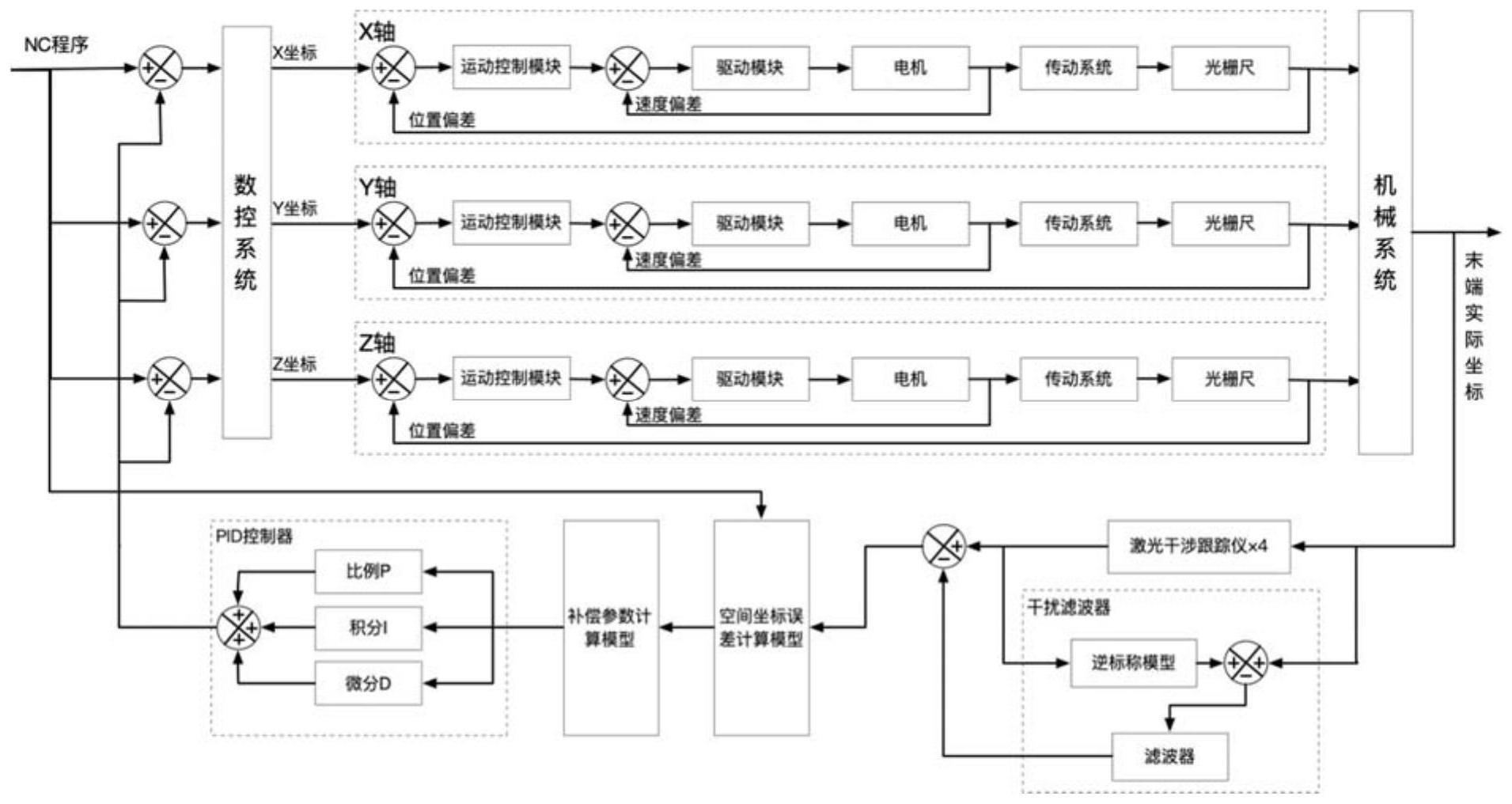
本发明涉及机床补偿,具体地,涉及一种基于激光干涉跟踪仪测量场的机床误差补偿方法及系统。
背景技术:
1、数控机床是一种装有程序控制系统的自动化机床,能够根据已编好的程序,使机床动作并加工零件。现在的数控机床配有高精度的光栅尺,运动精度非常精确,虽然有了高精度的传动系统,但加工精度不一定高,这是因为传动系统至刀具末端中间还存在一定机械的结构,机床中间任一部分的误差最终都会导致末端刀具切削加工运动的精度下降。在实际切削加工过程中,刀具刀尖点与加工零件直接接触,而机床在运行过程中主轴、进给系统会产生热变形以及刀具在加工过程中的磨损,均会造成刀具刀尖点的位置发生变化,从而造成加工误差,影响零件的加工精度。因此,如何快速、可靠的计算出刀尖点的位置,完成误差的实时补偿,是保证加工精度的关键。
2、在授权公告号为cn109345500b的中国专利文献中,公开了一种基于机器视觉的机床刀具刀尖点位置计算方法,包括步骤1,设置工业相机和背光光源;步骤2,设置工业相机相应的采样频率,采集刀具在旋转过程中,不同时刻的多张图像;对获得图像进行处理得到刀具边缘二值图并叠加,进而得到刀具在旋转过程中的整体轮廓二值图;步骤3,得到图像矩阵的像素值并求取刀具边缘坐标值得到刀具最外部边缘,得到刀具最低点位置坐标,即完成整个刀具刀尖点位置的计算过程。
技术实现思路
1、针对现有技术中的缺陷,本发明的目的是提供一种基于激光干涉跟踪仪测量场的机床误差补偿方法及系统。
2、根据本发明提供的一种基于激光干涉跟踪仪测量场的机床误差补偿方法,包括以下步骤:
3、步骤s1:使用多台激光干涉跟踪仪组网连接形成测量场;
4、步骤s2:通过多台激光干涉跟踪仪同步触发实时采集机床刀尖点运动数据;
5、步骤s3:根据所测数据将机床误差分离为离线几何误差与在线随机误差;
6、步骤s4:对机床离线几何误差进行检测与补偿;
7、步骤s5:通过测量场同步触发实时采集机床刀尖点运动数据,实时闭环控制机床刀尖点空间位置坐标。
8、优选地,所述步骤s1中,设激光干涉跟踪仪位于第j个基站位置pj(x0j,y0j,z0j),机床主轴上的靶镜位于点m0时跟踪仪设置干涉原点,即干涉测量的死径长度l0j为m0与pj间的绝对距离,当靶镜移动至测点mi(xi,yi,zi)时,mi与pj的绝对距离为l0j,δlij为此时干涉仪测得的相对位移量,即有:
9、
10、式中[xi,yi,zi,x0j,y0j,z0j,l0j]为未知常量,δlij为测量已知量;将上式用矢量写为误差形式:
11、∈ij=|mi-pj|l0j-δlij
12、∈ij为[mi,pj,l0j]的拟合量与测量值δlij间的拟合误差;通过最小化大量空间测点处的拟合误差∈ij平方和,来实现对测点实际坐标mi的精确计算,建立以下最优化问题:
13、
14、式中
15、
16、x=[{mi}i=1,…,m,{pj}j=1,…,n,{l0j}j=1,…,n]
17、为待辨识的未知量,m为测点总数,n为基站位置总数,以跟踪仪基站位置[p1,p2,p3]为参考点建立测量坐标系,通过坐标系约束了6个参数,使未知量总数下降为3m+4n-6,测点方程组共有m·n个,该最优化问题有解,得:
18、(n-3)m>4n-6
19、使用lm算法构建求解所建测量模型的算法过程:
20、
21、式中
22、f(x)=[f1(x),…,fr(x),…,fmn(x)]t(r=1,…,mm)
23、
24、且下标满足r=(j-1)m+i,即将不同测点误差方程按下标r组合为1×mn维向量;目标函数h(x)的梯度为:
25、
26、式中j为f(x)的雅各比矩阵:
27、
28、则根据lm算法在迭代点xk有下降方向:
29、
30、uk为阻尼系数,用于在拟hessen矩阵近似情况较差时调节dk趋向最速下降方向;在当前迭代点处对g(x)作二次泰勒展开近似:
31、
32、计算二次近似函数q(d)和原目标函数在dk下的增量之比
33、
34、当ηk接近1时,表明二次函数q(d)在迭代点xk处与目标函数拟合较好,取接近高斯牛顿方向迭代,阻尼系数μk取较小值,反之μk取较大值;为避免迭代中步长震荡,获得更快的收敛速度,μk的变化率应尽量光滑,更新规则如式(4-27)所示:
35、
36、根据激光干涉跟踪仪的测量误差(0.2+0.3μm/m)进行蒙特卡洛仿真,根据测量的距离对每个测量点附加高斯随机误差:
37、erorr=0.2+0.3*lij
38、加入误差后,原测量等式变为:
39、
40、进行仿真后,求解优化问题:
41、
42、计算每个激光干涉跟踪位置的期望与方差
43、
44、
45、若蒙特卡洛仿真后的激光干涉跟踪仪位置计算方差大于阈值,则需要对四台激光干涉跟踪仪的位置进行重新规划。
46、优选地,所述激光干涉跟踪仪数量不少于四台,且均匀分布,多台所述激光干涉跟踪仪处于非共平面位置,任意三台激光干涉跟踪仪处于非共直线位置。
47、优选地,所述离线几何误差指由机床结构件、地基部件发生稳定的变化所造成的误差,所述离线几何误差不随时间的变化而变化,或在长时间内仅发生微小的变化;所述在线随机误差指由机床环境温度、随机误差等因素所造成的误差,所述在线随机误差随着时间的变化而变化。
48、优选地,所述步骤s4包括:
49、步骤s4.1:建立工件坐标系中机床刀尖点位置在机床坐标系下与各运动轴的关系模型;
50、步骤s4.2:分析机床运动轴扰动误差对机床刀尖点位置的影响关系,建立误差影响下工件坐标系中刀尖点与机床坐标系中各运动轴位置之间的变换模型。
51、步骤s4.3:根据关系模型规划机床离线几何误差测量轨迹;
52、步骤s4.4:激光干涉跟踪仪测量场采集机床刀尖点运动误差数据;
53、步骤s4.5:通过误差分离算法计算分离机床刀尖点运动误差至机床各个运动轴;
54、步骤s4.6:根据计算结果生成数控系统对应几何误差补偿文件;
55、步骤s4.7:通过tcp通讯,将补偿文件导入数控系统并生效。
56、优选地,所述步骤s4.1包括:
57、建立刚体绕x轴、y轴和z轴分别旋转角度α、β和γ,以及沿着x轴、y轴和z轴分别平移位移dx、dy和dz的其次坐标变换矩阵:
58、根据刚体在空间中位姿可表示为平移、旋转变化的复合运动,即:
59、d=t(z,dx)t(y,dy)t(x,dz)r(z,γ)r(y,β)r(x,α)
60、化简上式得到:
61、
62、优选地,所述步骤s3.2包括:
63、建立工件坐标系中刀尖点位置与机床坐标系下各运动轴位置关系矩阵:
64、wp=ftw(x,y,z)tp
65、其中,wp代表工件坐标系下刀尖点的坐标,tp表示机床坐标系下刀尖点的坐标,将关系矩阵变换为代数式形式,得到:
66、
67、即ψ=fψ(x,y,z),其中ψ代表x,y,z,表示刀尖点坐标;
68、将上式取微分:
69、
70、将微分式变换为矩阵形式:
71、
72、其中,j(x,y,z)为雅克比矩阵,是从机床运动轴构成的向量到刀尖点位置坐标的线性转换矩阵,具体表达式为:
73、
74、建立考虑机床几何误差时刀具坐标系与工件坐标系之间的变换关系:
75、
76、得到刀尖点在工件坐标系下坐标位置(x,y,z)由nc指令(x,y,z)的表示如下:
77、
78、优选地,所述步骤s5包括以下子步骤:
79、步骤s5.1:进行数据检查,排除异常数据和噪点数据;
80、步骤s5.2:通过快速冗余迭代算法计算刀尖点空间位置坐标;
81、步骤s5.3:将刀尖点空间位置坐标导入机床数控系统中,计算补偿参数;
82、步骤s5.4:通过数控系统根据补偿参数对机床刀尖点位置进行实时补偿。
83、优选地,所述补偿参数采用pid控制器对数控系统进行补偿,位置式pid算法的控制量计算如下所示:
84、
85、式中kp、ki和kd即分别为比例系数、积分系数和微分系数,使用增量式pid控制算法,其控制量为:
86、δu(k)=u(k)-u(k-1)
87、=kp[e(k)-e(k-1)]+kie(k)+kd[e(k)-2e(k-1)+e(k-2)]
88、式中e(k)、e(k-1)和e(k-2)分别对应当前误差以及之前两次误差值,其输出量δμ=[δx,δy,δz]为对上一次控制量的增量,该增量通过数控系统的tcp通讯实时补偿进机床nc程序插补后的运动控制量,具体公式表示如下:
89、
90、式中,pk=[xk,yk,zk,x0j,y0j,z0j,l0j],以上是控制器的控制目标,通过pid控制算法,控制量计算如下:
91、。
92、根据本发明提供的一种基于激光干涉跟踪仪测量场的机床误差补偿系统,包括以下模块:
93、模块m1:使用多台激光干涉跟踪仪组网连接形成测量场;
94、模块m2:通过多台激光干涉跟踪仪同步触发实时采集机床刀尖点运动数据;
95、模块m3:根据所测数据将机床误差分离为离线几何误差与在线随机误差;
96、模块m4:对机床离线几何误差进行检测与补偿;
97、模块m5:通过测量场同步触发实时采集机床刀尖点运动数据,实时闭环控制机床刀尖点空间位置坐标。
98、与现有技术相比,本发明具有如下的有益效果:
99、1、本发明通过快速冗余迭代算法将四台激光干涉跟踪仪的位移测量数据偏差转化为刀尖的空间位置坐标偏差,达到了刀尖点空间位置的高精度测量效果;
100、2、本发明通过实时补偿系统,将测量场与数控系统进行集成,解决了机床与测量场的闭环控制问题,实现了机床刀尖点空间坐标的实时补偿控制。