低人工成本。当然,在其他实施方式中,也可采用人工分拣的方式。
41.如图3所示,本实施方式所述夹爪组件包括第一夹爪31和第二夹爪32,所述第一夹爪31和第二夹爪32分别设于所述上料台20的两相对侧,第一夹爪31和第二夹爪32分别夹取工件的两相对侧,使工件在升降和旋转检测过程中保持良好的稳定性,不会因夹持不稳而松裸。
42.相应地,所述旋转机构包括分别驱动第一夹爪31和第二夹爪32旋转的第一旋转电
机33和第二旋转电机34。通过预设程序使第一旋转电机33和第二旋转电机34在夹取到工件后同步旋转。
43.为了减少升降机构的数量,以及保证升降的同步性,本实施方式所述第一旋转电机33与第二旋转电机34通过连接板35连接,且所述升降机构驱动所述连接板35升降。从而,第一旋转电机33和第二旋转电机34通过连接板35集成,可只采用一个升降机构就能够同时驱动第一夹爪31和第二夹爪32的同步升降,既节约成本,又便于装配,同时最高限度保证了第一夹爪31和第二夹爪32升降的一致性。
44.由于汽车零部件中大部分为冲压件,在冲压过程中往往需要用到润滑油,而润滑油粘附于工件上不仅会影响夹具模组30的抓取,还会影响相机组件40获取到的图片质量,造成图片反光或误判。因此本实施方式还包括设于所述底座10上且用于对工件进行吹气的吹气机构80,所述吹气机构80与所述控制器电连接。通过吹气机构80对工件进行吹气,吹去或减少粘附于工件上的润滑油,保障检测顺利完成。
45.本实施方式所述吹气机构80包括第一吹气组件和第二吹气组件,所述第一吹气组件和第二吹气组件分别设于所述上料台20两侧。具体地,所述第一吹气组件对应于第一夹爪31设置,所述第二吹气组件对应于第二夹爪32设置,既不影响工件的抓取和检测,又能够保证工件的大部分面积均能经过吹气处理。
46.如图5-图6所示,本实施方式所述底座10上还设有用于对夹具模组30的滑动进行缓冲的第一缓冲件90。当工件被相机组件40扫描完成后,夹具模组30需滑动至与下料台50对接,使工件被夹具模组30松开后能够落于下料台50上,因此,为了避免夹具模组30滑动至下料台50的过程中因速度过快导致的撞击或惯性,本实施方式使夹具模组30稳定停靠的第一缓冲件90。所述第一缓冲件90为用于反向顶推夹具模组30的顶推件,所述夹具模组30上设有用于与顶推件配合的顶推板,当夹具模组30滑动至接近下料台50时,顶推件与顶推板接触,达到缓冲作用。其中,顶推件可设置为头部设有弹性部件的顶推棒,所述顶推棒设于下料台50的侧方或侧上方。弹性部件可为塑胶块、橡胶块等。
47.同理,所述底座10上还设有用于对上料台20的滑动进行缓冲的第二缓冲件(图中未示出),其原理与结构与第一缓冲件90相似,在此不再赘述。
48.本实施方式所述底座10上设有用于对夹具模组30的极限位置进行感应的第一传感器,所述第一传感器与所述控制器电连接;从而使夹具模组30在来回滑动时能够稳定停留在夹具工位和下料工位。即在夹具工位和下料工位处均设置第一传感器以感应夹具模组30的位置。本实施方式所述第一传感器为红外传感器,在其他实施方式中可为接触传感器或其他传感器。
49.同理,所述底座10上还设有用于对上料台20的极限位置进行感应的第二传感器,所述第二传感器与所述控制器电连接。第二传感器的结构、位置和原理与第一传感器相似,在此不再赘述。
50.本实施方式所述上料台20上设有用于感应工件的第三传感器,所述第三传感器与控制器电连接。第三传感器用于感应工件是否已到达上料台20,从而控制器可根据感应信号驱动上料台20滑动至夹取工位。当然,在其他实施方式中,也可不设置第三传感器,而是通过设定特定的节奏,使各模组、组件按特定节奏运行,互相配合以完成检测。
51.本实施方式所述上料台20包括与所述底座10滑动配合的滑动块21,以及设于所述
滑动块21上的定位台22,所述定位台22上设有定位销钉23。所述滑动块21与上料滑轨配合,定位台22用于放置工件,定位销钉23则与工件上的孔配合,使工件在上料台20上不会发生晃动、位移、掉落等,保证工件的顺利传送。另外,本实施方式的定位台22的形状可设置为与工件相匹配。
52.如图6所示,本实施方式的下料台50的上方还设有用于对工件的下料进行导向的导向板120,所述导向板120的数量为两个或多个,本实施方式以两个为例,两个导向板120间隔设置,且导向板120呈斜坡型,从而类似漏斗的效果,使夹具模组30松开工件110后,工件110能够顺利落入至下料台50。
53.如图2-图3所示,由于汽车零部件有较多呈对称结构,为了提高本检测装置的灵活性和通用性,实现两工位或多工位交叉检测,本实施方式还包括与底座10滑动配合的滑轨100,以及驱动底座10在所述滑轨100上位移的驱动件;所述驱动件为气缸。例如,当底座10位于第一位置时,此时对左工件进行检测,当底座10通过滑轨100滑动至第二位置时,此时对与左工件对称的右工件进行检测,只需对预设的检测程序稍作调整,即可完成右工件的检测,而无需另外设置一台检测装置。
54.另外,为了便于相机组件40顺利获取左工件和右工件的信息,本实施方式所述底座10的滑动方向与所述相机组件40的滑动方向匹配,且相机组件40的滑动行程能够覆盖底座10的滑动行程。即相机滑轨与底座10的滑轨100平行设置,且相机滑轨的长度大于底座10的滑轨100的长度。
55.本实施方式的相机组件40的滑动方向与夹具模组30的滑动方向不同。具体地,本实施方式的相机的滑动方向与夹具模组30的滑动方向垂直,便于检测装置的装配、工件的传输以及两工位或多工位的交错检测。
56.显然,本实用新型的上述实施例仅仅是为清楚地说明本实用新型技术方案所作的举例,而并非是对本实用新型的具体实施方式的限定。凡在本实用新型权利要求书的精神和原则之内所作的任何修改、等同替换和改进等,均应包含在本实用新型权利要求的保护范围之内。