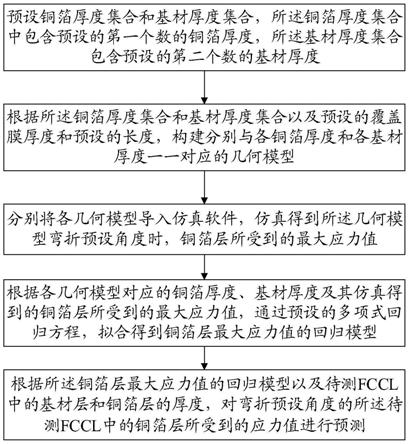
基于铜箔和基材厚度的fccl弯折疲劳应力的预测方法
技术领域
1.本发明涉及fccl测试技术领域,尤其涉及一种基于铜箔和基材厚度的fccl弯折疲劳应力的预测方法。
背景技术:2.挠性覆铜板(fccl)是指在绝缘基膜上覆盖以铜箔而形成的一种可以弯曲的薄片状复合材料,是仅次于刚性覆铜板的一个覆铜板大类品种。fccl除了具有刚性覆铜板的电气链接、绝缘、机械支撑等三大功能外,它的突出表现为可以弯曲,既可以静态弯曲,也可以动态反复弯曲,具有高挠曲性是fccl最突出的产品特征。挠性覆铜板与刚性覆铜板在产品特性上相比具有薄、轻和可挠性的特点。用fccl为基板材料的fpc被广泛应用于手机、数码相机、笔记本电脑等电子产品中。
3.如图1所示的结构是一种传统的单层fccl覆铜板与覆盖膜组合结构,包括依次层叠的基材层1、铜箔层2和覆盖膜层3。因其良好的运用场景,对于fccl覆铜板折弯寿命的研究也是各大软板厂商亟待关切的问题,而为了达到良好的机械性能,fccl结构往往采用不同的叠构搭配,通常通过改变fccl结构中的铜箔厚度或者基材厚度来实现折弯次数的要求,折弯寿命测试是一项费时费力的测试过程,市面上现有折弯测试设备多针对特定的测试场景和条件,不能测试在不同折弯曲率工况下的折弯寿命,同时测试噪音过大、测试设备尺寸过大、成本高、安全系数低也是限制fccl折弯寿命的重要因素。
技术实现要素:4.本发明所要解决的技术问题是:提供一种基于铜箔和基材厚度的fccl弯折疲劳应力的预测方法,可提高折弯寿命测试的效率,降低测试成本。
5.为了解决上述技术问题,本发明采用的技术方案为:一种基于铜箔和基材厚度的fccl弯折疲劳应力的预测方法,所述fccl包括依次层叠的基材层、铜箔层和覆盖膜层,所述预测方法包括:
6.预设铜箔厚度集合和基材厚度集合,所述铜箔厚度集合中包含预设的第一个数的铜箔厚度,所述基材厚度集合包含预设的第二个数的基材厚度;
7.根据所述铜箔厚度集合和基材厚度集合以及预设的覆盖膜厚度和预设的长度,构建分别与各铜箔厚度和各基材厚度一一对应的几何模型;
8.分别将各几何模型导入仿真软件,仿真得到所述几何模型弯折预设角度时,铜箔层所受到的最大应力值;
9.根据各几何模型对应的铜箔厚度、基材厚度及其仿真得到的铜箔层所受到的最大应力值,通过预设的多项式回归方程,拟合得到铜箔层最大应力值的回归模型;
10.根据所述铜箔层最大应力值的回归模型以及待测fccl中的基材层和铜箔层的厚度,对弯折预设角度的所述待测fccl中的铜箔层所受到的应力值进行预测。
11.本发明的有益效果在于:通过构建对应不同铜箔厚度和基材厚度的几何模型,并
利用仿真软件仿真得到不同厚度组合下的fccl弯折时铜箔层所受到的应力值,可极大地缩短通过试验设备获取数值的周期,极大地提高了效率且降低了成本;通过利用多项式回归模型进行拟合,得到铜箔层最大应力值的回归模型,后续可根据该回归模型来对待测fccl中的铜箔层所受应力进行预测,可以预测铜箔折弯寿命。本发明的方法操作简单,可操作性强,适用于不同铜箔厚度、不同基材厚度组合的fccl叠构应力值预估。
附图说明
12.图1为本发明的fccl的结构示意图;
13.图2为本发明的基于铜箔和基材厚度的fccl弯折疲劳应力的预测方法的流程图;
14.图3为本发明实施例一的方法流程图。
15.标号说明:
16.1、基材层;2、铜箔层;3、覆盖膜层。
具体实施方式
17.为详细说明本发明的技术内容、所实现目的及效果,以下结合实施方式并配合附图详予说明。
18.请参阅图2,一种基于铜箔和基材厚度的fccl弯折疲劳应力的预测方法,所述fccl包括依次层叠的基材层、铜箔层和覆盖膜层,所述预测方法包括:
19.预设铜箔厚度集合和基材厚度集合,所述铜箔厚度集合中包含预设的第一个数的铜箔厚度,所述基材厚度集合包含预设的第二个数的基材厚度;
20.根据所述铜箔厚度集合和基材厚度集合以及预设的覆盖膜厚度和预设的长度,构建分别与各铜箔厚度和各基材厚度一一对应的几何模型;
21.分别将各几何模型导入仿真软件,仿真得到所述几何模型弯折预设角度时,铜箔层所受到的最大应力值;
22.根据各几何模型对应的铜箔厚度、基材厚度及其仿真得到的铜箔层所受到的最大应力值,通过预设的多项式回归方程,拟合得到铜箔层最大应力值的回归模型;
23.根据所述铜箔层最大应力值的回归模型以及待测fccl中的基材层和铜箔层的厚度,对弯折预设角度的所述待测fccl中的铜箔层所受到的应力值进行预测。
24.从上述描述可知,本发明的有益效果在于:操作简单,可操作性强,适用于不同铜箔厚度、不同基材厚度组合的fccl叠构应力值预估,极大地提高了测试效率且降低了测试成本。
25.进一步地,所述根据所述铜箔厚度集合和基材厚度集合以及预设的覆盖膜厚度和预设的长度,构建分别与各铜箔厚度和各基材厚度一一对应的几何模型之后,进一步包括:
26.分别将各几何模型导入仿真软件,仿真得到所述几何模型弯折预设角度时,基材层所受到的最大应力值;
27.根据各几何模型对应的铜箔厚度、基材厚度及其仿真得到的基材层所受到的最大应力值,通过预设的多项式回归方程,拟合得到基材层最大应力值的回归模型;
28.根据所述基材层最大应力值的回归模型以及待测fccl中的基材层和铜箔层的厚度,对弯折预设角度的所述待测fccl中的基材层所受到的应力值进行预测。
29.进一步地,所述根据所述铜箔厚度集合和基材厚度集合以及预设的覆盖膜厚度和预设的长度,构建分别与各铜箔厚度和各基材厚度一一对应的几何模型之后,进一步包括:
30.分别将各几何模型导入仿真软件,仿真得到所述几何模型弯折预设角度时,覆盖膜层所受到的最大应力值;
31.根据各几何模型对应的铜箔厚度、基材厚度及其仿真得到的覆盖膜层所受到的最大应力值,通过预设的多项式回归方程,拟合得到覆盖膜层最大应力值的回归模型;
32.根据所述覆盖膜层最大应力值的回归模型以及待测fccl中的基材层和铜箔层的厚度,对弯折预设角度的所述待测fccl中的覆盖膜层所受到的应力值进行预测。
33.由上述描述可知,不仅可以预测铜箔折弯寿命,还可以预测基材及覆盖膜折弯寿命。
34.进一步地,所述预设角度为135
°
。
35.由上述描述可知,通过选取合适的弯折角度,可保证获取到较准确的最大应力值。
36.进一步地,所述多项式回归方程为p=β0+β1x+β2y+β3x2+β4xy+β5y2,所述p为最大应力值,x表示铜箔厚度,y表示基材厚度,β0,β1,β2,β3,β4,β5为回归方程的系数。
37.进一步地,所述根据各几何模型对应的铜箔厚度、基材厚度及其仿真得到的铜箔层所受到的最大应力值,通过预设的多项式回归方程,拟合得到铜箔层最大应力值的回归模型之后,进一步包括:
38.对所述回归模型进行方差分析。
39.由上述描述可知,通过对回归模型进行方差分析,以评估回归模型的准确度。
40.进一步地,所述铜箔厚度集合中包含6个铜箔厚度,分别为6μm、9μm、12μm、15μm、25μm和38μm。
41.进一步地,所述基材厚度集合中包含4个基材厚度,分别为25μm、50μm、75μm和100μm。
42.进一步地,所述预设的覆盖膜厚度为27μm,所述预设的长度为6mm。
43.进一步地,所述几何模型的个数为第一个数和第二个数的乘积。
44.由上述描述可知,保证几何模型覆盖了不同铜箔厚度和基材厚度的组合,可保证整体方法的有效性及准确性。
45.实施例一
46.请参照图1和图3,本发明的实施例一为:一种基于铜箔和基材厚度的fccl弯折疲劳应力的预测方法,可应用于fccl的测试场景中,针对fccl结构不同铜箔厚度和不同基材厚度的组合,通过仿真加数据拟合的方式来预测fccl叠构中不同层的应力,从而来定性分析fccl的折弯寿命和趋势。
47.如图1所示,所述fccl(挠性覆铜板)包括依次层叠的基材层1、铜箔层2和覆盖膜层3。如图3所示,本实施例的方法包括如下步骤:
48.s1:预设铜箔厚度集合和基材厚度集合,所述铜箔厚度集合中包含预设的第一个数的铜箔厚度,所述基材厚度集合包含预设的第二个数的基材厚度。
49.将fccl覆铜膜的铜箔厚度x、lcp基材厚度y作为影响fccl各层应力大小的两个因素。本实施例中,铜箔厚度分别选取6μm、9μm、12μm、15μm、25μm以及38μm作为常用fccl薄膜铜箔厚度,lcp基材分别选取25μm、50μm、75μm以及100μm。具体如表1所示。
50.表1:因素及其取值
[0051][0052][0053]
s2:根据所述铜箔厚度集合和基材厚度集合以及预设的覆盖膜厚度和预设的长度,构建分别与各铜箔厚度和各基材厚度一一对应的几何模型。
[0054]
为保证实验的有效性以及准确性,选取实验次数较多的正交表进行实验设计,即构建的几何模型的个数为第一个数和第二个数的乘积。本实施例中,即构建24个几何模型。
[0055]
优选地,本实施例中,所述覆盖膜厚度为27μm;基材层、铜箔层和覆盖膜层的长度均为6mm。即每个几何模型中的覆盖膜层的厚度均为27μm,每个几何模型的长度均为6mm。
[0056]
s3:分别将各几何模型导入仿真软件,仿真得到所述几何模型弯折预设角度时,基材层、铜箔层和覆盖膜层所受到的最大应力值。
[0057]
具体地,将几何模型导入有限元软件(如workbench)中,根据实际的弯折角度情况进行仿真,当弯折135
°
(弯折零度角与图1中的覆盖膜的上表面齐平,弯折正方向为图1中的顺时针方向,即以覆盖膜的上表面为弯折内表面)时,几何模型各层所受到的最大应力值,正交表以及仿真结果如下表2所示。其中,最大应力值是判断各层受到破坏的最大程度,也是评价各层收到破坏大小的依据,在材料力学中是最常用的参考值。
[0058]
表2:正交表及仿真数据
[0059]
[0060][0061]
s4:根据各几何模型对应的铜箔厚度、基材厚度及其仿真得到的基材层、铜箔层和覆盖膜层所受到的最大应力值,通过预设的多项式回归方程,拟合得到基材层最大应力值的回归模型、铜箔层最大应力值的回归模型和覆盖膜层最大应力值的回归模型。
[0062]
具体地,建立基于多项式法的应力值与铜箔厚度和基材厚度的回归模型,多项式回归模型采用二次回归方程,通过最小二乘法求取回归方程系数,进而构造出响应量和自变量之间的函数。
[0063]
fccl各层最大应力值与fccl铜箔厚度及基材厚度的关系复杂,因此,采用二元二次多项式回归方程来表达fccl各层最大应力值与fccl铜箔厚度及基材厚度之间的关系,具体表达式如第一公式所示。
[0064]
第一公式:p=β0+β1x+β2y+β3x2+β4xy+β5y2[0065]
其中,p表示最大应力值,x表示铜箔厚度,y表示基材厚度,β0,β1,β2,β3,β4,β5为回归方程的系数。
[0066]
然后分别将各层最大应力值以及铜箔厚度和基材厚度代入上述第一公式进行拟合,得到各层最大应力值的回归模型。
[0067]
具体地,根据各几何模型对应的铜箔厚度、基材厚度及其仿真得到的基材层所受到的最大应力值,通过上述回归方程,拟合得到基材层最大应力值的回归模型;根据各几何模型对应的铜箔厚度、基材厚度及其仿真得到的铜箔层所受到的最大应力值,通过上述回
归方程,拟合得到铜箔层最大应力值的回归模型;根据各几何模型对应的铜箔厚度、基材厚度及其仿真得到的覆盖膜层所受到的最大应力值,通过上述回归方程,拟合得到覆盖膜层最大应力值的回归模型。
[0068]
本实施例采用minitab19软件对实验所得到的数据进行拟合,得到的fccl各层最大应力值的二阶回归模型如下所示:
[0069]
p
cu
=3086+365.1x
‑
126.2y
‑
40.56x2‑
238.7xy
‑
50.38y2[0070]
p
lcp
=378
‑
9.235x+2.351y+0.1298x2+0.02023xy
‑
0.01992y2[0071]
p
cvl
=213.8
‑
2.025x
‑
1.767y+0.01655x2+0.01822xy+0.007647y2[0072]
其中,p
cu
表示铜箔层的最大应力值,p
lcp
表示基材层的最大应力值,p
cvl
表示覆盖膜层的最大应力值,x表示铜箔厚度,y表示基材厚度。
[0073]
s5:根据所述基材层最大应力值的回归模型、铜箔层最大应力值的回归模型和覆盖膜层最大应力值的回归模型以及待测fccl中的基材层和铜箔层的厚度,对弯折预设角度的所述待测fccl中的基材层、铜箔层和覆盖膜层所受到的应力值进行预测。
[0074]
即当存在相同折弯条件且已知fccl各层厚度时,可以根据步骤s4中拟合得到的回归模型来对各层所受应力值进行预测,从而缩短研发测试周期,大大缩短研发周期,降低研发成本。
[0075]
进一步地,在步骤s4中,采用软件进行拟合时,还会得到方差大小(方差大小为软件拟合公式的曲线跟实际曲线之间的偏差)。因此,在步骤s4之后,对拟合得到的回归模型进行方差分析,如表3所示。
[0076]
表3:最大应力值函数方差分析
[0077]
sser
‑
sqr
‑
sq(adj)f比3.591e+499.23%98.74%f
0.05
=4.41
[0078]
其中,r
‑
sq为99.23%,取值越大说明回归模型与数据拟合的越好,r
‑
sq(adj)取值98.74%,越接近r
‑
sq说明回归模型越可靠。同时,回归模型中各因素项的f比值均大于f
0.05
,说明这些项对最大应力值的影响是显著的。故而分析结果表明最大应力值回归模型的拟合程度良好,能有效预测该实验条件下的最大应力值大小。
[0079]
本实施例提出了一种适用于不同铜箔厚度、不同基材厚度组合的fccl叠构应力值预估方法,利用有限元仿真来获取不同层厚度组合下fccl弯折时所受的应力值,极大地缩短了通过试验设备获取数值的周期,极大地提高了效率和降低了成本;不仅可以预测铜箔折弯寿命,还可以预测基材及覆盖膜折弯寿命;本实施例的方法操作简易,可操作性强。
[0080]
综上所述,本发明提供的一种基于铜箔和基材厚度的fccl弯折疲劳应力的预测方法,利用有限元仿真来获取不同层厚度组合下fccl弯折时所受的应力值,极大地缩短了通过试验设备获取数值的周期,极大地提高了效率和降低了成本;不仅可以预测铜箔折弯寿命,还可以预测基材及覆盖膜折弯寿命。本发明的方法操作简单,可操作性强,适用于不同铜箔厚度、不同基材厚度组合的fccl叠构应力值预估。
[0081]
以上所述仅为本发明的实施例,并非因此限制本发明的专利范围,凡是利用本发明说明书及附图内容所作的等同变换,或直接或间接运用在相关的技术领域,均同理包括在本发明的专利保护范围内。