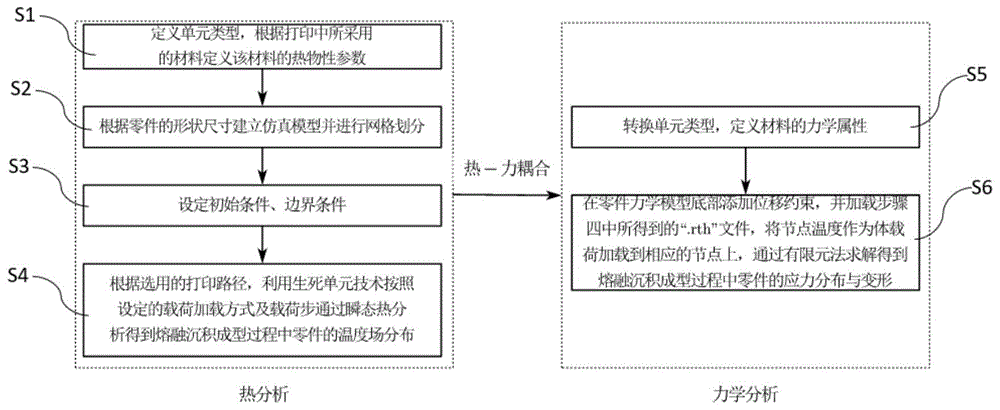
本发明涉及先进制造领域,尤其涉及一种熔融沉积制造过程中打印件的温度与翘曲变形的预测方法。
背景技术:
:近年来fdm(fuseddepositionmodeling,熔融沉积成型)以其低成本、易维护、成型材料广且价格较低、占用空间小等特点得到广泛应用。利用fdm技术进行模型的成型时,所采用的的材料基本为热塑性材料,材料在喷嘴处被加热,熔融的材料从喷嘴挤出并随着喷嘴的运动一层层堆积,随后逐渐冷却,最终形成所需的模型。在成型过程中材料会经历多次的不均匀的加热与冷却循环,这就造成了模型各处固化时间不同以及温度场、应力场分布不均,进而导致翘曲变形,甚至出现层间脱粘、开裂等失效现象,影响成型精度。为尽量避免零件失效,减小零件的翘曲变形,一般在正式生产前需要打印试块进行试错试验,得到较为合理的打印参数。但是该过程受资金和时间成本的限制,且实验中受到测量手段的限制,并不能很好地得到零件在成型过程中的温度、应力的分布状况,也不能预测整个零件的翘曲变形。技术实现要素:鉴于以上所述现有技术的缺点,本发明的目的至少在于提供一种熔融沉积制造过程中打印件的温度与翘曲变形的预测方法,旨在解决现有技术中心由于资金和时间成本的限制所导致的无法预测零件在成型过程中的温度、应力的分布及翘曲变形的情况。为实现上述目的及其他相关目的,本发明的一个实施方式提供一种熔融沉积制造过程中打印件的温度与翘曲变形的预测方法,包括步骤:获取所述打印件的仿真模型并对所述模型进行网格划分;获取所述模型的热学属性相关参数;以进行网格划分后的模型及所述热学相关参数为依据,利用瞬态热分析,获得打印件在熔融沉积成型过程中的温度分布;获取所述模型的力学属性,得到所述打印件的力学模型;以所述力学模型及所述打印件在熔融沉积成型过程中的温度分布为依据,获得打印件在熔融沉积成型过程中的应力分布与形变。在一个实施方式中,获取所述模型并对所述模型进行网格划分的步骤包括:根据待打印的零件形状尺寸建立仿真模型;将打印线宽定义为单元格的长与宽,分层层厚定义为单元格的高,对所述模型进行网格划分。在一个实施方式中,所述热学属性相关参数包括:单元类型、打印材料的热物性参数、熔融沉积制造装置的热学属性初始条件、打印件的热学属性边界条件、扫描方式、载荷加载方式及载荷步中的至少一种。在一个实施方式中,所述热物性参数包括:密度,比热容,导热系数,综合换热系数中的至少一种。在一个实施方式中,以进行网格划分后的模型及所述热学相关参数为依据的步骤包括:定义所述热物性参数;设定初始条件、边界条件、载荷加载方式及载荷步;确定扫描方式,以生死单元技术、设定的载荷加载方式及载荷步为依据。在一个实施方式中,所述载荷加载方式为阶跃方式加载载荷。在一个实施方式中,载荷步的步长为动态步长,是根据打印速度以及单元格长度进行设置的。在一个实施方式中,获取所述模型的力学属性的步骤包括:进行单元类型转换;定义单元类型转换后的材料的力学属性,所述力学属性包括:弹性模量、泊松比、热膨胀系数、拉伸屈服应力中的至少一种。在一个实施方式中,以所述力学模型及所述打印件在熔融沉积成型过程中的温度分布为依据,获得打印件在熔融沉积成型过程中的应力分布与形变的步骤包括:在所述力学模型底部添加位移约束;根据打印件在熔融沉积成型过程中的温度分布,将节点温度作为体载荷加载到相应的节点上;利用有限元法求解得到打印件在熔融沉积成型过程中的应力分布与形变。在一个实施方式中,根据打印件在熔融沉积成型过程中的温度分布,将节点温度作为体载荷加载到相应的节点上的步骤包括:通过读取命令,读取打印件在熔融沉积成型过程中的温度分布的结果文件;将节点温度作为体载荷加载到相应的节点上。本发明实施方式提供的上述技术方案,利用ansys对熔融沉积成型过程中零件进行热-力耦合计算,可一次性计算得到在熔融沉积制造过程中模型的温度分布、应力分布以及变形量,预测零件成型过程中的温度分布及最终翘曲变形;为优化打印参数、减少打印件的缺陷提供技术支持。附图说明图1显示为本发明所述方法的原理图;图2显示为本发明所述方法的具体实施流程图;图3显示为模型网格划分结果图;图4显示为扫描方式示意图;图5a显示为利用本发明所述方法测得的零件刚打印成型时的变形分布图;图5b显示为利用本发明所述方法测得的零件刚打印成型时的温度分布图;图6a显示为利用本发明所述方法测得的零件冷却20s时的变形分布图;图6b显示为利用本发明所述方法测得的零件冷却20s时的温度分布图。元件标号说明标号名称1长方体模型11第一层12第二层13第三层具体实施方式以下由特定的具体实施例说明本发明的实施方式,熟悉此技术的人士可由本说明书所揭露的内容轻易地了解本发明的其他优点及功效。请参阅图1及图2,其中,图1为本发明设计一种熔融沉积制造过程中打印件的温度与翘曲变形的预测方法的原理图,该方法是基于apdl语言的,是用于对熔融沉积成型过程中零件的温度分布、应力分布以及翘曲变形进行分析,并最终预测零件打印过程中的温度分布及最终翘曲变形情况,为优化打印参数,从而减小利用fdm技术打印零件产生的翘曲变形提供技术支持。图2为本发明所述方法的具体实施流程,该方法主要包括以下步骤:步骤s1:定义单元类型,根据打印中所采用的的材料定义该材料的热物性参数;所述步骤一中,所述的单元类型选用solid70三维热实体单元,该单元适用于瞬态或稳态热分析,且具有生死能力。所述的材料的热物性参数包括:密度、比热容、导热系数、综合换热系数,所述参数均与材料实时温度相关。所述的综合换热系数是指将热对流与热辐射综合考虑得到的,综合换热系数h的表达式如下:h=σε(tp2+tc2)(tp+tc)+hc式中:σ——斯蒂芬-玻尔兹曼常数,大小为5.67×10-8w/m2·k4;ε——材料黑度;tp——零件温度;tc——环境温度;hc——自然对流换热系数。定义密度、比热容、导热系数时采用“mptemp”与“mpdata”命令,定义综合换热系数时采用数组形式定义,本发明以聚醚醚酮(peek)为例。步骤s2:根据待打印的零件的形状尺寸建立打印件的仿真模型并进行网格划分;所述步骤二中,根据待打印零件的形状尺寸建立仿真模型并进行网格划分,具体包括以下步骤:第一步:根据所需打印的零件形状尺寸建立仿真模型;请参阅图3,图3为模型网格划分结果图,如图3所示,本发明以长方体模型1为例,进行网格划分。第二步:基于有限体积法结合分层厚度、打印线宽,将打印线宽定义为单元格的长与宽,分层层厚定义为单元格的高,进行网格划分。步骤s3:设定初始条件、边界条件;所述步骤三中,所述的初始条件为打印开始时的温度,因为利用fdm进行打印前机器会根据使用者设定的温度进行预热,所以初始温度是已知的,包括喷嘴温度、成型室温度、底板温度。所述的边界条件为已成型材料之间通过热传导进行热量传递,并且已成型材料与成型室内的空气通过热对流以及热辐射进行热量传递,并且材料从熔融态逐渐冷却至固态的过程中存在相变,也就存在相变潜热,通过采用比热容突变法对其进行处理,即以物质比热容的突变来代替潜热的作用。在ansys中是通过材料的焓来计入潜热,比焓的单位为kj/kg,其计算公式如下:h=∫ρc(t)dt式中,h——焓值;ρ——材料密度;c(t)——材料的比热容随温度变化的函数。步骤s4:根据选用的扫描方式,利用生死单元技术按照设定的载荷加载方式及载荷步通过瞬态热分析得到熔融沉积成型过程中零件的温度分布;所述步骤四中,所述的生死单元技术是指如果模型中增添或者删除材料,模型中相应的单元就存在或者消亡。单元的“死亡”并不是将其从模型中删除,而是将其刚度矩阵或者传导矩阵或者其他特性矩阵与一个很小的因子[estif]相乘,该因子默认为1.0e-6,使其单元载荷、质量、刚度、比热等都设为0,死单元的质量和能量都不包括在模型的求解结果中,单元的应变在“杀死”的同时也将设为0;单元的“出生”也不是在模型中加入了新的单元,而是将其重新激活,激活后其刚度、质量、单元载荷等都将恢复原始的数值。所述的载荷加载方式在ansys中包括斜坡施加方式与阶跃施加方式。在利用fdm打印零件过程中,喷嘴离打印平面的距离很短,且丝材的挤出速度较快,所以丝材从喷嘴到成型面的时间非常短,这一过程中材料的散热可忽略不计,所以采用阶跃方式加载载荷。所述的载荷步的步长根据打印速度以及单元格长度进行设置,并采用动态步长。请参阅图4,图4显示为扫描方式示意图。如图4所示,本发明以沿x、y轴平行往复扫描为例,长方体模型1被分为第一层11,第二层12,第三层13,具体扫描路线为图中的带有方向的标识线。进一步地,所述步骤四的具体步骤如下:第一步:通过“ekill,all”命令,将所有有限元单元都“杀死”;第二步:按照设定的路径通过“ealive”命令依次激活第n个单元;第三步:依次在第n个单元节点上施加温度载荷以及对流辐射条件;第四步:设置载荷加载方式,载荷步步长以及载荷子步;第五步:求解并删除第n个单元节点的温度载荷;第六步:判断是否所有有限元单元均已激活,若还存在没有激活的单元则返回第二步,继续循环直至所有单元被激活;第七步:进入打印完成后的冷却阶段,选择模型的表面单元,重新施加对流辐射条件;第八步:设置冷却时间,按照相同的载荷步步长以及载荷子步进行求解;第九步:进入后处理,得到零件在熔融沉积成型过程中各时刻的温度分布,从而得到温度梯度的相关信息。步骤s5:转换单元类型,定义材料的力学属性;所述步骤五中,所述的转换单元类型是将solid70转化为solid185。所述的材料的力学属性包括:弹性模量、泊松比、热膨胀系数、拉伸屈服应力,所述参数均与材料实时温度相关。定义弹性模量、泊松比、热膨胀系数时采用“mptemp”与“mpdata”命令。根据弹塑性理论强化模型分为双线性等向强化模型、多线性等向强化模型、非线性等向强化模型,定义拉伸屈服应力时根据材料的特性选择适当的强化模型,本发明以双线性等向强化模型为例。步骤s6:在零件力学模型底部添加位移约束,并加载步骤四中所得到的“.rth”文件,将节点温度作为体载荷加载到相应的节点上,通过有限元法求解得到熔融沉积成型过程中零件的应力分布与变形。所述步骤六的具体步骤如下:第一步:在模型底部施加位移约束条件;本发明以底部完全约束为例。第二步:通过“ldread”命令读取步骤四中得到的“.rth”文件,将节点温度作为体载荷加载到相应的节点上。第三步:设置载荷加载方式为阶跃方式,将载荷步步长设置与步骤四中的载荷步步长相同,并设置载荷子步。第四步:进入后处理阶段,得到零件在熔融沉积成型过程中各时刻的应力分布,从而得到翘曲变形情况。请参阅图5a、图5b、图6a以及图6b,其中,图5a为利用本发明所述方法测得的零件刚打印成型时的变形分布图;图5b为利用本发明所述方法测得的零件刚打印成型时的温度分布图;图6a为利用本发明所述方法测得的零件冷却20s时的变形分布图;图6b为利用本发明所述方法测得的零件冷却20s时的温度分布图。从上述图中可以得知,通过本发明所述方法能够准确的获取打印件的温度分布及形变分布图。上述实施例仅例示性说明本发明的原理及其功效,而非用于限制本发明。任何熟悉此技术的人士皆可在不违背本发明的精神及范畴下,对上述实施例进行修饰或改变。因此,举凡所属
技术领域:
中具有通常知识者在未脱离本发明所揭示的精神与技术思想下所完成的一切等效修饰或改变,仍应由本发明的权利要求所涵盖。当前第1页12