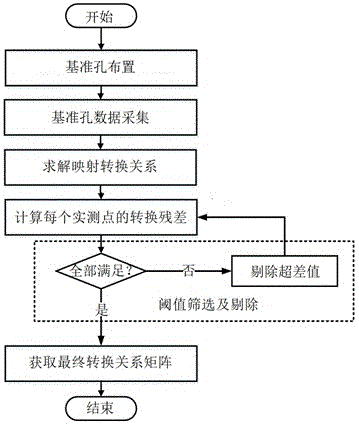
本申请涉及飞机装配
技术领域:
,尤其涉及一种飞机部件加工基准确定方法。
背景技术:
目前,在飞机装配制造过程中,为了提升制孔精度和效率,在飞机部件骨架零件完成装配后采用大型多轴联动数控机床中进行数控制孔和型面加工,部件加工基准建立的正确性作为保证飞机部件加工的关键,决定了飞机部件加工任务的成败。飞机部件加工基准建立实质是在解决如何将飞机理论状态中的加工信息通过某种转换关系映射到飞机实际结构上。而传统的工件加工坐标系建立方法无法适用于飞机部件加工,不能准确地反映飞机部件实际状态和理论状态之间的关系。技术实现要素:本申请的主要目的在于提供一种飞机部件加工基准确定方法,以达到能够有效地确定飞机部件加工基准,准确地反映飞机部件实际状态和理论状态之间的关系的作用。为实现上述目的,本申请提供一种飞机部件加工基准确定方法,包括以下步骤:在所述飞机部件上设计N个预留的基准孔,所述基准孔孔心布置均不在所述飞机部件的同一平面内;其中,N为基准孔数量,N≥4;获取所述飞机部件的基准孔孔心的实测数据和理论数据,具体包括以下步骤:步骤S1:建立机床坐标系C2,通过数控机床基于所述机床坐标系C2测量所述飞机部件上的基准孔孔心,所述基准孔孔心实测点集合记为{Qi=[XqiYqiZqi]T|Qi∈Q,i=1,2,...,n};其中,Qi为基准孔孔心实测点,Q为基准孔孔心实测点集合;步骤S2:建立飞机坐标系C1,并基于所述飞机坐标系C1获取实测的所述基准孔孔心对应的理论值,所述基准孔孔心理论点集合记为{Pi=[XpiYpiZpi]T|Pi∈P,i=1,2,...,n};其中,Pi为基准孔孔心理论点,P为基准孔孔心理论点集合;步骤S3:根据所述基准孔孔心理论位置与实测位置之间的对应关系,整理实测数据点和理论数据点,使得测量的每处基准孔孔心均有一数据对;其中,所述数据对为所述基准孔孔心对应的实测数据和理论数据;基于所述基准孔孔心的实测数据和理论数据,构建基准孔孔心实测点集合和基准孔孔心理论点集合之间的转换关系矩阵和评价函数;根据所述评价函数和所述转换关系矩阵,使用奇异值分解法计算求解获得使得所述评价函数取值最小的匹配转换关系矩阵R,t;其中,R为基准孔孔心实测点到理论点的旋转矩阵,t为基准孔孔心实测点到理论点的平移矩阵;根据所述匹配转换关系矩阵R,t,计算出每个基准孔孔心实测点位的转换残差Ei;判断所有基准孔孔心的转换残差Ei是否小于等于阈值e,若否,则剔除转换残差Ei最大的数据对,并使用剩余的数据对返回所述基于所述基准孔孔心的实测数据和理论数据,构建基准孔孔心实测点集合和基准孔孔心理论点集合之间的转换关系矩阵和评价函数的步骤,直至所有基准孔孔心的转换残差Ei均小于等于阈值e,获取最终转换关系矩阵R´,t´。可选地,所述基准孔孔心为基准孔凸台小平面与基准孔轴线相交得到,其中所述基准孔凸台小平面通过在基准孔凸台上取M个测量点拟合得到,所述基准孔轴线为基准孔内壁上取K个测量点拟合圆柱的轴线,分R层,每层S个,满足以下关系:。可选地,所述基准孔凸台厚度H满足8mm≥H≥4mm,所述基准孔孔径D满足20mm≥D≥4mm,所述基准孔间距要求为:至少有3个所述基准孔之间相互间距L满足2000mm≥L≥200mm。可选地,所述数据对的数量大于等于4。可选地,所述评价函数的表达式为:式中,Pi为基准孔孔心理论点,Qi为基准孔孔心实测点。可选地,所述根据所述匹配转换关系矩阵R,t,计算出每个基准孔孔心实测点位的转换残差Ei,具体包括:根据所述匹配转换关系矩阵R,t,将基准孔孔心实测点Qi转换到所述飞机坐标系C1下,记为Qi´=R*Qi-t;式中,Qi´为基准孔孔心实测点Qi经转换后在飞机坐标系C1下的表示;计算每个基准孔孔心实测点位的转换残差Ei=||Pi-Qi´||2。可选地,所述阈值e为基准允许误差,其取值范围为飞机部件型面加工精度要求的1/4~1/3。可选地,所述获取最终转换关系矩阵R´,t´的步骤之后,还包括以下步骤:根据所述最终转换关系矩阵R´,t´,以所述机床坐标系C2为所述飞机部件加工的工件坐标系,以所述机床坐标系C2原点为所述飞机部件加工原点,将所述飞机坐标系C1中的飞机部件中基准孔孔心的理论数据转换到所述机床坐标系C2中,开展加工任务。可选地,所述数控机床为多轴联动数控机床,所述多轴联动数控机床上设置有在线探头,通过所述在线探头测量所述飞机部件上的基准孔孔心。本申请所能实现的有益效果如下:本申请通过在飞机部件上预留基准孔,对基准孔的布置和测量作了明确定义,操作指导性强,有助于保证本申请方法的准确性;通过建立基准允许误差与飞机部件加工精度要求之间的联系,设计了一种阈值判断剔除机制用于辅助匹配转换关系矩阵求解,实现了飞机部件加工精度要求对部件基准建立的量化控制;基于建立的坐标系转换关系,求解了各个基准孔的转换残差,转换残差一方面可用于评估基准求解的误差情况,另一方也可以用于评价飞机部件结构的局部变形情况,因此,本申请方法通过在飞机部件上预留基准孔、采集基准孔数据、计算求解转换关系、建立飞机坐标系与机床坐标系的联系,从而能够有效地确定飞机部件加工基准,准确地反映飞机部件实际状态和理论状态之间的关系。附图说明为了更清楚地说明本申请具体实施方式或现有技术中的技术方案,下面将对具体实施方式或现有技术描述中所需要使用的附图作简单地介绍。在所有附图中,类似的元件或部分一般由类似的附图标记标识。附图中,各元件或部分并不一定按照实际的比例绘制。图1为本申请一种飞机部件加工基准确定方法的流程示意图;图2为本申请一种飞机部件加工基准确定方法的应用场景示意图;图3为本申请中测量基准孔孔心时的示意图;图4为本申请中实测基准孔孔心和理论基准孔孔心之间匹配转换时的原理示意图;图5为本申请中基准孔凸台在飞机部件上位置关系的示意图(局部放大)。附图标记:1-飞机部件,2-基准孔,3-数控机床,4-在线探头,5-基准孔孔心,6-基准孔凸台。本申请目的的实现、功能特点及优点将结合实施例,参照附图做进一步说明。具体实施方式下面将结合本申请实施例中的附图,对本申请实施例中的技术方案进行清楚、完整地描述,显然,所描述的实施例仅仅是本申请的一部分实施例,而不是全部的实施例。基于本申请中的实施例,本领域普通技术人员在没有作出创造性劳动前提下所获得的所有其他实施例,都属于本申请保护的范围。需要说明的是,本申请实施例中所有方向性指示(诸如上、下、左、右、前、后……)仅用于解释在某一特定姿态下各部件之间的相对位置关系、运动情况等,如果该特定姿态发生改变时,则该方向性指示也相应地随之改变。在本申请中,除非另有明确的规定和限定,术语“连接”、“固定”等应做广义理解,例如,“固定”可以是固定连接,也可以是可拆卸连接,或成一体;可以是机械连接,也可以是电连接;可以是直接相连,也可以通过中间媒介间接相连,可以是两个元件内部的连通或两个元件的相互作用关系,除非另有明确的限定。对于本领域的普通技术人员而言,可以根据具体情况理解上述术语在本申请中的具体含义。另外,若本申请实施例中有涉及“第一”、“第二”等的描述,则该“第一”、“第二”等的描述仅用于描述目的,而不能理解为指示或暗示其相对重要性或者隐含指明所指示的技术特征的数量。由此,限定有“第一”、“第二”的特征可以明示或者隐含地包括至少一个该特征。另外,全文中出现的“和/或”的含义,包括三个并列的方案,以“A和/或B”为例,包括A方案、或B方案、或A和B同时满足的方案。另外,各个实施例之间的技术方案可以相互结合,但是必须是以本领域普通技术人员能够实现为基础,当技术方案的结合出现相互矛盾或无法实现时应当认为这种技术方案的结合不存在,也不在本申请要求的保护范围之内。实施例1参照图1-图5所示,本实施例提供一种飞机部件加工基准确定方法,包括以下步骤:在所述飞机部件1上设计N个预留的基准孔2,基准孔孔心5布置均不在所述飞机部件1的同一平面内;其中,N为基准孔数量,N≥4;获取所述飞机部件1的基准孔孔心5的实测数据和理论数据,具体包括以下步骤:步骤S1:建立机床坐标系C2,通过数控机床3基于所述机床坐标系C2测量所述飞机部件1上的基准孔孔心5,所述基准孔孔心5实测点集合记为{Qi=[XqiYqiZqi]T|Qi∈Q,i=1,2,...,n};其中,Qi为基准孔孔心5实测点,Q为基准孔孔心5实测点集合;步骤S2:建立飞机坐标系C1,并基于所述飞机坐标系C1获取实测的所述基准孔孔心5对应的理论值,所述基准孔孔心5理论点集合记为{Pi=[XpiYpiZpi]T|Pi∈P,i=1,2,...,n};其中,Pi为基准孔孔心5理论点,P为基准孔孔心5理论点集合;步骤S3:根据所述基准孔孔心5理论位置与实测位置之间的对应关系,整理实测数据点和理论数据点,使得测量的每处基准孔孔心5均有一数据对;其中,所述数据对为所述基准孔孔心5对应的实测数据和理论数据;基于所述基准孔孔心5的实测数据和理论数据,构建基准孔孔心5实测点集合和基准孔孔心5理论点集合之间的转换关系矩阵和评价函数;根据所述评价函数和所述转换关系矩阵,使用奇异值分解法计算求解获得使得所述评价函数取值最小的匹配转换关系矩阵R,t;其中,R为基准孔孔心实测点到理论点的旋转矩阵,t为基准孔孔心实测点到理论点的平移矩阵;根据所述匹配转换关系矩阵R,t,计算出每个基准孔孔心实测点位的转换残差Ei;判断所有基准孔孔心5的转换残差Ei是否小于等于阈值e,若不满足,则剔除转换残差Ei最大的数据对,并使用剩余的数据对返回所述基于所述基准孔孔心5的实测数据和理论数据,构建基准孔孔心5实测点集合和基准孔孔心5理论点集合之间的转换关系矩阵和评价函数的步骤,直至所有基准孔孔心5的转换残差Ei均小于等于阈值e,获取最终转换关系矩阵R´,t´。由于传统数控零件加工通过调平找正等方法确定工件加工坐标系,方法简单便于操作,而飞机部件1具有尺寸大、零件数量多、结构形式复杂的特点,零件制造误差、结构装配误差、结构变形等因素的影响使得飞机部件1实际状态同理论状态相差巨大,传统的工件加工坐标系建立方法无法适用于飞机部件1加工。因此,亟需根据飞机部件1加工的结构特点,针对性的设计一种飞机部件1加工基准建立方法,该方法应当能够快速地完成加工基准建立,准确地反映飞机部件1实际状态和理论状态之间的关系。因此,在本实施例中,通过在飞机部件1上设计预留基准孔2,用于辅助加工基准建立;基准孔2孔心数据采集时,包括机床坐标系下的实测数据和飞机坐标系下的理论数据;映射转换矩阵求解时,构建转换关系评价函数,并使用奇异值分解方法求解函数极小值情况下的参数值,获得映射转换关系矩阵;然后进行基准孔2转换残差评价,基于求解的转换矩阵,在飞机坐标系下比较转换残差,剔除残差超差值并循环迭代,直至所有基准转换残差均满足阈值要求;确定最终映射转换矩阵,即可开展飞机部件1加工任务,本方法在数据输入源上使用的是飞机状态实测数据,并通过转换残差评价了转换误差和飞机实际状态同理论状态之间的差异,方法原理简单,可操作性好,在考虑数控机床3测量能力和飞机部件1骨架装配精度为常规水平的情况下,可以满足飞机部件1加工基准建立需求。基于本方法,不依赖外部工装,简单、快速、便捷,同时还可用于其他类似需要加工、但又无法找到可靠基准的加工场景。同时,在本实施例中,通过分别建立建立机床坐标系C2,先测得基准孔孔心5实测点集合的数据,然后根据建立飞机坐标系C1,基于实测的基准孔孔心5对应的理论值,从而获得基准孔孔心5理论点集合,即可根据基准孔孔心5理论位置与实测位置之间的对应关系,来保证测量的每处基准孔2均有一数据对,数据获取高效准确,为后续转换关系的求解奠定了基础。需要说明的是,在求解映射转换关系的步骤中,所述奇异值分解法是线性代数中一种重要的矩阵分解,奇异值分解则是特征分解在任意矩阵上的推广,在信号处理、统计学等领域有重要应用。奇异值分解法属于公知理论,这里不再赘述。作为一种可选的实施方式,基准孔孔心5为基准孔凸台6小平面与基准孔2轴线相交得到,其中基准孔凸台6小平面通过在基准孔凸台6上取M个测量点拟合得到,基准孔2轴线为基准孔2内壁上取K个测量点拟合圆柱的轴线,分R层,每层S个,满足以下关系:。在本实施例中,对基准孔孔心5作了明确定义,操作指导性强,并明确给出了基准孔凸台6小平面的获取方式及关系式,从而保证对基准孔孔心5的准确测量。作为一种可选的实施方式,所述基准孔凸台6厚度H满足8mm≥H≥4mm,所述基准孔2孔径D满足20mm≥D≥4mm,所述基准孔2间距要求为:至少有3个所述基准孔2之间相互间距L满足2000mm≥L≥200mm。在本实施例中,合理对基准孔2孔径D、间距要求以及基准孔凸台6厚度H进行限定,使后续测得数据更加可靠真实,更具有代表性。作为一种可选的实施方式,所述数据对的数量大于等于4,保证数据的可靠性。作为一种可选的实施方式,所述评价函数的表达式为:式中,Pi为基准孔孔心5理论点,Qi为基准孔孔心5实测点。依据该评价函数,可精确计算求解获得匹配转换关系矩阵R,t,具有较好的指导意义。作为一种可选的实施方式,所述根据所述匹配转换关系矩阵R,t,计算出每个基准孔孔心5实测点位的转换残差Ei,具体包括:根据所述匹配转换关系矩阵R,t,将基准孔孔心5实测点Qi转换到所述飞机坐标系C1下,记为Qi´=R*Qi-t;式中,Qi´为基准孔孔心5实测点Qi经转换后在飞机坐标系C1下的表示;计算每个基准孔孔心5实测点位的转换残差Ei=||Pi-Qi´||2。在本实施例中,具体给出了转换残差Ei的计算公式,依据该计算公式,可精确计算出每个基准孔孔心5实测点位的转换残差。作为一种可选的实施方式,所述阈值e为基准允许误差,其取值范围为飞机部件型面加工精度要求的1/4~1/3。保证阈值e处于合理误差范围内。作为一种可选的实施方式,获取最终转换关系矩阵R´,t´的步骤之后,还包括以下步骤:根据所述最终转换关系矩阵R´,t´,以所述机床坐标系C2为所述飞机部件1加工的工件坐标系,以所述机床坐标系C2原点为所述飞机部件1加工原点,将所述飞机坐标系C1中的飞机部件1中基准孔孔心的理论数据转换到所述机床坐标系C2中,开展加工任务。作为一种可选的实施方式,数控机床3为多轴联动数控机床,多轴联动数控机床上设置有在线探头4,通过在线探头4测量所述飞机部件1上的基准孔孔心5,无需再使用另外的测量装置。实施例2参照图1-4所示,本实施例结合具体实际运用,提供一种飞机部件加工基准确定方法,先设定相关参数如表1所示:表1基准孔测量值与理论值变量赋值基准孔数量N16基准孔凸台厚度H4mm基准孔间距L600~2000mm基准孔孔径DΦ12mm基准孔精度AH8平面凸台拟合点数量M4基准孔内壁取点数R2基准孔内壁取点层数S4加工基准允许误差e0.2下面就具体步骤进行说明:步骤1:基准孔布置:本实施例根据表1参数设置在飞机部件1上预先布置基准孔2,基准孔孔心5位置均不在飞机部件1的同一平面内;步骤2:基准孔数据采集:步骤2-1:使用多轴联动数控机床测量飞机部件1上基准孔孔心5,见表2,所述多轴联动数控机床的在线探头4测量不确定度为0.04mm;步骤2-2:根据测量的基准孔2信息,获取对应基准孔5在飞机坐标系下理论值,见表2;表2基准孔测量值与理论值统计表步骤3:求解映射转换关系:利用最小二乘法构建误差评价函数,使用奇异值分解法求解评价函数误差极小值,匹配实测孔心点集合{Qi=[XqiYqiZqi]T|Qi∈Q,i=1,2,...,n}到理论孔心点集合{Pi=[XpiYpiZpi]T|Pi∈P,i=1,2,...,n},获得匹配转换关系矩阵R1,t1,即:步骤4:计算每个实测点的转换残差:利用转换关系矩阵R1,t1,将实测孔位点Qi转换到飞机坐标系下,记为Qi´,计算实测点位转换残差Ei,见表3:表3转换后孔心点及残差步骤5:阈值筛选及剔除:对比基准孔孔心5残差Ei是否小于等于0.2mm,点14不满且为残差最大点,故剔除点14,使用剩余的数据对重复步骤3~步骤5,直至所有孔心点的转换残差均满足阈值要求,最终剩余11个基准孔参与基准计算,见表4:表4最终参与计算的基准孔及残差信息步骤6:获取最终转换关系矩阵:至此,最终获取的转换关系R´,t´,为机床坐标系相对于飞机坐标系的关系:利用该转换关系,并以机床原点为加工坐标系原点,可将设计数模的部件加工信息转换到机床坐标系中,开展部件加工工作。以上仅为本申请的优选实施例,并非因此限制本申请的专利范围,凡是利用本申请说明书及附图内容所作的等效结构或等效流程变换,或直接或间接运用在其他相关的
技术领域:
,均同理包括在本申请的专利保护范围内。当前第1页12