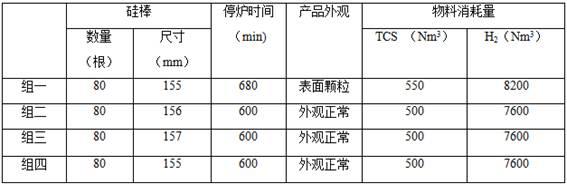
1.本发明属于多晶硅还原炉控制技术领域,具体的说,是一种还原炉停炉控制工艺及其系统和计算机可读存储介质。
背景技术:2.还原炉工艺是多晶硅生产过程中一项重要的工艺环节。在还原炉工艺中,高纯三氯氢硅汽化形成饱和蒸汽,与高纯氢气按比例混合后,在规定温度和流量的情况下送入还原炉中,在还原炉内通电的高温硅芯表面发生化学气相沉积反应,晶体硅沉积于硅芯表面使得硅棒直径不断变大,直至达到规定的直径,再停炉取出硅棒。在还原炉多晶硅的沉积过程中,还原炉的加热电流、物料流量、压力、气流分布等因素对硅棒质量都有较大影响,因此,需要对还原炉的运行过程进行精细化和严格化的控制。
3.还原炉运行过程的控制包括开炉、运行和停炉,其中,由于还原炉停炉工艺十分复杂,包括停炉前降电降气、停炉时降电降气、氢气空烧、降电流、提升氢气吹扫等诸多环节,这些环节中的操作均会对还原炉中电流、物料流量、压力、气流分布等因素造成影响。然而,现有还原炉的停炉工艺仍然采用人员手动操作,因此,还存在以下问题:(1)停炉工艺由人员操作易出现偏离或参数调整不方便的情况,例如:停炉时当炉内气流控制出现偏离或参数调整不及时,会使气流波动大,在硅棒表面长出鱼鳞,进一步还会影响炉内温差,导致裂棒甚至倒炉的风险。
4.(2)停炉工艺的具体控制参数由人员操作控制,易出现误操作的情况,例如:关错阀门造成还原炉憋压,安全阀起跳;或关错氢气阀门,导致硅棒雾化长鱼鳞甚至毛刺,影响产品质量;或关错冷却水阀,导致管道干烧,安全阀起跳或持续加热而造成漏管,等等。
5.(3)停炉工艺的安全确认项由操作人员进行确认,易出现遗忘而造成安全事故或延长拆炉时间。
6.基于上述情况,在实际生产过程中,为提高多晶硅产品质量,避免人员手动操作而造成产品质量下降及安全事故的情况,对现有还原炉停炉工艺进行合理、精确的控制是关键。
7.现有技术中,公布号为cn108394905a的发明专利公开了还原炉全自动平稳运行方法,在还原炉停炉时期,按照预设的氢气和三氯氢硅降料曲线坡度式减小氢气和三氯氢硅进料调节阀的开度,按照预设的降电流曲线坡度式降低输入硅棒的电流大小,以及依次进行氮气和氢气的置换并带走炉内残余物料及热量的过程,能够平滑均匀的降低反应物料的流量和电流量。该方法通过阀门开度的稳定调节,在一定程度上实现了还原炉停炉操作时物料流量的平稳运行,但仍然缺乏合理的还原炉停炉过程的控制工艺,为此,公布号为cn102608913a的发明专利公开了多晶硅生产还原炉停炉控制系统及其方法,通过计算生长完成硅棒所受到的最大磁力和最小释放应力,来优化还原炉停炉的工艺参数,如停炉时间和停炉温度,系统再根据该停炉时间和停炉温度控制还原炉进行停炉。但在实际操作时,计算出的当前应停炉时间往往并不是运行消耗的最优时间,同时,气相温度与硅棒温度会因
硅棒大小及气量大小而改变,而不是统一恒定的数据,因此,采用该还原炉停炉控制方法无法正常完成停炉,同时,也无法减小系统运行能耗。
技术实现要素:8.本发明的目的在于提供一种还原炉停炉控制工艺,按开始停炉和停炉阶段分别对h2进气量、tcs进气量和电流值进行程序控制,再进行降温冷却、气体置换后完成整个停炉过程,本发明还提供了该还原炉停炉控制系统和计算机可读存储介质,可根据控制工艺要求实现自动化的智能控制程序,大大降低了因人员操作不便或误操作等因素带来的产品质量和安全问题。
9.本发明通过下述技术方案实现:一种还原炉停炉控制工艺,包括以下步骤:s1.开始停炉,分别控制还原炉的h2进气阀、tcs进料阀和电流值,降低还原炉的h2进气量、tcs进气量和电流值;s2.停炉,逐渐关闭tcs进料阀,同时控制还原炉的h2进气阀和电流值,继续降低还原炉的h2进气量和电流值,保持该h2进气量和电流值使还原炉空烧,继续降低电流值至终点值,然后断电;s3.冷却置换,控制炉筒水对还原炉进行降温冷却后,控制还原炉的h2进气阀关闭后,将还原炉内的废气送至淋洗装置,并置换还原炉内的气体。
10.所述步骤s1中,在控制还原炉的h2进气阀时,判断开始停炉时的h2进气量,当h2进气量大于1400 nm3/h时,控制h2进气量在120min内降低至1400nm3/h,当h2进气量小于1400 nm3/h时,控制不执行;在控制还原炉的tcs进料阀时,判断开始停炉时的tcs进气量,当tcs进气量大于500nm3/h时,控制tcs进气量在120min内降低至500nm3/h,当tcs进气量小于500nm3/h时,控制不执行;在控制还原炉的电流值时,判断开始停炉时的电流值,当电流值大于1400a时,控制电流值在120min内降低至1400a,当电流值小于1400a时,控制不执行。
11.所述步骤s2中,停炉时,在10min内逐渐关闭tcs进料阀,同时控制还原炉的h2进气阀和电流值,在30min内将h2进气量降至800nm3/h,电流值降至1200a。
12.所述步骤s2中,还原炉空烧50min,在60min内降低电流值至500a,切断还原炉电源。
13.所述步骤s3中,还原炉的降温冷却步骤包括:a. 2min内关闭炉筒上水调节阀,再关闭炉筒上水切断阀,停止对炉筒进行加热;b. 打开炉筒排水泄压阀,待炉筒回水温度降至145℃后,关闭炉筒排水泄压阀,打开停炉上排水阀对炉筒进行冷却;c.5min内关闭底盘上水调节阀,再关闭底盘上水切断阀,停止对底盘进行加热。
14.所述步骤s3中,在断电240min后,控制还原炉的h2进气阀,1min内将h2进气量降至200
‑
300nm3/h后,关闭尾气系统连通阀门后,再关闭h2进气阀,将还原炉内的气体泄压至回收系统,泄压时关闭还原炉的混合气阀门,当还原炉压力为20kpa时,停止泄压,断开回收系统,开启废气淋洗阀,通过淋洗装置对还原炉内的剩余气体进行淋洗,淋洗时间控制在30min,淋洗结束后,关闭废气淋洗阀。
15.所述步骤s3中,按以下步骤对还原炉内的气体进行置换:a.开启氮气冲压阀对还原炉进行一次冲压,待还原炉压力>300kpa时,关闭氮气冲压阀,开启废气淋洗阀,泄压至淋洗装置,待还原炉压力高于淋洗装置压力20kpa时,关闭废气淋洗阀,完成一次泄压;b.开启真空泵后,控制真空阀开启,对还原炉抽真空,待还原炉压力<
‑
30kpa时,关闭真空泵和真空阀,完成一次抽真空;c.重复上述三步骤a、b,待泄压、抽真空三次后,完成对还原炉内气体的置换。
16.一种还原炉停炉控制系统,包括储存器、处理器以及存储在所述处理器上运行的计算机程序,所述处理器执行所述计算机程序时实现如上述任一项所述停炉控制工艺。
17.一种计算机可读存储介质,所述计算机可读存储介质储存有计算机程序,所述计算机程序被处理器执行时实现如上述任一项所述停炉控制工艺。
18.本发明与现有技术相比,具有以下优点及有益效果:(1)本发明将现有停炉过程分为开始停炉和停炉两个阶段,开始停炉时,通过智能化控制程序精确控制阀门开度与还原电气的电流给定,使开始停炉阶段中对还原炉的h2进气量、tcs进气量和电流值的控制更加稳定,再进入停炉阶段,分别对tcs进料阀、h2进气阀和电流值进行控制,在实现稳定、精确的操作控制的同时,通过对h2进气量、tcs进气量和电流值在开始停炉和停炉两个阶段中不同终点值的设定,进一步的对停炉工艺的进行优化,有利于多晶硅产品品质的提高,同时节约物料消耗,降低工艺成本。
19.(2)本发明利用智能化控制程序可实现还原炉停炉过程中自动控制,解决还原炉停炉过程中人员操作过多、干预频繁问题,降低人员工作量及防止误操作,实际生产过程中,通过dcs系统和还原电气plc之间的通信及控制,即可实现还原停炉过程的顺序化、流程化和自动化,极大地提高了停炉过程中的自动化控制程度。
20.综上所述,本发明提供了一种自动化控制的还原炉停炉工艺,通过对还原炉停炉工艺的改进,结合智能化控制程序,解决了人员操作还原炉停炉时的一系列操作失误或偏差,实现了还原炉停炉工艺的稳定化、精确化控制,能提高产品质量,缩短停炉时间约1小时,具有增效提产的明显优势。
具体实施方式
21.下面结合实施例对本发明作进一步地详细说明,但本发明的实施方式不限于此。
22.实施例1:本实施例是一种还原炉停炉控制工艺。
23.通过自动化控制程序和智能控制程序对还原炉停炉工艺进行控制,具体步骤如下:步骤一:开始停炉待硅棒生长结束后,自动化控制程序启动,通过智能控制程序对当前还原炉的h2进气量、tcs进气量和电流值进行判断,如下:当h2进气阀的h2进气量大于1400 nm3/h时,智能控制程序根据起点值及预先设定的终点值和周期,自动计算出斜率,获得按时间均匀控制的阀门开度(斜坡公式,下同),将该指令发送至自动化控制程序,来控制h2进气阀的阀门开度,使h2进气量在120min内均匀降
低至1400nm3/h;当h2进气量小于1400 nm3/h时,控制不执行。
24.当tcs进气量大于500nm3/h时,由智能控制程序将指令发送至自动化控制程序,来控制tcs进气阀的阀门开度,使tcs进气量在120min内均匀降低至500nm3/h;当tcs进气量小于500nm3/h时,控制不执行;当电流值大于1400a时,由智能控制程序将指令发送至自动化控制程序,来控制还原炉中通过硅棒的电流大小,使电流值在120min内均匀降低至1400a;当电流值小于1400a时,控制不执行。
25.步骤二:停炉智能控制程序根据预先设定的时间和终点值,将指令发送至自动化控制程序,分别控制tcs进料阀和h2进气阀的开度以及还原炉的电流大小,控制过程如下:停炉开始时,10min内逐渐关闭tcs进料阀,使tcs进气量均匀减小并归零;停炉开始的同时,控制还原炉的h2进气阀和电流值,使h2进气量在30min内均匀降至800nm3/h,电流值在30min内均匀降至1200a。
26.在tcs进气量为零、h2进气量为800nm3/h、电流值1200a的情况下,控制还原炉空烧50min,再控制还原炉的电流值,使电流值在60min内均匀降至500a,然后切断还原炉的电源,停炉完成。
27.步骤三:冷却置换(1)冷却降温待智能控制程序监测还原炉电源电流值小于1a后,向自动化控制程序发送指令,控制炉筒水对还原炉进行降温冷却,具体控制步骤如下:a. 2min内缓慢关闭炉筒上水调节阀,再关闭炉筒上水切断阀,停止对炉筒进行加热;b. 打开炉筒排水泄压阀,待炉筒回水温度降至145℃后,关闭炉筒排水泄压阀,打开停炉上排水阀对炉筒进行冷却;c.5min内逐渐关闭底盘上水调节阀,再关闭底盘上水切断阀,停止对底盘进行加热,冷却降温完成。
28.(2)废气淋洗智能控制程序进一步确认冷却水管线与炉筒、底盘之间的阀门已闭,此时自停炉完成共计240min。向自动化控制程序发送指令,进入废气淋洗过程,具体控制如下:控制还原炉的h2进气阀,1min内将h2进气量均匀降至200
‑
300nm3/h后,关闭尾气系统连通阀门后,再关闭h2进气阀。智能控制程序监测h2进气量为零,开启回收系统,将还原炉内的气体泄压至回收系统,泄压时关闭还原炉的混合气阀门,防止物料阀门内漏进还原炉,当还原炉与回收系统压力差小于20kpa时,停止泄压,断开回收系统,再开启氮气冲压阀和废气淋洗阀,通过淋洗装置对还原炉内的剩余气体进行淋洗,淋洗时间控制在30min,淋洗结束后,关闭氮气冲压阀和废气淋洗阀。
29.(3)气体置换废弃淋洗结束后,智能控制程序继续向自动化控制程序发送指令,进入气体置换过程,具体控制如下:a.开启氮气冲压阀对还原炉进行一次冲压,氮气进气量设置为500
‑
550nm3/h,待
还原炉压力>300kpa时,关闭氮气冲压阀,开启废气淋洗阀,泄压至淋洗装置,待还原炉压力高于淋洗装置压力20kpa时,关闭废气淋洗阀,并通过智能控制程序监测确认各阀门情况后,完成一次泄压,;b.开启真空泵后,控制真空阀开启,对还原炉抽真空,待还原炉压力<
‑
30kpa时,关闭真空泵和真空阀,完成一次抽真空;c.重复上述三步骤a、b,待泄压、抽真空三次后,完成对还原炉内气体的置换。
30.实施例2:本实施例是一种还原炉停炉控制系统。
31.该设备主要由存储器、处理器以及存储在处理器上运行的计算机程序组成,处理器执行该计算机程序时实现实施例1所述停炉控制工艺。。
32.实施例3:本实施例是一种计算机可读存储介质。
33.该计算机可读存储介质储存有计算机程序,该计算机程序被处理器执行时实现实施例1所述停炉控制工艺。
34.对现有还原大厅的某一还原炉进行电气和dcs系统改造,改造后按实施例1所述方法对还原炉的停炉工艺进行控制,与该还原炉改造前的停炉工艺进行比较,其数据如下表1所示。
35.改造前,该还原炉停炉时采用人员手动操作,具体控制步骤、温度和时间等数据均与实施例1相同,其数据参见组一。对该还原炉改造后,采用实施例1所述停炉工艺对还原炉进行自动停炉控制,其数据参见组二、组三、组四。(上述每组停炉过程均为同一还原炉在改造前和改造后进行的控制过程,且保证每次还原炉开炉及生长过程的工艺控制一致)表1以上所述,仅是本发明的较佳实施例,并非对本发明做任何形式上的限制,凡是依据本发明的技术实质对以上实施例所作的任何简单修改、等同变化,均落入本发明的保护范围之内。