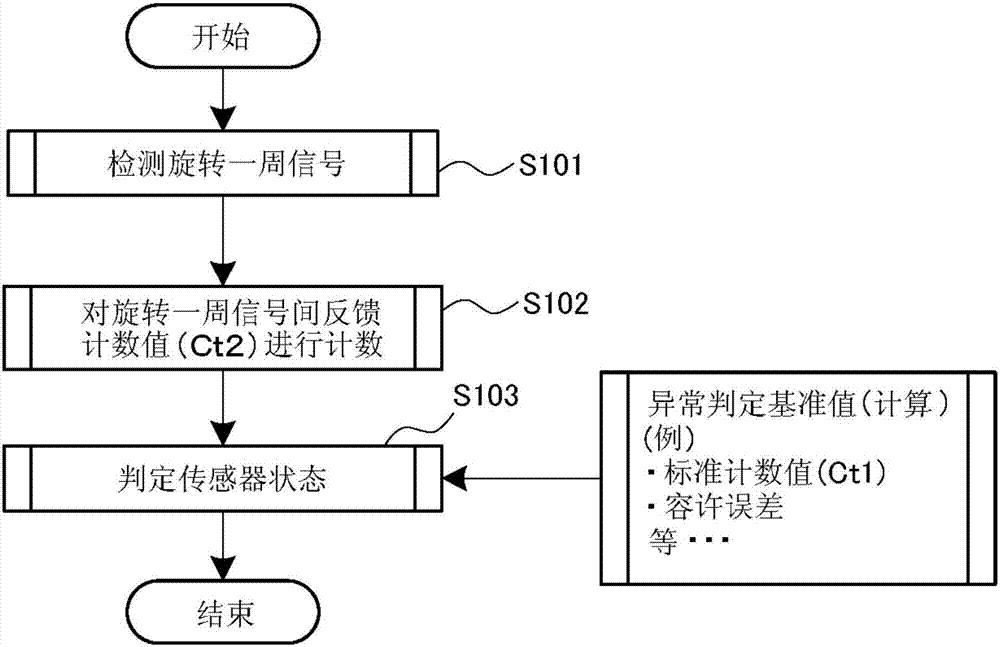
本发明涉及一种机床的控制装置,特别涉及一种具有检测旋转一周信号的传感器的故障诊断功能的机床的控制装置。
背景技术:
在对机床的进给轴或主轴进行驱动时,为了检测其速度或位置而使用传感器。在该传感器发生了某些异常的情况下,需要进行该异常的原因的分析。为了进行传感器的异常原因的分析,通常需要示波器、计算机工具等外部测定装置。通过这些装置来观测来自传感器的信号波形,从而能够根据波形推测异常原因。
作为传感器的异常的原因,可以考虑到接线错误、传感器的安装错误、噪音等几个原因。然而,存在如下问题:为了使用上述这样的装置来进行具体的原因的确定,而花费时间和成本。
因此,报告有如下一种装置:对z相信号(旋转一周信号)的脉冲间的反馈脉冲数进行计数,在该计数值与规格值不同时判定为接线错误(例如实用新型授权第2574740号公报)。根据该以往技术,根据旋转一周信号间的反馈脉冲数的计数值能够检测出反馈信号存在异常。然而,存在如下问题:关于异常的计数值,全部判定为接线错误,因此无法判定计数值的异常是由于噪音引起的还是由于传感器自身的异常引起的。
技术实现要素:
本发明的目的在于提供一种在确认出旋转一周信号间的反馈脉冲数的计数值存在异常的情况下能够确定传感器的异常部位的机床的控制装置。
本发明的一个实施例所涉及的机床的控制装置是通过电动机对进给轴或主轴进行驱动的机床的控制装置,所述机床的控制装置的特征在于,具备:反馈计数器,其获取从检测被驱动轴或电动机的位置或速度的传感器输出的矩形波或正弦波的a/b相信号以及在电动机或主轴旋转一周时产生的旋转一周信号,对根据a/b相信号生成的反馈脉冲数的计数值即反馈计数值进行计数;反馈计数值存储部,其存储在两个连续的旋转一周信号之间进行计数所得到的反馈计数值即旋转一周信号间反馈计数值;基准值存储部,其存储用于根据旋转一周信号间反馈计数值来判定是否存在异常的异常判定基准值;以及异常原因判定部,其通过将旋转一周信号间反馈计数值与异常判定基准值进行比较来判定异常原因。
附图说明
本发明的目的、特征以及优点通过与附图相关的以下的实施方式的说明会变得更加明确。在该附图中,
图1是本发明的实施例所涉及的机床的控制装置的框图,
图2是用于说明本发明的实施例所涉及的机床的控制装置的动作过程的概要的流程图,
图3是用于说明在本发明的实施例所涉及的机床的控制装置中,在旋转一周信号间反馈计数值比异常判定基准值小的情况下的异常判定过程的流程图,
图4是用于说明在本发明的实施例所涉及的机床的控制装置中,在旋转一周信号间反馈计数值比异常判定基准值大的情况下的异常判定过程的流程图,以及
图5是用于说明在本发明的实施例所涉及的机床的控制装置中,在旋转一周信号间反馈计数值比异常判定基准值小的情况以及旋转一周信号间反馈计数值比异常判定基准值大的情况下的异常判定过程的流程图。
具体实施方式
下面,参照附图来说明本发明所涉及的机床的控制装置。在图1中示出本发明的实施例所涉及的机床的控制装置的框图。本发明的实施例所涉及的机床的控制装置(以下也仅称为“控制装置”。)10是通过电动机30来对进给轴或主轴进行驱动的机床的控制装置,具有反馈计数器1、反馈计数值存储部2、基准值存储部3、异常原因判定部4以及电动机控制部5。
在电动机30的附近设置有传感器40。传感器40检测被驱动轴(未图示)或电动机30的位置或速度。作为传感器40,例如能够使用编码器。传感器40输出a/b相信号和旋转一周信号。a/b相信号为具有90°的相位差的两个脉冲信号。根据电动机的旋转方向,输出的b相信号相对于a相信号的相位差为+90°或-90°。根据电动机的旋转量,输出的a/b相信号的脉冲(反馈脉冲)的数量发生增减。根据电动机的旋转速度,输出的a/b相信号的脉冲间隔变宽或变窄。所谓旋转一周信号是电动机或主轴每旋转一周时生成的脉冲信号。
电动机控制部5将来自传感器40的旋转一周信号和a/b相信号用作反馈信号来控制电动机30。
反馈计数器1获取从传感器40输出的a/b相信号和旋转一周信号,对旋转一周信号间反馈计数值进行计数。在此,所谓旋转一周信号间反馈计数值是根据两个连续的旋转一周信号间的a/b相信号生成的反馈脉冲数的计数值。反馈计数器1将计数出的旋转一周信号间反馈计数值输出到异常原因判定部4。
异常原因判定部4具有反馈计数值存储部2和基准值存储部3。但是,反馈计数值存储部2和基准值存储部3也可以设置在异常原因判定部4的外部。
反馈计数值存储部2存储旋转一周信号间反馈计数值。
基准值存储部3存储用于根据旋转一周信号间反馈计数值判定是否存在异常的异常判定基准值。例如,能够将异常判定基准值设为推测为在传感器40正常的情况下计数出的旋转一周信号间反馈计数值即标准计数值(ct1)。或者,也可以将异常判定基准值设为容许误差。但是,这些只是一例,并不限于这些例子。
异常原因判定部4通过将旋转一周信号间反馈计数值与异常判定基准值进行比较来判定异常原因。关于异常原因的判定方法的详情在后面进行叙述。异常原因判定部4将异常原因的判定结果输出到数值控制装置20。
数值控制装置20具备显示器21。当数值控制装置20接收到从异常原因判定部4所输出的旋转一周信号间反馈计数值与异常判定基准值不同的意思的信号(通知)时,在显示器21上显示督促确认异常的发生的消息。并且,显示器21能够显示检测出旋转一周信号的意思的消息或显示旋转一周信号间反馈脉冲。
接着,使用图2所示的流程图来说明本发明的实施例所涉及的机床的控制装置的动作过程。首先,在步骤s101中,传感器40检测旋转一周信号。传感器40还检测a/b相信号,将所检测到的旋转一周信号和a/b相信号输出到反馈计数器1。
接着,在步骤s102中,反馈计数器1对旋转一周信号间反馈计数值(ct2)进行计数。反馈计数器1将计数出的旋转一周信号间反馈计数值输出到异常原因判定部4。异常原因判定部4将获取到的旋转一周信号间反馈计数值存储到反馈计数值存储部2。
接着,在步骤s103中,异常原因判定部4判定传感器状态。即,异常原因判定部4通过对反馈计数值存储部2中存储的旋转一周信号间反馈计数值与基准值存储部3中存储的异常判定基准值进行比较来判定传感器的状态。
像以上这样,根据本发明的实施例所涉及的机床的控制装置,能够根据从传感器输出的旋转一周信号和a/b相信号检测传感器是否存在异常。
接着,对判别传感器的异常的原因的方法进行说明。本发明的实施例所涉及的机床的控制装置10通过考虑在旋转一周信号存在异常的情况和a/b相信号存在异常的情况下旋转一周信号间的反馈脉冲分别如何变化,来确定传感器的异常部位。
首先,使用图3所示的流程图来说明在本发明的实施例所涉及的机床的控制装置中旋转一周信号间反馈计数值比异常判定基准值小的情况下的异常判定过程。
首先,在步骤s201中,判定旋转一周信号间反馈计数值(计数值(ct2))是否比异常判定基准值a小。可以认为,在旋转一周信号由于噪音而发生紊乱从而发生异常这样的情况下,在旋转一周内的多个部位产生旋转一周信号的可能性高。因此,相对于正常的情况,旋转一周信号间反馈计数值(计数值)极端地变小的可能性高。
另外,在传感器的安装存在问题而没有正常地对根据a/b相信号生成的反馈脉冲进行计数的情况下也同样地,旋转一周信号间的反馈脉冲极端地变小的可能性高。
因此,在旋转一周信号间反馈计数值比异常判定基准值a小的情况下,在步骤s202中,判定为旋转一周信号的异常或传感器的安装调整的异常。像这样,异常原因判定部4在旋转一周信号间反馈计数值比异常判定基准值小的情况下,判定为旋转一周信号由于噪音而发生紊乱或传感器的安装调整存在问题。
接着,说明在本发明的实施例所涉及的机床的控制装置中在旋转一周信号间反馈计数值比异常判定基准值大的情况下的异常判定过程。
在a/b相信号由于噪音而发生紊乱的情况下,通过a/b相信号的比较来检测相位变化的电路发生异常。因此,在a/b相信号为矩形波的情况下,在各信号的1个脉冲的宽度的期间,反馈脉冲的计数值与正常的情况相比产生误差d,在a/b相信号为正弦波的情况下,在各信号的一个波的宽度的期间,反馈脉冲的计数值与正常的情况相比产生误差d。然而,在发生一次异常的情况下产生的误差比较小。因此,相比于正常的情况,旋转一周信号间反馈计数值不会极端地变小。因此,在旋转一周信号间反馈计数值比异常判定基准值大的情况并且相对于正常的情况的误差为上述误差d的整数倍的情况下,判定为a/b相信号由于噪音而发生紊乱。即,异常原因判定部4在旋转一周信号间反馈计数值比异常判定基准值大并且旋转一周信号间反馈计数值与传感器正常的情况下的旋转一周信号间反馈计数值之间的误差相当于根据a/b相信号的每旋转一周的脉冲或波的数量求出的、具有每当a/b相信号由于噪音而发生紊乱就产生的可能性的误差的整数倍的情况下,判定为a/b相信号由于噪音而发生紊乱。
另一方面,在旋转一周信号间反馈计数值比异常判定基准值大的情况并且相对于正常的情况的误差不是上述误差d的整数倍的情况下,判定为由于旋转一周信号的异常而旋转一周信号的产生位置产生了偏差的可能性高。即,异常原因判定部4在旋转一周信号间反馈计数值的误差不相当于具有每当a/b相信号由于噪音而发生紊乱时就产生的可能性的误差的整数倍的情况下,判定为旋转一周信号的异常。
接着,使用图4所示的流程图来说明在本发明的实施例所涉及的机床的控制装置中旋转一周信号间反馈计数值比异常判定基准值大的情况下的异常判定过程。首先,在步骤s301中,判定旋转一周信号间反馈计数值(计数值(ct2))是否比异常判定基准值a大。在计数值比异常判定基准值a大的情况下,在步骤s302中,判定表示传感器正常的情况下的旋转一周信号间反馈计数值(ct1)与计数出的旋转一周信号间反馈计数值(ct2)之差为误差d的整数倍(n倍)的下述的等式(1)是否成立。
(ct1-ct2)=n×d(1)
在式(1)成立的情况下,在步骤s303中,判定为a/b相信号的由于噪音而发生的异常。另一方面,在式(1)不成立的情况下,在步骤s304中,判定为z相信号(旋转一周信号)的异常。
在以上的说明中,说明了在旋转一周信号间反馈计数值(计数值(ct2))比异常判定基准值a小的情况和旋转一周信号间反馈计数值(计数值(ct2))比异常判定基准值a大的情况的各个情况下的判定异常的方法。然而,并不限于这样的例子,也可以连续进行这两个判定方法。因此,使用图5所示的流程图来说明在针对旋转一周信号间反馈计数值(计数值(ct2))比异常判定基准值a大的情况判定了是否存在异常之后、在旋转一周信号间反馈计数值(计数值(ct2))比异常判定基准值a小的情况判定是否存在异常的方法。
首先,在步骤s401中,判定旋转一周信号间反馈计数值(计数值(ct2))是否比异常判定基准值a大。在计数值比异常判定基准值a大的的情况下,在步骤s402中,判定表示传感器正常的情况下的旋转一周信号间反馈计数值(ct1)与计数出的旋转一周信号间反馈计数值(ct2)之差为误差d的整数倍(n倍)的上述的等式(1)是否成立。
在式(1)成立的情况下,在步骤s403中,判定为a/b相信号的由于噪音而发生的异常。另一方面,在式(1)不成立的情况下,在步骤s404中,判定为z相信号(旋转一周信号)的异常。
另一方面,在计数值为异常判定基准值a以下的情况下,在步骤s405中,判定旋转一周信号间反馈计数值(计数值(ct2))是否比异常判定基准值a小。在旋转一周信号间反馈计数值比异常判定基准值a小的情况下,在步骤s406中,判定为旋转一周信号的异常或传感器安装调整的异常。
另一方面,在旋转一周信号间反馈计数值(计数值(ct2))与异常判定基准值a相等的情况下,判定为传感器没有发生异常。
在上述的说明中,说明了在针对旋转一周信号间反馈计数值比异常判定基准值大的情况判定了是否存在异常之后、针对旋转一周信号间反馈计数值比异常判定基准值小的情况判定是否存在异常的方法,但并不限于这样的例子。即,也可以在针对旋转一周信号间反馈计数值比异常判定基准值小的情况判定了是否存在异常之后、针对旋转一周信号间反馈计数值比异常判定基准值大的情况判定是否存在异常。
如以上所说明的那样,根据本发明的实施例所涉及的机床的控制装置,能够不使用外部测定装置而监视传感器状态来进行传感器的异常部位的判定。
根据本发明的一个实施例所涉及的机床的控制装置,在确认出旋转一周信号间的反馈脉冲数的计数值存在异常的情况下,能够确定传感器的异常部位。