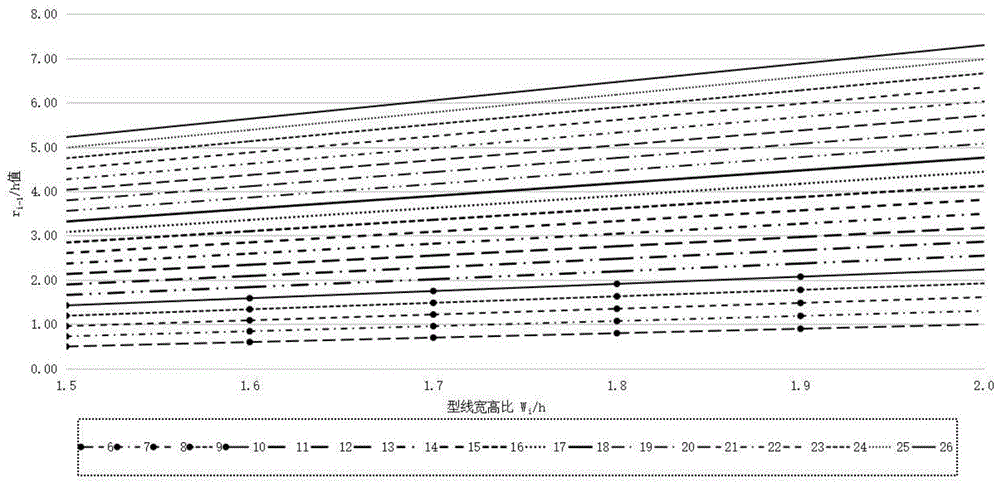
本发明涉及型线同心绞合导体结构的设计方法。
背景技术:
:导体的结构类型主要有独根圆形导体、非紧压圆形导体、紧压圆形导体和分割导体,这几类导体的区别在于独根圆形导体弯曲性不佳,一般应用于导体截面不大的电缆;非紧压圆形导体弯曲性改善,但导体外表不光滑,在高电压环境下易产生电场集中、且不均匀,在高压电缆中绝缘承受的畸变场强高;紧压圆形导体外表经紧压后光滑度有改善,但截面做不大,一般在800平方及以下;分割导体截面可做到2500平方,但分割导体的圆整性和表面光滑性不佳;基于上述情况下,型线同心导体引起工程应用人员的注意,由于型线同心导体采用的是预制瓦形股块,拼装而成的圆形导体,截面可做到2500平方,且导体外表圆整、光滑,具有良好的均化电场的作用,适合低、中、高电压等级电缆应用,特别是超高压电压等级的电缆,可大大降低绝缘所需承受的电场强度;另外型线同心绞具有极高的填充系数,可大大减小导体外径,从而降低电缆绝缘、护套材料的使用量,降低电缆材料使用成本;同时如此高的填充系数,大大减小了导体单丝之间的缝隙,提高了导体的密实性,特别有利于提高导体的纵向阻水能力,很好的满足了高电压阻水电缆的使用要求,如±320kv直流海底、湖底电缆的使用。型线同心绞导体的设计目前还没有一个系统、简便和有效的方法,一般采用的是不断设计和调整的方式得到最佳设计结构,然而这样的做法特别耗时耗材,特别是在高压、超高压电缆的设计过程中,由于电缆成本极高,频繁的设计调整将会造成巨大的设计成本;如果高压电缆采用德国troester公司最新的500kv悬链式交联生产线生产的话,由于悬链线的特殊工艺要求,导体需要经受弯曲,拉伸、扭转的机械外力共同作用,对型线同心绞导体的设计要求就更高了,所以急需一套系统的,适合导体拉制(或挤制)、导体绞合、以及绝缘挤出(悬链交联)工艺要求的,直观、简便、精准的型线同心绞导体结构设计方法。技术实现要素:本发明的目的是提供一种型线同心绞合导体结构的设计方法。实现本发明目的的技术方案是:型线同心绞合导体结构的设计方法,包括以下步骤:步骤1,通过标准规定的导体最大直流电阻设计导体称重截面;步骤2,根据导体称重截面设计导体绞合外径;步骤3,根据导体的绞合外径设计中心圆导体直径和每层型线高度;步骤4,设计每层型线根数;步骤5,对型线进行角度修正,通过角度修正后,根据每层型线尺寸参数,设计绘制每层单根型线成品截面图;步骤6,根据步骤1~5设计的参数,绘制成品型线尺寸图。所述步骤1中导体称重截面的计算公式为:其中,as为导体称重截面,ρ为导体材质的电阻率,l为导体长度,r为导体电阻,k1为单根导线加工过程中引起金属电阻率增加所引入的系数,k2为由于多根导线绞合使单线长度增加所引入的系数;k3为因紧压过程使导线发硬,引起电阻率增加所引入的系数;k4为因成缆绞合,使线芯长度增加所引入的系数;k5为因考虑导线允许公差所引入的系数。所述步骤2中的导体绞合外径的计算公式为:其中,dc为导体绞合外径,as为导体称重截面,0为填充系数,0的取值范围为92%~96%。所述步骤3具体为:设计导体层数n,根据步骤2计算的导体绞合外径,按照均匀分布的原则,计算中心圆形导体直径和每层型线高度,计算公式为:dc=dc1+n×hdc1=2×r其中,dc为导体绞合外径,dc1为中心圆形导体直径,n为型线层数,h为每层型线高度,r为中心圆导体半径。所述步骤4具体包括以下步骤:步骤4.1,绘制型线绞合导体结构参数设计关系曲线图,其中横坐标表示型线宽高比η,纵坐标为内层半径与型线高的比值γ,曲线表示型线根数。步骤4.2,根据η和γ的设计值,在型线绞合导体结构参数设计关系曲线图上找到相应的型线根数值,其中,η的值为1.5~2.0,γ的值为(i-1)+0.98。所述步骤4.1中的型线绞合导体结构参数设计关系曲线图根据以下公式的计算值进行趋势曲线点线图的绘制后得到,计算公式包括:η=wi/hγ=ri-1/hwi=2×ri×sin(α)ri=ri-1+hα=360/mi其中,i为型线所处的层数;wi为第i层型线宽度;ri为第i层型线绞合后半径;ri-1为第i-1层型线绞合后半径;h为每层型线高度;α为型线角度;η为型线宽高比;mi为第i层型线根数。所述步骤5中对型线进行角度修正的计算公式为:α=(360/mi)-β其中,i为型线所处的层数;mi为第i层型线根数,β为角度收缩值。所述角度收缩值β的由以下步骤得到:步骤5.1,绘制型线角度收缩曲线图,其中横坐标表示绞合节径比,纵坐标为角度收缩值,曲线表示型线根数。步骤5.2,根据每层型线的根数和节径比,在型线角度收缩曲线图上找到相应的角度收缩值。所述型线角度收缩曲线图根据以下多项式连列推导计算后绘制:w1=ro×sin(β1)w2=ro×sin(β2)其中,w1为绞合前型线宽度,w2为绞合后型线宽度,d为导体外径,h为每层型线高度,ro为型线外弧半径,β1为绞合前型线角度的一半,β2为绞合后型线角度的一半。采用了上述技术方案,本发明具有以下的有益效果:(1)本发明为型线同心绞合导体提供了一个系统的结构设计方案,避免了重复试制调整的麻烦。(2)本发明通过工艺验证,统计量化型线同心绞导体结构尺寸设计关键参数,降低了设计错误的概率。(3)本发明提供了图表对照的设计方法,理清结构设计诸多影响因素之间的关系,大大降低了理论计算工作量,量化了诸多因素的影响结构设计的轻重程度;(4)通过本发明提供的设计方法设计的型线同心绞导体结构,能够满足各种绝缘挤出设备、工艺的生产,包括德国troester公司最新的500kv悬链式交联生产线生产的需求。附图说明为了使本发明的内容更容易被清楚地理解,下面根据具体实施例并结合附图,对本发明作进一步详细的说明,其中图1为本发明的实施例1绘制的型线绞合导体结构参数设计关系曲线图。图2为本发明的实施例1绘制的型线角度收缩曲线图.具体实施方式(实施例1)本实施例的型线同心绞合导体结构的设计方法,包括以下步骤:步骤1,通过标准规定的导体最大直流电阻设计导体称重截面。根据金属电阻的物理特性,导体电阻与导体长度成正比、与导体截面成反比、与导体材质的电阻率成正比,计算公式如下:其中,a为导体称重截面,ρ为导体材质的电阻率,l为导体长度,r为导体电阻。由于导体的加工硬化和接触电阻的影响,都会增加导体的成品电阻值,所以引进5个加工系数来修正导体电阻值:k1、k2、k3、k4、k5。其中,k1为单根导线加工过程中引起金属电阻率增加所引入的系数,它与导线直径大小,金属种类,表面是否有涂层有关,一般可取1.02~1.07;k2为由于多根导线绞合使单线长度增加所引入的系数1.02(240mm2以下)~1.03(240mm2及以上);k3为因紧压过程使导线发硬,引起电阻率增加所引入的系数,一般取1.01;k4为因成缆绞合,使线芯长度增加所引入的系数,一般取1.01左右;k5为因考虑导线允许公差所引入的系数,对紧压结构一般取1.01左右。通过上述k1、k2、k3、k4、k5系数修正后,导体电阻与截面的关系式如式下:通过公式推导可得到由电阻计算导体截面的设计计算公式:以1800平方导体为例,1800平方导体称重截面设计计算过程中k1×k2×k3×k4×k5的乘积一般取1.045。通过上述公式设计计算,导体称重截面最小必须做到1784平方,才能确保导体直流电阻合格。1800平方型线同心绞合导体称重截面设计数据如表1所示。表11800平方型线绞合导体称重截面设计数据设计项目单位设计数值导体规格mm21800导体20℃导体最大直流电阻ω/km0.0101导体结构型线同心绞导体称重截面mm21784步骤2,根据导体称重截面设计导体绞合外径,计算公式为:其中,dc为导体绞合外径,as为导体称重截面,0为填充系数,0的取值范围为92%~96%。以1800平方铜型线绞合导体为例,其结构与圆形紧压导体绞合结构以及分割导体结构相比较,导体的填充系数最大,导体填充系数可达到94%以上。另外考虑到铜型线采用的挤出生产工艺,铜材经过挤出获得的型线,材质更柔软,可塑性更强,所以填充系数按照95%来进行设计计算。根据步骤2的公式,可以计算出1800平方型线绞合导体的绞合外径,如表2所示。表21800平方型线绞合导体称重截面设计数据设计项目单位设计数值导体规格mm21800导体20℃导体最大直流电阻ω/km0.0101导体结构型线同心绞导体称重截面mm21784导体填充系数%95导体设计外径mm48.9步骤3,设计导体层数n,根据步骤2计算的导体绞合外径,按照均匀分布的原则,计算中心圆形导体直径和每层型线高度,计算公式为:dc=dc1+n×hdc1=2×r其中,dc为导体绞合外径,dc1为中心圆形导体直径,n为型线层数,h为每层型线高度,r为中心圆导体半径。步骤4,设计每层型线根数,具体包括以下步骤:步骤4.1,绘制型线绞合导体结构参数设计关系曲线图,如图1所示,其中横坐标表示型线宽高比η,纵坐标为内层半径与型线高的比值γ,曲线表示型线根数(从下至上依次代表6根、7根、8根、9根、10根、11根、12根、13根、14根、15根、16根、17根、18根、19根、20根、21根、22根、23根、24根、25根、26根)。型线绞合导体每层的结构设计与中心圆导体外径、每层型线根数、每根型线的截面、型线单丝的宽高比有关,这几者之间相互关联又相互影响。型线绞合导体结构参数设计关系曲线图根据以下公式的计算值进行趋势曲线点线图的绘制后得到,计算公式包括:η=wi/hγ=ri-1/hwi=2×ri×sin(α)ri=ri-1+hα=360/mi其中,i为型线所处的层数;wi为第i层型线宽度;ri为第i层型线绞合后半径;ri-1为第i-1层型线绞合后半径;h为每层型线高度;α为型线角度;η为型线宽高比;mi为第i层型线根数。步骤4.2,根据η和γ的设计值,在型线绞合导体结构参数设计关系曲线图上找到相应的型线根数值,其中,η的值为1.5~2.0,γ的值为(i-1)+0.98。从导体加工工艺上来讲,中心圆形导体大小,可调节外面型线单丝的宽高比。型线单丝的宽高比影响着加工工艺性能。通过型线加工工艺原理来看,型线单丝结构尺寸从圆形向瓦形过渡过程中,变形比越小越容易实现,一般拉制型线控制宽高比为4:3。但宽高比越接近1,越会造成型线绞合过程中单丝型线翻身而拉断问题。所以型线同心绞合的拉制成型控制与绞合控制对型线的宽高比的要求是对矛盾体。如果型线生产采用的挤制工艺,可控的型线宽高比相对可宽泛一些,宽高比控制可达1.2~2.0之间,为了确保型线绞合工艺的控制,型线的宽高比最佳控制范围为1.5~2.0之间。导体的中心圆导体直径虽然能调节外围型线单丝的宽高比,但中心圆导体的直径不仅仅只和外围型线的宽高比有关,还涉及到导体每层的根数,每根型单线的截面等参数。这几者之间相互关联又相互影响,需要找到一个平衡点来设计。按照上述推论,进行1800平方铜型线导体的结构设计,根据已经设计计算掌握的数据如表2所示,导体称重截面1784平方,导体绞合后外径48.9mm。首先确定层数,1800平方是此次新工艺研发设计的最大规格,所以层数选择5层加一根中心圆导体,这样通过计算可得,均匀分布中心圆形导体直径8.15mm,每层高4.075mm。中心圆形导体就选择8mm直径,其他5层型线高度先按照4.08mm进行设计,后面再作微调。第1层根数设计,根据内层半径与型线高的比值γ=ri-1/h=0.98,型线宽高比η=wi/h=1.5~2.0这两个参数,对照图1所示的型线绞合导体结构参数设计关系曲线,可以看出,第一层型线根数选择6根的话,型线宽高比为2.0;选择7根的话型线宽高比为1.7;选择8根的话型线宽高比为1.5;选择8根的话型线宽高比为1.4。根据这些查图数据可得根数为6~8根均合适,但结合框绞设备第一节绞笼放线架个数,选择6根结构为最佳。并核算每根型线截面积,根据下面公式计算可得,每根导体截面积为25.7平方,在可控截面范围之内。其中,a1为第1层每根型线截面积,d1为第一层型线外径,d0为中心圆形导体直径,m1为第1层根数,π为圆周率。第2层根数设计,根据内层半径与型线高的比值γ=ri-1/h=1.98,型线宽高比η=wi/h=1.5~2.0这两个参数,对照图1所示的型线绞合导体结构参数设计关系曲线,可以看出,第2层型线根数选择6根往上选,到第10根的那条曲线才能与ri-1/h=1.98横坐标有交点,也就是说小于10根的根数选择不适合。选择10根结构时,型线宽高比为1.85,符合1.5~2.0的区间要求。同时核算每根导体的截面,同样通过式5.2.4d计算可得,每根导体截面为25.8平方,在可控截面范围之内。其中,a2为第2层每根型线截面积,d2为第2层型线外径,d1为第一层型线外径,m2为第2层根数,π为圆周率。依此类推:第3层根数为14;第4层根数为18根;第5层根数为22根。分别计算每层每根单丝截面,都在25平方左右。这样推导下来,导体整体结构为71根,排列为1+6+10+14+18+22,导体结构参数如表3所示,每层导体型线尺寸参数如表4所示。表31800平方型线绞合导体称重截面设计数据表4每层导体型线尺寸参数步骤5,对型线进行角度修正,通过角度修正后,根据每层型线尺寸参数,设计绘制每层单根型线成品截面图。型线同心绞合导体,每层每根单丝型线是以一定角度缠绕绞合轴线的,因此在绞合导体的横截面上,各单丝型线的剖面,型线宽度将会增加。这种现象在圆形导体绞合也存在,将圆形绞合导体垂直轴向剖开,观察圆形单丝成了椭圆形,也就是增加了宽度。对型线进行角度修正的计算公式为:α=(360/mi)-β其中,i为型线所处的层数;mi为第i层型线根数,β为角度收缩值。所述角度收缩值β的由以下步骤得到:步骤5.1,绘制型线角度收缩曲线图,如图2所示,其中横坐标表示绞合节径比,纵坐标为角度收缩值,曲线表示型线根数(从下至上依次代表6根、8根、10根、12根、14根、16根、18根、20根、22根、24根)。步骤5.2,根据每层型线的根数和节径比,在型线角度收缩曲线图上找到相应的角度收缩值。所述型线角度收缩曲线图根据以下多项式连列推导计算后绘制:w1=ro×sin(β1)w2=ro×sin(β2)其中,w1为绞合前型线宽度,w2为绞合后型线宽度,d为导体外径,h为每层型线高度,ro为型线外弧半径,β1为绞合前型线角度的一半,β2为绞合后型线角度的一半。型线角度收缩曲线图可以测算出每层不同根数、不同节径比情况下,由于绞合加宽因素造成的型线设计角度的减少值。通过曲线测算型线挤出成品角度收缩值如表5所示。表5型线挤出成品角度收缩值绞合层数型线根数节径比设计角度收缩第1层6250.4°第2层10200.4°第3层14180.5°第4层18150.6°第5层22130.6°步骤6,通过角度修正后,并根据表4及表5每层导体型线尺寸参数,设计绘制每层单根型线成品截面图,绘制成品型线尺寸图。以上所述的具体实施例,对本发明的目的、技术方案和有益效果进行了进一步详细说明,所应理解的是,以上所述仅为本发明的具体实施例而已,并不用于限制本发明,凡在本发明的精神和原则之内,所做的任何修改、等同替换、改进等,均应包含在本发明的保护范围之内。当前第1页12