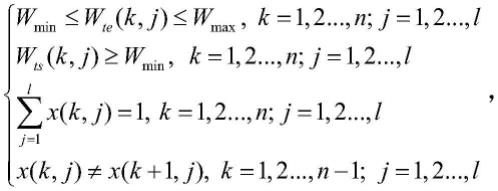
1.本发明属于冶金自动化技术领域,更具体地,涉及一种基于优化的混匀配料仓自动供料的时序编制方法。
背景技术:2.由于我国矿源的多样性,钢铁企业原料场通常需要将十几种甚至几十种不同种类的原料通过一定比例均匀混合,来满足烧结矿的质量需求。原料场混匀配料工艺包含两个过程:第一个是一次料场的取料作业,在一次料场掘取对应的原料并通过皮带运送到混匀配料槽暂存;第二个过程是混匀配料槽按照配方比例通过圆盘给料机设置不同的下料速度并将配料槽的原料下放至同一条皮带上,由皮带将矿石原料运输至混匀料场的堆料机制成混匀料堆。其中混匀配料槽一般包含多个料仓,每个配料槽会装配1~2个加料小车给各个料仓供料,每个加料小车则对应1~2个取料机。由于混匀配比不同,各个料仓原料的下料速度也不同,因此如何合理的调度各个加料小车和取料机,确保各个料仓不空仓的情况下尽量减少能耗是提高原料场运行效率的关键。
3.目前钢铁企业原料场多采用人工时序编制的方式来给各个料仓供料,这种方式依赖人工经验,容易出现调度不及时,料仓空仓导致混匀成分与预期差别大的情况,且不易控制运行成本。近年来,也有通过自动化的方法计算加料时序,但是无法确保不出现空仓,也没有考虑加料小车和取料机的运行效率的问题,这个环节还有很大的提升空间。
4.综上所示,研发混匀料仓自动供料时序编制方法以避免料仓空仓,保证原料混匀质量,同时提高自动供料过程的运行效率是进一步提高混匀料场能效和生产水平的一个关键环节。
技术实现要素:5.针对现有技术的以上缺陷或改进需求,本发明提出了一种基于优化的混匀配料仓自动供料的时序编制方法,通过建立混匀配料的数学模型,预测后续多个任务周期的系统状态,来建立以料仓内原料重量为约束条件,以供料效率最优为性能指标的自动供料时序编制优化问题,并求解符合需求的自动供料的时序。
6.为实现上述目的,本发明提供了一种基于优化的混匀配料仓自动供料的时序编制方法,包括:
7.获取混匀料仓系统的参数信息和状态信息,并根据实际设备状态和参数建立对应的混匀料仓系统的数学模型,以预测后续多个任务周期的系统状态;
8.以料仓内原料重量为约束条件,以预测时间内加料小车加料的原料量最大为优化目标,建立性能指标函数;
9.以加仓序列为决策变量,以性能指标函数为优化目标设计整数遗传算法,对每个遗传算法的种群,均以对偶单纯形法计算最大加仓重量,得到优化的加仓序列;
10.将优化的加仓序列,带入到混匀料仓系统的数学模型中,将原始的非线性混合整
数优化模型转换成线性规划模型,使用对偶单纯形法求解线性规划模型得到每个加料任务的起始时刻和结束时刻;
11.综合优化的加仓序列和每个加料任务的起始时刻和结束时刻,得到自动供料的时序。
12.在一些可选的实施方案中,所述混匀料仓系统的参数信息包括:混匀料仓数量l,混匀料仓内原料重量的上限w
max
,料仓原料重量的下限w
min
,相邻料仓之间的距离d,加料小车的数量nc,每个加料小车对应的取料机的数量mr,料仓和对应品种料堆之间的皮带长度。
13.在一些可选的实施方案中,所述混匀料仓系统的状态信息包括:料仓内原料品种,料仓内的原料重量w,料仓的下料流量f-,加料小车的移动速度vc,加料小车的加料流量f
+
,取料机的移动速度vr,加料小车的位置pc,取料机的位置pr。
14.在一些可选的实施方案中,获取混匀料仓系统的参数信息和状态信息,并根据实际设备状态和参数建立对应的混匀料仓系统的数学模型,包括:
15.设x(i,j)表示第i个任务第j个料仓是否加料,0表示不加料,1表示加料,ts(i)表示第i个任务加料的起始时刻,te(i)表示第i个任务加料的结束时刻,第j个料仓的初始重量为w(0,j);
16.由w
ts
(k,j)=w
te
(k-1,j)-f-·
(ts(k)-te(k-1))得到第k个任务加料起始时刻,第j个料仓内原料重量w
ts
(k,j),其中,w
te
(k-1,j)表示第k-1个任务加料结束时刻,第j个料仓内原料重量,f-·
(ts(k)-te(k-1))表示第k-1个任务加料的结束时刻te(k-1)和第k个任务加料的起始时刻ts(k)这段时间内料仓的下料量;
17.由w
te
(k,j)=w
ts
(k,j)-f-·
(te(k)-ts(k))+f
+
·
(te(k)-ts(k))
·
x(k,j)得到第k个任务加料结束时刻,第j个料仓内原料重量w
te
(k,j),其中,f-·
(te(k)-ts(k))表示第k个任务加料的结束时刻te(k)与第k个任务加料的起始时刻ts(k)这段时间内料仓的下料量,f
+
·
(te(k)-ts(k))表示第k个任务加料的结束时刻te(k)与第k个任务加料的起始时刻ts(k)这段时间内料仓的加料量,x(k,j)表示第k个任务第j个料仓是否加料,0表示不加料,1表示加料;
18.由得到tk时刻,第i个加料小车的位置pc(i,tk),其中,pc(i,0)表示第i个加料小车的初始位置,vc表示加料小车的移动速度;
19.由得到tk时刻,第i个取料机的位置pr(i,tk),其中,pr(i,0)表示第i个取料机的初始位置,vr表示取料机的移动速度;
20.根据每个料仓的品种、品种对应料堆位置以及皮带速度计算原料从料堆运输到料仓所需要的时间。
21.在一些可选的实施方案中,所述约束条件为:n表示预测的任务周期数,l表示混合料仓数
量。
22.在一些可选的实施方案中,所述性能指标函数为:其中,f
+
(k)表示第k个任务加料小车的加料流量。
23.在一些可选的实施方案中,所述方法还包括:
24.监测系统状态变化,若出现影响料仓序列的状态发生变化,则重新计算加料的料仓序列和加料任务的起始时刻和结束时刻,若没有出现影响料仓序列的状态发生变化,则使用当前的供料时序直到完成整个混匀造堆过程。
25.总体而言,通过本发明所构思的以上技术方案与现有技术相比,能够取得下列有益效果:
26.通过建立混匀配料的数学模型,预测后续多个任务周期的系统状态,来建立以料仓内原料重量为约束条件,以供料效率最优为性能指标的自动供料时序编制优化问题,并通过设计遗传算法和对偶单纯形法求解料仓的加料序列以及每个加料任务的起始时间和终止时间完成自动供料时序的编制。可以解决原料场混匀配料工艺中料仓自动供料的时序编制,可以避免混匀过程中料仓出现空仓影响混匀料品质的问题,同时提高系统运行效率。
附图说明
27.图1是本发明实施例提供的一种基于优化的混匀配料仓自动供料的时序编制方法的实施流程图;
28.图2是本发明实施例提供的一种各个料仓内原料重量变化的曲线图。
具体实施方式
29.为了使本发明的目的、技术方案及优点更加清楚明白,以下结合附图及实施例,对本发明进行进一步详细说明。应当理解,此处所描述的具体实施例仅仅用以解释本发明,并不用于限定本发明。此外,下面所描述的本发明各个实施方式中所涉及到的技术特征只要彼此之间未构成冲突就可以相互组合。
30.本实施例公开的是某钢铁企业基于优化的混匀配料仓自动供料的时序编制方法,由于人工调度的方法依赖操作经验,容易出现空仓的情况,影响混匀质量和效率,且不易控制生产能耗。如何合理制定混匀配料仓自动供料的时序,保证不发生空仓断料情况,并尽可能提高混匀过程运行效率成为企业亟需解决的问题。
31.如图1所示,本发明实施例提供的基于优化的混匀料仓自动供料的时序编制方法,包含以下步骤:
32.s001.获取系统的参数信息;
33.在本发明实施例中,混匀料槽包括11个混匀料仓,分别记为1#、2#...11#。料仓内原料重量的上限w
max
=[736,736,736,736,736,736,736,736,520,520,520]t、料仓原料重量的下限w
min
=50t、各个相邻料仓中心之间的距离d=10m,加料小车的数量nc=1、每个加料小车对应取料机的数量mr=2。
[0034]
s002.读取系统的状态信息,状态信息包括:料仓内原料品种,以向量记为c,料仓内的原料重量,w=0.8*w
max
,料仓的下料流量f-=[100,150,100,150,150,50,50,100,50,
50,50]t/h,加料小车的移动速度vc=0.5m/s,加料小车的加料流量f
+
=2000t/h,取料机的移动速度vr=0.6m/s,加料小车的位置pc=[114,25]m,取料机的位置pr=[51,121]m。
[0035]
s003.设x(i,j)表示第i个任务第j个料仓是否加料,0表示不加料,1表示加料,ts(i)表示第i个任务加料的起始时刻,te(i)表示第i个任务加料的结束时刻,第j个料仓的初始重量为w(0,j),建立混匀料仓的数学模型,具体如下:
[0036]
步骤3.1)第k个任务加料起始时刻,第j个料仓内原料重量:
[0037]wts
(k,j)=w
te
(k-1,j)-f-·
(ts(k)-te(k-1))
ꢀꢀꢀꢀꢀꢀꢀꢀꢀꢀꢀꢀꢀꢀꢀꢀꢀꢀꢀꢀ
(1)
[0038]
步骤3.2)根据步骤3.1)中的公式进行递推,得:
[0039][0040]
步骤3.3)第k个任务加料结束时刻,第j个料仓内原料重量:
[0041]wte
(k,j)=w
ts
(k,j)-f-(te(k)-ts(k))+f
+
(te(k)-ts(k))
·
x(k,j)
ꢀꢀꢀꢀꢀꢀꢀꢀꢀꢀꢀꢀ
(3)
[0042]
步骤3.4)根据步骤3.3)中的公式递推,得:
[0043][0044]
步骤3.5)tk时刻,第i个加料小车的位置:
[0045][0046]
步骤3.6)tk时刻,第i个取料机的位置:
[0047][0048]
步骤3.7)根据每个料仓的品种、品种对应料堆位置以及皮带速度计算原料从料堆运输到料仓所需要的时间。
[0049]
s004.设置约束条件:为了避免混匀过程中料仓出现空仓的情况,设置对应的约束条件如下:
[0050][0051]
s005.设置性能指标函数:以预测时间内加仓小车加料的原料量最大为优化目标,建立性能指标函数如下:
[0052][0053]
其中f
+
(k)表示加料小车在第k个仓的加料流量,预测周期n设置为36。
[0054]
s006.以加仓序列x(k,j)为决策变量,以步骤s005中建立的性能指标为优化目标设计整数遗传算法,对每个遗传算法的种群,均以对偶单纯形法计算最大加仓重量,得到优化的加仓序列;
[0055]
s007.将步骤s006中得到的加仓序列,带入到步骤s003建立的混匀料仓的数学模型中,将原始的非线性混合整数优化模型转换成线性规划模型,使用对偶单纯形法求解这个线性规划模型得到每个加料任务的起始时刻ts(k)和结束时刻te(k);
[0056]
s008.综合步骤s006计算的加仓序列和步骤s007计算的加仓起始和结束时刻,即可得到自动供料的时序;
[0057]
s009.监测系统状态变化,如果出现影响料仓序列的状态发生变化,如料仓品种、下料流量等,则跳转到步骤s006,重新计算加料的料仓序列和加料任务的起始结束时刻,如果没有出现这种变化,则使用该供料时序直到完成整个混匀造堆过程,如图2所示,反映了1#、2#...11#料仓内原料重量变化的曲线图。
[0058]
需要指出,根据实施的需要,可将本技术中描述的各个步骤/部件拆分为更多步骤/部件,也可将两个或多个步骤/部件或者步骤/部件的部分操作组合成新的步骤/部件,以实现本发明的目的。
[0059]
本领域的技术人员容易理解,以上所述仅为本发明的较佳实施例而已,并不用以限制本发明,凡在本发明的精神和原则之内所作的任何修改、等同替换和改进等,均应包含在本发明的保护范围之内。