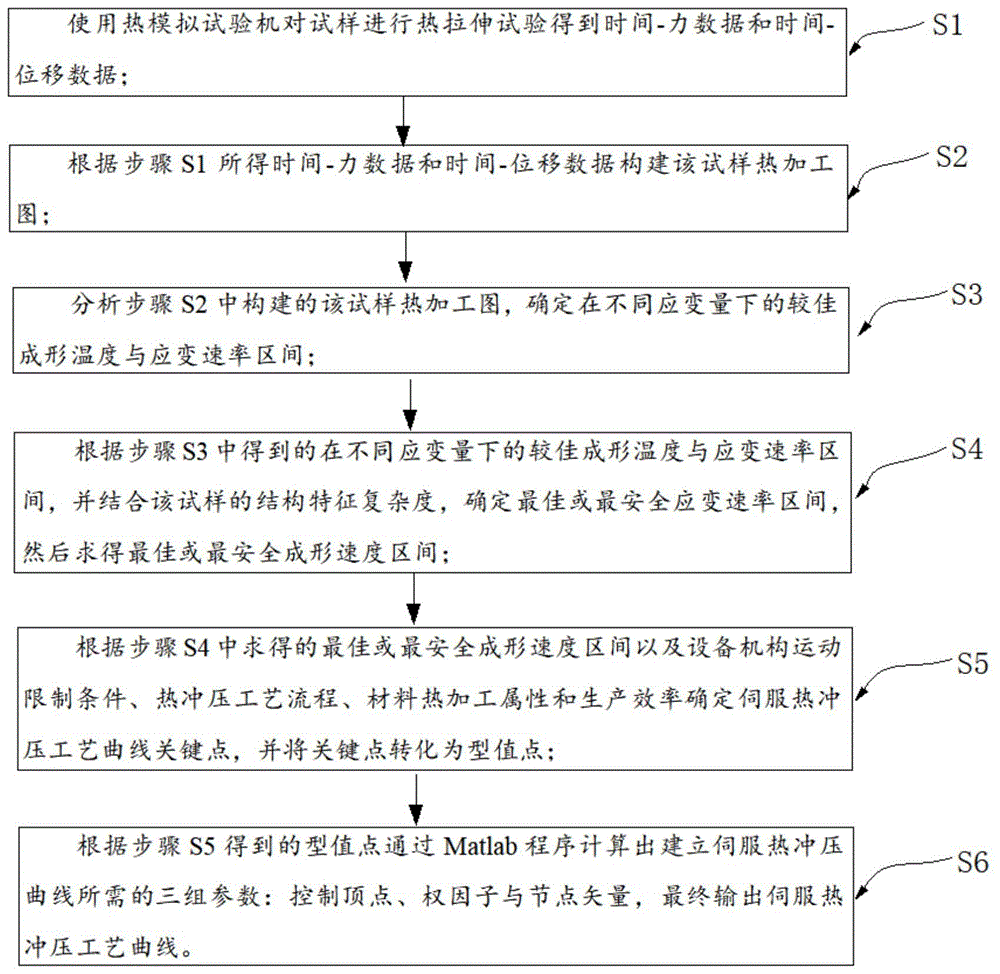
本发明涉及伺服热冲压技术领域,尤其涉及一种伺服热冲压工艺设计方法。
背景技术:
板料冷冲压变形抗力大、塑形差,易发生破裂、起皱和回弹。在高温下,板料塑形与延展性会大大提高,可获得形状复杂的成型性优良的零件,热冲压成形技术应运而生。伺服压力机可实现滑块的柔性控制,速度连续可调,从而改善零件成形性与精度,提高生产率,诸如此类优点使得伺服热冲压技术快速发展起来。伺服特性在热冲压过程中体现在成形速度对塑形变形和组织演变的影响,具体来说,冲压速度直接决定板料变形速率,而形变会对组织演变产生重要影响,从而影响零件成形性与组织力学性能。此外,变形时间对高温板料散热及其与模具之间的摩擦也有着不可忽略的影响,从而进一步影响成形组织与性能。
伺服热冲压工艺是一项新型的成形技术,目前在伺服曲线设计时大多基于高次多项式函数,通过对其进行求导获得速度、加速度曲线,无法保证工艺曲线的高阶连续性,并且修正困难,不具有局部可调性,无法使板料达到最佳成形性能,也影响设备使用寿命。对于热冲压工艺中最关键的合模阶段,伺服成形位移(或速度)的确定大多根据经验,未能考虑材料特性对成形速度的影响。基于此,本专利提出一种考虑材料加工特性与设备机构运动特性,工艺曲线高阶连续、局部可调的伺服热冲压工艺设计方法。
技术实现要素:
有鉴于此,有必要提供一种伺服热冲压工艺设计方法,用以解决目前在伺服工艺曲线设计大多根据经验,无法使板料达到最佳成形性能,也影响设备使用寿命,伺服成形位移(或速度)的确定的问题。
本发明提供一种伺服热冲压工艺设计方法,包括:
s1:使用热模拟试验机对试样进行热拉伸试验得到时间-力数据和时间-位移数据;
s2:根据步骤s1所得时间-力数据和时间-位移数据构建该试样热加工图;
s3:分析步骤s2中构建的该试样热加工图,确定在不同应变量下的较佳成形温度与应变速率区间;
s4:根据步骤s3中得到的在不同应变量下的较佳成形温度与应变速率区间,并结合该试样的结构特征复杂度,确定最佳或最安全应变速率区间,然后求得最佳或最安全成形速度区间;
s5:根据步骤s4中求得的最佳或最安全成形速度区间以及设备机构运动限制条件、热冲压工艺流程、材料热加工属性和生产效率确定伺服热冲压工艺曲线关键点,并将关键点转化为型值点;
s6:根据步骤s5得到的型值点通过matlab程序计算出建立伺服热冲压曲线所需的三组参数:控制顶点、权因子与节点矢量,最终输出伺服热冲压工艺曲线。
进一步的,所述步骤s1包括:
s11:将板料切割为满足热模拟试验机标准尺寸要求的拉伸试样,对该试样进行高温标距测量试验;
s12:对该试样进行热拉伸试验,获得高温拉伸时间-力数据和时间-位移数据;
s13:对得到的数据进行处理,得到该试样在不同变形温度、应变速率下的真应力-应变曲线;
s14:在真应力-应变曲线的塑性变形阶段选取相同间隔的应变量数据,获得不同应变量下的变形温度、应变速率对应的真应力数值。
进一步的,所述对该试样进行高温标距测量试验时,以距试样中心线温降小于等于40℃为标准确定标距。
进一步的,所述步骤s4中确定最佳或最安全应变速率区间的步骤包括:
根据拉伸量确定对应应变量下的热加工图,在安全区内选择功率耗散效率最高的区域作为最佳应变速率区间;
确定最安全应变速率区间的步骤包括:取该材料在不同应变量下的较佳应变速率区间的交集,作为最安全应变速率区间。
进一步的,步骤s2中所述热加工图是基于动态材料模型,所建立热加工图是功率耗散图与塑性失稳图的叠加,采用的基于动态材料模型的功率耗散判断准则为:
其中,η为功率耗散系数,j为材料塑性变形过程中组织结构演化耗散的能量,jmax为线性耗散能量,p为输入能量,g为耗散量,m为应变速率敏感指数,σ为真应力,为应变速率;采用的基于动态材料模型的塑性失稳判断准则为2mπη≤0。
本发明还提供了一种伺服热冲压工艺设计系统,包括处理器和存储器,所述存储器上存储有计算机程序,所述计算机程序被所述处理器执行时,实现所述的伺服热冲压工艺设计方法。
本发明还提供了一种计算机可读存储介质,其上存储有计算机程序,所述计算机程序被处理器执行时,实现所述的伺服热冲压工艺设计方法。
本发明提供的一种伺服热冲压工艺设计方法,具有以下有益效果:
(1)运用热加工图可以合理选择合模阶段变形工艺参数以改善材料热加工性能,控制变形过程中形成的组织结构形态,避免组织缺陷的产生,工艺曲线设计考虑材料特性可提升零件成形质量;
(2)所述伺服热冲压工艺设计方法基于nurbs数学模型,其数学特性决定伺服热冲压工艺曲线高阶连续,可提升设备寿命,并具有局部柔性可调性,可满足不同材料热冲压工艺需求;
(3)考虑材料特性确定的最佳或最安全成形速度应用到伺服热冲压工艺中,结合设备机构运动特性,使用较大空载下行、上行速度,保证零件成形质量与无组织缺陷的同时提高生产效率。
附图说明
图1为本发明提供的一种伺服热冲压工艺设计方法的流程示意图;
图2为实施例一中高温标距测量热电偶焊接示意图;
图3为实施例一中热拉伸工艺流程图;
图4为实施例一中热拉伸真应力-应变曲线;
图5为实施例一中材料热加工图建立流程图;
图6为实施例一中b1500hs钢不同应变量下热加工图;
图7为实施例一中基于nurbs模型的伺服热冲压工艺曲线图。
具体实施方式
下面结合附图来具体描述本发明的优选实施例,其中,附图构成本申请一部分,并与本发明的实施例一起用于阐释本发明的原理,并非用于限定本发明的范围。
实施例一
本发明提供了一种伺服热冲压工艺设计方法,如图1所示为所述伺服热冲压工艺设计方法的流程示意图,所述伺服热冲压工艺设计方法包括:
s1:使用热模拟试验机对试样进行热拉伸试验得到时间-力数据和时间-位移数据;
s2:根据步骤s1所得时间-力数据和时间-位移数据构建该试样热加工图;
s3:分析步骤s2中构建的该试样热加工图,确定在不同应变量下的较佳成形温度与应变速率区间;
s4:根据步骤s3中得到的在不同应变量下的较佳成形温度与应变速率区间,并结合该试样的结构特征复杂度,确定最佳或最安全应变速率区间,然后求得最佳或最安全成形速度区间;
s5:根据步骤s4中求得的最佳或最安全成形速度区间以及设备机构运动限制条件、热冲压工艺流程、材料热加工属性和生产效率确定伺服热冲压工艺曲线关键点,并将关键点转化为型值点;
s6:根据步骤s5得到的型值点通过matlab程序计算出建立伺服热冲压曲线所需的三组参数:控制顶点、权因子与节点矢量,最终输出伺服热冲压工艺曲线。
具体地,在本实施例一中,选择的试样材料为b1500hs钢,是一种低碳铁素体加珠光体的冷轧硼钢,含有多种金属元素与非金属元素,属于复杂合金钢。步骤s1中所述热拉伸试验包括以下具体步骤:
s11:将板料切割为满足热模拟试验机标准尺寸要求的拉伸试样,对该试样进行高温标距测量试验
采用激光切割方式将厚度为1.6mm的b1500hs钢板切割为满足热模拟试验机标准尺寸要求的拉伸试样,由于试样热拉伸存在沿试样长度方向的温度梯度,为保证试验结果准确性,在本实施例一中,所述对该试样进行高温标距测量试验时,以距试样中心线温降小于等于40℃为标准确定标距。每个试验在试样上点焊两对热电偶采集温度,其中的一对热电偶位于试样中线用于控制加热温度,另外一对位置分别为距中线3mm、4.5mm、6mm和7.5mm处,如图2所示,加热温度分别为950℃、850℃、750℃和650℃,对数据进行处理后确定高温标距为12mm。
s12:对该试样进行热拉伸试验,获得高温拉伸时间-力数据和时间-位移数据
设计符合热冲压过程的工艺流程,选取变形温度与应变速率为变量,变量取值范围应根据具体材料及工艺相应确定。确定b1500hs钢的成形范围为650℃-950℃,每隔100℃选取一个水平,共四个水平;确定应变速率范围为0.01/s-10/s,因此试验设计的应变速率为0.01/s、0.1/s、1/s、10/s共四个水平;试验采用单因素试验设计方法,在热模拟试验机上共进行16组试验,试验过程中首先以50℃/s将试样加热到该材料热冲压所需奥氏体化温度950℃,保温5min保证奥氏体均匀化,再以20℃/s降温至变形温度并保持5s进行等温热拉伸,直至试样断裂后采用水淬,以保留变形组织,便于对试样进行微观组织观察,热拉伸工艺流程图如图3所示。
s13:对热拉伸试验得到的数据进行处理,得到该试样在不同变形温度、应变速率下的真应力-应变曲线
对热拉伸试验所得数据,即时间-位移、时间-力数据进行截取、转化与光顺最终可得16条真应力-应变曲线,如图4所示。
s14:在真应力-应变曲线的塑性变形阶段选取相同间隔的应变量数据,获得不同应变量下的变形温度、应变速率对应的真应力数值
在真应力-应变曲线塑性变形节段选取相同间隔应变量数值,获得不同应变量下的变形温度、应变速率对应的真应力数值,获得不同应变量下的变形温度、应变速率对应的真应力数值,选取应变量为0.1、0.15与0.2。
如图5所示为步骤s2中构建该试样热加工图具体流程,包括:
s21:在matlab程序中输入某应变量ε下的应力值σ和应变速率
s22:计算应力σ的对数lgσ和应变速率的对数并在一定应变量下对作图;
s23:用三次样条函数拟合lgσ与得到
以求
s24:将函数对求导得
s25:判断试样材料的本构关系是否满足
s26:如满足,计算功率耗散系数和塑性失稳函数如不满足,计算功率耗散系数
和塑性失稳函数ζ:2m-ηπ0.or.ηπ0;
所述热加工图的绘制过程完全通过matlab程序实现。所述热加工图是基于动态材料模型,所建立热加工图是功率耗散图与塑性失稳图的叠加,采用的基于动态材料模型的功率耗散判断准则为:
其中,η为功率耗散系数,j为材料塑性变形过程中组织结构演化耗散的能量,jmax为线性耗散能量,p为输入能量,g为耗散量,m为应变速率敏感指数,σ为真应力,为应变速率;采用的基于动态材料模型的塑性失稳判断准则为2mπη≤0。
s27:将m值代入功率耗散判断准则与塑性失稳准则,在变形温度t和应变速率对数组成的坐标系内绘制功率耗散图和塑性失稳图;
s28:将绘制的功率耗散图和塑性失稳图叠加,得到热加工图。
利用热拉伸试验所得真应力-应变数据,在一定应变量下对作图,对不同温度下曲线进行三次多项式拟合,可得:
对求一次偏导可得:
因考虑板料热冲压过程板料的受力状态与高温拉伸过程中板料受力状态相近,所述热加工图是基于热拉伸试验确定,而不是热压缩试验,属首创。
通过matlab程序可以快速准确的计算出应变速率敏感指数、功率耗散系数和塑性失稳参数,自动绘制出功率耗散图和塑性失稳图并将两图叠加,输出最终热加工图,可避免计算误差,大大提高计算效率。最终得到b1500hs钢在应变量分别为0.1、0.2、0.15与下的热加工图,如图6所示。
步骤s3所述的分析步骤s2中构建的该试样热加工图时,功率耗散系数越高表明材料组织演变所消耗的能量越高,材料的加工性越好,同时还要避免材料出现失稳性,塑性失稳区如图6中阴影部分所示。在选择材料的热加工工艺参数时要再材料的加工安全区内尽量选择功率耗散系数高的区域。由此可确定材料不同应变量下的较佳成形温度与应变速率区间;根据图6,红色方框内的区域(d1-d5)满足上述要求,即为要寻找的材料在不同应变量下的较佳成形温度与应变速率区间,具体请参照表1:
表1
步骤s4中确定最佳或最安全应变速率区间的步骤包括:
确定最佳应变速率区间的步骤包括:根据拉伸量确定对应应变量下的热加工图,在安全区内选择功率耗散效率最高的区域作为最佳应变速率区间;因考虑结构复杂易破裂的零件实际成形各部位均处于塑性阶段但应变量不同,确定最安全应变速率区间的步骤包括:取该材料在不同应变量下的较佳应变速率区间的交集,作为最安全应变速率区间。
然后根据应变速率与成形速度v之间的关系,求得最佳或最安全成形速度区间;根据步骤s3中确定的不同应变量下的较佳应变速率区间,对于拉伸量较小的零件,选择最佳应变速率区间,对于结构复杂易破裂的零件,选择最安全应变速率区间。所述最佳或最安全应变速率区间的最终确定还需要考虑所用材料在实际冲压过程的速度限制范围,若超出限制范围,最佳或最安全成形速度取速度范围上限值。
在本实施例一中,分析的对象为汽车中立柱,属于结构复杂易破裂的零件,以此为例具体说明。应当理解,对于拉伸量较小的零件最佳应变速率区间选择与此类似。因此取上述较佳应变速率区间的交集,即最安全应变速率区间为0.32-5.6s-1。
所述最佳或最安全成形速度区间确定后取其区间最大值,以提高生产效率。所述最佳或最安全成形速度作为模具接触板料瞬间速度,即合模开始速度,在nurbs模型中增加此关键点速度限制条件实现。
应变速率与成形速度v之间的关系为:其中l为标距,单位mm;单位s-1,v单位mm/s。故本实施例一中最安全成形速度区间为3.84-67.2mm/s。查阅该材料在热冲压过程的速度限制范围为小于等于400mm/s,未超出限制范围。最安全成形速度取68mm/s,作为模具接触板料瞬间速度,即合模开始速度,在nurbs模型增加此关键点速度插值条件实现。
步骤s5中,所述设备限制条件主要包括滑块行程(具体设备决定,600mm)、冲压工作行程(根据具体零件结构决定,80mm)、最大下行速度(具体设备决定,800mm/s)、最大拉伸速度(材料决定,400mm/s)、最大回程速度(具体设备决定,800mm/s)、最大加速度(具体设备决定,2000mm/s2);根据热冲压工艺流程将所述伺服热冲压过程分为空程高速下行区、冲压成形区、下死点保压淬火区、低速脱模区和高速回程区,所述最佳或最安全成形速度使用在冲压成形区,即合模区;所述高速下行区、高速回程区速度应在设备限制范围内取较大值,以提高生产率;材料热加工属性由热加工图确定。
确定伺服热冲压工艺曲线关键点时,关键点规划数学模型采用如下形式:
伺服热冲压工艺曲线边界条件的约束,一般取首末端点切矢条件,具体来说,必须保证首末端点速度、加速度保持为0。为保证加速度曲线连续,曲线次数不低于3。
由此可确定伺服热冲压工艺曲线关键点坐标如下:(0,600),(0.4,440),(0.7,200),(0.9,80),(1.15,60),(1.35,0),(7.35,0),(7.75,160),(8.1,440),(8.5,600)。
将关键点转化为型值点时,以关键点横坐标t除以总的冲压时间,纵坐标x除以总的冲压位移,分别得到名义时间t=t/t总,名义位移x=x/x总,由此得到一组型值点
对应型值点坐标如下(0,1),(0.047,0.733),(0.082,0.333),(0.106,0.133),(0.135,0.1),(0.159,0),(0.865,0),(0.912,0.267),(0.953,0.733),(1,1)。
在本实施例一中,所述伺服热冲压工艺曲线基于nurbs数学模型设计,在设计伺服热冲压工艺曲线之前需进行等效与转化处理。所述nurbs数学模型有理基函数表示形式为:
其中,为控制顶点,其组成控制多边形,{ωi}为权因子(ωiφ0),{ri,k(u)}为有理基函数,是u∈[0,1]上的分段有理函数,{ni,k(u)}为定义在非均匀节点矢量u=(u0,…,um)=(0,…,0,uk+1,…,um-k-1,1,…,1),m=n+k+1上的第i个k次b样条基函数。
所述b样条基函数的递推定义表达式为:
由于伺服热冲压曲线的建立需要考虑四个因素,即控制顶点的确定、权因子的确定、节点矢量的确定及曲线次数的确定,因此需要通过步骤s6计算出建立伺服热冲压曲线所需的三组参数:控制顶点、权因子与节点矢量,最终输出伺服热冲压工艺曲线。计算控制顶点、权因子与节点矢量具体过程如下:
对型值点进行规范积累弦长参数化,求取节点矢量,规范积累弦长参数参数化过程具体表示为:
其中,l为总弦长,为节点矢量中间元素;
采用平均技术(avg技术)对平均化得到最终节点矢量u,即:
所述nurbs曲线控制顶点与权因子的确定是在四维空间的非有理b样条曲线作投影变换得到。有理插值可以看作插值带权型值点的问题,解出插值带权型值点的非有理b样条曲线的控制顶点同样是带权的,然后取其在ω=1超平面上的投影即为所求nurbs曲线的控制顶点带权控制顶点的最后一个分量即为与所求控制点相联系的权因子ωi,节点矢量确定过程中也采用带权型值点。
非有理b样条曲线的表示形式为:
其中,各参量含义与表示形式均与nurbs曲线的有理基函数表示形式一致。
最终输出伺服热冲压工艺曲线,由n-1个型值点反求出nurbs插值曲线的n+1个控制顶点与权因子,并根据已确定的次数k,节点矢量u=(u0,…,um)=(0,0,0,0,uk+1,…,um-k-1,1,1,1,1),最终可确定一条经过所有型值点的高次nurbs插值曲线。
由matlab程序计算出的控制顶点为(0,1),(0.066,0.624),(0.103,0.426),(0.059,0.165),(0.156,0.091),(0.13,0.031),(0.267,0.008),(0.358,0.002),(0.461,0),(0.56,0),(0.661,0),(0.758,0.004),(0.942,0.028),(0.89,0.398),(0.928,0.585),(1,1),权因子均取为1,节点矢量为(0,0,0,0,0.099,0.245,0.319,0.335,0.372,0.409,0.446,0.482,0.519,0.556,0.592,0.630,0.73,0.9,1,1,1,1)。曲线次数取3,仅输入型值点坐标,即可输出最终伺服热冲压工艺曲线,可大大提高计算速率,避免计算误差,最终设计出来的伺服热冲压工艺曲线如图7所示。
本发明提供的所述伺服热冲压工艺设计方法,通过考虑具体材料热加工属性与设备机构运动特性基础上设计热冲压伺服工艺曲线,保证工艺曲线的高阶连续性与局部可调性,减少零件微观组织缺陷,提升复杂及难成形零件的成形质量,提高生产效率。所述基于nurbs数学模型确定的伺服热冲压工艺曲线完全通过matlab程序实现,相较于传统方法,设计效率大大提高。后期可通过调节控制顶点与权因子来达到控制曲线形状的目的,达到自由调节伺服热冲压工艺曲线的目的。
本发明实施例一还提供了一种伺服热冲压工艺设计系统,包括处理器和存储器,所述存储器上存储有计算机程序,所述计算机程序被所述处理器执行时,实现所述的伺服热冲压工艺设计方法。
本发明实施例一还提供了一种计算机可读存储介质,其上存储有计算机程序,所述计算机程序被处理器执行时,实现所述的伺服热冲压工艺设计方法。
以上所述,仅为本发明较佳的具体实施方式,但本发明的保护范围并不局限于此,任何熟悉本技术领域的技术人员在本发明揭露的技术范围内,可轻易想到的变化或替换,都应涵盖在本发明的保护范围之内。