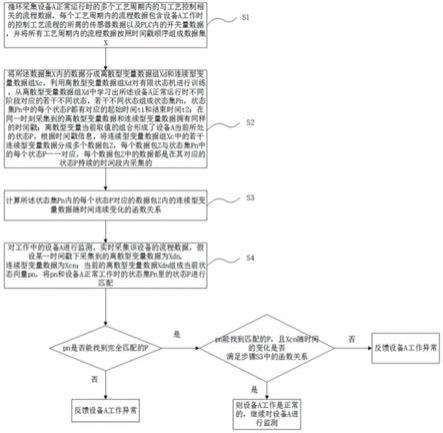
1.本发明涉及设备状态监测技术领域,尤其涉及一种基于概率混合有限状态机的设备状态监测方法。
背景技术:2.流程行业主要通过对原材料进行混合、分离、粉碎、加热等物理或化学方法操作,使原材料增值。它包括化工、造纸、钢铁、食品、制药等行业,最终产品类型有固体、液体、气体以及各种形式的能量,通常以批量或连续的方式进行生产。流程行业所用的设备大多为大型的生产设备,在制备产品的不同阶段都必须对反应设备中的温度、流量、压力、浓度等变量进行精确调控,以满足生产工艺的要求,确保产品的质量符合相应的标准。
3.随着产品工艺复杂程度的不断提高,在每个大型设备中均需要完成多个制备流程。由于每个流程的工艺参数都不同,因此,同一设备中的温度,流量,压力等信号会在不同的时间段有较大的差异,需要进行监测。
4.目前,设备状态监测的方法主要有两种:一种是,提前手工配置工艺流程,针对流程不同阶段,根据工艺工程师的经验来设置每个需要监测的传感器信号的最大和最小值(边界值),通过实时检测当前传感器信号是否越界,从而判断设备运行是否发生异常。这种方式往往需要消耗大量的人力物力,如果后续需要对流程参数进行调整,所有配置也必须随之手动修改。另外,人工手动配置出错几率较大,少许偏差均会大大降低异常诊断及预测的精度。从而导致对整个工艺流程监测的精度无法达到要求,产品质量出现瑕疵。另一种是,不考虑工艺流程信息,仅仅对关键的传感器信号,采用时间连续信号建模方法,试图去挖掘出一个大概率满足不同工艺阶段要求的统一的模型出来,用于异常监测和预警。由于同一信号在不同工艺流程中的参数一般并不相同,使用统一模型会产生过多的误报和漏报。另外,全局统一的数据模型在工艺状态转换衔接处诊断和预测效果并不是很好。
技术实现要素:5.本发明要解决的技术问题是:为了解决现有技术中的对流程行业的大型设备状态监测方法的监测精度较低,导致产品出现瑕疵的技术问题。本发明提供一种基于概率混合有限状态机的设备状态监测方法,通过采集设备正常运行时的多个工艺周期的流程数据,得到数据集x;并将数据集x分成离散型变量数据组和连续型变量数据组,利用离散型变量数据组对有限状态机进行训练,得到设备工作的状态集pn;计算所述状态集pn内的每个状态里的连续型变量数据组随时间连续变化的函数关系;再利用状态集pn和函数关系对设备的实时工作状态进行监测,及时发现故障或者错误,提高设备工作的准确性和效率。
6.本发明解决其技术问题所采用的技术方案是:一种基于概率混合有限状态机的设备状态监测方法,包括以下步骤:s1:循环采集设备a正常运行时的多个工艺周期内的与工艺控制相关的流程数据,每个工艺周期内的流程数据包含设备a工作时的控制工艺流程的所需的传感器数据以及
plc内的开关量数据,并将所有工艺周期内的流程数据按照时间戳顺序组成数据集x。
7.s2:将所述数据集x内的数据分成离散型变量数据组xd和连续型变量数据组xc,利用离散型变量数据组xd对有限状态机进行训练,从离散型变量数据组xd中学习出所述设备a正常运行时不同阶段对应的若干不同状态,若干不同状态组成状态集pn,状态集pn中的每个状态p都有对应的起始时间t1和结束时间t2;在同一时刻采集到的离散型变量数据和连续型变量数据拥有同样的时间戳;离散型变量当前取值的组合形成了设备a当前所处的状态p,根据时间戳信息,将连续型变量数据组xc中的若干连续型变量数据分成多个数据包z,每个数据包z与状态集pn中的每个状态p一一对应,每个数据包z中的数据都是在其对应的状态p持续的时间段内采集的。
8.s3:计算所述状态集pn内的每个状态p对应的数据包z内的连续型变量数据随时间连续变化的函数关系。
9.s4:对工作中的设备a进行监测,实时采集该设备的流程数据,假设某一时间戳下采集到的离散型变量数据为xdn, 连续型变量数据为xcn;当前的离散型变量数据xdn组成当前状态向量pn,将pn和设备a正常工作时的状态集pn里的状态p进行匹配,若pn不能找到完全匹配的p,则反馈设备a工作异常,若pn能找到匹配的p,且xcn随时间的变化满足步骤s3中的函数关系,则设备a工作是正常的,继续对设备a进行监测,若pn能够找到匹配的p,但是xcn随时间的变化不满足步骤s3中的函数关系,则反馈设备a工作异常。
10.进一步的,步骤s3中的函数关系包括一元函数关系和多元函数关系,当所述连续型变量数据组xc中只包含一个连续型变量的变化数据时,计算得到的函数关系为一元函数关系;当所述连续型变量数据组xc中包含多个连续型变量的变化数据时,计算得到的函数关系为多元函数关系,该多元函数关系表示多个连续型变量的变化数据之间的相互关联关系。
11.进一步的,利用所述离散型变量数据组xd对有限状态机进行训练时,还能够获得所述状态集pn中的相互之间能够转换的任意两个状态之间的转换条件集tn,每个所述转换条件t包括状态转换的触发条件、状态转换发生的概率以及转换之前上一个状态停留的时间区间。
12.进一步的,所述离散型变量数据是指取值是自然数或整数的变量数据,所述离散型变量数据组xd中包含至少一个离散型变量的变化数据;连续型变量数据是指在定义区间内任意取值的变量数据,所述连续型变量数据组xc中包含至少一个连续型变量的变化数据。例如,离散型变量数据可以是0,1,3等,连续型变量数据可以是随时间戳连续变化的数据。
13.进一步的,步骤s2中利用离散型变量数据组xd对有限状态机进行训练的过程具体包括:s21:将离散型变量数据组xd中所有的离散型变量组成一个信号向量v,初始化有限状态机内的状态集和转换条件集,得到初始状态集p’和初始转换条件集t’,设置当前的信号向量v形成的状态为初始状态p0,并将初始状态p0保存至初始状态集p’内;s22:每隔一个采样周期监测一次信号向量v中的值是否发生改变,信号向量v中值
的改变即为状态转换的触发条件;如果信号向量v中的值发生变化,则先查看当前变化tc引起的状态转换的触发条件是否已记录在初始转换条件集t’中,如果初始转换条件集t’中没有记录,则将该变化tc引起的状态转换的触发条件写入初始转换条件集t’中;如果初始转换条件集t’中已有记录,则不做修改;再查看由该变化tc触发的下一个状态st是否已记录在初始状态集p’中,如果初始状态集p’中没有记录,则将状态st写入初始状态集p’中;如果初始状态集p’中已有记录,则不做修改;根据时间戳信息计算tc触发状态发生转换前的上一状态停留的时间区间;s23:如果信号向量v中的值没有发生变化,则重复步骤s22直至所述离散型变量数据组xd中所有的数据使用完毕,将所有的状态st写入初始状态集p’得到设备a正常工作的状态集pn;并统计从同一状态转换到其他状态的总次数,计算同一状态转换到其他状态的概率,即状态转换发生的概率;将所有的将所有的状态转换的触发条件、状态转换发生的概率及转换之前上一个状态停留的时间区间写入初始转换条件集t’中,得到转换条件集tn。
14.进一步的,所述步骤s4还包括:对工作中的设备a进行监测,实时采集该设备的流程数据,假设某一时间戳下采集到的离散型变量数据为xdn, 连续型变量数据为xcn;当前的离散型变量数据xdn组成当前状态向量pn,将pn和设备a正常工作时的状态集pn里的状态p进行匹配,并且将由上一状态转换到状态pn引起的转换条件tn与转换条件集tn里的转换条件t进行匹配,若pn不能找到完全匹配的p或者tn不能找到完全匹配的t,则反馈设备a工作异常,若pn能找到完全匹配的p,且tn能找到完全匹配的t,且xcn随时间的变化满足步骤s3中的函数关系,则设备a工作是正常的,继续对设备a进行监测,若pn能找到完全匹配的p,且tn能找到完全匹配的t,但是xcn随时间的变化不满足步骤s3中的函数关系,则反馈设备a工作异常。
15.本发明的有益效果是,本发明的基于概率混合有限状态机的设备状态监测方法,与现有的解决方法相比,本发明充分考虑了工艺流程控制的参数细节,能够更好地对工艺流程变化进行精准监测,实现更高的监测和预警准确度。此外,本发明的监测方法不再需要工程师手工设置警戒值,能够自动进行监测和预警,当发现异常情况时,本方法也能够自动更新相应的参数配置,提高监测的效率和精度。
附图说明
16.下面结合附图和实施例对本发明进一步说明。
17.图1是本发明的基于概率混合有限状态机的设备状态监测方法的流程图。
18.图2是本发明的利用离散型变量数据组对有限状态机进行训练的流程图。
19.图3是本发明实施例反应釜的概率混合有限状态机模型。
具体实施方式
20.现在结合附图对本发明作进一步详细的说明。这些附图均为简化的示意图,仅以示意方式说明本发明的基本结构,因此其仅显示与本发明有关的构成。
21.有限状态机是为研究有限内存的计算过程和某些语言类而抽象出的一种计算模
型。有限状态机内拥有有限数量的状态,每个状态可以迁移到零个或多个状态,输入字串决定执行哪个状态的迁移。有限状态自动机可以表示为一个有向图。现有技术中的有限状态机只能对离散型变量数据进行处理,而本发明的概率混合有限状态机能够同时对离散型变量数据和连续型变量数据进行处理。
22.如图1所示,一种基于概率混合有限状态机的设备状态监测方法,包括以下步骤:s1:循环采集设备a正常运行时的多个工艺周期内的与工艺控制相关的流程数据,每个工艺周期内的流程数据包含设备a工作时的控制工艺流程的所需的传感器数据(包含连续型变量的数据和/或离散型变量的数据)以及plc内的开关量数据(为离散型变量数据),并将所有工艺周期内的流程数据按照时间戳顺序组成数据集x。
23.需要说明的是,流程数据可以从设备a的plc中获取,或者通过通讯中间件(例如opc)获取。数据采集应在设备a按照工艺标准要求生产出合格产品时进行,使得采集到的数据更加准确的反应标准的工艺流程。流程数据包含设备a中与工艺流程控制相关的传感器数据和plc开关控制量数据,可以根据具体的工艺流程控制需求进行选择。在本实施例中,可以循环采集设备a正常运行时的35个合格生产周期或者生产批次的流程数据,该数据量可以满足有限状态机的训练使用。将所有工艺周期内的流程数据按照时间戳顺序组成数据集x。
24.s2:将数据集x内的数据分成离散型变量数据组xd和连续型变量数据组xc,利用离散型变量数据组xd对有限状态机进行训练,从离散型变量数据组xd中学习出设备a正常运行时不同阶段对应的若干不同状态,若干不同状态组成状态集pn,状态集pn中的每个状态p都有对应的起始时间t1和结束时间t2;在同一时刻采集到的离散型变量数据和连续型变量数据拥有同样的时间戳;离散型变量当前取值的组合形成了设备a当前所处的状态p,根据时间戳信息,将连续型变量数据组xc中的若干连续型变量数据分成多个数据包z,每个数据包z与状态集pn中的每个状态p一一对应,每个数据包z中的数据都是在其对应的状态p持续的时间段内采集的。
25.需要说明的是,离散型变量数据是指取值是自然数或整数的变量数据,离散型变量数据组xd中包含至少一个离散型变量的变化数据,例如开关量数据,二进制信号数据,电机的启停信号数据,限位开关流程数据等等。连续型变量数据是指在定义区间内任意取值的变量数据,连续型变量数据组xc中包含至少一个连续型变量的变化数据,例如,温度数据,压力数据,流量数据等等,连续型数据可以是随时间连续变化的数据。
26.从离散型变量数据中可以了解到设备工作状态是否发生变化,因此,本实施例利用离散型变量数据组对有限状态机进行训练。训练完成后可以获得设备a正常运行时不同阶段对应的若干不同状态,若干不同状态组成状态集pn,状态集pn中包含若干个不同的状态p,状态集pn中的每个状态p都有对应的起始时间t1和结束时间t2,也就是说,每个状态都会持续一段时间。例如,离散型变量数据组xd中包含4个离散型变量v1、v2、v3和v4,4个离散型变量可以组成信号向量(v1,v2,v3,v4),变量v1、v2、v3和v4的值均可以变化,4个变量不同的取值可以形成不同的状态p,每个状态p都会在一定时间段里持续存在(可以认为是一个工艺子流程)。根据时间戳信息,可以将连续型变量数据组xc中的数据分成多个数据包z,每个数据包z内可以包含一个或多个连续型变量的数据,每个数据包z中的数据都是在其对应的状态p持续的时间段内采集的。例如,数据包z内可以包含一段时间内的温度变量的多
个数据,或者数据包z内可以包含一段时间内的温度变量的多个数据和压力变量的多个数据。因此,根据时间戳信息,可以将状态p和数据包z进行一一匹配。
27.利用离散型变量数据组xd对有限状态机进行训练时,还能够获得状态集pn中的相互之间能够转换的任意两个状态之间的转换条件集tn,每个转换条件t包括状态转换的触发条件、状态转换发生的概率以及转换之前上一个状态停留的时间区间。
28.如图2所示,利用离散型变量数据组xd对有限状态机进行训练的过程具体包括:s21:将离散型变量数据组xd中所有的离散型变量组成一个信号向量v,初始化有限状态机内的状态集和转换条件集,得到初始状态集p’和初始转换条件集t’,设置当前的信号向量v形成的状态为初始状态p0,并将初始状态p0保存至初始状态集p’内。
29.s22:每隔一个采样周期(例如是1ms或者1s)监测一次信号向量v中的值是否发生改变,信号向量v中值的改变即为状态转换的触发条件;如果信号向量v中的值发生变化,则先查看当前变化tc引起的状态转换的触发条件是否已记录在初始转换条件集t’中,如果初始转换条件集t’中没有记录,则将该变化tc引起的状态转换的触发条件写入初始转换条件集t’中;如果初始转换条件集t’中已有记录,则不做修改;再查看由该变化tc触发的下一个状态st是否已记录在初始状态集p’中,如果初始状态集p’中没有记录,则将状态st写入初始状态集p’中;如果初始状态集p’中已有记录,则不做修改;根据时间戳信息计算该信号向量v中的值变化前的上一状态停留的时间区间。
30.s23:如果信号向量v中的值没有发生变化,则重复步骤s22直至离散型变量数据组xd中所有的数据使用完毕,将所有的状态st写入初始状态集p’得到设备a正常工作的状态集pn;并统计从同一状态转换到其他状态的总次数,计算同一状态转换到其他状态的概率,即状态转换发生的概率;将所有的将所有的状态转换的触发条件、状态转换发生的概率及转换之前上一个状态停留的时间区间写入初始转换条件集t’中,得到转换条件集tn。
31.s3:计算状态集pn内的每个状态p对应的数据包z内的连续型变量数据随时间连续变化的函数关系。
32.需要说明的是,函数关系包括一元函数关系和多元函数关系。当连续型变量数据组xc中只包含一个连续型变量的变化数据时,计算得到的函数关系为一元函数关系。当连续型变量数据组xc中包含多个连续型变量的变化数据时,计算得到的函数关系为多元函数关系,该多元函数关系表示多个连续型变量之间的相互关联关系。例如,当连续型变量数据组xc中只包含温度变量随时间变化的多个数据,这些数据是设备a正常运行时,不同工艺周期内温度变量变化数据(例如,采集了35个工艺周期的温度变化数据)。为了在实时监测时,对温度变量数据的监测更加准确和方便,首先需要将xc内的数据根据与xc在同一时间段内采集到的离散型变量的取值情况,将xc与pn中一个具体的状态p进行对应,从而得到若干子集x1,x2,...,xn。对处于同一状态p内的多个温度变化数据进行拟合,得到温度变量数据与时间的函数关系,此时函数关系为一元函数关系,例如x=at+b,x为温度变量数据,t为时间。例如,当连续型变量数据组xc中包含了温度、压力和流量三种连续型变量数据时,可以分别得到若干子集x1,x2,...,xn;f1,f2,...fn;k1,k2,...,kn。对处于同一状态p内的多个温度、压力和流量数据可以使用线性回归分别对这三个变量数据进行线性拟合,得到温度变量数据与时间的函数关系x=a1t+b1,压力变量数据与时间的函数关系f=a1t+b1,流量变量数据与时间的函数关系k=a3t+b3。也可以使用其它统计学或者数据挖掘算法(例如,邻近算
法、支持向量回归算法)进行拟合得到多元函数关系,该多元函数关系体现了温度、压力和流量三个变量数据在设备a正常工作时的相互关联关系。
33.经过步骤s1
‑
s3能够得到设备a正常工作时的状态集pn,转换条件集tn及多个函数关系(可以记为函数集ω),将状态集pn,转换条件集tn及函数集ω的组合记为概率混合有限状态集模型,并将该概率混合有限状态集模型存入本地电脑中。后面可以直接读取这个概率混合有限状态集模型对其他设备a的工作状态进行实时监测。
34.s4:对工作中的设备a进行监测,实时采集该设备的流程数据,假设某一时间戳下采集到的离散型变量数据为xdn, 连续型变量数据为xcn;当前的离散型变量数据xdn组成当前状态向量pn,将pn和设备a正常工作时的状态集pn里的状态p进行匹配;若pn不能找到完全匹配的p,则反馈设备a工作异常;若pn能找到匹配的p,且xcn随时间的变化满足步骤s3中的函数关系,则设备a工作是正常的,继续对设备a进行监测;若pn能够找到匹配的p,但是xcn随时间的变化不满足步骤s3中的函数关系,则反馈设备a工作异常。
35.步骤s4还可以包括:对工作中的设备a进行监测,实时采集该设备的流程数据,假设某一时间戳下采集到的离散型变量数据为xdn, 连续型变量数据为xcn;当前的离散型变量数据xdn组成当前状态向量pn,将pn和设备a正常工作时的状态集pn里的状态p进行匹配,并且将由上一状态转换到状态pn引起的转换条件tn与转换条件集tn里的转换条件t进行匹配;若pn不能找到完全匹配的p或者tn不能找到完全匹配的t,则反馈设备a工作异常,若pn能找到完全匹配的p,且tn能找到完全匹配的t,且xcn随时间的变化满足步骤s3中的函数关系,则设备a工作是正常的,继续对设备a进行监测,若pn能找到完全匹配的p,且tn能找到完全匹配的t,但是xcn随时间的变化不满足步骤s3中的函数关系,则反馈设备a工作异常。
36.当tn与t进行匹配时,只要tn中的状态转换的触发条件和转换转换之前上一个状态停留的时间区间中的任一个没有和t匹配,即认为是设备a工作异常。
37.下面以反应釜的工艺流程中为例来说明获得概率混合有限状态机的具体过程。
38.例如,反应釜包括两个进料阀门,一个出料阀门,两个液位开关和一个温度传感器。在这个反应釜中执行的工艺过程如下:向反应釜中添加液体原料a到液位一后停止。然后向反应釜中再添加液体原料b到液位二后停止。在添加原料的过程中持续给反应釜加热,直到反应釜内混合液体温度达到35摄氏度后保持恒温。混合液体在35摄氏度恒温条件下搅拌反应290秒后将混合液体从反应釜中排出。
39.在这一个工艺周期中可以采集到反应釜运行的部分流程数据如表1所示。可以循环采集反应釜的35个工艺周期的流程数据,也就是说可以得到35张表1的数据。
40.表1
时间戳(t)进料阀门1(v1)进料阀门2(v2)出料阀门(v3)液位开关1(h1)液位开关2(h2)温度(tem1)01000015.1011.50001018.30120101019.10170001120.50270001132.2300001135317.5001113532900110353460010035
346.50000035
从表1中可知,两个进料阀门变量、出料阀门变量和两个液位开关变量的数据是自然数,所以是离散型变量数据,数值1表示阀门或者开关是打开状态,数值0表示阀门或者开关是关闭状态。温度变量数据是连续型变量数据,温度值是随时间连续性变化,最终趋于平衡。三个阀门和两个开关的变量数据可以组成一个向量(v1,v2,v3,h1,h2)。利用三个阀门和两个开关的变量数据可以对有限状态机进行训练,可以得到反应釜在不同时间阶段的状态集pn。从表1中可知,向量(v1,v2,v3,h1,h2)共有8种取值组合,所以状态集pn中包含8个状态p1
‑
p8及1个初始状态p0。状态p1
‑
p8分别为p1(1,0,0,0,0)、p2(0,0,0,1,0)、p3(0,1,0,1,0)、p4(0,0,0,1,1)、p5(0,0,1,1,1)、p6(0,0,1,1,0)、p7(0,0,1,0,0)、p8(0,0,0,0,0),初始状态p0为反应釜未开始工作时的状态。表1中每一横条采集到的数据包含离散型变量和连续型变量在同一个时间点上的取值,采样时间点保存在时间戳里。由于篇幅的限制,表1里面的时间戳是跳跃的,真实数据里时间戳是等距的,两个相邻时间戳之间的时差总是等于一个采样周期。根据上一个状态,以及当前离散变量的取值情况,可以将采集到的每条数据里的连续型变量数据对应到一个状态里。属于同一个状态的连续性变量数据看作一个数据包。这里将温度变量数据分成8个数据包z1,z2,...,z8。状态p1
‑
p8和数据包z1
‑
z8是一一对应的,例如,状态p1对应数据包z1,状态p2对应数据包z2,等等。计算每个状态对应的数据包里的温度与时间变化的函数关系,本实施例的函数关系为一元函数关系,例如,状态p1对应的函数关系为y=t+6,状态p4对应的函数关系为y=1.2t+1,等等,其中,t表示时间戳,y表示温度。本实施例还可以得到反应釜的状态集pn中能够转换的任意两个状态之间的转换条件集tn,转换条件包括状态转换的触发条件、状态转换发生的概率以及转换之前上一个状态停留的时间区间。本实施例的状态转换的触发条件是1个或者多个离散型变量值发生变化。
41.图3是本发明实施例反应釜的概率混合有限状态机模型。p1
‑
p8分别表示8个状态,与表1对应。每个状态里均包含一个由离散型变量数据组成的向量和函数关系。例如,状态p1的向量为(1,0,0,0,0),函数关系为y=t+6。状态p2的向量为(0,0,0,1,0),函数关系为y=t+6。从状态p1转换到状态p2时,进料阀门1的变量v1从1变为0,同时,液位开关1的变量h1从0变为1,因此,由状态p1转换到状态p2引起的状态转换的触发条件是(
‑
1,0,0,1,0)。从状态p1转换到状态p2,本实施例共采集了35个工艺周期的流程数据,根据时间戳可以计算出状态p1停留的时间在10.5s
‑
11.5s之间,这样,就可以得到状态p1停留的时间区间(最小值到最大值)为[10.5,11.5]。由于本实施例的反应釜执行的工艺是按顺序进行,认为两个相邻的状态之间转换发生的概率是100%。因此,从状态p1转换到状态p2的转换条件集tn为(
‑
1,0,0,1,0)、[10.5,11.5]及100%。同理,从状态p2转换到状态p3的转换条件集tn为(0,1,0,0,0)、[0.5,0.5]及100%,从状态p3转换到状态p4的转换条件集tn为(0,
‑
1,0,0,1)、[4.5,5]及100%,从状态p4转换到状态p5的转换条件集tn为(0,0,1,0,0)、[300,301]及100%,从状态p5转换到状态p6的转换条件集tn为(0,0,0,0,
‑
1)、[11,12]及100%,从状态p6转换到状态p7的转换条件集tn为(0,0,0,
‑
1,0)、[17,18]及100%,从状态p7转换到状态p8的转换条件集tn为(0,0,
‑
1,0,0)、[0.5,0.5]及100%。将该概率混合有限状态机模型保存至本地电脑中。工作人员可以利用该概率混合有限状态机对反应釜的工艺流程进行监测和预警。
[0042]
以上述依据本发明的理想实施例为启示,通过上述的说明内容,相关工作人员完
全可以在不偏离本项发明技术思想的范围内,进行多样的变更以及修改。本项发明的技术性范围并不局限于说明书上的内容,必须要如权利要求范围来确定其技术性范围。