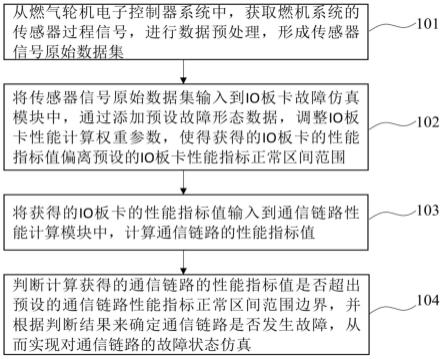
1.本发明涉及燃气轮机发电厂故障诊断技术领域,具体涉及一种燃气轮机控制系统电子控制器通信链路故障仿真方法。
背景技术:2.随着燃气轮机及其联合循环技术的日臻成熟,以及世界范围内天然气资源的大量开发及地球环保压力的日益严峻,燃气轮机发电不仅用作紧急备用电源和尖峰负荷,还作为清洁能源、分布式能源和基本负荷向电网输送电力。时至今日,燃气轮机在发电领域正在不断成长和迅猛发展;而在碳达峰碳中和的背景下,使用氢气作为燃料的燃气轮机发电,得到了空前重视和极大发展。
3.燃气轮机控制系统是由大量的零部件按一定的方式、功能和要求集合而成的复杂非线性动态系统。燃气轮机控制系统中的电子控制器(dcs系统),是整个燃机控制系统的核心和关键。如何对燃机控制系统的电子控制器进行有效地故障诊断,一直是工业界的难题。传统的基于bit技术的电子控制器故障诊断方法,需要在电子部件内增加大量冗余诊断电路,这一方面增加了系统成本,另一方面也增加了新的电子故障点。不同燃机控制系统的生产厂家,在各自的dcs系统中内置了很多专业的系统诊断功能,这些功能必须在具有相应权限的工程师操作站中才能查看到,并且信息获取的过程都是被动式的,需要操作人员自己到不同位置查找各种报警信息,然后再结合纸质版的各种图纸资料,甚至需要到dcs机柜内实际查看硬件指示状态,才能判断系统的故障点。要进一步判断发生故障的原因,则更多是工程师的个人能力和经验程度。这严重制约了燃机电厂在出现系统故障的快速判断,其结果是经常性出现因电子控制器系统误报警而导致的非计划停机,给电厂造成极大的经济损失。
4.dcs系统有高精度和高密度的电子元器件/芯片构成,各种元器件的工作原理和失效机制完全不同,其失效模式经常是
‘
突然式’,仅仅凭借日常的检查手段和测试手段根本无法有效解决故障检测问题。在燃气轮机的日常运行过程中,以最为重要的燃烧室的温度参数为例,该组参数(9f机组是31个圆周型排布的测点)的稳定性和一致性,直接关系到机组是否可以继续运行;一旦出现因通信链路故障造成测量值失真,就可能需要立刻停机,后果非常严重。
5.研究电子控制器通信链路的数据驱动故障诊断方法,缺少实际的故障样本是制约诊断算法发展和应用的主要瓶颈,如何有效获取有实用价值的故障样本,一直是工业界的难题。
技术实现要素:6.本发明的目的在于,针对上述现有技术的不足,提供一种燃气轮机控制系统电子控制器通信链路故障仿真方法,以解决燃气轮机控制系统中电子控制器的通信链路故障诊断问题中存在的故障样本难以获取、进而导致故障诊断方法无法有效验证的问题。
7.为实现上述目的,本发明采用的技术方案如下:
8.本发明提供了一种燃气轮机控制系统电子控制器通信链路故障仿真方法,该方法包括:
9.从燃气轮机电子控制器系统中,获取燃机系统的传感器过程信号,进行数据预处理,形成传感器信号原始数据集;
10.将传感器信号原始数据集输入到io板卡故障仿真模块中,通过添加预设故障形态数据,调整io板卡性能计算权重参数,使得获得的io板卡的性能指标值偏离预设的io板卡性能指标正常区间范围;
11.将获得的io板卡的性能指标值输入到通信链路性能计算模块中,计算通信链路的性能指标值;
12.判断计算获得的通信链路的性能指标值是否超出预设的通信链路性能指标正常区间范围边界,并根据判断结果来确定通信链路是否发生故障,从而实现对通信链路的故障状态仿真。
13.可选地,从燃气轮机电子控制器系统中,以opc ua工业协议,获取燃机系统的传感器过程信号。
14.可选地,从燃气轮机电子控制器系统中,以opc ua工业协议接口,从燃气轮机电子控制器dcs系统中获取与目标通信链路相关联的所有传感器的实时过程数据,数据预处理包括剔除冗余样本操作、去除异常样本操作以及数据归一化操作。
15.可选地,预设故障形态包括:突变偏移故障、短时干扰故障、时间偏移故障、周期性干扰故障和随机干扰故障;在io板卡故障仿真模块中,利用阶跃信号来仿真传感器信号发生突变偏移故障;利用脉冲信号来仿真传感器信号发生短时干扰故障;利用预定斜率的直线信号来仿真传感器信号发生时间偏移故障;利用周期正弦波信号来仿真传感器信号发生周期性干扰故障;利用高斯白噪声信号来仿真传感器信号发生随机干扰故障。
16.可选地,io板卡的性能指标值通过如下方式计算:
17.使用基于无迹卡尔曼滤波器的传感器残差序列加权平方和作为传感器的性能指标值,
[0018][0019]
∑=(diag(σ))2[0020]
其中ri是io板卡的第i个通道所对应的传感器的性能指标值,基于无迹卡尔曼滤波器,建立与io板卡相关联的m个传感器对应的滤波器,每个滤波器的输入均为m-1个测量参数值,第i个滤波器的输入是除第i个传感器之外的其余m-1个传感器测量参数,σ为测量参数的标准差,y(i)为第i个滤波器的测量参数,为第i个滤波器非线性模型预测输出;m为与io板卡相关联的传感器的总数;
[0021]
然后基于传感器的性能指标值,利用加权求和方式计算io板卡的性能指标值,
[0022][0023]
其中,r
io
为io板卡的性能指标值,ki是io板卡的第i个通道的加权权重。
[0024]
可选地,通信链路的性能指标值通过如下方式计算:
[0025]
将与通信链路相关联的所有io板卡的性能指标值加权求和,作为该通信链路的性能指标值,
[0026][0027]
其中,r
link
为通信链路的性能指标值,是通信链路的第i个io板卡的性能指标值,li为第i个io板卡的权重,n为与通信链路相关联的所有io板卡的总数。
[0028]
本发明的有益效果包括:
[0029]
本发明提供的燃气轮机控制系统电子控制器通信链路故障仿真方法包括:从燃气轮机电子控制器系统中,获取燃机系统的传感器过程信号,进行数据预处理,形成传感器信号原始数据集;将传感器信号原始数据集输入到io板卡故障仿真模块中,通过添加预设故障形态数据,调整io板卡性能计算权重参数,使得获得的io板卡的性能指标值偏离预设的io板卡性能指标正常区间范围;将获得的io板卡的性能指标值输入到通信链路性能计算模块中,计算通信链路的性能指标值;判断计算获得的通信链路的性能指标值是否超出预设的通信链路性能指标正常区间范围边界,并根据判断结果来确定通信链路是否发生故障,从而实现对通信链路的故障状态仿真。通过获得通信链路故障状态下的性能指标值,可用于通信链路进行故障状态诊断算法的设计验证,为燃气轮机控制系统回路故障诊断提供决策支持。
附图说明
[0030]
为了更清楚地说明本发明实施例中的技术方案,下面将对实施例或现有技术描述中所需要使用的附图作简单地介绍,显而易见地,下面描述中的附图仅仅是本发明的一些实施例,对于本领域普通技术人员来讲,在不付出创造性劳动的前提下,还可以根据这些附图获得其他的附图。
[0031]
图1示出了本发明实施例提供的燃气轮机控制系统电子控制器通信链路故障仿真方法的流程示意图;
[0032]
图2示出了本发明实施例提供的燃气轮机控制系统电子控制器通信链路故障仿真实验装置的示意图;
[0033]
图3示出了本发明实施例提供的燃气轮机控制系统电子控制器通信链路故障仿真方法的实际操作流程示意图。
具体实施方式
[0034]
下面将结合本发明实施例中的附图,对本发明实施例中的技术方案进行清楚、完整地描述,显然,所描述的实施例仅仅是本发明一部分实施例,而不是全部的实施例。基于本发明中的实施例,本领域普通技术人员在没有作出创造性劳动前提下所获得的所有其他实施例,都属于本发明保护的范围。
[0035]
燃气轮机控制系统中的电子控制器,是高度集成的电子元器件构成的复杂系统,
基于bit的故障诊断方法,不但实施成本高,而且新增加的故障诊断回路,一方面增加了系统的复杂度,另外也额外增加了系统出现故障的概率。基于数据的故障诊断方法,是最近的研究热点。但基于数据的故障诊断方法,需要有大量高质量的故障样本,用于算法训练和验证。工业现场无法产生足够的故障样本(这很容易理解,如果工业现场的故障样本很丰富,那说明该工艺方法不成熟,也就不可能获得广泛工业应用),这导致基于数据的故障诊断方法往往只能在实验室环境下表现良好,而无法真正用于工业现场。
[0036]
为了解决上述问题,本发明给出了一种方便可行的通信链路故障仿真方法。
[0037]
图1示出了本发明实施例提供的燃气轮机控制系统电子控制器通信链路故障仿真方法的流程示意图,如图1所示,本发明提供的燃气轮机控制系统电子控制器通信链路故障仿真方法包括:
[0038]
步骤101、从燃气轮机电子控制器系统中,获取燃机系统的传感器过程信号,进行数据预处理,形成传感器信号原始数据集。
[0039]
例如,从使用天然气燃料的9f机组燃气轮机控制系统电子控制器系统中,获取燃机系统的传感器过程信号。
[0040]
步骤102、将传感器信号原始数据集输入到io板卡故障仿真模块中,通过添加预设故障形态数据,调整io板卡性能计算权重参数,使得获得的io板卡的性能指标值偏离预设的io板卡性能指标正常区间范围。也就是说,通过将叠加了故障信号的数据,输入到io板卡性能指标值计算模型中,获得io板卡的性能指标值。
[0041]
步骤103、将获得的io板卡的性能指标值输入到通信链路性能计算模块中,计算通信链路的性能指标值;
[0042]
步骤104、判断计算获得的通信链路的性能指标值是否超出预设的通信链路性能指标正常区间范围边界,并根据判断结果来确定通信链路是否发生故障,从而实现对通信链路的故障状态仿真。
[0043]
基于电子控制器通信链路出现故障后,该链路相关传感器的信号状态会出现异常,通信链路出现故障的第一反应就是上述这些传感器信号异常。本发明利用在传感器信号数据中叠加故障信号的方式,实现io板卡的性能指标值异常,进而实现通信链路性能指标值的异常,从而仿真通信链路故障状态下的形态。使用本方法可以很方便地产生大量故障样本,解决了电子控制器通信链路故障诊断的样本缺失问题,为进一步的通信链路故障诊断提供了基础。通过获得通信链路故障状态下的性能指标值,可用于通信链路进行故障状态诊断算法的设计验证,为燃气轮机控制系统回路故障诊断提供决策支持。
[0044]
可选地,从燃气轮机电子控制器系统中,以opc ua工业协议,连接到燃气轮机电子控制器系统的opc server数据源,获取燃机系统的传感器过程信号。
[0045]
可选地,从燃气轮机电子控制器系统中,以opc ua工业协议接口,从燃气轮机电子控制器dcs系统中获取与目标通信链路相关联的所有传感器的实时过程数据,数据预处理包括剔除冗余样本操作、去除异常样本操作以及数据归一化操作,将数据转换成0均值、1方差的高斯分布形态。
[0046]
可选地,预设故障形态包括:突变偏移故障、短时干扰故障、时间偏移故障、周期性干扰故障和随机干扰故障;在io板卡故障仿真模块中,利用阶跃信号来仿真传感器信号发生突变偏移故障;利用脉冲信号来仿真传感器信号发生短时干扰故障;利用预定斜率的直
线信号来仿真传感器信号发生时间偏移故障(温漂);利用周期正弦波信号来仿真传感器信号发生周期性干扰故障(如大功率电气设备干扰);利用高斯白噪声信号来仿真传感器信号发生随机干扰故障(如接地不良/接触不良等)。
[0047]
可选地,io板卡的性能指标值通过如下方式计算:
[0048]
使用基于无迹卡尔曼滤波器的传感器残差序列加权平方和作为传感器的性能指标值,
[0049][0050]
∑=(diag(σ))2[0051]
其中ri是io板卡的第i个通道所对应的传感器的性能指标值,基于无迹卡尔曼滤波器,建立与io板卡相关联的m个传感器对应的滤波器,每个滤波器的输入均为m-1个测量参数值,第i个滤波器的输入是除第i个传感器之外的其余m-1个传感器测量参数,σ为测量参数的标准差,y(i)为第i个滤波器的测量参数,为第i个滤波器非线性模型预测输出;m为与io板卡相关联的传感器的总数。
[0052][0053]
由上式可知,无迹卡尔曼滤波器可以根据燃气轮机的测量参数yk与非线性模型预测输出的残差来估计参数p,并通过更新非线性模型的参数,使得模型的输出参数跟踪真实燃气轮机的输出,实现对燃气轮机参数的估计。
[0054]
然后基于传感器的性能指标值,利用加权求和方式计算io板卡的性能指标值,
[0055][0056]
其中,r
io
为io板卡的性能指标值,ki是io板卡的第i个通道的加权权重。
[0057]
可选地,通信链路的性能指标值通过如下方式计算:
[0058]
将与通信链路相关联的所有io板卡的性能指标值加权求和,作为该通信链路的性能指标值,
[0059][0060]
其中,r
link
为通信链路的性能指标值,是通信链路的第i个io板卡的性能指标值,li为第i个io板卡的权重,n为与通信链路相关联的所有io板卡的总数。
[0061]
图2示出了本发明实施例提供的燃气轮机控制系统电子控制器通信链路故障仿真实验装置的示意图。图3示出了本发明实施例提供的燃气轮机控制系统电子控制器通信链路故障仿真方法的实际操作流程示意图。具体的实际燃气轮机控制系统通信链路的故障仿真流程如图3所示。
[0062]
基于电子控制器通信链路出现故障后,系统所采集的传感器信号状态会出现异常,比如数值突然跳变(阶跃故障)、数值突然跳变后又恢复正常(脉冲故障)、数值持续变大或变小(时变/温漂故障)、数值中有周期性干扰(经常是因为板卡中有强电感应信号串入)、或者信号稳定性变差(白噪声干扰,经常是因为接触不良或接地异常造成)。通信链路出现故障的第一反应就是上述这些传感器信号异常,本发明利用在传感器信号数据中叠加故障信号的方式,使得与通信链路相关联的io板卡的性能指标值出现异常,进而导致通信链路的性能指标值超出正常区间范围,从而实现了对通信链路故障状态的仿真。该方法可以很方便地产生大量故障样本,解决了电子控制器通信链路故障诊断的样本缺失问题,为进一步的通信链路故障诊断提供了基础。
[0063]
上述实施例只为说明本发明的技术构思及特点,其目的在于让本领域普通技术人员能够了解本发明的内容并加以实施,并不能以此限制本发明的保护范围,凡根据本发明精神实质所作的等效变化或修饰,都应涵盖在本发明的保护范围内。