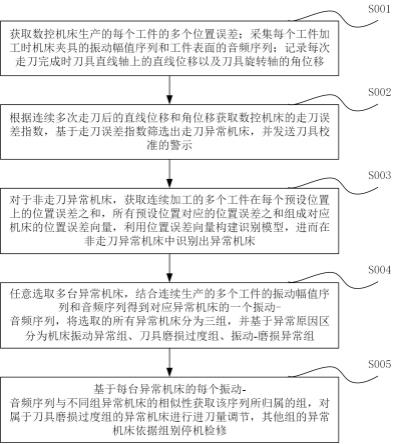
1.本发明涉及智能控制技术领域,具体涉及一种基于大数据的数控机床控制方法及系统。
背景技术:2.数控机床是一种装有程序控制系统的自动化机床,作为现代制造加工业的工业母机,在航天发动机、汽轮机、精密的光学等设备的生产中扮演着重要的角色,尤其是对于加工大批量和高精度要求的零件,各种数控机床承担着无可替代的作用,因此数控机床的精度稳定性和可靠性,对于企业生产有着非常重要的意义。同时,数控机床结构复杂、价格昂贵,在设备运行过程中如果出现精度误差,需要及时检测误差来源,严重时需要停机检修,以免出现数控机床产品不合格的情况,造成经济损失,甚至导致数控机床损坏。
3.对于数控机床精度误差的检测,大多需要定期停机检测,影响生产进度和效率,与产品加工同时进行的在线检测精度的方法较少,并且仅仅通过检测机床的基础件是否形变来确定机床精度是否有误差,检测依据单一,合理性较差;并且不能检测出精度误差源,无法对数控机床定点诊断。
技术实现要素:4.本发明提供一种基于大数据的数控机床控制方法及系统,用于检测数控机床的精度误差源并进行相应控制,所采用的技术方案具体如下:第一方面,本发明一个实施例提供了一种基于大数据的数控机床控制方法,该方法包括以下步骤:采集数控机床生产的每个工件在多个预设位置的坐标,并与标准件的对应坐标进行差异对比,得到每个工件的多个位置误差;采集每个工件加工时机床夹具的振动幅值序列和工件表面的音频序列;记录每次走刀完成时刀具直线轴上的直线位移以及刀具旋转轴的角位移;根据连续多次走刀后的所述直线位移和所述角位移获取数控机床的走刀误差指数,基于走刀误差指数筛选出走刀异常机床,并发送刀具校准的警示;对于非走刀异常机床,获取连续加工的多个工件在每个预设位置上的位置误差之和,所有预设位置对应的所述位置误差之和组成对应机床的位置误差向量,利用位置误差向量构建识别模型,进而在非走刀异常机床中识别出异常机床;任意选取多台异常机床,结合连续生产的多个工件的振动幅值序列和音频序列得到对应异常机床的一个振动-音频序列,根据每两台异常机床对应的振动-音频序列之间的差异距离将选取的所有异常机床分为三组,并基于异常原因区分为机床振动异常组、刀具磨损过度组、振动-磨损异常组;基于每台异常机床的每个振动-音频序列与不同组异常机床的相似性获取该序列所归属的组,对属于刀具磨损过度组的异常机床进行进刀量调节,其他组的异常机床依据
组别停机检修。
5.优选的,所述位置误差的获取方法为:利用两点之间的距离公式计算每个工件的每个预设位置处的坐标与标准件对应位置坐标之间的距离,即为所述位置误差。
6.优选的,所述走刀误差指数的获取方法为:获取正常走刀完成时的标准直线位移和标准角位移,计算每次走刀完成时的直线位移与标准直线位移的差值绝对值作为第一差值,以及角位移与标准角位移的差值绝对值作为第二差值,将第一差值和第二差值分别归一化并求和,获取连续多次走刀后的求和结果的和作为累积误差,以允许误差与累积误差的差值作为符号函数的自变量,得到的函数结果为所述走刀误差指数。
7.优选的,所述基于走刀误差指数筛选出走刀异常机床,包括:当所述走刀误差指数为-1时,对应的数控机床为走刀异常机床。
8.优选的,所述利用位置误差向量构建识别模型,包括:选取多个位置误差向量构建数据集,基于精度误差对每个选取的位置误差向量标注标签,所述标签为代表正常的第一预设值和代表异常的第二预设值,通过模型训练得到所述识别模型。
9.优选的,所述振动-音频序列的获取方法为:对于选取的每台异常机床对应的振动幅值序列和音频序列,以预设的第一数值作为振动幅值序列中每个时刻下的振动幅值的底数,以预设的第二数值作为音频序列中对应时刻下的音频信号的底数,将得到的两个指数函数结果相乘,乘积为对应时刻的振动-音频因子,连续加工的多个工件对应的所有的振动-音频因子组成所述振动-音频序列。
10.优选的,所述差异距离的获取方法为:利用wdtw算法计算每两个振动-音频序列之间的距离作为所述差异距离。
11.优选的,所述相似性的获取方法为:在刀具磨损过度组中任意选取多个振动-音频序列,将所有振动-音频序列中同一时刻的多个振动-音频因子求均值,所有时刻的均值组成一个新的振动-音频序列作为刀具磨损过度组的第一代表序列,计算每个振动-音频序列与所述第一代表序列之间的皮尔逊相关系数,作为振动-音频序列与刀具磨损过度组的相似性;在机床振动异常组任意选取多个振动-音频序列,将所有振动-音频序列中同一时刻的多个振动-音频因子求均值,所有时刻的均值组成一个新的振动-音频序列作为机床振动异常组的第二代表序列,计算每个振动-音频序列与所述第二代表序列之间的皮尔逊相关系数,作为振动-音频序列与机床振动异常组的相似性。
12.优选的,所述获取该序列所归属的组的过程为:预设一个相似阈值,当振动-音频序列与刀具磨损过度组的相似性大于所述相似阈值时,该序列属于刀具磨损过度组;当振动-音频序列与机床振动异常组的相似性大于所述相似阈值时,该序列属于机床振动异常组;否则属于振动-磨损异常组。
13.第二方面,本发明另一个实施例提供了一种基于大数据的数控机床控制系统,包括存储器、处理器以及存储在所述存储器中并可在所述处理器上运行的计算机程序,所述处理器执行所述计算机程序时实现上述基于大数据的数控机床控制方法的步骤。
14.本发明实施例至少具有如下有益效果:利用数控机床生产工件时的走刀数据筛选出走刀异常机床,走刀异常机床的走刀误差已经过大,不论其它方面如何调整,最终加工出的产品精度都会不符合要求,因此将走刀异常机床先行筛选出来进行刀具校准,然后对无走刀异常的机床进行后续检测;根据连续多个工件的总误差来判断非走刀异常机床中误差过大的异常机床;任意选取多台异常机床,利用异常机床的振动数据和音频数据区分异常原因并分组,将同一异常原因的异常机床分为一组,能够识别出精度异常的来源,方便后续检修;获取每台异常机床的每个振动-音频序列所归属的组别,依据组别得到异常数控机床的精度误差源,并对刀具磨损过度组的数控机床的进刀量进行调节,刀具磨损过度可以通过控制进刀量来减小精度误差,但是另外两种异常原因需要立刻停机从而减少因精度误差带来产品不合格的损失,通过区分异常原因能够对不同组别做出不同的控制行为,避免频繁停机导致较大的经济损失,同时实时检测精度误差源能够及时控制产品精度,保证产品质量,并且避免重大故障。
附图说明
15.为了更清楚地说明本发明实施例或现有技术中的技术方案和优点,下面将对实施例或现有技术描述中所需要使用的附图作简单的介绍,显而易见地,下面描述中的附图仅仅是本发明的一些实施例,对于本领域普通技术人员来讲,在不付出创造性劳动的前提下,还可以根据这些附图获得其它附图。
16.图1为本发明一个实施例提供的一种基于大数据的数控机床控制方法的步骤流程图。
具体实施方式
17.为了更进一步阐述本发明为达成预定发明目的所采取的技术手段及功效,以下结合附图及较佳实施例,对依据本发明提出的一种基于大数据的数控机床控制方法及系统,其具体实施方式、结构、特征及其功效,详细说明如下。在下述说明中,不同的“一个实施例”或“另一个实施例”指的不一定是同一实施例。此外,一或多个实施例中的特定特征、结构或特点可由任何合适形式组合。
18.除非另有定义,本文所使用的所有的技术和科学术语与属于本发明的技术领域的技术人员通常理解的含义相同。
19.下面结合附图具体说明本发明所提供的一种基于大数据的数控机床控制方法的具体方案。
20.请参阅图1,其示出了本发明一个实施例提供的一种基于大数据的数控机床控制方法的步骤流程图,该方法包括以下步骤:步骤s001,采集数控机床生产的每个工件在多个预设位置的坐标,并与标准件的对应坐标进行差异对比,得到每个工件的多个位置误差;采集每个工件加工时机床夹具的振动幅值序列和工件表面的音频序列;记录每次走刀完成时刀具直线轴上的直线位移以及刀具旋转轴的角位移。
21.具体的步骤包括:1、采集数控机床生产的每个工件在多个预设位置的坐标,并与标准件的对应坐标
进行差异对比,得到每个工件的多个位置误差。
22.以数控机床生产的工件为齿轮作为示例,为了能够精准的测量误差量,需要使用图像尺寸测量仪,此仪器的原理是将齿轮通过图像识别,识别出齿轮的边缘,然后得到尺寸数据,精度误差在0.1微米左右。
23.将在数控机床上加工完成的齿轮经图像尺寸测量仪扫描后获取尺寸参数。为了数据的准确性,需要多个部位的测量数据来评价齿轮加工的精度误差程度,在齿轮的多个预设位置进行坐标测量,本实施例中作齿轮的剖面图,以齿轮圆心作为原点构建二维直角坐标系,沿剖面图中齿轮的周向均匀选取八个齿顶端点作为预设位置,相邻预设位置之间的距离相等,记录八个预设位置的尺寸坐标,然后确定作为标准件的标准齿轮相应的八个位置的坐标,利用两点之间的距离公式计算每个工件的每个预设位置处的坐标与标准件对应位置坐标之间的距离,即为位置误差,将第i个位置误差记为。
24.2、采集每个工件加工时机床夹具的振动幅值序列和工件表面的音频序列。
25.夹具振动偏移会对齿轮的加工精度产生不小的影响,在每台机床的夹具处安装一个振动传感器,在每个工件加工时采集夹具的振动情况,采集记录频率为50hz,得到的振动幅值序列 , 表示第n个时刻的振幅,n表示每个工件加工过程中的总时刻数。
26.刀头磨损会对齿轮最终加工的精度有影响,当刀头发生磨损时,刀头与加工件的接触摩擦面积增加,此时摩擦异常所产生的音频也不同,将微型音频传感器固定在每个数控机床的加工齿轮附近,不影响正常加工,采集频率同样为50hz,得到的音频序列为 , 表示第n个时刻的音频信号。
27.3、记录每次走刀完成时刀具直线轴上的直线位移以及刀具旋转轴的角位移。
28.数控机床中刀具的走位距离是由伺服电机控制的,虽然伺服电机相对步进电机来说精度较高,但还有精度误差出现的可能性,以及长时间的走刀过程可能会出现偏差,与校准坐标不重合。这些情况都会造成工件的精度较低,因此为了能够排除此情况,需要测量刀具走位的精准度。
29.光栅尺是利用光栅的光学原理工作的测量反馈装置,在刀具直线轴上使用光栅尺测量直线位移,在刀具旋转轴上使用圆光栅测量角位移,判断其刀具误差,采集每一次走刀完成时光栅尺测量的直线位移 ,角位移 ,p表示走刀次数。
30.需要说明的是,角位移的单位为弧度,代表一个实数长度,而不是度数。
31.步骤s002,根据连续多次走刀后的直线位移和角位移获取数控机床的走刀误差指数,基于走刀误差指数筛选出走刀异常机床,并发送刀具校准的警示。
32.具体的步骤包括:1、根据连续多次走刀后的直线位移和角位移获取数控机床的走刀误差指数。
33.获取正常走刀完成时的标准直线位移和标准角位移,计算每次走刀完成时的直线位移与标准直线位移的差值绝对值作为第一差值,以及角位移与标准角位移的差值绝对值作为第二差值,将第一差值和第二差值分别归一化并求和,获取连续多次走刀后的求和结果的和作为累积误差,以允许误差与累积误差的差值作为符号函数的自变量,得到的函数结果为走刀误差指数。
34.以第p次走刀为例,计算第一差值: ,其中 表示标准直线位移;计算第二差值: ,其中表示标准角位移;由于直线位移和角位移的数字量级不同,将第一差值和第二差值分别进行归一化,将对应数值映射到[0,1]中,得到归一化后的第一差值和归一化后的第二差值,归一化的方法有多种,且为现有技术,本发明不再详细赘述具体过程。
[0035]
每次走刀时得到的直线位移与标准直线位移之间的差距,以及角位移与标准角位移之间的差距能够体现当次走刀的误差,通过连续多次走刀后的累积误差与允许误差做对比,计算走刀误差指数,判断对应数控机床的走刀误差是否在允许范围内。走刀误差指数的具体过程为:其中, 表示第m台数控机床的走刀误差指数, 表示允许误差, 表示累积误差, 表示符号函数。
[0036]
需要说明的是,符号函数中,自变量大于等于0时,输出为1;小于零时,输出为-1。
[0037]
作为一个示例,在本发明实施例中,累积误差对应的连续多次走刀的次数为10次,在其他实施例中通过实际情况确定连续多次的次数。
[0038]
2、基于走刀误差指数筛选出走刀异常机床,并发送刀具校准的警示。
[0039]
筛选走刀异常机床的过程为:当走刀误差指数为-1时,对应的数控机床为走刀异常机床。
[0040]
当走刀误差指数 为-1时,说明累积误差大于允许误差,意味着走刀误差已经过大,不论其它方面如何调整,最终加工出的产品精度都会不符合要求。因此,当走刀误差指数 为-1时,对应的数控机床为走刀异常机床,输出停机信号,并给维修人员发送机床刀具校准的指令;当走刀误差指数为1时,意味着走刀误差在精度范围内,对应的数控机床为非走刀异常机床,继续正常加工。
[0041]
步骤s003,对于非走刀异常机床,获取连续加工的多个工件在每个预设位置上的位置误差之和,所有预设位置的位置误差之和组成对应机床的位置误差向量,利用位置误差向量构建识别模型,进而在非走刀异常机床中识别出异常机床。
[0042]
具体的步骤包括:1、获取每台非走刀异常机床的位置误差向量。
[0043]
对于第i个预设位置,获取连续加工的多个工件在该预设位置处的位置误差之和: , 表示第k个工件在第i个预设位置处的位置误差。在本发明实施例中连续加工多个工件的个数为10个。
[0044]
所有预设位置对应的位置误差之和组成对应机床的位置误差向量,假设连续加工的10个工件为第m台非走刀异常机床加工的,则第m台非走刀异常机床的位置误差向量为 ,每台非走刀异常机床连续加工10个齿轮即会得到一个位置误差向量。
[0045]
2、利用位置误差向量构建识别模型。
[0046]
选取多个位置误差向量构建数据集,基于精度误差对每个选取的位置误差向量标注标签,标签为代表正常的第一预设值和代表异常的第二预设值,通过模型训练得到识别模型。
[0047]
由于位置误差向量 中的元素过多,变化不一,很难直接判断是否有精度误差。因此本发明实施例中通过构建识别模型来进行精度误差的判断。
[0048]
每台非走刀异常机床连续加工10个齿轮即会得到一个位置误差向量,每台非走刀异常机床加工的存在多个位置误差向量,且随着时间变化,位置误差向量在不断更新增加。选取多个位置误差向量构建数据集,以one-class svm模型作为训练基础,基于此数据集训练加工精度分类器模型,本实施例中共选取1000个位置误差向量构建数据集,其中包括遇到的各种不同的精度误差情况,将1000个位置误差向量人为打上标签,标签分为两类,分别将精度误差正常的位置误差向量标注为0,将精度误差异常的位置误差向量标注为1,然后将1000个数据分为训练集和测试集,900个精度误差向量作为训练集,用于正常的模型训练,100个作为测试集,用于分类器的正确率测试。
[0049]
分类器模型训练完成后,将100个测试集数据投入到该模型中,判断分类的正确率,不断修正模型参数,直到正确率符合加工要求,识别模型构建完成。具体参数计算步骤属于现有技术,不再详细赘述。
[0050]
在本发明实施例中第一预设值为0,第二预设值为1。
[0051]
3、在非走刀异常机床中识别出异常机床。
[0052]
将所有位置误差向量输入训练完成的识别模型中,当加工齿轮精度正常时,输出0,结果异常时输出1。当输出0时,意味着对应的非走刀异常机床未出现问题,当输出1时,意味着对应的非走刀异常机床出现了异常,当异常时需要进一步分析。
[0053]
步骤s004,任意选取多台异常机床,结合连续生产的多个工件的振动幅值序列和音频序列得到对应异常机床的一个振动-音频序列,根据每两台异常机床对应的振动-音频序列之间的差异距离将选取的所有异常机床分为三组,并基于异常原因区分为机床振动异常组、刀具磨损过度组、振动-磨损异常组。
[0054]
具体的步骤包括:1、获取选取的每台异常机床的多个振动-音频序列。
[0055]
对于选取的每台异常机床对应的振动幅值序列和音频序列,以预设的第一数值作为振动幅值序列中每个时刻下的振动幅值的底数,以预设的第二数值作为音频序列中对应时刻下的音频信号的底数,将得到的两个指数函数结果相乘,乘积为对应时刻的振动-音频因子,连续加工的多个工件对应的所有的振动-音频因子组成振动-音频序列。
[0056]
因为精度误差的来源是多样性的,有可能是由于刀头磨损过度引起的,也有可能是由机床的零件异常振动所引起的。为了分析精度误差的来源,需要基于步骤s001所采集的数据进行分析,为了减少不必要的计算量,只对异常机床进行分析:步骤s001中采集了振动和音频的数据集,利用振动幅值和音频信号获取振动-音频因子: ,其中 表示振动-音频因子;100表示预设的第一数值; 为自然常数,表示预设的第二数值。
[0057]
相同时刻下采集的振动幅值和音频信号分别以相差较大的两个的数值作为底数,能够防止音频和振动数值接近时不易分辨,通过此因子可以分析出精度误差的来源。
[0058]
需要说明的是,第一数值和第二数值均为本发明实施例给出的示例值,在其他实施例中可以根据实际情况预设其他两个相差较大的数值作为第一数值和第二数值。
[0059]
每加工一个工件,根据对应的振动幅值序列和音频序列能够获得一个同样长度的序列,序列中每个元素为对应时刻的振动-音频因子。连续加工的多个工件对应的所有的振动-音频因子组成振动-音频序列,在本发明实施例中将连续加工10个工件得到的对应的所有的振动-音频因子组成振动-音频序列,每台数控机床每连续加工10个工件即可得到一个振动-音频序列,所以每台异常机床都有多个振动-音频序列,且随着时间变化不断增加更新。
[0060]
2、获取每两台异常机床对应的振动-音频序列之间的差异距离。
[0061]
利用wdtw算法计算每两个振动-音频序列之间的距离作为差异距离。
[0062]
目前常用计算时间序列之间的距离方法为动态时间规整(dtw),主要是计算序列各点之间的欧氏距离,但dtw在序列对齐过程中产生不自然的扭曲翘曲。为了解决此问题,本实施例中使用了一种改进的dtw算法wdtw(weighted dynamic time warping)。
[0063]
wdtw在计算两个序列上的两个点之间的欧式距离上加上一个权重(weight),且该权重与两个点在x轴上的距离有关系,当两个点在x轴上的距离的值较大时,会赋予一个较大的权重,避免算法将两个距离较大的点匹配在一起。
[0064]
wdtw为现有算法,具体的数学计算不再详细叙述。
[0065]
通过wdtw算法得到每两台异常机床对应的振动-音频序列之间的距离作为差异距离。
[0066]
3、将选取的所有异常机床分为三组,并基于异常原因区分为机床振动异常组、刀具磨损过度组、振动-磨损异常组。
[0067]
通过步骤s002将出走刀异常机床剔除,排除了走刀误差的情况,对于异常机床来说,精度误差出现异常的原因有可能是机床振动异常、刀具磨损过度或者是两者结合的振动-磨损异常。
[0068]
选取出部分异常机床进行分组,是为了后续再进行异常原因判断时,不再需要大量计算,依据异常机床所属的组别即可得到该异常机床的精度误差源。
[0069]
由于k-means算法对异常值非常敏感,具有极大值的对象可能会产生严重扭曲的数据分布,因此本发明实施例使用k-medoids聚类算法对选取的所有异常机床分组,分组的过程为:选取的所有异常机床对应的振动-音频序列作为数据样本,在数据样本中随机选择3个振动-音频序列作为参考点,将剩下的样本点分配到差异距离最小的参考点所在的簇类中,随机选择一个非参考点样本作为交换对象和参考点进行交换,并重复上一步的操作重新分组,产生新的一组簇类,计算目标函数,当目标函数值小于0则将交换对象和参考点进行交换,交换对象替换原参考点作为新参考点,同时保留新的簇类,否则保留原参考点和对应簇类。重复交换参考点的过程直到3个参考点不再变化。
[0070]
k-medoids聚类算法的详细过程为公知技术,不再赘述。
[0071]
通过k-medoids聚类算法将选取的所有异常机床分为3组之后,基于每组内的振
动-音频因子的数值通过人工判别将三组分为机床振动异常组、刀具磨损过度组、振动-磨损异常组。
[0072]
步骤s005,基于每台异常机床的每个振动-音频序列与不同组异常机床的相似性获取该序列所归属的组,对属于刀具磨损过度组的异常机床进行进刀量调节,其他组的异常机床依据组别停机检修。
[0073]
具体的步骤包括:1、获取每台异常机床的每个振动-音频序列与不同组异常机床的相似性。
[0074]
在刀具磨损过度组中任意选取多个振动-音频序列,将所有振动-音频序列中同一时刻的多个振动-音频因子求均值,所有时刻的均值组成一个新的振动-音频序列作为刀具磨损过度组的第一代表序列,计算每个振动-音频序列与第一代表序列之间的皮尔逊相关系数,作为振动-音频序列与刀具磨损过度组的相似性。
[0075]
从刀具磨损过度组中随机抽取10条振动-音频序列,将10条序列同一时刻下的振动-音频因子求均值,整合成一条新的序列作为刀具磨损过度组的第一代表序列,第一代表序列代表刀具磨损过度组的序列特征,计算每个振动-音频序列与第一代表序列之间的皮尔逊相关系数,作为振动-音频序列与刀具磨损过度组的相似性。后续不再重复挑选,减少不必要的计算量。
[0076]
在机床振动异常组任意选取多个振动-音频序列,将所有振动-音频序列中同一时刻的多个振动-音频因子求均值,所有时刻的均值组成一个新的振动-音频序列作为机床振动异常组的第二代表序列,计算每个振动-音频序列与第二代表序列之间的皮尔逊相关系数,作为振动-音频序列与机床振动异常组的相似性。
[0077]
同样的,从机床振动异常组中随机抽取10条振动-音频序列,将10条序列同一时刻下的振动-音频因子求均值,整合成一条新的序列作为机床振动异常组的第二代表序列,第二代表序列代表机床振动异常组的序列特征,计算每个振动-音频序列与第二代表序列之间的皮尔逊相关系数,作为振动-音频序列与机床振动异常组的相似性。
[0078]
由于振动-磨损异常组是由两种异常共同造成的,所合成的序列数据不能保证每次都相似,不能简单计算相似度分入该组,容易增加误判率,因此,不计算与振动-磨损异常组的相似性。
[0079]
需要说明的是,皮尔逊相关系数为公知技术,此处不再描述具体计算过程。
[0080]
2、获取振动-音频序列所归属的组。
[0081]
预设一个相似阈值,当振动-音频序列与刀具磨损过度组的相似性大于相似阈值时,该序列属于刀具磨损过度组;当振动-音频序列与机床振动异常组的相似性大于相似阈值时,该序列属于机床振动异常组;否则属于振动-磨损异常组。
[0082]
皮尔逊相关系数的取值范围为[-1,1],作为一个示例,本发明实施例中预设的相似阈值为0.65,即当振动-音频序列与刀具磨损过度组的相似性大于0.65时,该序列属于刀具磨损过度组;当振动-音频序列与机床振动异常组的相似性大于0.65时,该序列属于机床振动异常组;当振动-音频序列既不属于刀具磨损过度组又不属于机床振动异常组时,该序列属于振动-磨损异常组。
[0083]
需要说明的是,每台数控机床每连续加工10个工件即可得到一个振动-音频序列,一台数控机床对应的振动-音频序列不止一个,随着时间的变化,可能原本未出现异常的数
控机床变得异常,通过实时更新数控机床对应的振动-音频序列,能够实时检测数控机床的异常情况。
[0084]
3、对属于刀具磨损过度组的异常机床进行进刀量调节,其他组的异常机床依据组别停机检修。
[0085]
由于刀具磨损过度可以通过控制进刀量来减小精度误差但是另外两种异常原因则需要立刻停机从而减少因精度误差带来产品不合格的损失。所以依据振动-音频序列所属的组别做出不同的控制行为。
[0086]
对属于刀具磨损过度组的异常机床进行进刀量调节,对其他组的异常机床依据组别停机检修。由于不同组别代表了不同的精度误差源,检修人员通过上述分组与判断能够清晰的知道机床故障原因,能够有效地进行维修,大大减少成本与时间。
[0087]
进刀量调节的过程为:根据加工的齿轮精度要求确定每次调节的量,本实施例中结合实际因素,每次调节0.5mm的进刀量,当调节一次后,计算下一批的齿轮是否精度误差回归正常,若依然异常,继续调节一次0.5mm的进刀量,若依旧不正常,则需立刻停工,联系人员更换刀头。若调节后恢复正常,则继续生产。
[0088]
综上所述,本发明实施例提供了一种基于大数据的数控机床控制方法,该方法采集数控机床生产的每个工件在多个预设位置的坐标,并与标准件的对应坐标进行差异对比,得到每个工件的多个位置误差;采集每个工件加工时机床夹具的振动幅值序列和工件表面的音频序列;记录每次走刀完成时刀具直线轴上的直线位移以及刀具旋转轴的角位移;根据连续多次走刀后的直线位移和角位移获取数控机床的走刀误差指数,基于走刀误差指数筛选出走刀异常机床,并发送刀具校准的警示;对于非走刀异常机床,获取连续加工的多个工件在每个预设位置上的位置误差之和,所有预设位置对应的位置误差之和组成对应机床的位置误差向量,利用位置误差向量构建识别模型,进而在非走刀异常机床中识别出异常机床;任意选取多台异常机床,结合连续生产的多个工件的振动幅值序列和音频序列得到对应异常机床的一个振动-音频序列,根据每两台异常机床对应的振动-音频序列之间的差异距离将选取的所有异常机床分为三组,并基于异常原因区分为机床振动异常组、刀具磨损过度组、振动-磨损异常组;基于每台异常机床的每个振动-音频序列与不同组异常机床的相似性获取该序列所归属的组,对属于刀具磨损过度组的异常机床进行进刀量调节,其他组的异常机床依据组别停机检修。本发明实施例通过区分异常原因能够对不同组别做出不同的控制行为,避免频繁停机导致较大的经济损失,同时实时检测精度误差源能够及时控制产品精度,保证产品质量,并且避免重大故障。
[0089]
本发明实施例还提出了一种基于大数据的数控机床控制系统,包括存储器、处理器以及存储在所述存储器中并可在所述处理器上运行的计算机程序,所述处理器执行所述计算机程序时实现上述的步骤。由于基于大数据的数控机床控制方法在上述给出了详细描述,不再赘述。
[0090]
需要说明的是:上述本发明实施例先后顺序仅仅为了描述,不代表实施例的优劣。且上述对本说明书特定实施例进行了描述。另外,在附图中描绘的过程不一定要求示出的特定顺序或者连续顺序才能实现期望的结果。在某些实施方式中,多任务处理和并行处理也是可以的或者可能是有利的。
[0091]
本说明书中的各个实施例均采用递进的方式描述,各个实施例之间相同或相似的部分互相参见即可,每个实施例重点说明的都是与其他实施例的不同之处。
[0092]
以上所述实施例仅用以说明本技术的技术方案,而非对其限制;对前述各实施例所记载的技术方案进行修改,或者对其中部分技术特征进行等同替换,并不使相应技术方案的本质脱离本技术各实施例技术方案的范围,均应包含在本技术的保护范围之内。