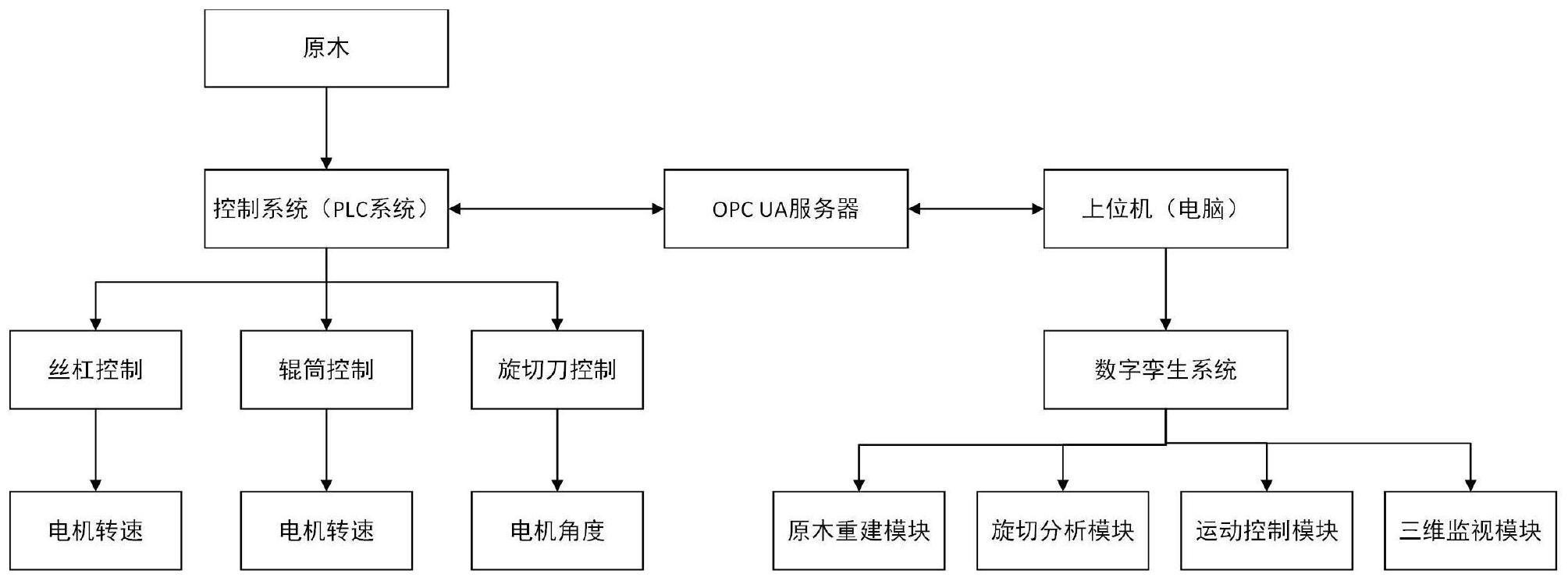
本发明是一种面向旋切机的数字孪生系统及其实现方法,属于旋切机控制。
背景技术:
1、旋切机作为目前木质单板的主要生产设备,其功能是将长度和直径在一定范围内的圆木经旋切过程后加工成为连续不间断的一条单板带,后经过人工测量或闸刀自动的方式将这一条单板带剪切成为多张规格相同的单板。目前旋切机存在旋切参数不可控、测试开发成本高及调刀步骤繁琐等问题。
2、目前无卡轴旋切方式主要是利用一根既起压紧作用又起进给作用的挤压摩擦辊(压尺辊),和两根起压紧圆木并起摩擦驱动作用的具有表面纹路的主摩擦辊(驱动辊)固定圆木,一把旋刀在压尺辊的下方与圆木接触进而产生一定的切削力后开始进行旋切生产。其中驱动辊两端安有电机,通过plc采用变频调速的方式控制驱动辊旋转;旋刀架设在刀台上,刀台采用丝杠进给方式,两端分别安有带减速器的电机,旋切前由工人调整旋刀安装参数,包括刀高、间隙等,旋切时plc通过采用变频调速的方式控制两端电机使刀台完成进给运动,从而将原木旋切成单板。
3、目前无卡轴旋切机普遍存在以下几点问题:
4、1、旋切过程参数不可控,在旋切过程中,刀台进给速度及旋刀旋切角度均为固定值,无法根据原木状态进行实时更新。
5、2、测试开发成本高,根据不同树种,不同径级原木旋切方案存在差异,如每次确认旋切参数都采用旋切机试切不仅会造成材料浪费,还会增加旋切机的损耗。
技术实现思路
1、本发明要解决的技术问题是针对以上不足,提供一种面向旋切机的数字孪生系统及其实现方法,在虚拟场景中对1:1的虚拟旋切机模型进行旋切模拟,实现真实旋切机的三维可视化在线监控和远程反馈闭环操作,可以提高旋切机智能化水平,使旋切机高效地旋切出厚度均匀高质量单板,并能实时掌握旋切机状态,针对问题及时预警,减少安全事故发生。
2、为解决以上技术问题,本发明采用以下技术方案:
3、一种面向旋切机的数字孪生系统,包括物理世界的真实旋切机、数字世界的旋切机和互连二者的opc ua服务器,opc ua服务器包括opc ua网关,数字世界的旋切机和物理世界的真实旋切机通过opc ua网关和通讯协议进行数据双向传输;
4、所述物理世界的旋切机由旋切机主体、测量模块和控制系统组成;
5、所述测量模块包括一组激光测距传感器,同一直线上设有8个激光测距传感器,最外侧激光测距传感器测量到旋刀旁标定块距离,其余激光测距传感器测量到原木表面距离
6、所述控制系统包括丝杠控制、辊筒控制和旋刀控制;
7、所述数字世界的旋切机是指上位机上unity3d下的旋切机工作场景及旋切机数字孪生系统,旋切机数字孪生系统包括原木重建模块、旋切分析及运动规划模块、控制决策模块、三维在线监视模块。
8、进一步的,所述原木重建模块是利用真实旋切机采集的激光测距传感器数据计算原木缺陷位置,寻找原木最低点,剔除缺陷后,利用再次采集的激光测距传感器数据计算圆木半径并生成圆木模型,用于后续旋切分析以及三维旋切展示;
9、圆木半径计算过程如下:
10、最外侧激光测距传感器测量其到标定块距离记为l2,其余激光测距传感器测量其到圆木距离记为l1,r为圆木半径,r为辊筒半径,h为标定块距离辊筒中心距离,根据几何关系可得
11、进一步的,所述旋切分析及运动规划模块是建立基于前馈和pid神经元网络,其隐含层分别由比例元、积分元和微分元构成,能够完成对输入信号的比例、积分和微分运算,输出层神经元可实现整个网络控制规律的综合和输出,利用原木重建模块最后所得圆木尺寸、预设旋切板厚及旋切机安装尺寸等计算出丝杠进给速度,利用原木重建模块最后所得圆木尺寸计算出旋刀角度。
12、进一步的,所述丝杠进给速度计算过程如下:
13、设双驱动辊和进给辊的直径均为d(mm),转速为n0(r/min);a、b间的中心距为c(mm);待加工原木的瞬时直径为φ(mm),瞬时转速为n(r/min);旋刀的进给速度为vt(mm/min),单板旋切厚度为s(mm);
14、双驱动辊和进给辊夹持原木旋转,双驱动辊和进给辊与原木线速度相等,所以φ·n=d·n0;
15、设旋刀与原木接触点为p点,
16、上式两边同时对旋转时间t求导,
17、依据旋切前后的原木质量守恒和密度守恒,则单板的横截面积变化率vc·s与原木的横截面积变化率s‘相等,因此有s'φ=vc·s,其中所以φ'=2ns;
18、即得运动学方程
19、设丝杠进给速度u=vt,sd为预设单板厚度值,w为pidnn的输出值,则根据市场经验选取输入层到隐含层连接权初值,再经由隐含层计算可得出u,即丝杠进给速度。
20、进一步的,所述旋刀角度计算过程如下:
21、设h为装刀高度,αg(∠fag)为工作后角,αz(∠dag)为装刀后角,αf(∠dae)为附加后角,αy(∠eaf)为运动后角。切削角度唯一影响因素为工作后角αg,其中αz为安装参数,
22、根据几何关系可得:φ为圆木瞬时半径,s为预设旋切板材厚度,所以切削角度只由装刀高度决定。
23、进一步的,所述控制决策模块是根据旋切分析及运动规划模块得出的丝杠进给速度与旋刀角度,计算得出电机转速及步进电机角度,并根据电机伺服驱动器开关频率进行匹配,通过服务器反馈至plc中,控制电机转速与角度。
24、进一步的,所述三维在线监视模块是通过服务器与plc通信,获取各电机运行状态,以及各激光测距传感器数据,在unity3d中进行利用上述数据通过三维虚拟仿真、实时曲线图、表对旋切过程进行三维可视化监视。
25、进一步的,所述opc ua服务器包括opc ua网关、路由器组成的通信网络及针对物理世界的旋切机与数字世界的旋切机建立的opc ua感知数据模型,通过建模规范统一数据格式,将多源数据映射到模型结构树,在数据集成的基础上实现了模型的实例化与数据交互,其中opc ua网关通过rs485通讯协议与物理世界的旋切机的plc相连,上位机通过无线网络与opc ua网关相连,使unity3d可远程与物理世界的旋切机的plc通信,从而与各激光测距传感器及各电机交互。
26、进一步的,所述opc ua数据感知模型建立过程:
27、确认建模需要的设备类型、设备的参数、设备具有的方法,以及设备之间或设备与参数、设备与方法之间的关系,通过ua modeler软件定义类型模型,主要包括定义对象类型模型、变量类型模型、引用类型模型、数据类型模型,之后合并为统一的类型模型,对4个类型模型进行实例化,同时按照opc ua服务器的标准地址空间方式,建立实例化信息模型,利用ua modeler工具导出xml,作为实现实例化信息的数据来源,最后使用open62541自带的工具把信息模型转成代码并添加到opc ua server里。
28、一种面向旋切机的数字孪生系统的实现方法,包括以下步骤:
29、步骤s01,系统初始化;
30、步骤s02,是否选择离线模式,如果是,先执行步骤s03,再执行步骤s04,并返回步骤s02,如果否,则执行s05;
31、步骤s03,设置参数;
32、步骤s04,进行旋切仿真;
33、步骤s05,控制激光测距传感器依次采集圆木表面深度信息,即激光测距传感器到原木表面距离;
34、步骤s06,plc将原木表面数据通过opc ua网关传至unity中;
35、步骤s07,原木重建模块利用原木表面深度信息,计算出缺陷位置,寻找原木表面最低点,将结果反馈至plc中,控制其将原木旋切至缺陷位置,获得有效圆木,即标准圆柱;
36、步骤s08,剔除缺陷后再次采集圆木表面深度信息,检测表面是否存在缺陷,如果存在缺陷执行s07,否则,利用圆木表面深度信息,计算出圆木半径,并在unity中生成圆木模型,用于旋切分析及三维旋切展示;
37、步骤s09,通过调用旋切分析及运动规划模块计算出丝杠进给速度以及旋刀角度;
38、步骤s10,控制决策模块将步骤s09计算得出的丝杠进给速度与旋刀角度根据电机伺服驱动器开关频率进行匹配,将电机所需转速与角度通传送至plc中;
39、步骤s11,通过opc ua网关与plc进行数据交换,经由opc ua数据感知模型将数据进行分类储存,unity根据信息类型就行三维可视化;
40、步骤s12,判断是否有下一次作业信号,如果是则执行步骤s05,如果否则执行步骤s02,也可以直接结束。
41、本发明采用以上技术方案,与现有技术相比,具有如下技术效果:
42、1、对比传统旋切机,所述面向旋切机的数字孪生系统可以根据旋切原木形态分析得出最优旋切方案,提高木板旋切质量及木材利用率。
43、2、所述旋切机数字孪生系统,可通过opc ua网关与旋切机激光测距传感器进行通信并在数字世界旋切机界面三维可视化显示,从而实现对旋切机的远程实时监控与控制,减少工厂人员,提高工厂安全系数。
44、3、所述旋切机数字孪生系统,配备的数字世界旋切机可离线使用,以便工作人员测试或学习旋切机功能,改善旋切机操作教育方式。
45、4、旋切过程参数可控,在旋切过程中,刀台进给速度及旋刀旋切角度均可根据原木状态进行实时更新。
46、5、测试开发成本低,可适用于不同树种、不同径级原木旋切方案。