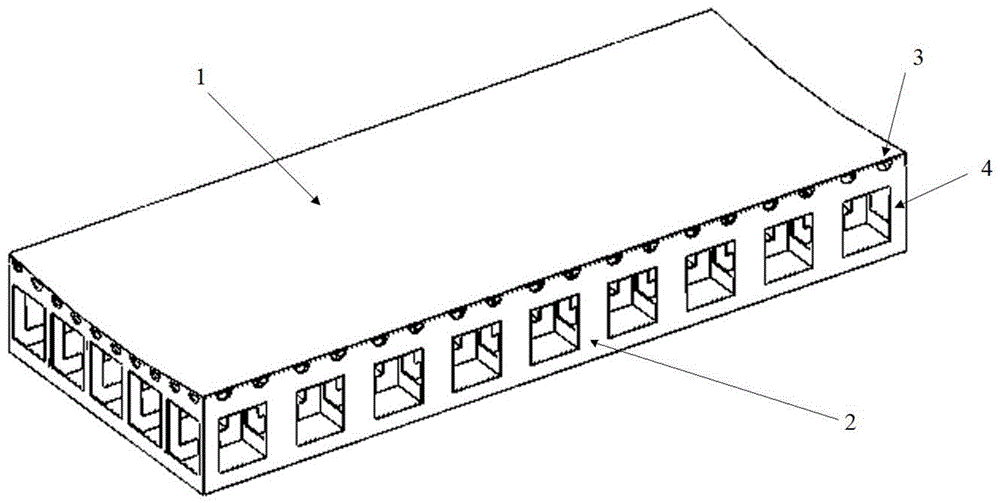
本发明涉及拓扑优化设计领域,特别是涉及一种热压罐成型框架式模具的整体拓扑优化设计方法。
背景技术:
复合材料凭借其较高的比强度、比刚度、抗疲劳和耐腐蚀等优越的性能,在飞机结构中的占比越来越大,也逐渐应用到了飞机的大型主承力结构中。其中热压罐成型是热固性复合材料的主要制造方式,成型过程中,复合材料预浸料铺贴于模具表面,模具的变形会直接影响到复合材料构件的形状和尺寸精度,模具型面的温度均匀性影响复合材料的同步固化性。框架式模具作为热压罐成型的关键工装,随着结构件尺寸的不断增大,模具的支撑结构形式将会变得更加复杂,若模具的结构排布不合理,一方面会导致模具质量过大、刚度降低,对搬运环节带来困难;另一方面还会导致模具的通畅性较差,导致成型过程中模具表面的温度分布过于不均匀,从而降低构件的同步固化度。在实际设计过程中往往依据经验反复调整框架式结构构型,导致设计效率低、成本高。
目前,针对热压罐成型框架式模具的优化设计方法的研究分析主要有以下两类:
文献1“wangqing,wanglingyun,zhuweidong,etal.designoptimizationofmoldsforautoclaveprocessofcompositemanufacturing[j].journalofreinforcedplasticsandcomposites,2017,36(21):1564-1576.doi:10.1177/073168441771265”中,作者提出了一种将数值模型与遗传算法相结合的模具子结构参数优化方法,以提高模具固化的同步性。文中将框架式模具长、宽方向支撑板数量、支撑板厚度、通风孔形状、以及通风孔与模具边缘间距五个参数作为设计参数进行优化设计,将最大固化度标准差提高了17.21%,但文中设计参数选择具有局限性,且没有考虑改变参数后对模具的静刚度和热变形的影响。
文献2“张铖.大型复合材料结构热压罐工艺温度场权衡设计[d].哈尔滨工业大学,2009.”中,作者通过实验验证了使用cfx软件模拟模具温度场的可靠性,提出了将热压罐成型过程中模具型面的最大温差作为评价模具温度场均匀程度的表征值,对模具型面及加筋厚度、模具纵向长度、模具横向长度、通风孔形状(圆形、方形)及几何尺寸变化这四个参数对模具温度场的影响规律进行了研究,并且对风速、升温速率、降温速率和模具摆放位置这四个工艺因素对模具温度场的影响规律进行了探索,得到设计参数和工艺因素对模具温度场的影响规律,对模具优化设计有很大的参考意义,但是文中的设计参数选择依然具有局限性,同时缺乏改变参数后对模具静刚度和热变形的影响,并且该种优化方法对于模具性能提高不明显。
综上,现有的热压罐成型框架式模具的优化设计,模具的优劣评判指标主要集中在热压罐成型过程中复合材料的固化度同步性和模具的型面温度均匀性,优化设计方法主要有模具子结构参数优化方法和研究一些模的基本参数对于模具性能的影响,从而得到一些相应参数对于模具的影响规律,再进行选择最优的参数进行模具的制造,但是目前的优化设计方法均没有考虑成型过程中改变模具结构对于模具静刚度和热变形的影响,同时改进模具的基本参数对于模具的整体性能并不会有很明显的提高,于是需要提出优化效果更明显的设计方法。
技术实现要素:
本发明的目的是提供一种热压罐成型框架式模具的整体拓扑优化设计方法,在考虑模具温度均匀性与减重需求的前提下,以提高模具整体刚度为目标开展了模具结构拓扑优化设计,并对优化前后的模具结构进行静刚度、温度场和热力耦合的计算,进行模具性能综合的对比分析。
为实现上述目的,本发明提供了如下方案:本发明提供一种热压罐成型框架式模具的整体拓扑优化设计方法,包括以下步骤:
s1、创建框架式模具的三维几何实体模型;
s2、创建三维几何实体模型的有限元模型,并创建有限元模型的拓扑化设计模型;
s3、根据拓扑化设计模型对框架式模具的三维几何实体模型进行重构;
s4、对重构的三维几何实体模型和原始三维几何实体模型进行性能计算和分析对比。
所述框架式模具顶面为一型面,所述型面为曲面,所述型面底部为支撑板,所述支撑板沿所述框架式模具的长度方向和宽度方向均匀交叉分布,所述支撑板上开设矩形通风孔和半圆形均温孔,所述框架式模具底部分布有四个支脚。
优选的,步骤s2中对框架式模具模型进行拓扑化设计时,首先保持模型中所述支撑板的排布方式不变,将所述支撑板做实体化设计,将实体化后的支撑板作为拓扑优化设计域,设计所述支撑板的材料分布,然后将模型进行网格划分,将模型整体分成若干六面体网格单元,同时将型面划分为壳单元;选取所述型面的最小柔顺度作为优化目标,选取支撑板区域的材料体积分数作为约束,根据模具的工作情况对模具进行边界条件的设定,最后进行拓扑优化。
优选的,s4中对重构的框架式模具和原始框架式模具进行性能计算和分析对比,包括框架式模具的质量、静刚度、在热压罐中的温度均匀性和热变形的计算:
1)分别测量原始框架式模具和优化框架式模具的体积,得到拓扑优化模具的减重情况;
2)对原始框架式模具和优化框架式模具分别进行静刚度计算:模具所受载荷简化承受自身重力,约束方式为四个底脚中的一个底脚为6自由度约束,其余三个底脚为重力方向自由度约束;
3)实现热压罐内流场温度场模拟计算:首先,采用前处理模块进行框架式模具与热压罐的耦合模型的网格划分,将模型划分为实体区域和流体区域,并且对流体域和实体域进行细节划分,然后进行热压罐成型过程模型的建立和计算,在此过程中分别进行稳态和升温阶段的计算,最后使用后处理平台进行计算结果的处理,得到升温结束时刻模具上型面的温度分布云图;
4)使用软件构建框架式模具热力耦合计算模型,对原始框架式模具和优化框架式模具分别计算热变形和热应力,边界条件设定为其中一个底脚6自由度约束,其余三底脚约束重力方向自由度,施加的载荷为框架式模具自身重力和温度载荷,得到框架式模具热变形和热应力计算结果。
优选的,所述温度载荷包括框架式模具初始状态温度载荷和框架式模具表面的温度载荷。
本发明相对于现有技术取得了以下技术效果:
现有针对复合材料热压罐成型框架式模具的优化设计研究,往往集中于对模具的支撑结构的排布形式、支撑板的厚度、通风孔的大小和形状这几个模具的基本参数,这具有很大的局限性,对模具的性能改善较小,设计效率低下、成本高,同时还缺少对模具刚度和热变形的研究。
本发明提出的框架式模具整体的拓扑优化方法,将框架式模具的三维几何模型中的支撑板进行实体化设计,将实体化后的支撑板作为拓扑优化设计域,能够改变支撑板的厚度、通风孔的大小、形状,局限性更小,能够得到不同结构的框架式模具并对其进行性能测试,选择性能最优者进行生产,从而使得本领域技术人员对支撑板结构的选择更加多样,且对提高框架式模具的整体性能具有重大意义。
另外,本发明在考虑模具温度均匀性与减重需求的前提下,以提高模具整体刚度为目标开展了拓扑优化设计,达到了优化设计模具相比按照经验设计模具减重17.2%(支撑结构减重36.1%)、最大静变形减小32%、最大静应力减小23.5%、模具在升温结束时刻最大温度差减小34%的目标,同时热变形和热应力也略有减小,优化模具的减重效果明显,并且刚度和温度均匀性有了很大的提高,明显改善了模具性能。
附图说明
为了更清楚地说明本发明实施例或现有技术中的技术方案,下面将对实施例中所需要使用的附图作简单地介绍,显而易见地,下面描述中的附图仅仅是本发明的一些实施例,对于本领域普通技术人员来讲,在不付出创造性劳动性的前提下,还可以根据这些附图获得其他的附图。
图1为框架式模具几何模型;
图2为框架式模具的有限元模型;
图3为框架式模具的拓扑优化设计模型;
图4为框架式模具的拓扑优化结果;
图5为框架式模具的重构模型;
图6为框架式模具温度场计算的有限元模型;
图7为框架式模具温度场计算模型;
其中,1-型面,2-支撑板,3-均温孔,4-通风孔,5-入口,6-出口,7-实体域,8-流体域,9-管壁,10-invar合金,11-速度为0.4m/s、压强为0.6mpa的空气。
具体实施方式
下面将结合本发明实施例中的附图,对本发明实施例中的技术方案进行清楚、完整地描述,显然,所描述的实施例仅仅是本发明一部分实施例,而不是全部的实施例。基于本发明中的实施例,本领域普通技术人员在没有做出创造性劳动前提下所获得的所有其他实施例,都属于本发明保护的范围。
本发明的目的是提供一种热压罐成型框架式模具的整体拓扑优化设计方法,在考虑模具温度均匀性与减重需求的前提下,以提高模具整体刚度为目标开展了模具结构拓扑优化设计,并对优化前后的模具结构进行静刚度、温度场和热力耦合的计算,进行模具性能综合的对比分析。
为实现上述目的,本发明提供了如下方案:本发明提供一种热压罐成型框架式模具的整体拓扑优化设计方法,包括以下步骤:
s1、创建框架式模具的三维几何实体模型;
s2、创建三维几何实体模型的有限元模型,并创建有限元模型的拓扑化设计模型;
s3、根据拓扑化设计模型对框架式模具的三维几何实体模型进行重构;
s4、对重构的三维几何实体模型和原始三维几何实体模型进行性能计算和分析对比。
为使本发明的上述目的、特征和优点能够更加明显易懂,下面结合附图和具体实施方式对本发明作进一步详细的说明。
如图1所示,本发明提供的框架式模具顶面为一型面1,型面1为曲面,型面1底部为支撑板2,支撑板2沿框架式模具的长度方向和宽度方向均匀交叉分布,支撑板2上开设半圆形均温孔3和矩形通风孔4,框架式模具底部分布有四个支脚。
如图2-3所示,本发明提供的热压罐成型框架式模具的整体拓扑优化设计方法,步骤s2中对框架式模具模型进行拓扑化设计时,首先保持模型中所述支撑板的排布方式不变,将所述支撑板做实体化设计,将实体化后的支撑板作为拓扑优化设计域,设计所述支撑板的材料分布,然后将模型进行网格划分,将模型整体分成若干六面体网格单元,同时将型面划分为壳单元。
构建模具的拓扑优化设计模型时,根据模具的工作环境和模具的特点确定优化目标和约束。由于复合材料直接与模具上型面接触,故选择模具上型面的柔顺度最小作为优化目标;为实现模具的减重和提高通畅性,选取支撑板区域的材料体积分数作为约束;随后根据模具的工作情况对模具进行边界条件和载荷的设定,对模具的四个支脚中一个六自由度约束,其余三个支脚在重力方向约束,模具受到自身重力以及型面均布压强。
本发明提供的热压罐成型框架式模具的整体拓扑优化设计方法,经过步骤s3拓扑优化后得到如图4所示的设计域结构,随后考虑优化结果和实际生产制造工艺的可行性,同时兼顾提升模具通畅性,以优化结果为参考,对模具进行重构,得到如图5所示的模具支撑结构。
本发明提供的热压罐成型框架式模具的整体拓扑优化设计方法,在步骤s4中综合比较原始模具和优化模具的性能,包括模具的质量、静刚度、在热压罐中的温度均匀性和热变形的计算。
1)使用solidworks软件分别测量原始模具和优化模具的体积,进而得到拓扑优化模具的减重情况,本发明实现模具整体减重17.2%,其中支撑结构减重36.1%,减重效果明显;
2)使用abaqus软件对两个模具分别进行静刚度计算,模具所受载荷简化为:模具承受自身重力(型面上预浸料铺层和辅助材料质量较小,可忽略不计),约束方式为其中一个支脚六自由度约束,其余3支脚重力方向自由度约束,进行静刚度计算,根据模具的静变形和应力大小对比模具的性能;
3)通过商业有限元仿真模拟软件ansys来实现热压罐内流场温度场模拟计算,首先采用前处理模块icem-cfd进行该模具与热压罐的耦合模型的网格划分,将模型划分为实体区域和流体区域,并且对流体域和实体域进行细节划分,保证网格的质量和计算精度,如图6所示;随后使用cfx模块进行热压罐成型过程模型的建立和计算,如图7所示,在该过程中需要分别进行稳态和升温阶段的计算;最后使用后处理平台cfx-post进行计算结果的后处理,得到升温结束时刻模具上型面的温度分布云图,根据升温结束时刻模具型面的最大温差来衡量模具在热压罐内的温度均匀性;
4)使用abaqus软件构建框架式模具热力耦合计算模型,对两个模具分别计算热变形和热应力,模具的边界条件设定为其中一个底脚6自由度约束,其余三底脚约束重力方向位移,施加的载荷为模具自身重力和温度载荷,其中温度载荷包括模具初始状态温度载荷(预定义温度场)和模具表面的温度载荷,得到模具热变形和热应力计算结果,根据变形和应力大小对比模具的性能。
根据实际需求而进行的适应性改变均在本发明的保护范围内。
需要说明的是,对于本领域技术人员而言,显然本发明不限于上述示范性实施例的细节,而且在不背离本发明的精神或基本特征的情况下,能够以其他的具体形式实现本发明。因此,无论从哪一点来看,均应将实施例看作是示范性的,而且是非限制性的,本发明的范围由所附权利要求而不是上述说明限定,因此旨在将落在权利要求的等同要件的含义和范围内的所有变化囊括在本发明内。不应将权利要求中的任何附图标记视为限制所涉及的权利要求。