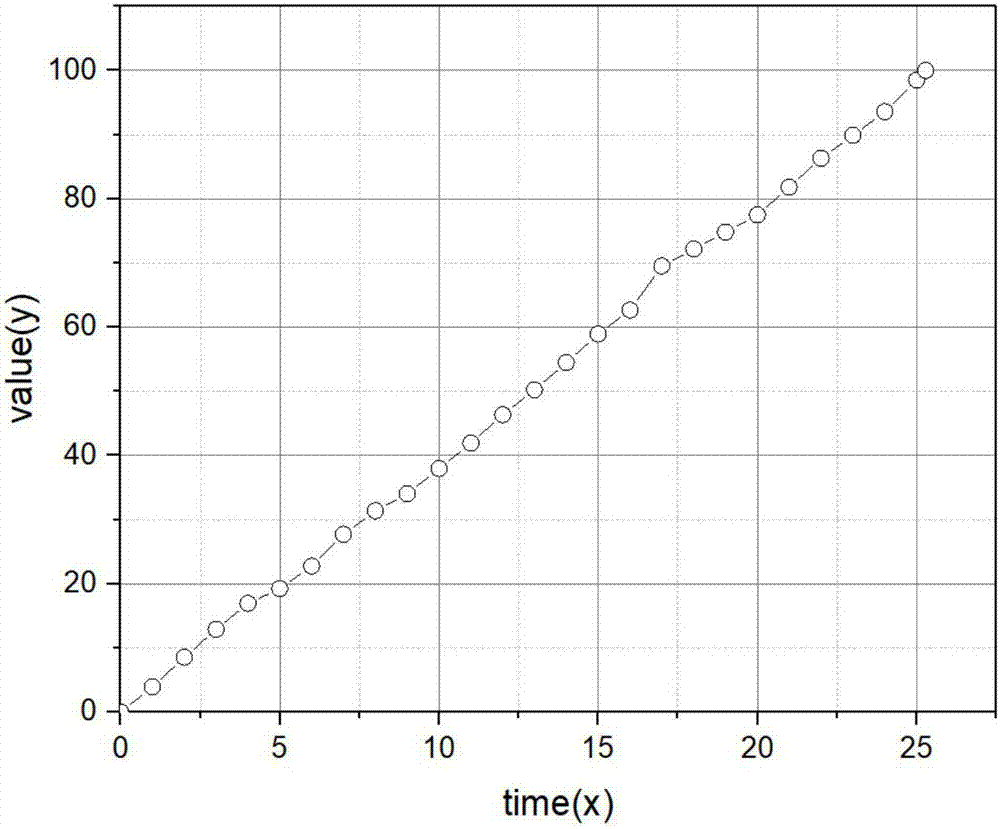
本发明提供一种基于寿命信息融合的动态退化可靠性评估方法,它涉及一种基于寿命信息融合针对单机产品的动态退化可靠性评估方法。旨在融合实时运行的单机产品性能退化寿命信息与总体性能退化寿命信息,构建合理的在线退化可靠性模型,解决高可靠长寿命产品单机实时性能退化可靠性分析问题,属于可靠性工程领域。
背景技术:
:当前的可靠性工程领域对产品可靠性要求极其严格,任务剖面和运行状态的个性化、多样化,使单机动态可靠性备受关注。如何面向全服役周期进行有效的状态监测和动态可靠性分析已成为可靠性工程领域迫切需要解决的热点和难点问题。为此,借助性能退化可靠性分析方法,结合在先同类产品寿命信息和/或关键部组件寿命信息构建合理的退化模型,在单机服役期间,基于实时监测数据对退化模型进行在线更新,实现高可靠长寿命产品单机可靠性的实时分析和预报。退化型失效是指产品的性能特征量随着时间的推移逐渐劣化直到不能满足规定的工作状态的现象,比如材料的老化、机械零件的磨损等等。在工程实际中,大部分失效过程都可以用退化失效来描述,所以对退化失效过程进行建模分析具有重要的现实意义。退化路径是使用较早的退化模型。随着认识的不断深入,研究人员发现性能退化过程往往受到多种随机因素的影响,采用随机过程方法描述和分析更为合理和有效。singpurwalla概括性地提出了用于说明失效机制的一些随机过程,其中维纳过程是应用最为普遍的退化模型之一,研究者已经建立了一系列的模型,包括简单维纳过程模型、混合效应维纳过程模型、考虑测量误差的维纳过程模型以及基于时间尺度变换的维纳过程等。在单机动态可靠性分析方面,gebraeel等针对旋转元件轴承,通过贝叶斯原理建立同一系统过去和现在的退化状况之间的联系,提出了一种指数剩余寿命预测模型。基于系统中固定参数的历史退化信息,得到模型参数的最大似然估计;基于轴承实时监测的退化数据,进行动态分析。本发明基于退化寿命信息融合的思想,提出了一种基于寿命信息融合的动态退化可靠性评估方法,包括融合同类产品在先寿命信息和/或关键部组件寿命信息和单机性能监测寿命信息的退化建模,采用贝叶斯理论结合单机实时监测信息的退化模型在线更新方法,最后对单机的可靠性和寿命进行实时评估和分析。技术实现要素:目的:针对高可靠性长寿命产品单机服役期间的可靠性评估的特点和难点,提出一种基于寿命信息融合的动态退化可靠性评估方法,它是一种方便有效的小子样单机可靠性评估方法。技术方案:本发明提出了一种基于寿命信息融合的动态退化可靠性评估方法,其实现步骤如下:步骤一:对产品的结构特点和失效模式进行分析,确定关键性能参数及其失效阈值;步骤二:根据产品关键性能参数随时间的退化规律,建立退化模型,其中模型参数分为两类,表征总体退化寿命特征的固定参数和表征单机个体退化寿命特征的随机参数;本发明以性能退化率作为随机参数,假设其服从正态分布,来表征单机性能退化的个体差异;步骤三:融合产品或关键部组件在先退化试验得到的关键性能参数退化数据,采用极大似然估计法,估计退化模型中各未知参数,确定模型退化率的先验分布;步骤四:根据退化率的先验分布,融合服役单机的动态性能退化监测结果,基于贝叶斯理论得到当前时刻退化率的后验分布,得到更新的性能退化模型;步骤五:利用融合了产品单机在线监测信息的退化模型,对服役单机进行可靠性评估;步骤六:随着服役单机性能监测的不断推进,采用贝叶斯理论在线更新性能退化模型,并进行动态可靠性分析和寿命预测。本发明基于性能退化寿命信息融合的思想,采用退化可靠性分析手段,融合同类产品在先寿命信息和/或关键部组件寿命信息与实时运行单机的性能监测寿命信息。基于贝叶斯理论,通过以上步骤,达到了对单机的可靠性和寿命进行动态分析和评估的效果,解决了高可靠性长寿命产品单机可靠性评估的实际问题。其中,在步骤一中所述的“对产品的结构特点和失效模式进行分析,确定关键性能参数及其失效阈值”,其做法如下:结合已有经验,对产品整机、关键部组件的物理工作过程进行分析,确定其关键失效模式和机理,进而确定能够作为失效判别依据的性能参数及其失效阈值。对于产品或关键部组件性能退化试验或在先服役期间得到性能参数的退化数据,记第i个试样在时刻ti1<ti2<…<tin进行测量得到退化测量值zi1,zi2,...,zin,i=1,2,3,...,m,分析退化过程测试结果统计特征的变化规律;在工程实际中,产品退化过程的均值通常为线性规律或通过适当变换为线性规律(例如,线性、二次函数、对数、指数、幂函数等变换);不失一般性,定义变换时间x为测试时间t的严格单调递增函数定义性能参数退化量变换函数y=φ(z),使得到的退化过程y=y(x)具备线性独立增量特性。其中,在步骤二中所述的“根据产品关键性能参数随时间的退化规律,建立退化模型”,其做法如下:1.产品性能退化均值的确定;通过测试时间和/或性能参数值的变换,对试样i,其性能退化均值pi(x)与测试时间为如下线性关系pi(x)=αi+βixi=1,2,…,m(1)其中pi(x)表示试件i性能参数的退化均值函数;x表示变换后的测试时间;αi和βi为第i个试件的模型参数;2.样本方差形式的确定;在x时刻,退化参数的方差的无偏估计为其中m表示试件的个数,表示x时刻性能参数的平均退化量,为各试样模型参数的均值。则可见,在产品退化均值为线性的情况下,退化过程的方差可以表示为时间x的二次函数;3.产品单机退化路径差异性考虑;在实际应用中,产品个体退化过程之间存在差异,其中退化率β的个体差异性最为显著;因此,假定表征个体差异性;4.性能参数退化建模;基于上述分析,本发明提出一种考虑产品个体间差异的线性独立增量过程退化模型,可表示为式中α,μβ,σβ2,d0,d1和d2均为模型参数,其中α是固定参数;β是服从正态分布的随机参数体现退化过程的个体差异性;α+βx表示产品性能的退化均值;ε(ti)为独立增量过程,且β与ε(ti)相互独立;定义δε1=ε(x1),δε2=ε(x2)-ε(x1),…,δεn=ε(xn)-ε(xn-1),根据独立增量过程的特点,有δεj~n(0,d1(xj-xj-1)+d2(xj2-xj-12))(5)δε1~n(0,d0+d1x1+d2x12)(6)。其中,在步骤三中所述的“融合产品或关键部组件在先退化试验得到的关键性能参数退化数据,采用极大似然估计法,估计退化模型中各未知参数,确定模型退化率的先验分布”,其做法如下:1.确定似然函数的形式设第i个试件的退化量测量值为yi1,yi2,...,yin,令xi=(xi1,xi2,...,xin)',yi=(yi1,yi2,...,yin)',则yi服从正态分布,其均值为αin×1+μβxi;根据线性独立增量过程的定义,可以确定协方差矩阵为其中in×1=(1,1,...,1)'n×1,且:进而可得到m个试件的对数极大似然函数为:式中,l(θ)表示极大似然函数;yi表示退化量的向量;μβ表示退化量期望值的向量;σ为各试件协方差矩阵;σ表示协方差矩阵的行列式。2.计算模型参数上式对参数α和μβ求偏导,有由上两式为0并结合对数似然函数的表达式,可以得到相应的条件对数似然函数;然后,利用多维搜索使其取得最大值,可以得到参数的极大似然估计,以及退化率β的先验分布遗传算法(ga)为这种组合优化问题的解决提供了一种很好的途径,也是相对简单并且可靠收敛的。其中,在步骤四中所述的“根据退化率的先验分布,融合服役单机的动态性能退化监测结果,基于贝叶斯理论得到当前时刻退化率的后验分布,得到更新的性能退化模型”,具体过程为:在实际应用中,个体间退化过程存在差异,这种差异由随机参数β表征;根据服役单机截止当前时刻的退化数据序列y1:k={y1,y2,…,yk},yi=y(xi),定义δy1=y1,δyi=yi-yi-1,δx1=x1,δxi=xi-xi-1;由于ε(t1),ε(xi)-ε(xi-1),i=2,…,k是独立的正态随机变量,所以在给定β时y1:k的联合条件概率密度函数为其中δσ2(x1)是在第一个测试时间点x1时的方差,δσ2(xi)=σ2(xi)-σ2(xi-1)表示在时间区间(xi-1,xi),i=1,2,…,k.上退化增量的方差;设π(β)是β的先验分布,本专利假设随机参数β服从正态分布则根据贝叶斯理论一方面,后验分布满足另一方面,后验分布又满足:上述两式β2,β项的系数应该相等,得到:于是,由贝叶斯理论得出对的更新结果,系统将基于实时退化监测结果不断更新均值参数μβ和方差参数在对产品单机性能参数监测得到退化数据序列y1:k后,其后验分布可由贝叶斯理论得到为式中先验分布所对应的后验分布的均值和方差,δσ2(t1)是在第一个测试时间点x1时的方差,δσ2(xi)=σ2(xi)-σ2(xi-1)表示在时间区间(xi-1,xi),i=1,2,…,k.上退化增量的方差。其中,在步骤五中所述的“利用融合了产品单机在线监测信息的退化模型,对服役单机进行可靠性评估”,其做法如下:1.根据上述推导和分析,在测试时刻x,被监测单机产品性能参数退化量y(x)的分布函数为式中σ2(x)=var(y(x))=σβ2x2+d0+d1x+d2x2为性能参数退化量的方差,βk为融合了产品单机性能参数退化信息的退化率,φ(·)为标准正态分布的分布函数,fy(y|x)表示性能参数退化量y(x)的分布函数;2.假设产品的失效阈值为df,若βk>0,则产品寿命t的分布函数为若βk<0,则产品寿命t的分布函数为式中p表示概率,ft表示产品寿命t的分布函数。3.可靠度为r的可靠寿命t1-r可通过求解下式得到若1-r=0.50,可以得到中位失效寿命为其中,在步骤六中所述的“随着服役单机性能监测的不断推进,采用贝叶斯理论在线更新性能退化模型,并进行动态可靠性分析和寿命预测”,其作法如下:随着服役单机性能监测的不断推进,单机性能参数监测得到退化数据序列y1:k={y1,y2,…,yk}不断得到新的数据点,根据步骤四退化率的均值方差更新方法对退化模型进行更新,得到新的退化模型,再根据步骤五的可靠性分析步骤对产品进行动态可靠性分析和寿命预测,从而得到随单机监测进行实时更新的单机可靠性分析结果。本发明的优点与积极效果在于:(1)基于静态线性独立增量过程退化模型,对于单机产品实时监测结果,融合目标产品实时性能参数退化信息,不断更新退化模型退化率均值和方差参数,使退化模型实时的反应单机产品特征。(2)利用基于实时监测结果的动态退化模型,给出了单机产品在给定退化失效阈值下可靠性评估方法,具有实际应用价值。附图说明图1为在先试验数据的示意图。图2为单机产品在线监测试验数据的示意图。图3为本发明所述方法流程图。图中序号、符号、代号说明如下:time(t)表示测量时间,value(z)表示性能参数退化数据。具体实施方式下面将结合附图和具体数据对本发明作进一步的详细说明;附图所示如下:图1为在先试验数据的示意图,每条线对应一个试样性能退化量的测试结果,横轴为时间,纵轴为性能参数退化量;图2为单机产品在线监测试验数据的示意图,横轴为时间,纵轴为性能参数退化量;图3为本发明所述方法流程图。本发明一种基于寿命信息融合的动态退化可靠性评估方法,见图3所示,其具体步骤如下:步骤一:对应技术方案中的步骤一,选取合适的退化参数,使其可以通过适当的变换而转化为线性独立增量过程,记第i个试件在时间tj的性能退化测量值为zij,i=1,2,…,m,j=1,2,…,n;其中,退化参数的选取基于物理失效分析开展。确定退化参数后,本发明以一组工程实测数据为例,共30个测试时刻,15个在先试样性能参数,如图2所示,可以看出测试数据经变换后呈线性变化规律,因而不必对其进行变换。利用退化数据进行下面的步骤。步骤二:对应技术方案中的步骤二,性能参数退化建模;基于上述分析,本发明提出一种考虑产品个体间差异的线性独立增量过程退化模型,可表示为步骤三:对应技术方案中的步骤三,计算似然函数,通过极大似然函数法,确定退化模型中的未知参数。具体过程如下:1.将测试数据表示为向量形式:设第i个试件的退化量测量值为yi1,yi2,...,yin,令xi=(xi1,xi2,…,xin)',yi=(yi1,yi2,...,yin)',则yi服从正态分布,其均值为αin×1+μβxi;根据线性独立增量过程的定义,可以确定协方差矩阵为其中in×1=(1,1,...,1)'n×1,且:2.定义似然函数。进而可得到m个试件的对数极大似然函数为:式中,l(θ)表示极大似然函数;yi表示退化量的向量;μβ表示退化量期望值的向量;σ为各试件协方差矩阵;σ表示协方差矩阵的行列式。3.求解模型参数。采用本文方法进行处理,由于工程实测数据初始值等于0,有α=0,基于matlab平台,采用优化算法求上述似然函数的极大值,对应的模型参数即为极大似然估计结果,计算结果如下:μβσβd0d1d24.11510.12770.01000.34580.0266步骤四:对应技术方案中的步骤四,根据退化率的先验分布,融合服役单机的动态性能退化监测结果,基于贝叶斯理论得到当前时刻退化率的后验分布,得到更新的性能退化模型。采用贝叶斯理论基于matlab平台在线更新性能退化模型,得到退化模型后验分布参数μβ,k、σβ,k如图3所示。步骤五:对应技术方案中的步骤五、六,产品单机监测数据如图3所示。基于在先性能参数得到模型参数先验分布后,采用贝叶斯理论基于matlab平台在线更新性能退化模型,并进行动态可靠性分析和寿命预测,基于上述模型,假设失效阈值100,研究可靠度r=0.5和r=0.9的失效寿命继而得到剩余寿命,.基于matlab平台的计算结果如下:当前第1页12