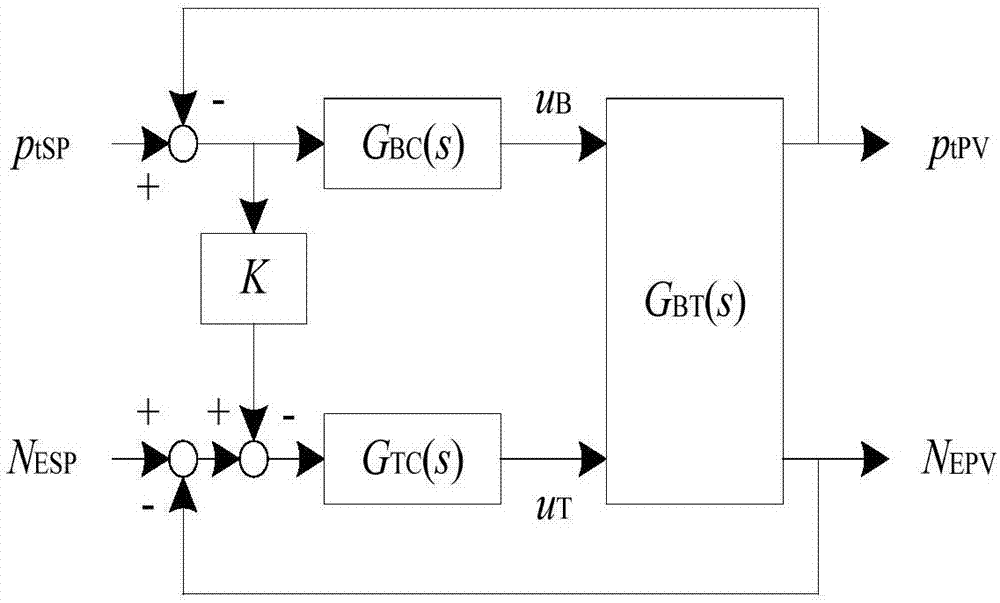
本发明属于自动化
技术领域:
,特别涉及火电机组协调控制系统中压力拉回控制的补偿控制方法。
背景技术:
:当前及未来一段时间内我国电力供应仍将以火电为主,需要火电机组提高运行灵活性消纳风电等带有强扰动性的发电电源大规模并网造成的各种扰动,衡量灵活性的指标中最为重要的是发电负荷调节范围和发电负荷调节速率。受热力系统特性制约火电机组响应发电负荷变化的能力相对较差,提高发电负荷响应速率必然会导致机组自身运行稳定性变差,使得锅炉燃料量、汽轮机前蒸汽压力、过热/再热蒸汽温度、烟气氧量等决定着机组安全、经济、环保指标的参数波动加剧。因此火电机组控制系统设计、调试时,需要在发电负荷响应性能和机组自身运行稳定性之间作出权衡。火电机组协调控制系统被控对象为双入双出多变量对象,特性为:增加锅炉燃料量时,机前压力和发电负荷同时缓慢增加;增加汽轮机调门开度时,发电负荷先快速增加后降低恢复至原值,机前压力快速降低。协调控制系统的主要任务是控制发电负荷快速跟随发电负荷指令变化,同时维持汽轮机前蒸汽压力的稳定。为了快速响应发电负荷指令,机组多采用汽轮机调门控制发电负荷,锅炉燃料量控制机前压力即以炉跟机为基础的协调控制方式。控制特点是,发电负荷设定值增加时,汽轮机侧控制器动作增加调门开度,实际发电负荷快速增加跟随发电负荷设定值,但同时导致机前压力快速降低,锅炉侧控制器动作增加燃料量,使机前压力缓慢跟随机至前压力设定值。技术实现要素::本发明要解决的技术问题:针对现有协调控制系统中压力拉回控制动作时会改变控制系统结构、减弱锅炉侧控制器对汽轮机前蒸汽压力的控制作用之不足,提出一种压力拉回控制的补偿控制方法。本发明采取的技术方案为:一种机炉协调控制系统中压力拉回控制的补偿控制方法,该方法为在机炉协调控制系统的压力拉回控制逻辑中,将压力偏差经过多点折线函数计算出的发电负荷偏置指令信号,引入到另外一个多点折线函数计算得到一个锅炉侧控制器增益补偿系数,再用该补偿系数以乘积的形式修正协调控制系统锅炉侧控制器的偏差输入信号。所述的控制增益补偿系数的获得,包括以下步骤:步骤一、首先将控制增益补偿系数设置为1;步骤二、在机组小幅变负荷工况下,观察压力拉回未动作时机前压力变化幅度对应锅炉燃料量变化幅度的比例并记录;步骤三、在机组不同负荷点重复进行步骤二,对多次记录结果取平均值;步骤四、在机组大幅变负荷工况下,逐渐增加拉回控制增益补偿系数,使得压力拉回动作时机前压力变化幅度对应锅炉燃料量变化幅度的比例等于步骤三得到的平均值,记录增益补偿系数;步骤五、在机组不同负荷点重复进行步骤四,对多次调试得到的增益补偿系数取平均值,作为最终设置值。所述的压力拉回控制满足以下条件:a.当压力拉回控制未动作时,锅炉侧控制器增益补偿系数为1;协调控制系统保持原有状态;当压力拉回控制动作时,锅炉侧控制器增益补偿系数大于1,维持锅炉侧控制器对机前压力的控制作用不变。所述的压力拉回控制逻辑为将机前压力偏差信号经过带死区和限幅作用的多点折线函数转化为发电负荷偏置指令,与原发电负荷指令与发电负荷反馈的偏差相迭加,构成实际发电负荷指令。采用本发明的技术方案,在压力拉回控制逻辑中,将压力偏差经过多点折线函数计算出的发电负荷偏置指令信号,引入到另外一个多点折线函数计算得到一个锅炉侧控制器增益补偿系数,再用该补偿系数以乘积的形式修正协调控制系统锅炉侧控制器的偏差输入信号。通过设置增益补偿系数的多点折线函数的参数可以实现:当压力拉回控制未动作时,锅炉侧控制器增益补偿系数为1,协调控制系统保持原有状态;当压力拉回控制动作时,锅炉侧控制器增益补偿系数大于1,增强锅炉侧控制器的控制作用以抵消压力拉回控制动作的影响,维持锅炉侧控制器对机前压力的控制作用不变,快速减小压力偏差从而减少对发电负荷控制品质的影响。与现有技术比较,本发明有以下技术效果:(1)补偿控制效果好。本发明给出机炉协调控制系统中压力拉回控制的补偿控制方法,能够保留压力拉回控制有利的一面,即汽轮机机前蒸汽压力偏差大时,强迫机组改变发电负荷维持压力稳定;能够克服压力拉回控制不利的一面,即压力拉回控制动作时不减弱锅炉侧控制器的调节强度,尽快结束压力拉回动作避免长时间影响发电负荷的控制品质。现场实用效果好,特别适用于频繁大幅参与电网调峰的火电机组。(2)组态简单、调试快捷。本发明组态简单,只需要在原协调控制系统中增加2个模块,可以在任何dcs中实现。整个补偿控制逻辑只有一个需要调试的参数,参数变化范围小调试方向明确,现场调试过程简单快捷。参数调试好后,控制系统可长期运行不需要维护。附图说明:图1协调控制系统闭环结构示意图;图2压力拉回控制动作后协调控制系统闭环结构示意图;图3压力拉回控制的补偿控制系统结构示意图;图4压力拉回控制的补偿控制逻辑。具体实施方式一种机炉协调控制系统中压力拉回控制的补偿控制方法,具体的实施方式如下:炉跟机协调控制系统闭环结构如图1所示。以炉跟机方式为基础的机炉协调控制系统能够有效利用锅炉蓄热快速响应发电负荷,但利用蓄热的过程会导致机前压力变化,因此也必须加大对锅炉燃料量的调节幅度以同时弥补发电负荷和机前压力的变化。压力拉回控制逻辑通过机前压力的偏差修正发电负荷的偏差,当压力拉回控制动作后,协调控制系统闭环结构如图2所示。相当于在基本控制系统基础上,增加了一路压力偏差对发电负荷侧控制回路的单向解耦通道。单向解耦通道的存在使得整个控制系统的调节作用减弱。当机组发电负荷快速跟随发电负荷指令变化时,会导致机前压力反馈值偏离设定值出现偏差,这种偏差反而又会限制发电负荷变化,使得实际发电负荷的变化速率减缓;另外由于减缓发电负荷变化能够起到辅助调节机前压力的作用,机前压力偏差的变化幅度和变化速率也会减缓,又会使得锅炉侧控制器的控制作用减弱。压力拉回空话子逻辑中,压力偏差对发电负荷偏差的增益越大,减弱调节作用的程度越为明显。图1~3中:ptsp为机前压力设定值,mpa;ptpv为机前压力反馈值,mpa;ub为锅炉燃料量,t/h;ut为汽轮机调门开度,%;模块gbc(s)为锅炉侧控制器传递函数;模块gtc(s)为汽轮机侧控制器传递函数;模块gbt(s)为被控对象传递函数;模块k为机前压力偏差对发电负荷偏差的增益系数;模块kpb为压力拉回补偿控制的增益系数。从大方向上分析,由于压力拉回控制都设置有压力偏差的死区,即压力偏差小于死区高低限值时压力拉回控制是不发生作用的;当压力拉回控制动作时,可以认为机组处于非正常工作状态,需要减弱整个控制系统的调节作用,以维持机组安全运行。但是从细节上分析,压力拉回控制动作时,强迫发电负荷变化对维持机前压力稳定是有利的;但减弱锅炉侧控制器的调节强度,这在许多情况下不符合现场要求的。如果锅炉运行状态没有明显异常,则期望锅炉侧控制器快速调节燃料量使机前压力尽快恢复正常。特别是电负荷指令频繁大幅变化时,这种期望表现得更为迫切。因此,更加符合现场需要的控制思路是:当机前压力偏差大时,同样强迫发电负荷变化维持压力稳定,但不减弱锅炉侧控制器的调节强度。对压力拉回控制增加补偿控制逻辑能够实现以上思路,控制系统结构如图3所示。即在图2所示控制系统基础上,锅炉侧控制器前增加一个大于1的增益补偿环节,对机前压力偏差信号进行放大,从而增强压力拉回动作时的锅炉侧控制器的调节强度。参考图4说明发明技术方案。图3中的虚线框内是在原协调控制系统基础上新增加的逻辑。原协调控制系统中,机前压力设定值与反馈值的偏差直接进入到锅炉侧控制器。新系统中,机前压力设定值与反馈值的偏差,乘以由多点折线函数计算出的压力拉回控制增益补偿系数后,再进入到锅炉侧控制器。图4中:sum1~3为均为求和模块;mul1为乘法模块;f(x)1为计算机前压力偏差对发电负荷偏差的多点折线函数模块,参数设置为死区加限幅的格式;f(x)2为计算压力拉回控制增益补偿系数的多点折线函数模块;pid1为锅炉侧控制器;pid2为汽轮机侧控制器。图4中,依靠计算机前压力偏差对发电负荷偏差的多点折线函数模块f(x)1设置压力拉回的死区、限值以及机前压力偏差对发电负荷偏差的增益系数。以表1的参数设置为例,压力拉回的死区高低幅值为±0.6mpa,即只有机前压力偏差超过±0.6mpa时压力拉回控制才动作;压力拉回的限值为±15mw,即压力拉回控制最多只产生±15mw的发电负荷偏置指令;机前压力偏差对发电负荷偏差的增益系数为15/1.2=12.5。表1多点折线函数模块f(x)1设置表1序号123456x-100-1.2-0.60.61.2100y-15-15001515图4中,依靠计算压力拉回控制增益补偿系数的多点折线函数模块f(x)2设置不同情况下的锅炉侧控制器增益补偿系数。以表2的参数设置为例,未发生压力拉回时f(x)2的输入为0,不需要进行补偿因此拉回控制增益补偿系数为1;发生压力拉回时f(x)2的输入不为0,拉回控制增益补偿系数为1.4;f(x)2的第2点和第4点的作用是设置一个±10%的缓冲区,作用是避免拉回控制增益补偿系数突然变化导致锅炉侧控制器输入的突然变化。表2为多点折线函数模块f(x)2设置。表2序号12345x-15-1.501.515y1.41.411.41.4压力拉回控制逻辑结构为将机前压力偏差信号经过带死区和限幅作用的多点折线函数转化为发电负荷偏置指令,与原发电负荷指令与发电负荷反馈的偏差相迭加,构成实际发电负荷指令。实现的功能是:当机前压力反馈值和设定值的偏差在死区内时,压力拉回控制不起作用,协调控制系统处于正常工作方式下;当机前压力反馈值高于设定值并超出死区时,提高发电负荷指令,通过增加发电负荷的方式达到降低机前压力的目的,保证机组运行安全;当机前压力反馈值低于设定值并超出死区时,降低发电负荷指令,通过减少发电负荷达到提高机前压力的目的,保证机组运行安全。从控制系统的角度分析,当压力拉回控制动作时,相当于在原协调控制系统结构的基础上增加了一个压力偏差对发电负荷控制回路的单向耦合通道,这一通道的存在将导致整个控制系统的结构和控制特性发生变化。实际运行过程中表现为:正常情况下机组协调控制系统锅炉侧控制器依据机前压力的偏差调节锅炉燃料量实现对机前压力的控制;但压力拉回控制动作时系统会通过调整发电负荷的方式协助减小压力偏差,因此会导致锅炉侧控制器接收到的压力偏差信号减弱,使得锅炉侧控制器输出的调节量也相应减弱,进而导致对机前压力的控制作用减弱。最终结果是,压力拉回控制一旦动作就会持续较长一段时间,降低发电负荷的控制品质。举例说明如下:压力拉回死区上限为0.6mpa,当机前压力反馈值超过设定值0.6mpa时压力拉回控制动作。如果压力拉回不动作,机前压力反馈值会超过设定值0.8mpa,锅炉侧控制器会减少20t/h的燃料量,经过一段时间后机前压力反馈值会降低至正常水平。但压力拉回动作后,由于发电负荷增加,机前压力反馈值只会超过设定值0.7mpa,锅炉侧控制器会只减少15t/h的燃料量,因此要经过较长一段时间后机前压力反馈值才会降低至正常水平。发明实施步骤为(1)实施条件确认发明适用于采用以炉跟机炉方式为基础的火电机组协调控制系统,分析组态逻辑,确认压力拉回逻辑的位置。(2)补偿逻辑组态在机组dcs(分散控制系统)中增加图4中虚线框内的压力拉回控制补偿控制逻辑。其中多点折线函数f(x)2的设置方式见表2。(3)现场调试在机组运行过程中对f(x)2中的拉回控制增益补偿系数进行调试。调试过程是,1)首先将系数设置为1;2)在机组小幅变负荷工况下,观察压力拉回未动作时机前压力变化幅度对应锅炉燃料量变化幅度的比例并记录;3)在机组不同负荷点重复进行步骤2,对多次记录结果取平均值;4)在机组大幅变负荷工况下,逐渐增加拉回控制增益补偿系数,使得压力拉回动作时机前压力变化幅度对应锅炉燃料量变化幅度的比例等于步骤3得到的平均值,记录增益补偿系数;5)在机组不同负荷点重复进行步骤4,对多次调试得到的增益补偿系数取平均值,作为最终设置值。以上所述,仅为本发明的具体实施方式,但本发明的保护范围并不局限于此,任何熟悉本
技术领域:
的技术人员在本发明揭露的技术范围内,可轻易想到变化或替换,都应涵盖在本发明的保护范围之内,因此,本发明的保护范围应以所述权利要求的保护范围为准。当前第1页12