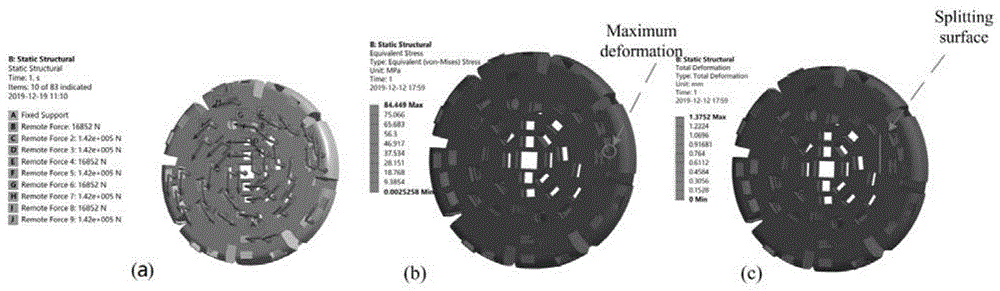
本发明涉及刀盘的结构分析
技术领域:
,特别是一种刀盘疲劳寿命预测方法及其应用。
背景技术:
:全断面隧道掘进机(fullfacetunnelboringmachine,tbm)是一种靠旋转并推进刀盘,通过盘形滚刀破碎岩石而使隧洞全断面一次成形的机器。由于具有安全、高效、快速的施工特点,在各种隧道施工中得到了广泛应用,并已成为未来的发展趋势。刀盘为隧道掘进机的关键部件之一,安装于掘进机的最前端,为大型金属结构,通常是针对某个特定工程,在某些标准约束下制作完成的零部件,承担着隧道开挖、支撑掌子面和出渣等作用,其可靠性至关重要。刀盘在工作过程中受到来自驱动系统的巨大推进力和旋转扭矩,同时在和掌子面岩石作用时还受到较大的冲击和振动,载荷复杂。在掘进过程中刀盘会出现磨损、局部开裂、温升过高等问题,其中磨损和温升过高可以通过在刀盘表面加装耐磨板和喷淋系统,通过人工检修和严格控制施工工艺来保证施工安全。刀盘裂纹一般通过无损探伤检测,在隧道施工中操作不便,也不易发现,但是在交变载荷作用下刀盘裂纹会逐渐扩展,轻则导致掘进机停工修复,延误工期,重则造成巨大的安全事故,甚至是人员伤亡。因此对刀盘进行疲劳可靠性分析,研究含裂纹刀盘结构的裂纹扩展寿命与可靠性对于提高隧道掘进机的施工效率,制定科学的刀盘检修周期,保证隧道掘进机的施工安全性和整个隧道工程顺利贯通具有重要意义。近年来,国内外专家学者针对掘进机刀盘的结构强度和疲劳性能分析等问题开展了许多研究。在刀盘的结构分析方面,程永亮等人结合掘进地质条件、刀盘结构参数和掘进参数,建立了刀具布置、开口、盘体设计等关键参数计算模型,提出相应的tbm刀盘地质适应性设计方法,并进行了工程验证,对刀盘设计方案进行了力学性能和出渣性能仿真分析。夏毅敏等人从刀盘的结构性能、刀具布置性能、力学性能、经济性、安全可靠性和环境适应性等方面建立了刀盘性能评价指标体系,提出一种基于模糊数学与评价理论的刀盘综合性能评价方法,最后工程实例进行了验证。孙伟等人提出了一套基于tbm刀盘裂纹失效区域划分的tbm刀盘裂纹位置预估与分析方法,通过tbm刀盘的应力分布,结合裂纹失效统计结果,预估tbm刀盘裂纹位置,分析计算tbm刀盘疲劳寿命裂纹所需参数,为计算tbm刀盘疲劳寿命提供基础。霍军周等人分析了tbm刀盘系统设计中,刀群与盘体支撑结构之间空间位置耦合以及支撑结构与刀盘强度刚度之间的非线性耦合关系,建立刀群与盘体支撑结构耦合布置优化模型,提出多子系统协同进化的刀具适应性布置与盘体结构耦合设计方法,并进行了工程验证,证明提出的耦合优化模型及其求解方法的可行性和有效性。laikuanglin等人针对tbm刀盘受到冲击和振动导致结构开裂问题,利用集中质量法建立了包含刀盘的tbm主机等效动力学模型,并进行了相关动力学参数的求解,分析了掘进机主机的动态响应特点,得出刀盘的多向振动比其它部件的多向振动更剧烈,振动与外界激励呈现相同的变化趋势。综上所述,以往研究侧重于刀盘的力学性能、载荷特性和结构设计与优化等方面,而未开展刀盘在含裂纹情况下的可靠性分析研究。技术实现要素:本发明提出一种刀盘疲劳寿命预测方法及其应用,针对刀盘在含裂纹情况下的疲劳裂纹扩展和可靠性问题,建立了掘进机刀盘的有限元模型,计算出刀盘的疲劳损伤容限值,建立刀盘结构的疲劳裂纹扩展寿命预测模型,计算疲劳裂纹扩展寿命,可以将刀盘裂纹分析到0.5mm精度,为刀盘结构的裂纹检测、寿命预测和可靠性评估提供了科学依据。本发明的技术方案如下:一种刀盘疲劳寿命预测方法,所述方法包括以下步骤,a、确定刀盘结构:刀盘结构为中方五分式结构,中心块和分体块连接成一个整体,刀盘面板上装有盘形滚刀,刀盘周围布置有出渣槽;b、对刀盘进行有限元分析:利用有限元方法建立刀盘的有限元模型,分析得出,刀盘的疲劳裂纹扩展的三个危险部位分别为刀盘分体面结合处、刀盘分块最大变形处和刀盘中心刀座处;c、确定刀盘的损伤容限:对刀盘进行瞬态动力学分析,得出刀盘最大应力值,然后根据断裂准则,计算出刀盘的疲劳损伤容限值,确定裂纹初始深度;d、获得合成载荷谱和雨流计数矩阵:在疲劳损伤容限值和裂纹初始深度一定的情况下,对不同工况、不同温度下掘进机刀盘的载荷谱进行合成,编制matlab程序,对载荷序列进行数据处理,对得到的载荷序列进行雨流计数,得到刀盘三个危险部位的合成载荷谱和雨流计数矩阵;e、建立刀盘结构的疲劳裂纹扩展寿命预测模型,计算疲劳裂纹扩展寿命:疲劳裂纹扩展寿命da/dn的表达式为,da/dn=f(c,m,δσ,δkth,a)=c(δkeff)m=c(δk-δkth)mr=σmin/σmax上式中,σy为材料的屈服强度,σmax为循环最大应力,σmin为循环最小应力,r为应力比,a为裂纹深度,δkth为裂纹门槛值,通过实验或者参考文献确定。在步骤a中,刀盘直径为φ7930mm,刀盘面板上共装有49把17英寸单刃盘形滚刀,4把17英寸双刃盘形滚刀,根据分布位置不同盘形滚刀分为正面滚刀和边滚刀。在步骤b中,利用ansys软件对刀盘进行有限元静力分析,得出有限元分析的应力和变形结果,通过对该结果和已有的施工工程tbm刀盘进行统计得到的数据综合分析后得出,刀盘的疲劳裂纹扩展的三个危险部位。在步骤c中,根据断裂准则可知,临界裂纹尺寸即刀盘裂纹深度方向损伤容限值ac的计算方法如下面的式(1)所示:式(1)中,α为裂纹形状系数,取1;n为安全系数,取2;σmax代表刀盘结构最大应力值(mpa);kic为刀盘的断裂韧度;对刀盘进行瞬态动力学分析,得到刀盘瞬态响应的载荷幅值,根据载荷幅值得出最大应力值,根据式(1)得出刀盘裂纹深度方向的损伤容限值ac,裂纹初始深度a0参照工程中无损检测的方法确定。在步骤c中,对刀盘进行瞬态动力学分析,分别以1级、4级盘形滚刀载荷进行加载,得到刀盘瞬态响应的1级、4级载荷幅值,根据载荷幅值和式(1)计算得出刀盘分块最大变形处的损伤容限值小于刀盘中心刀座处的损伤容限值,刀盘的损伤容限值ac取二者中的较小值。在步骤c中,a0=0.5mm。在步骤d中,裂纹应力强度因子幅值δk如下面的式(2)所示,式(2)中,α为裂纹形状系数;a为裂纹深度(m);δσ为裂纹应力幅值(mpa),由式(2)可知,刀盘疲劳扩展寿命主要考虑裂纹应力幅值和裂纹深度的影响;为了构建典型地质下刀盘载荷谱,对不同工况、不同温度下掘进机刀盘载荷谱进行合成,载荷谱合成公式如下面的式(3)所示,ni=106pi(3)式(3)中,ni是第i个工况在总累积频次中所占的频次比;pi是第i个工况占计算周期的比例;第i个工况的载荷谱外推系数为ki,式(4)中,nij为第i个工况中的第j作业段的累积频次;按照上述载荷谱编制方法,编制matlab程序。在步骤e中,还包括计算疲劳裂纹扩展速率,具体方法为:取m为确定值,lgc服从正态分布,记为,式中,n(μ,σ2)为均值μ,标准差σ的正态分布函数;μlgc表示lgc均值;表示lgc方差;裂纹扩展疲劳参数lgc取值的分布符合正态分布,取lgc~n(-10.14,0.342);疲劳裂纹扩展参数m=2.81;裂纹扩展速率lg(da/dn)的变化是由于lgc的随机变化引起,因此,其疲劳裂纹扩展速率可以表示为:[lg(da/dn)]p=lgcp+mlg△k,式中,角标p表示不同的存活率;定义lgcp=μlgc-upσlgc,up为对应于不同存活率p的标准正态偏量,查阅对应手册可得;σlgc=0.34为其标准差,于是p-da/dn-lgδk曲线可以表示为:[lg(da/dn)]p=μlgc-upσlgc+mlg(△k)。一种刀盘疲劳寿命预测方法在隧道掘进机的隧道施工中的应用。本发明的工作原理及有益效果为:本发明将刀盘结构设置为中方五分式结构,利用有限元方法建立刀盘的有限元模型,分析得出,刀盘的疲劳裂纹扩展的三个危险部位分别为刀盘分体面结合处、刀盘分块最大变形处和刀盘中心刀座处,对刀盘进行瞬态动力学分析,得出刀盘最大应力值,然后根据断裂准则,计算出刀盘的疲劳损伤容限值,确定裂纹初始深度,在疲劳损伤容限值和裂纹初始深度一定的情况下,对不同工况、不同温度下掘进机刀盘的载荷谱进行合成,编制matlab程序,对载荷序列进行数据处理,对得到的载荷序列进行雨流计数,得到刀盘三个危险部位的合成载荷谱和雨流计数矩阵,建立刀盘结构的疲劳裂纹扩展寿命预测模型,计算疲劳裂纹扩展寿命。本发明可以将刀盘裂纹分析到0.5mm精度,而目前常用超声探伤只能达到2mm精度,对小于2mm的裂纹检测困难,提出对刀盘危险部位可用磁粉检测仪检测,精度可以达到0.5mm,本发明的这一结果为刀盘结构的裂纹检测、寿命预测和可靠性评估提供了科学依据。附图说明图1为本发明中隧道掘进机的刀盘结构示意图。图2为本发明中刀盘边界条件及有限元分析结果。图3为本发明中刀盘瞬态分析云图。图4为本发明中刀盘分体面结合处的雨流计数结果。图5为本发明中刀盘分块最大变形处的雨流计数结果。图6为本发明中刀盘中心刀座处的雨流计数结果。图7为本发明中刀盘疲劳扩展寿命预测。图8为本发明中刀盘分体面结合处不同初始裂纹疲劳扩展寿命预测。图9为本发明中刀盘分块最大变形处不同初始裂纹尺寸疲劳扩展寿命。图10为本发明中刀盘中心刀座处不同初始裂纹尺寸疲劳扩展寿命。图11为本发明中刀盘分体面结合处不同幅值的疲劳裂纹扩展寿命。图12为本发明中刀盘分块最大变形处不同幅值的疲劳裂纹扩展寿命。图13为本发明中刀盘中心刀座处不同幅值的疲劳裂纹扩展寿命。具体实施方式下面结合附图和具体实施例对本发明作详细说明。一、一种刀盘疲劳寿命预测方法,包括以下步骤:a、确定刀盘结构:如图1所示,本发明隧道掘进机的刀盘结构为中方五分式结构,刀盘直径为φ7930mm,中心块和周围四个分体块采用焊接或者栓接方式连接成一个整体,刀盘面板上共装有49把17英寸单刃盘形滚刀,4把17英寸双刃盘形滚刀,根据分布位置不同盘形滚刀可以分为正面滚刀和边滚刀,刀盘周围均匀布置有八组出渣槽,设有两个人孔用于刀盘检修,tbm刀盘材料采用高强度结构钢q345d,其物理参数如表1所示。表1q345d材料物理参数序号性能指标数值1密度7850kg/m32弹性模量210gpa3泊松比0.34屈服强度σy345mpa5极限拉伸强度σu500mpa6裂纹门槛值δkth6.59mpa·m1/27断裂韧度kⅰc198.3mpa·m1/28导热系数48w/(m·k)9线膨胀系数1.2×10-510质量热容480j·m-1·k-1b、对刀盘进行有限元分析:利用ansys软件对刀盘进行有限元静力分析,采用四面体单元划分网格,其中单元数181064个,节点数333417个,边界条件设置为:在刀盘法兰上添加固定约束,盘形滚刀受力采用csm模型计算滚动力和垂直力添加于刀座处,忽略侧向力,得出有限元分析的应力和变形结果,如图2所示,csm模型计算的滚刀参数如下面的表2所示:表2csm模型计算的滚刀参数序号性能指标数值1滚刀直径216mm2贯入度6mm3刀刃宽度10mm4刀尖压力分布系数ψ0.15无量纲系数c2.126刀尖间距s100mm掘进过程中不同岩石的强度参数如下面的表3所示,一般情况下,岩石抗剪强度约为其抗压强度值的十分之一,根据tbm掘进过程可以划分为四种常见岩石硬度即岩石抗压强度情况下的推进盘形滚刀受力计算,即岩石抗压强度为40mpa、80mpa、120mpa、150mpa时,利用csm模型计算出盘形滚刀四个等级的滚刀垂直力fn和滚刀滚动力fr后进行后续分析计算,盘形滚刀的滚刀垂直力fn和滚刀滚动力fr如下面的表3所示。表3岩石参数及盘形滚刀受力预测值载荷等级岩石抗压强度岩石抗剪强度滚刀垂直力fn滚刀滚动力fr1150mpa15mpa142.00kn16.852kn2120mpa12mpa113.60kn13.482kn380mpa8mpa75.734kn8.988kn440mpa4mpa37.867kn4.494kn如图2中的(b)和(c)所示,最大应力为84.449mpa,位于刀盘分块最大变形处;最小应力为0.0025258mpa,刀盘的最大变形为1.3752mm,位于刀盘中心,由于刀盘结构的应力远低于材料的屈服强度,因此刀盘结构具有较高的安全系数,通过对已有的施工工程tbm刀盘统计数据表明:tbm刀盘在中心刀座焊缝、刀盘分体结合面、分块最大变形处、出渣板等位置容易失效,由于出渣板处的失效以磨损失效为主,通过对有限元分析的结果和已有的施工工程tbm刀盘进行统计得到的数据综合分析后得出,刀盘的疲劳裂纹扩展的三个危险部位分别为刀盘分体面结合处、刀盘分块最大变形处和刀盘中心刀座处,所以下面将对刀盘的上述三个危险部位进行断裂分析;c、确定刀盘的损伤容限:一般tbm刀盘损伤为表面裂纹的缓慢扩展,扩展到一定深度,即认为刀盘失效,称为损伤容限尺寸,一般,确定损伤容限尺寸的办法有:经验法,如取板厚的80%;公式法,按照断裂准则公式计算;临界裂纹尺寸即刀盘裂纹深度方向损伤容限值ac的计算方法如下面的式(1)所示:式(1)中,α为裂纹形状系数,取1;n为安全系数,取2;σmax代表刀盘结构最大应力值(单位是mpa);q345d的断裂韧度kic可按国标gb/t2038-1991确定,kic=198.3mpa·m1/2=6270.80mpa·mm1/2;对刀盘进行瞬态动力学分析,分别以表3中的1级、4级盘形滚刀载荷进行加载,得到刀盘瞬态响应的1级、4级载荷幅值,如图3所示,根据图3(a)中所示的1级载荷幅值得出刀盘最大应力值σmax为214.16mpa,位于分块最大变形处,刀盘裂纹深度方向损伤容限值根据图3(b)中所示的4级载荷幅值得出刀盘中心的最大应力值σmax为148.29mpa,刀盘中心块裂纹深度方向的损伤容限值当裂纹深度扩展到临界尺寸时,即认为刀盘面板失去了服役能力,所以刀盘的损伤容限值ac取较小值67.95mm,裂纹初始深度一般参照工程中无损检测(超声波探伤和磁粉探伤)的方法确定,裂纹初始深度a0=0.5mm;d、获得合成载荷谱和雨流计数矩阵:掘进机刀盘的裂纹扩展主要由应力强度因子幅值△k=f(△σ)控制,刀盘由疲劳裂纹初始深度a0=0.5mm扩展到损伤容限值ac=67.95mm时的寿命即为刀盘的疲劳裂纹扩展寿命,根据“薛海.基于实测载荷谱的重载货车车钩疲劳可靠性研究[d].北京:北京交通大学,2017”、以及“d.bowness,m.m.k.lee.predictionofweldtoemagnificationfactorsforsemi-ellipticalcracksint–buttjoints[j].internationaljournaloffatigue,2000,22(5):389-396.”可知,裂纹应力强度因子幅值δk如下面的式(2)所示:式(2)中,α为裂纹形状系数;a为裂纹深度(m);δσ为裂纹应力幅值(mpa);由上面的式(2)可知,刀盘疲劳扩展寿命主要考虑裂纹应力幅值和裂纹深度的影响。同时裂纹应力强度因子幅值δk的大小又决定了裂纹扩展速率da/dn,因此,刀盘疲劳扩展寿命主要考虑裂纹应力幅值和裂纹深度两个方面的影响;tbm掘进过程中,面临不同的岩层,所需破岩力等载荷参数也不同,根据某引水隧洞地质勘探和施工方反馈数据:岩石单轴抗压强度值大于150mpa的占60%、101-150mpa的占30%、小于101mpa的占10%;由于地层随机出现、温度始终处在循环交变,因此,为了构建典型地质下刀盘载荷谱,需要对不同工况、不同温度下掘进机刀盘载荷谱进行合成,载荷谱合成公式如下面的式(3)所示:ni=106pi(3)式(3)中,ni是第i个工况在总累积频次中所占的频次比;pi是第i个工况占计算周期的比例;第i个工况的载荷谱外推系数为ki,式(4)中,nij为第i个工况中的第j作业段的累积频次;按照上述载荷谱编制方法,编制matlab程序,对载荷序列进行数据处理,对得到的载荷序列进行雨流计数,合成的刀盘分体面结合处的合成载荷谱和雨流计数矩阵如图4所示,刀盘分块最大变形处的合成载荷谱和雨流计数矩阵如图5所示,刀盘中心刀座处的合成载荷谱和雨流计数矩阵如图6所示;由图4可知,分体面结合处载荷幅值较大,这与其应力均值大直接相关,载荷时间序列进行雨流计数后得到的,主要的幅值频次出现在300mpa(频次约500)和450mpa(频次约200)附近,均值基本在150mpa以内,其它频次出现几乎为零。由图5可知,刀盘分块最大变形处载荷幅值在200mpa附近有一个集中,频次约400;载荷幅值200-400mpa出现机会基本均等,频次约200,无过大差距;均值100mpa以内占据了绝大多数,其它部分占比很少,可以忽略。由图6可知,刀盘中心刀座处的雨流计数矩阵有两个峰值中心,一个在120mpa附近,频次约500,另一个在300mpa附近,频次约300,均值均小于100mpa;按照平均载荷作业循环时间来计算,合成工况载荷谱每加载一次,相当于掘进3.33×104次循环,按照tbm施工数据,贯入度一般为6mm/r,刀盘转速为6r/min,每个典型载荷谱相当于掘进里程为19.98m;e、建立刀盘结构的疲劳裂纹扩展寿命预测模型,计算疲劳裂纹扩展寿命:疲劳裂纹扩展寿命da/dn的表达式为,上式(5)中,σy为材料的屈服强度,σmax为循环最大应力,σmin为循环最小应力,r为应力比,r随时会变化,a为裂纹深度,δkth为裂纹门槛值,c、m同存活率相关,c为疲劳扩展系数;m为疲劳裂纹扩展指数,通过实验或者参考文献确定,本发明中,a的初始尺寸为a0=0.5mm,临界尺寸为ac=67.95mm,计算过程进行中a逐步累加,达到ac时,计算终止。由表1可知,高强度结构钢q345d的屈服强度σy=345mpa,裂纹门槛值δkth=6.59mpa·m1/2。疲劳裂纹扩展速率直接受到c和m的影响,基于疲劳裂纹扩展试验数据,采用m为定值和lgc服从正态分布计算疲劳裂纹扩展速率,具体方法为:取m确定值,lgc服从正态分布,即c服从对数正态分布的单随机变量理论,记为:式中,n(μ,σ2)为均值μ,标准差σ的正态分布函数;μlgc表示lgc均值;表示lgc方差;根据文献liangzong,gangshi,yuanqingwang.experimentalinvestigationonfatiguecrackbehaviorofbridgesteelq345qdbasemetalandbuttweld[j].materialsanddesign,2015,66:196-208.给出的研究结果:裂纹扩展疲劳参数lgc取值的分布符合正态分布,取lgc~n(-10.14,0.342);疲劳裂纹扩展参数m=2.81;由3σ准则可知,在(μ-3σ,μ+3σ)区间内的概率为99.74%,对于超出该置信区间的数据,其存在概率小于千分之三,可以忽略不计;裂纹扩展速率lg(da/dn)的变化是由于lgc的随机变化引起,因此,其疲劳裂纹扩展速率可以表示为:[lg(da/dn)]p=lgcp+mlg△k(8)式(8)中,角标p表示不同的存活率;定义lgcp=μlgc-upσlgc,up为对应于不同存活率p的标准正态偏量,查阅对应手册可得;σlgc=0.34为其标准差,于是p-da/dn-lgδk曲线可以表示为:[lg(da/dn)]p=μlgc-upσlgc+mlg(△k)(9)存活率p=50%时的标准正态偏量up=0,裂纹扩展速率公式为:存活率p=90%的标准正态偏量up=-1.232,裂纹扩展速率公式为:存活率p=95%的标准正态偏量up=-1.645,裂纹扩展速率公式为:存活率p=99%的标准正态偏量up=-2.326,裂纹扩展速率公式为:由此,得到了不同存活率的疲劳裂纹扩展速率公式。对于每一个微小的裂纹深度增量△a,存在对应的△n满足:da/dn=△a/△n,于是可以知道,每当载荷作用一次,就要重新计算一次裂纹应力强度因子,于是有:式(10)中,△nn为载荷循环作用次数(cycle);an为第n次循环时裂纹尺寸(m);an+1为经过△nn为载荷循环作用时裂纹尺寸(m);△an为裂纹经过△nn为载荷循环作用的增量(m);nn+1为与an+1对应的载荷循环次数(cycle)。通过matlab编程分别将计算所需的载荷谱、计算参数导入程序,计算求得tbm刀盘不同位置的疲劳裂纹扩展寿命,计算的刀盘转速ω=6r/min,刀盘滚刀贯入度p=6mm/r,由此可以将疲劳裂纹扩展寿命转化为掘进里程,计算结果如图7所示。由图7可知,不同可靠度下、不同位置的tbm刀盘疲劳裂纹扩展寿命相差很大,中值下tbm刀盘掘进里程为29.11km。主要原因有:由于应力幅值是裂纹扩展最主要的驱动力,在刀盘分体面结合处的应力最大,分块最大变形处的应力次之,中心刀座处应力最小,随着裂纹扩展循环的进行,初始较小的应力差距导致的裂纹扩展速率变化很大,因此结构裂纹疲劳扩展寿命差距较大;当可靠度从50%增加到90%的时候,三处裂纹扩展速率增加很大,导致结构疲劳裂纹扩展寿命减小,当可靠度从90%增加到99%时,结构裂纹扩展寿命继续减小,二者相比,后一段疲劳裂纹扩展寿命变化幅度小,但变化率较大;通过掘进速度和载荷作用次数的转换,tbm刀盘掘进里程可以作为tbm刀盘设计、检修和再制造的依据,同时方便施工单位使用,具有工程实际意义。相关的结果可以给工程技术人员提供参考,在长大隧道、硬岩/超硬岩隧道施工时,tbm刀盘受力急剧增加,对tbm刀盘结构耐久性、可靠性提出了更高的要求,可以进行定量评估,以适应不同的工程项目、不同地质条件等对tbm刀盘疲劳寿命的影响,并采取合理措施提高刀盘结构可靠性。对图7进行分析得出,数据点与二参数的威布尔分布曲线较为接近,表达式为:式(11)中,r(l)为可靠度函数,介于0到1之间;l为掘进里程(km);θ为尺度参数;β为形状参数;且有θ>0,β>0;为了便于区别,记分体面结合处、分块最大变形处和中心刀座处的下标分别为1、2、3,也就是可靠度函数和尺度系数分别记为r1(l)、r2(l)、r3(l)和θ1、θ2和θ3。由图7可知,可靠度函数r(l)曲线的拟合相关性较好,可靠性趋势下降比较平缓。函数表达式建立了任意掘进里程l与可靠度r之间的函数对应关系,二者一一对应,可以方便求解任意可靠度对应的掘进里程或计算掘进里程对应的结构可靠度。二、刀盘可靠性的影响因素tbm刀盘掘进过程中刀盘结构形式、初始裂纹尺寸、刀盘载荷、施工环境等因素影响刀盘安全性和可靠性,其中刀盘载荷幅值、初始裂纹尺寸等参数对刀盘结构安全寿命影响较大,直接影响了tbm刀盘安全掘进里程。(一)裂纹初始深度对tbm刀盘的安全性分析当tbm刀盘经历一定的应力循环之后会萌生裂纹,刀盘裂纹初始深度的确定受到检测仪器精度等的影响。针对不同裂纹初始深度对刀盘疲劳裂纹扩展寿命的影响问题,利用典型地质下刀盘载荷谱对以上三个刀盘疲劳寿命危险部位进行寿命计算,刀盘分体面结合处在存活率p为0.5、0.9、0.95、0.99时不同初始裂纹疲劳扩展寿命计算结果如图7所示。由图7可知,刀盘初始裂纹尺寸对结构疲劳裂纹扩展寿命有较大影响,当初始裂纹尺寸小于0.5mm时,刀盘结构疲劳裂纹扩展寿命随着初始裂纹尺寸减小而增大,且对掘进里程的影响很大;当可靠度要求较高时,疲劳裂纹扩展寿命变小,且差值较大;对于同等的可靠度要求时,以0.5mm为分界,小于0.5mm时,结构疲劳裂纹扩展寿命相应的增大,而且随着尺寸减小而急剧增加,表明裂纹在初始阶段扩展速率低,扩展缓慢,随着裂纹尺寸的增大,扩展速度逐渐增加,裂纹在扩展到一定尺寸(临界尺寸)后会由于结构的强度不足或者是因为裂纹扩展速率急剧增大而发生瞬断。由此可以知道疲劳裂纹初始深度对计算结构的疲劳裂纹扩展寿命影响较大,因此提高对微小初始裂纹的检测能力,提高初始裂纹尺寸的检测精度对预测结构疲劳裂纹寿命有积极意义。通过计算,刀盘分块最大变形处在存活率p为0.5、0.9、0.95、0.99时不同初始裂纹疲劳扩展寿命计算结果如图9所示。由图9可知,由于分块最大变形处载荷幅值小,所以此处的刀盘结构扩展寿命比分体面结合处大;因为裂纹扩展的初始阶段扩展速率较小,当裂纹初始深度小于0.5mm时,疲劳裂纹扩展寿命大幅增加;裂纹尺寸介于0.5-1mm之间时,裂纹扩展寿命变化很小,图形趋近于直线,从数值上来说,疲劳裂纹扩展寿命几乎增加了一倍;可靠度要求较高时,裂纹扩展寿命很短。同样,通过计算得出刀盘中心刀座处在存活率p为0.5、0.9、0.95、0.99时不同初始裂纹疲劳扩展寿命计算结果如图10所示。由图10可知,随着可靠度的增大,结构疲劳裂纹扩展寿命急剧减小,从中值的疲劳寿命掘进里程来看,几乎下降到了四分之一,表明对结构可靠性要求的加强会显著降低安全掘进里程,从中值到99%可靠度的变化过程中,疲劳裂纹扩展寿命掘进里程显著降低,大约下降到了40%。(二)含裂纹tbm刀盘过载作用下安全性分析对典型地质下刀盘载荷谱分别给予不同的幅值系数,分析不同载荷谱过载系数对裂纹扩展寿命的影响,如图11、图12和图13所示,分别为tbm刀盘分体面结合处、分块最大变形处和中心刀座处不同倍数的载荷幅值时疲劳寿命掘进里程的变化情况。由图11可知,当载荷谱倍乘系数进行疲劳裂纹扩展“加速”后,刀盘分体面结合处的裂纹扩展寿命大幅下降,分别对应1.2倍载荷谱幅值系数和1.5倍载荷谱幅值系数时,幅值系数倍数较大者下降幅度较大,当位于可靠度90-99%区间时,裂纹扩展寿命仍然在继续减小,由于此时裂纹扩展寿命掘进里程都比较小,因此数值比较接近,载荷谱倍乘系数对裂纹扩展寿命的影响相对变小。由图12可知,当可靠度为50%时,刀盘分块最大变形处的疲劳裂纹扩展寿命大幅下降,从55.0805km下降到了约四分之一15.6857km,说明载荷谱幅值倍数对疲劳裂纹扩展寿命影响很大;当可靠度增加到90%时,疲劳裂纹扩展寿命基本下降到中值(50%可靠度)的一半,随着可靠度增长,掘进里程继续减少;可靠度位于90%~99%之间时,疲劳裂纹扩展寿命下降较快,变化速率大,过大的载荷幅值将会严重的影响结构裂纹扩展寿命,使结构裂纹扩展寿命减小。由图13可以看出,刀盘中心刀座处的载荷谱幅值倍数越大,裂纹扩展寿命减少越快,随着可靠度增加,结构安全寿命的减小就越来越快,即变化率更大,当载荷谱幅值为典型载荷谱的幅值1.5倍时,结构安全扩展寿命不到其三分之一,可见此处的载荷幅值影响很大,对tbm刀盘结构安全寿命影响也更大。通过以上分析表明,在刀盘三处危险部位的初始裂纹尺寸和载荷幅值对刀盘疲劳裂纹扩展寿命影响较大,在刀盘加工完成后采用合适的检测方法,确定刀盘的初始裂纹尺寸,并在施工过程中根据地质情况合理控制掘进参数,对于提高刀盘的疲劳可靠性具有重要的作用。三、一种刀盘疲劳寿命预测方法的工程应用隧道tbm掘进施工标段围岩主要为安山岩凝灰岩和火山岩,近70%岩石的单轴抗压强度达到或超过140mpa,个别地方甚至可以达到200mpa。在隧道掘进机的掘进过程中,刀盘平均推力约10500kn。为了验证理论分析的正确性,进行了刀盘掘进跟踪试验。tbm刀盘在隧道掘进过程中,为了确保安全,会定期对刀盘进行检查,例如检查测量刀具磨耗、刀盘面板裂纹、焊缝开裂等,以便于及时的对刀盘进行修补,确保施工安全。在掘进至5km处,检查中发现刀盘中心刀座处存在刀座变形、开裂和刀座焊缝开裂,刀盘上刀座位置由于局部应力集中发生了裂纹,裂纹扩展将使该部分结构逐步失去服役能力,导致刀座振动加大、盘形滚刀异常的磨耗,于是停机进行了检修。裂纹扩展深度为70mm,由图13可知,当可靠度为99%时,理论计算的中心刀座处裂纹扩展寿命为5.56km,与tbm刀盘掘进距离5km的误差为11.2%,验证了损伤容限数值的正确性,对工程应用有一定的指导意义。修复刀盘的具体过程如下所示:第一步,刨除刀座露出母材、修整出焊接坡口;第二步,按照焊接工艺进行分段、对称焊接,过程中保证温度合适;第三步,焊接后进行保温,消除焊接应力;第四步,渗透探伤检查。完成修复后,检查达到合格标准,方可继续进行掘进施工。当前第1页12