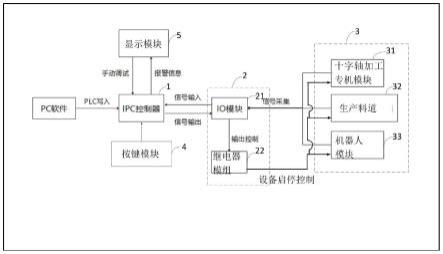
一种基于ipc的十字轴专机自动化生产控制系统
技术领域
1.本发明涉及生产控制领域,尤其是涉及一种基于ipc的十字轴专机自动化生产控制系统。
背景技术:2.在电气工程领域应用智能化技术,能够替代人工作业,降低劳动强度和危险,电气工程自动化是目前发展的主要方向,加入智能技术,能够提高电气工程及其自动化的作用效果,提高工程质量和安全。
3.产品质量与准确性和可重复性息息相关。如果随着时间的推移计量不一致,则会影响产品的一致性。良好的工业自动化系统将帮助加工方确保每天制造出的产品一致性,同时监视产品质量和一致性中的故障或失败。
4.现有技术中,十字轴加工生产一般是由人工操作各种加工设备,例如,十字轴加工专机、上料料道、传输料道、机器人等,但是,需要人为对生茶加工设备进行近距离操作,不仅浪费人力成本,而且容易因为人为操作失误,导致人员(受伤)、产品(不一致)、设备(故障或异常)的风险,不利于提高十字轴加工生产的效率以及安全可靠性。
技术实现要素:5.本发明为了解决现有技术中存在的问题,创新提出了一种基于ipc的十字轴专机自动化生产控制系统,有效解决由于现有技术造成十字轴加工生产的效率以及安全可靠性低的问题,有效地提高了十字轴加工生产的效率以及安全可靠性。
6.本发明提供了一种基于ipc的十字轴专机自动化生产控制系统,包括:ipc控制器、io控制单元、自动化生产单元,所述自动化生产单元包括十字轴加工专机模块、生产料道及机器人模块,所述ipc控制器分别与十字轴加工专机模块、生产料道、机器人模块、io控制单元通信连接,用于分别获取十字轴加工专机模块、生产料道及机器人模块反馈的状态信号,并根据获取十字轴加工专机模块、生产料道及机器人模块反馈的状态信号生成对应的控制指令,并将生成对应的控制指令通过io控制单元发送至对应的十字轴加工专机模块、生产料道及机器人模块;十字轴加工专机模块、生产料道及机器人模块根据接收到的对应的控制指令,控制自身执行对应的操作;其中,十字轴加工专机模块至少包括第一十字轴加工专机以及第二十字轴加工专机,所述第一十字轴加工专机用于对待加工的十字轴进行第一工序加工,所述第二十字轴加工专机用于对待加工的十字轴进行第一工序加工之后的第二工序加工。
7.可选地,io控制单元包括io模块以及继电器模组,所述io模块的数据通信端与ipc控制器通信连接,信号输出端通过继电器模组与自动化生产单元中的十字轴加工专机模块、生产料道及机器人模块分别通信连接,信号输入端与自动化生产单元中的十字轴加工专机模块、生产料道及机器人模块分别通信连接,用于将获取十字轴加工专机模块、生产料道及机器人模块反馈的状态信号反馈至ipc控制器,并将ipc控制器生成对应的控制指令通
过继电器模组发送至对应的十字轴加工专机模块、生产料道及机器人模块。
8.可选地,生产料道包括振动盘、成品料道、转运料道,所述振动盘包括振动盘料道,所述振动盘用于将振动盘内部的振动盘料道中待加工的十字轴经过机器人模块输送至第一十字轴加工专机;所述转运料道用于将经过第一十字轴加工专机进行第一加工工序加工后的十字轴转运至第二十字轴加工专机处,所述成品料道用于存放经过第二十字轴加工专机加工后的十字轴成品。
9.进一步地,振动盘还包括胚料不足传感器、气缸顶伸传感器、第一有料检测传感器,所述胚料不足传感器设置在振动盘料道入口处,用于检测振动盘料道入口处是否有待加工的十字轴通过,在预设时间周期内未检测到有待加工的十字轴通过时,提示坯料不足,由ipc控制器控制,实现振动盘自行启动上料进入振动盘料道;所述气缸顶伸传感器设置在振动盘料道出口侧,用于检测振动盘料道中是否有待加工的十字轴经过,在检测到有待加工的十字轴经过时,由ipc控制器控制,实现振动盘料道旁的气缸顶伸动作,拦截住后面的十字轴,并且振动盘停止上料;所述第一有料检测传感器设置在振动盘出口末端定位机构,用于检测振动盘出口末端是否有待加工的十字轴,在检测振动盘出口没有待加工的十字轴后,由ipc控制器控制,实现振动盘重复上料动作。
10.进一步地,所述机器人模块至少包括第一机器人、第二机器人以及第三机器人,所述第一机器人用于抓取振动盘出口末端处的待加工的十字轴,并将抓取的待加工的十字轴放置于第一十字轴加工专机的待加工区域;所述第二机器人用于抓取经过第一十字轴加工专机第一加工工序完成后的十字轴,并将抓取第一加工工序完成后的十字轴放置于转运料道,抓取第二十字轴加工专机第二加工工序完成后的十字轴成品,并将抓取的第二加工工序完成后的十字轴成品放置于成品料道;所述第三机器人用于抓取转运处的第一加工工序完成后的十字轴,并将抓取的第一加工工序完成后的十字轴放置于第二十字轴加工专机的待加工区域。
11.进一步地,根据获取十字轴加工专机模块、生产料道及机器人模块反馈的状态信号生成对应的控制指令具体包括:取料控制指令、放料控制指令;
12.其中,取料控制指令包括:
13.当第一有料检测传感器发送检测到有待加工的十字轴的状态信号后,ipc控制器通过取料控制指令控制第一机器人从振动盘末端取料并放至第一十字轴加工专机的安全位置等待;当第一十字轴加工专机发送第一加工工序的完成信号后,ipc控制器通过取料控制指令控制第二机器人从第一十字轴加工专机工作台上抓取十字轴至转运料道安全位置等待;当第二十字轴加工专机发送第二加工工序的完成信号后,ipc控制器通过取料控制指令控制第二机器人从第二十字轴加工专机工作台上抓取十字轴成品并放至成品料道安全位置等待;当设置于转运料道末端的第二有料检测传感器发送检测到有第一加工工序完成的十字轴的状态信号后,ipc控制器通过取料控制指令控制第三机器人从转运料道末端取料并放至第二十字轴加工专机的安全位置等待;
14.其中,放料控制指令包括:
15.当第一十字轴加工专机发送允许放料信号且第一机器人发送放料等待信号后,ipc控制器通过放料控制指令控制第一机器人执行放料动作;并在放料完成后,控制第一机器人返回取料等待位置;当设置于转运料道末端的第二有料检测传感器发送检测到没有第
一加工工序完成的十字轴的状态信号且第二机器人发送放料等待信号后,ipc控制器通过放料控制指令控制第二机器人执行放料动作;并在放料完成后,控制第二机器人返回取料等待位置;当设置于成品料道末端的第三有料检测传感器发送检测到没有第二加工工序完成的十字轴成品的状态信号且第二机器人发送放料等待信号后,ipc控制器通过放料控制指令控制第二机器人执行放料动作;并在放料完成后,控制第二机器人返回取料等待位置;当第二十字轴加工专机发送允许放料的状态信号且第三机器人发送放料等待信号后,ipc控制器通过放料控制指令控制第三机器人执行放料动作;并在放料完成后,控制第三机器人返回取料等待位置。
16.进一步地,根据获取十字轴加工专机模块、生产料道及机器人模块反馈的状态信号生成对应的控制指令还包括:加工控制指令;
17.其中,加工控制指令包括:
18.当第一机器人发送放料完成的状态信号后,ipc控制器通过加工控制指令控制第一十字轴加工专机执行一次第一加工工序的加工动作;当第三机器人发送放料完成的状态信号后,ipc控制器通过加工控制指令控制第二十字轴加工专机执行一次第二加工工序的加工动作;加工完成后,第一十字轴加工专机或第二十字轴加工专机退回到起始位置,并将允许取料信号通过ipc控制器间接反馈或直接反馈至第二机器人;
19.当第二机器人接收到第一十字轴加工专机的允许取料信号后,将经过第一加工工序加工后的十字轴夹取至转运料道指定位置,当第二机器人接收到第二十字轴加工专机的允许取料信号后,将经过第二加工工序加工后的十字轴夹取至成品料道指定位置,并分别将允许放料信号通过ipc控制器间接反馈或直接反馈至第一机器人以及第二机器人。
20.进一步地,根据获取十字轴加工专机模块、生产料道及机器人模块反馈的状态信号生成对应的控制指令还包括:料道输送控制指令;
21.其中,料道输送控制指令具体包括:
22.当第二机器人发送放料完成的状态信号后,ipc控制器通过料道输送控制指令控制第二机器人放料对应的转运料道或成品转动设定的距离后停止,用于将转运料道中经过第一加工工序的十字轴传输至转运料道末端,等待第三机器人抓取,并在第三机器人抓取后返回转运料道起始位置,等待第二机器人再次放料;或,将成品料道中经过第二加工工序的十字轴成品传输至成品料道末端,等待收取,并在收取后返回成品料道起始位置,等待第二机器人再次放料。
23.可选地,还包括按键模块,所述按键模块的数据输出端与ipc控制器的数据输入端通信连接,用于十字轴加工专机模块、生产料道及机器人模块的启动、暂停、急停、复位控制。
24.可选地,还包括显示模块,所述显示模块的数据输入端与ipc控制器的数据输出端通信连接,用于显示十字轴加工专机模块、生产料道及机器人模块反馈的状态信息。
25.本发明采用的技术方案包括以下技术效果:
26.1、本发明ipc控制器分别获取十字轴加工专机模块、生产料道及机器人模块反馈的状态信号,并根据获取十字轴加工专机模块、生产料道及机器人模块反馈的状态信号生成对应的控制指令,并将生成对应的控制指令通过io控制单元发送至对应的十字轴加工专机模块、生产料道及机器人模块,有效解决由于现有技术造成十字轴加工生产的效率以及
安全可靠性低的问题,有效地提高了十字轴加工生产的效率以及安全可靠性。
27.2、本发明技术方案中振动盘料道还包括胚料不足传感器、气缸顶伸传感器、第一有料检测传感器,可以实现基于胚料不足传感器、气缸顶伸传感器、第一有料检测传感器,振动盘自行启动、停止上料;并且通过气缸顶伸传感器在检测到有待加工的十字轴经过时,由ipc控制器控制,实现振动盘料道旁的气缸顶伸动作,拦截住后面的十字轴,并且振动盘停止上料,有效防止了两个及以上十字轴堆积在末端定位机构,造成机器人取料时夹爪压到其他的十字轴而引发机器人臂电机过流故障和报警。
28.3、本发明技术方案中还包括按键模块,可以实现十字轴加工专机模块、生产料道及机器人模块的启动、暂停、急停、复位控制。
29.4、本发明技术方案中还包括显示模块,可以实时显示十字轴加工专机模块、生产料道及机器人模块反馈的状态信息,便于维护人员及时了解十字轴加工专机模块、生产料道及机器人模块的状态信息。
30.应当理解的是以上的一般描述以及后文的细节描述仅是示例性和解释性的,并不能限制本发明。
附图说明
31.为了更清楚说明本发明实施例或现有技术中的技术方案,下面将对实施例或现有技术描述中所需要使用的附图作简单介绍,显而易见的,对于本领域普通技术人员而言,在不付出创造性劳动的前提下,还可以根据这些附图获得其他的附图。
32.图1为本发明方案中实施例一系统的结构示意图;
33.图2为本发明方案中实施例一系统中十字轴加工专机模块、生产料道及机器人模块之间的加工流程示意图。
具体实施方式
34.为能清楚说明本方案的技术特点,下面通过具体实施方式,并结合其附图,对本发明进行详细阐述。下文的公开提供了许多不同的实施例或例子用来实现本发明的不同结构。为了简化本发明的公开,下文中对特定例子的部件和设置进行描述。此外,本发明可以在不同例子中重复参考数字和/或字母。这种重复是为了简化和清楚的目的,其本身不指示所讨论各种实施例和/或设置之间的关系。应当注意,在附图中所图示的部件不一定按比例绘制。本发明省略了对公知组件和处理技术及工艺的描述以避免不必要地限制本发明。
35.实施例一
36.如图1-图2所示,本发明提供了一种基于ipc的十字轴专机自动化生产控制系统,包括:ipc控制器1、io控制单元2、自动化生产单元3,自动化生产单元3包括十字轴加工专机模块31、生产料道32及机器人模块33,ipc控制器1分别与十字轴加工专机模块31、生产料道32、机器人模块33、io控制单元2通信连接,用于分别获取十字轴加工专机模块31、生产料道32及机器人模块33反馈的状态信号,并根据获取十字轴加工专机模块31、生产料道32及机器人模块33反馈的状态信号生成对应的控制指令,并将生成对应的控制指令通过io控制单元2发送至对应的十字轴加工专机模块31、生产料道32及机器人模块33;十字轴加工专机模块31、生产料道32及机器人模块33根据接收到的对应的控制指令,控制自身执行对应的操
作;其中,十字轴加工专机模块31至少包括第一十字轴加工专机(一号专机或专机1)以及第二十字轴加工专机(二号专机或专机2),第一十字轴加工专机(一号专机)用于对待加工的十字轴进行第一工序加工,第二十字轴加工专机(二号专机)用于对待加工的十字轴进行第一工序加工之后的第二工序加工。
37.其中,io控制单元2包括io模块21以及继电器模组22,io模块21的数据通信端与ipc控制器1通信连接,信号输出端通过继电器模组22与自动化生产单元3中的十字轴加工专机模块31、生产料道32及机器人模块33分别通信连接,信号输入端与自动化生产单元3中的十字轴加工专机模块31、生产料道32及机器人模块33分别通信连接,用于将获取十字轴加工专机模块31、生产料道32及机器人模块33反馈的状态信号反馈至ipc控制器1,并将ipc控制器1生成对应的控制指令通过继电器模组22发送至对应的十字轴加工专机模块31、生产料道32及机器人模块33,实现对十字轴加工专机模块31、生产料道32及机器人模块33的启停控制。
38.其中,生产料道32包括振动盘、成品料道、转运料道,振动盘包括振动盘料道(振动盘内部的一部分),振动盘用于将振动盘内部的振动盘料道中待加工的十字轴经过机器人模块33中的第一机器人(1号机器人)输送至第一十字轴加工专机(一号专机);转运料道用于将经过第一十字轴加工专机(一号专机)进行第一加工工序加工后的十字轴转运至第二十字轴加工专机(二号专机)处,成品料道用于存放经过第二十字轴加工专机(二号专机)加工后的十字轴成品。
39.进一步地,振动盘还包括胚料不足传感器、气缸顶伸传感器、第一有料检测传感器,胚料不足传感器设置在振动盘料道入口处,用于检测振动盘料道入口处是否有待加工的十字轴通过,在预设时间周期内未检测到有待加工的十字轴通过时,提示坯料不足,由ipc控制器1控制,实现振动盘自行启动上料进入振动盘料道,十字轴在振动盘中工序为:振动盘
→
振动盘料道
→
振动盘出口;气缸顶伸传感器设置在振动盘料道出口侧,用于检测振动盘料道中是否有待加工的十字轴经过,在检测到有待加工的十字轴经过时,由ipc控制器1控制,实现振动盘料道旁的气缸顶伸动作,拦截住当前待加工的十字轴后面的十字轴,并且振动盘停止上料,即振动盘停止将待加工的十字轴振动进入振动盘料道;第一有料检测传感器设置在振动盘出口末端定位机构,用于检测振动盘出口末端是否有待加工的十字轴,在检测振动盘出口没有待加工的十字轴后(机器人模块中的第一机器人,即第一机器人取料完成),由ipc控制器1控制,实现振动盘重复上料动作。
40.具体地,胚料不足传感器可以采用德力西直流型npn型接近开关,感应距离为5mm;气缸顶伸传感器可以采用德力西直流型npn型接近开关,感应距离为2mm;第一有料检测传感器可以采用德力西直流型npn型接近开关,感应距离为2mm。
41.其中,机器人模块33至少包括第一机器人(1号机器人)、第二机器人(2号机器人)以及第三机器人(3号机器人),第一机器人用于抓取振动盘出口末端处的待加工的十字轴,并将抓取的待加工的十字轴放置于第一十字轴加工专机的待加工区域;第二机器人用于抓取经过第一十字轴加工专机第一加工工序完成后的十字轴,并将抓取第一加工工序完成后的十字轴放置于转运料道,抓取第二十字轴加工专机第二加工工序完成后的十字轴成品,并将抓取的第二加工工序完成后的十字轴成品放置于成品料道;第三机器人用于抓取转运处的第一加工工序完成后的十字轴,并将抓取的第一加工工序完成后的十字轴放置于第二
十字轴加工专机的待加工区域。
42.进一步地,生产料道还可以包括下滑料道以及2序上料道(即用于第二加工工序的上料料道),下滑料道的入口连接至转运料道的出口处,下滑料道的出口处连接至2序上料道的入口处,实现经过第一加工工序加工后的十字轴下滑至2序上料道;2序上料道的出口处,实现经过第一加工工序加工后的十字轴上料至第二十字轴加工专机的待加工区域,用于第三机器人抓取转运处的第一加工工序完成后的十字轴,并将抓取的第一加工工序完成后的十字轴放置于第二十字轴加工专机的待加工区域。
43.根据整个十字轴加工流程,将现场分别定义为取料控制、放料控制、专机加工控制、料道输送控制以及振动盘上料控制。
44.整个控制流程都是由ipc控制器1来做处理。将构建好的plc程序下载到ipc控制器1中,此时ipc控制器1已经和所有的十字轴加工专机模块31、生产料道32及机器人模块33的状态信号建立连接。ipc控制器1通过io模块21采集到各设备(十字轴加工专机模块31、生产料道32及机器人模块33)的当前状态信号并做判断,当响应某一条件时,通过继电器模组22将对应控制指令下达给对应的设备,实现想要的动作。当每个设备完成指令动作后,便将当前状态反馈给io模块21,包括各设备的启停、待机、就绪、报警状态等,实现整个动作的闭环控制。
45.具体地,根据获取十字轴加工专机模块、生产料道及机器人模块反馈的状态信号生成对应的控制指令具体包括:取料控制指令、放料控制指令;
46.其中,取料控制指令包括:
47.当第一有料检测传感器发送检测到有待加工的十字轴的状态信号(gtasksched.bifeeder1detectb)后,ipc控制器通过取料控制指令控制第一机器人从振动盘末端取料并放至第一十字轴加工专机的安全位置等待;当第一十字轴加工专机发送第一加工工序的完成信号(gtasksched.bicnc1ready)后,ipc控制器通过取料控制指令控制第二机器人从第一十字轴加工专机工作台上抓取十字轴至转运料道安全位置等待;当第二十字轴加工专机发送第二加工工序的完成信号(gtasksched.bicnc2ready)后,ipc控制器通过取料控制指令控制第二机器人从第二十字轴加工专机工作台上抓取十字轴成品并放至成品料道安全位置等待;当设置于转运料道末端的第二有料检测传感器发送检测到有第一加工工序完成的十字轴的状态信号(gtasksched.bifeeder4induction)后,ipc控制器通过取料控制指令控制第三机器人从转运料道末端取料并放至第二十字轴加工专机的安全位置等待。针对取料控制部分,需将振动盘末端第一有料检测传感器的输出信号(gtasksched.bifeeder1detectb)接入1号机器人的io模块的允许取料信号端口,将一号专机和二号专机的加工完成状态信号(gtasksched.bicnc1ready和gtasksched.bicnc2ready)接入2号机器人的io模块的允许取料信号端口,将2序上料道末端第二有料检测传感器的输出信号(gtasksched.bifeeder4induction)接入3号机器人的io模块的允许取料信号端口。
48.其中,放料控制指令包括:
49.当第一机器人发送放料等待信号且第一十字轴加工专机发送允许放料信号(gtasksched.borob1tocnc1)后,ipc控制器通过放料控制指令控制第一机器人执行放料动作;并在放料完成后,控制第一机器人返回取料等待位置;当第二机器人发送放料等待信号
且设置于转运料道末端的第二有料检测传感器发送检测到没有第一加工工序完成的十字轴的状态信号(gtasksched.borob2tofeeder3)后,ipc控制器通过放料控制指令控制第二机器人执行放料动作;并在放料完成后,控制第二机器人返回取料等待位置;当第二机器人发送放料等待信号且设置于成品料道末端的第三有料检测传感器发送检测到没有第二加工工序完成的十字轴成品的状态信号(gtasksched.borob2tofeeder2)后,ipc控制器通过放料控制指令控制第二机器人执行放料动作;并在放料完成后,控制第二机器人返回取料等待位置;当第三机器人发送放料等待信号且第二十字轴加工专机发送允许放料的状态信号(二号专机电控机构)(gtasksched.borob3tocnc2)后,ipc控制器通过放料控制指令控制第三机器人执行放料动作;并在放料完成后,控制第三机器人返回取料等待位置。针对放料控制部分,需将一号专机允许放料信号gtasksched.borob1tocnc1(一号专机电控机构,,例如plc)接入1号机器人的io模块的允许放料信号端口,将转运料道允许放料信号gtasksched.borob2tofeeder3(即第二有料检测传感器检测到转运料道上未有经过第一加工工序加工的十字轴)接入2号机器人的io模块的允许放料信号端口,将成品料道允许放料信号gtasksched.borob2tofeeder2(即设置于成品料道末端的第三有料检测传感器检测到成品料道上未有经过第二加工工序加工的十字轴成品)接入2号机器人的io模块的允许放料信号端口,将二号专机允许放料信号gtasksched.borob3tocnc2(二号专机电控机构,例如plc)接入3号机器人的io模块的允许放料信号端口。
50.当通过振动盘料道的待加工十字轴经振动盘料道传动至振动盘出口末端定位机构时,第一有料传感器检测到有十字轴后,料道停止运转;当第一有料传感器检测到没有十字轴后,即有下降沿信号(机器人取料完成),则振动盘重复上料动作。
51.进一步地,根据获取十字轴加工专机模块、生产料道及机器人模块反馈的状态信号生成对应的控制指令还包括:加工控制指令;
52.其中,加工控制指令包括:
53.当第一机器人发送放料完成的状态信号后,ipc控制器通过加工控制指令控制第一十字轴加工专机执行一次第一加工工序的加工动作;当第三机器人发送放料完成的状态信号后,ipc控制器通过加工控制指令控制第二十字轴加工专机执行一次第二加工工序的加工动作;加工完成后,第一十字轴加工专机或第二十字轴加工专机退回到起始位置,并将允许取料信号通过ipc控制器间接反馈或直接反馈至第二机器人;
54.当第二机器人接收到第一十字轴加工专机的允许取料信号后,将经过第一加工工序加工后的十字轴夹取至转运料道指定位置,当第二机器人接收到第二十字轴加工专机的允许取料信号后,将经过第二加工工序加工后的十字轴夹取至成品料道指定位置,并分别将允许放料信号通过ipc控制器间接反馈或直接反馈至第一机器人以及第二机器人。针对专机加工部分,需将1号机器人放料完成信号接入一号专机plc中加工指令信号端口,将3号机器人放料完成信号接入二号专机plc中加工指令信号端口。
55.进一步地,根据获取十字轴加工专机模块、生产料道及机器人模块反馈的状态信号生成对应的控制指令还包括:料道输送控制指令;
56.其中,料道输送控制指令具体包括:
57.当第二机器人发送放料完成的状态信号后,ipc控制器通过料道输送控制指令控制第二机器人放料对应的转运料道或成品转动设定的距离后停止,用于将转运料道中经过
第一加工工序的十字轴传输至转运料道末端,等待第三机器人抓取,并在第三机器人抓取后返回转运料道起始位置,等待第二机器人再次放料;或,将成品料道中经过第二加工工序的十字轴成品传输至成品料道末端,等待收取,并在收取后返回成品料道起始位置,等待第二机器人再次放料。针对料道输送控制,需将2号机器人放料完成信号接入到转运料道和成品料道启停控制继电器端口。
58.以上所有的输出信号接入均需由信号输出端上传至ipc控制器,并由ipc控制器根据预先设置的逻辑语句判断当前信号所匹配的动作指令,然后下发至相应设备执行相关动作。
59.进一步地,本发明技术方案还提供了一种一种基于ipc的十字轴专机自动化生产控制系统,还包括按键模块4,按键模块4的数据输出端与ipc控制器1的数据输入端通信连接,用于十字轴加工专机模块31、生产料道32及机器人模块33的启动、暂停、急停、复位控制。
60.具体地,由ipc控制器1采集的十字轴加工专机模块31、生产料道32及机器人模块33的设备状况,包括各设备的启停、待机、就绪、报警状态等,实现整个动作的闭环控制。按键模块4的实现方式即在生产线总控柜端设置启动、暂停、急停、复位按键,分别对应四个状态控制的输入信号i16~i19并接入到io模块21的对应端口,用于在程序中设置此四个状态的框架。当检测到启动信号后产线整体启动,振动盘上料、料道运转、机器人等待抓取放料、专机等待加工动作;当检测到暂停信号后各设备处于待机状态,可通过启动键继续执行当前加工轨迹;当检测到急停信号后,各设备卸载程序并停止,只可通过复位指令另行启动;当检测到复位信号后,各设备及各条件语句全部初始化。
61.当产线暂停时,所有设备全部停止,对应的状态指示灯
‑‑
三色灯呈黄灯状,保持当前状态及信号输出。待接收到启动信号后继续执行当前动作,恢复正常生产。
62.优选地,也可以分别设置坯料不足报警、机器人取放料异常报警、专机加工异常报警、料道满料报警,当产线加工为异常状态或执行急停信号时,三色灯呈红灯和蜂鸣状。所有设备急停锁死,机器人程序卸载,并将报警信号对应的写入到hmi警示栏中实时反馈。只能完成复位操作后另行启动。
63.进一步地,本发明技术方案还提供了一种一种基于ipc的十字轴专机自动化生产控制系统,还包括显示模块5,显示模块(hmi显示屏)的数据输入端与ipc控制器的数据输出端通信连接,用于显示十字轴加工专机模块、生产料道及机器人模块反馈的状态信息。
64.ipc控制器也和hmi显示屏通过既定的通讯协议建立连接,此时hmi显示屏等同于io模块,可通过触摸屏直接对各个设备进行调试。
65.将十字轴加工专机模块动作、生产料道运转、机器人模块抓取、振动盘上料等结果性质的状态通过io模块、ipc控制器实时反馈到hmi触摸屏上,并显示当前加工步骤及加工状态。当每个设备完成指令动作后,便将当前状态反馈给io模块,由ipc控制器采集后在hmi显示屏中显示出设备状况,包括各设备的启停、待机、就绪、报警状态等,实现整个动作的闭环控制。
66.本发明ipc控制器分别获取十字轴加工专机模块、生产料道及机器人模块反馈的状态信号,并根据获取十字轴加工专机模块、生产料道及机器人模块反馈的状态信号生成对应的控制指令,并将生成对应的控制指令通过io控制单元发送至对应的十字轴加工专机
模块、生产料道及机器人模块,有效解决由于现有技术造成十字轴加工生产的效率以及安全可靠性低的问题,有效地提高了十字轴加工生产的效率以及安全可靠性。
67.本发明技术方案中振动盘料道还包括胚料不足传感器、气缸顶伸传感器、第一有料检测传感器,可以实现基于胚料不足传感器、气缸顶伸传感器、第一有料检测传感器,振动盘自行启动、停止上料;并且通过气缸顶伸传感器在检测到有待加工的十字轴经过时,由ipc控制器控制,实现振动盘料道旁的气缸顶伸动作,拦截住后面的十字轴,并且振动盘停止上料,有效防止了两个及以上十字轴堆积在末端定位机构,造成机器人取料时夹爪压到其他的十字轴而引发机器人臂电机过流故障和报警。
68.本发明技术方案中还包括按键模块,可以实现十字轴加工专机模块、生产料道及机器人模块的启动、暂停、急停、复位控制。
69.本发明技术方案中还包括显示模块,可以实时显示十字轴加工专机模块、生产料道及机器人模块反馈的状态信息,便于维护人员及时了解十字轴加工专机模块、生产料道及机器人模块的状态信息。
70.上述虽然结合附图对本发明的具体实施方式进行了描述,但并非对本发明保护范围的限制,所属领域技术人员应该明白,在本发明的技术方案的基础上,本领域技术人员不需要付出创造性劳动即可做出的各种修改或变形仍在本发明的保护范围以内。