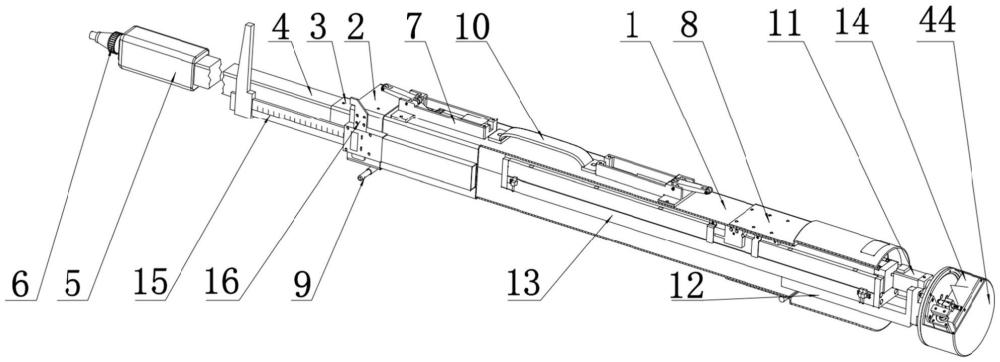
本发明涉及测量,尤其涉及一种超长深孔反型腔自动测量装置及使用方法。
背景技术:
1、深孔反型腔是指在深孔加工过程中,为了测量或检验深孔的形状和尺寸而特意在其周围制作的一个与之形状完全相反的凹槽或腔体。这个凹槽或腔体被称为反型腔,位于工件的表层。反型腔深孔类零件测量技术广泛应用于多个行业,由于其精度和适应性,主要集中在航空航天、汽车工业、医疗器械、军事装备、建筑机械等领域中,测量存在很多难以解决的问题,如深孔型腔复杂、内部难以直接接触、尺寸和形状公差较小,精度要求高、深孔内部结构易被破坏、空间狭窄,深孔的大长径比限制测量范围等测量问题。
2、而传统的反型腔深孔检测手段是使用三坐标对深孔的开口小段距离进行测量,然而对于超长深孔内部空间限制,深部盲孔端只能用游标卡尺、高度规、千分尺等,粗略测量其直径、深度和形状,这种方法可能存在精度受限和操作困难的问题,且只能做定性判断,判断合格与否,不能测出精确的实际尺寸。现阶段关于反型腔深孔测量的研究存在测量精度低、效率低等问题
技术实现思路
1、针对上述问题,本发明的目的在于提供一种超长深孔反型腔自动测量装置及使用方法,可高效、高精度的测量反型腔深孔的孔径、圆度、圆弧角、锥角和直线度等重要技术参数。
2、本发明的目的是通过以下技术方案来实现的:
3、一种超长深孔反型腔自动测量装置,包括碳纤维方管、钢套b、连接方套、支撑管、手持柄、航空插座、涨紧组件、钢套a、支撑组件、把手、旋转单元、连接长板、平移单元、测量单元、高度尺和高度尺安装板;
4、所述碳纤维方管的左端与钢套b的右端连接,所述钢套b的左端与连接方套的右端连接,所述连接方套的左端与支撑管的右端连接,所述支撑管的左端与手持柄的右端连接,所述手持柄的左端安装航空插座;所述碳纤维方管的右部与钢套a的左端连接;所述支撑组件有两个、分别安装于钢套a和钢套b的底部,所述涨紧组件有两个、分别前后对称安装于碳纤维方管的顶部;
5、所述连接长板固定在所述连接长板为l型折板,轴向板为长板、径向板为短板且位于轴向板的右端;所述连接长板的径向板与旋转单元连接、轴向板与平移单元连接;
6、所述涨紧组件包括推杆架、电动推杆、滑动垫片、楔形拉块、扭簧和摆动杆;所述推杆架为矩形槽结构,槽口朝上,内端封闭开小槽口、外端开口;所述电动推杆的固定件安装于推杆架的小槽口内,电动推杆的伸出杆端与楔形拉块的内端连接,所述楔形拉块的外端上部与摆动杆的内端滚动连接,楔形拉块的外端下部与滑动垫片滑动连接,所述滑动垫片固定安装于推杆架的外端槽内,所述摆动杆内外两端均通过短圆柱销固定安装滚动轴承,摆动杆通过长圆柱销固定安装于推杆架外端槽内,推杆架两侧的长圆柱销上分别嵌套扭簧;
7、所述支撑组件包括脚座、插换腿、顶杆、弹簧和紧定螺钉;所述插换腿有两根,分别前后对称安装在脚座的前后方向通孔中;所述插换腿的外端为两阶梯圆柱、内端为带有环形锥槽的圆柱;所述顶杆有两个,顶杆的顶端为圆球状、前段为圆柱,所述弹簧嵌套在圆柱上,所述紧定螺钉通过个螺纹孔安装在脚座的前部、且与顶杆的前端面接触;所述顶杆的顶端与插换腿内端的环形锥槽接触;
8、所述平移单元由直线模组组成,包括滑轨、固定块、直线电机、光栅尺和限位开关;所述固定块安装于碳纤维方管右端,通过螺栓与碳纤维方管和钢套a固定连接;所述光栅尺读数头安装在固定块上;所述滑轨与固定块滑动连接,构成滑动副;所述直线电机安装在滑轨内部;
9、所述测量单元包括转台连接盘、直角架、微型推杆、激光位移传感器、内窥镜和测量单元外壳;所述微型推杆包括微型推杆固定件、微型推杆移动件和推杆电机;所述转台连接盘固定在旋转单元的中空转台上;所述直角架的左侧固定于转台连接盘上,右侧与微型推杆固定件连接;所述传感器安装架与微型推杆移动件固定连接;所述推杆电机安装于微型推杆固定件上;所述激光位移传感器与传感器安装架通过螺钉固定连接,激光位移传感器所产生的激光束沿中空转台径向出射,出射光线位于垂直中空转台轴线的平面内;所述内窥镜安装架与微型推杆的移动件固定连接,所述内窥镜固定安装在内窥镜安装架上;
10、所述高度尺安装板安装于高度尺尺头外壳上,高度尺左端通过高度尺安装板安装于钢套b上,高度尺尺身和右端分别由两块高度尺安装块通过螺钉固定在碳纤维方套上。
11、进一步地,所述钢套b的右端设置大方孔、左端设置小方孔。
12、进一步地,所述旋转单元包括中空转台、转台支架和旋转电机;所述中空转台和旋转电机均安装在转台支架上,所述转台支架固定在连接长板的径向板上;所述中空转台的轴线与碳纤维方管的轴线共线,所述中空转台的大齿轮圈与旋转电机轴端的小齿轮啮合;所述旋转电机的轴线偏离中空转台的轴线且与中空转台的轴线平行。
13、进一步地,所述脚座的后侧中部开有前后方向的通气孔;所述通气孔的前端与插换腿左右的通孔连通。
14、进一步地,所述插换腿为前后对称结构。
15、进一步地,所述插换腿的伸入端的锥形环槽在插入脚座时与弹簧作用下顶出的顶杆球头形成配合,将插换腿定位。
16、进一步地,所述插换腿有多组,每组插换腿的长度不同,同组插换腿的长度相同,不同组的插换腿用于整组替换以适应不同的越长深孔直径要求。
17、一种超长深孔反型腔自动测量装置的使用方法,包括如下步骤:
18、a、对固定长度l’进行标定
19、将超长深孔反型腔自动测量装置安装于标定装置上,记标定装置上的固定长度段为l、激光位移传感器出射位置到滑轨零点位置的固定距离为l1、滑轨伸出长度为l2、高度尺读数为l3,使用l对超长深孔反型腔自动测量装置中间部分的固定长度l’进行标定,标定步骤如下:
20、a1、用三坐标测量仪标定测量装置上的激光位移传感器出射位置到滑轨零点位置的固定距离l1和标定装置上的固定长度段l;
21、a2、将超长深孔反型腔自动测量装置安装于标定装置上,拉伸高度尺至标定装置上固定段l的末端,记录高度尺读数l3;
22、a3、驱动滑轨移动,带动激光位移传感器至固定段l的首端,光栅尺读数头记录滑轨伸出长度l2;
23、a4、计算超长深孔反型腔自动测量装置中间部分的固定长度l’,公式如下:
24、l’=l-l1-l2-l3
25、b、管内定位
26、顶部涨紧组件的电动推杆默认伸出状态,此时2个摆动杆被扭簧顶起;使用时,驱动顶部涨紧组件的电动推杆缩回,此时2个摆动杆被拉平,将超长深孔反型腔自动测量装置推入深孔反型腔零件内,支撑组件的插换腿端面上加工有带圆弧段的凸缘,通过凸缘与深孔反型腔零件内孔母线的配合使整个装置支撑于深孔反型腔零件内孔下壁上,驱动顶部涨紧组件的电动推杆再伸出,2个摆动杆再次被扭簧顶起,摆动杆抵住深孔反型腔零件内孔上壁,完成整个装置的管内定位;
27、c、测量
28、c1、截面测量
29、测量时,直线电机驱动滑轨带动测量单元沿深孔反型腔零件内孔轴线方向平移,旋转电机驱动中空转台带动测量单元绕深孔反型腔轴线旋转,微型推杆电机驱动测量单元沿径向方向移动,实现对深孔反型腔的孔径、圆度、直线度、圆弧角、锥度、深度的测量,具体步骤如下;
30、c11、截面测量时,直线电机驱动滑轨带动测量单元沿孔轴线方向移动到被测截面处,微型推杆根据激光位移传感器此时待测的截面孔径调整径向伸出量,直到达到激光位移传感器有效测量量程后,中控转台带动激光位移传感器绕轴线旋转360°采点并记录,记录轴向深度位置l”,记录多组激光位移传感器读数;
31、c12、在深孔反型腔零件当前待测截面数据采集完成后,移动到下一被测截面处,重复步骤c11,直到完成深孔反型腔零件所有待测截面处的测量,通过计算机对被测截面处的数据进行处理,并通过最小二乘法拟合出被测截面处的孔径、圆度;
32、c13、通过实际测量得到不同截面处点的位置数据,采用最小二乘法计算出各测量截面圆心的位置,通过不同截面处的圆心拟合出实际轴线,采用最小区域包容法计算出所测件圆柱段的直线度;
33、c2、母线测量
34、c21、母线测量时,直线电机驱动滑轨带动测量单元沿孔轴线方向移动到被测圆弧段或锥段起点处,中空转台周向锁定至0°方向,记录该处激光位移传感器的读数,记录轴向位置l”,激光位移传感器沿该母线轴向缓慢移动,行走同时微型推杆根据激光位移传感器此时距待测母线的距离调整径向伸出量,保证移动过程中激光位移传感器读数有效,记录多组轴向位置和激光位移传感器读数;
35、c22、在深孔反型腔零件当前待测母线数据采集完成后,旋转中空转台分别至90°、180°、270°,重复步骤c21中测量过程,直到完成深孔反型腔零件每个圆弧段或锥段四个方向待测母线的测量,通过计算机对圆弧段或锥段被测母线数据进行处理,并通过最小二乘法拟合出圆弧段和锥段的圆弧角和锥角。
36、c23、通过实际测量得到测量单元的轴向移动量l2,从而确定各待测深度值l”,公式如下:
37、l”=l1+l2+l’+l3。
38、本发明与现有技术相比具有以下优点:
39、1、本发明采用集成式非接触光学测量手段,解决了反型腔深孔测量研究存在的表面形状复杂、测量困难,便携程度低、深部端测量空间受限且测量精度低、效率低等问题。
40、2、本发明采用可伸缩集成式测量结构,通过外壳和方套保护整个核心测量结构,采用弹簧涨紧定位、旋转和移动、测量等多单元设计,结实耐用,结构简单、便携性好,使用方便,可适用于恶劣的测量环境;
41、3、本发明设计了三个方向的运动机构,实现轴向、周向、径向运动,采用轴向移动、周向转动、径向调整的设计来调整激光位移传感器的位置,满足反型腔内壁复杂表面的孔径测量需求,实现可伸缩式多孔径测量,适用于测量空间发生变化的情况,且装置各运动单元移动灵活、刚性好、运动精度高、结构紧凑。