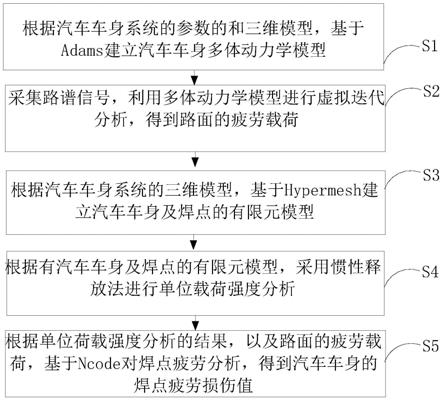
1.本发明涉及汽车检测技术领域,特别是涉及一种车身焊点疲劳度评估方法、存储介质及设备。
背景技术:2.随着汽车工业的飞速发展和人们生活水平的提升,汽车已经成为人们出行、货运等不可或缺的交通工具之一。
3.在汽车的零部件中,点焊被广泛应用于零部件和结构中,焊点的疲劳性能直接影响车辆的安全性和可靠性,因此需要对焊点的疲劳寿命进行仿真分析计算。目前,焊点的疲劳计算方法多采用单一的有限元模型进行模拟计算,根据对应部件的参数以及模拟路面,实现焊点的疲劳寿命的计算。
4.现有的焊点疲劳寿命计算方法只采用单一的有限元模型,其存在模型过于简化、载荷难以获取、计算精度较低等问题,不能够科学有效地指导车身的设计开发。
技术实现要素:5.本发明的一个目的在于提出一种模拟精度高的车身焊点疲劳度评估方法。
6.一种车身焊点疲劳度评估方法,应用于汽车车身系统,包括以下步骤:
7.根据汽车车身系统的参数的和三维模型,基于adams建立汽车车身多体动力学模型;
8.采集路谱信号,利用多体动力学模型进行虚拟迭代分析,得到路面的疲劳载荷;
9.根据汽车车身系统的三维模型,基于hypermesh建立汽车车身及焊点的有限元模型;
10.根据汽车车身及焊点的有限元模型,采用惯性释放法进行单位载荷强度分析;
11.根据单位荷载强度分析的结果,以及路面的疲劳载荷,基于ncode对焊点疲劳分析,得到汽车车身的焊点疲劳损伤值,所述焊点疲劳损伤值的计算采用下列公式:
[0012][0013]
其中,d
i
为每级载荷下的损伤,n
i
为每级载荷的循环次数,n
i,f
为每级载荷对应的疲劳极限次数,∑n为总寿命。
[0014]
本发明提供的车身焊点疲劳度评估方法,通过基于汽车整车参数及其三维模型,采用adams软件建立整车多体动力学模型。然后采集路谱信号数据,基于整车多体动力学模型进行虚拟迭代计算与分解,获取车身连接点在各个路面的疲劳载荷数据。再采用hypermesh建立车身有限元模型,基于惯性释放法对车身进行单位载荷受力静强度分析,获取车身焊点应力信息,最后基于强度分析结果与各个路面的疲劳载荷,采用ncode对车身焊点进行疲劳寿命分析。本发明的有益效果是:综合采用adams建立多体动力学模型、hypermesh建立有限元模型和ncode对焊点疲劳分析,得到汽车车身的焊点疲劳损伤值,同
cycle,添加多个time series load provider并设置循环次数;
[0037]
选取time series load provider,并在load case中导入单位载荷的各个分析工况,在time series中导入各个路面的疲劳载荷;
[0038]
在sheet1 material中加载spot;generic sheet,在sheet2 material中也加载spot;generic sheet,在nugget material中加载spot,generic nugget,得到焊点曲线。
[0039]
本发明的附加方面和优点将在下面的描述中部分给出,部分将从下面的描述中变得明显,或通过本发明的实践了解到。
附图说明
[0040]
本发明的上述和/或附加的方面和优点从结合下面附图对实施例的描述中将变得明显和容易理解,其中:
[0041]
图1是本发明第一实施例的车身焊点疲劳度评估方法的流程图;
[0042]
图2是本发明第一实施例的汽车车身多体动力学模型的示意图;
[0043]
图3是本发明第一实施例的车身焊点疲劳度评估设备的示意图。
具体实施方式
[0044]
为使本发明的目的、特征和优点能够更加明显易懂,下面结合附图对本发明的具体实施方式做详细的说明。附图中给出了本发明的若干实施例。但是,本发明可以以许多不同的形式来实现,并不限于本文所描述的实施例。相反地,提供这些实施例的目的是使对本发明的公开内容更加透彻全面。
[0045]
请参阅图1,本发明的第一实施例提出一种车身焊点疲劳度评估方法,应用于汽车车身系统,包括以下步骤:
[0046]
s1、根据汽车车身系统的参数的和三维模型,基于adams建立汽车车身多体动力学模型。
[0047]
具体的,所述汽车车身系统的参数包括硬点坐标、衬套刚度曲线、弹簧刚度、减震器速度阻尼力曲线、各个零部件质量、前后悬架轴荷、轮胎三向刚度、整车重量、重心高度、轴距、轮距。
[0048]
更进一步地,所述基于adams建立汽车车身多体动力学模型的步骤包括:
[0049]
采用adams软件创建汽车车身系统的硬点坐标,创建汽车车身系统的各零部件的几何信息;
[0050]
根据各零部件的几何信息,创建各零部件之间的连接关系;
[0051]
将汽车车身系统的三维模型的中性文件导入adams软件中,更新三维模型的对应属性文件以及汽车车身系统的参数,得汽车车身多体力学模型。
[0052]
需要说明的是,采用多种参数基于adams建立汽车车身多体动力学模型能增加模型的真实性,提高模拟的精度。
[0053]
s2.采集路谱信号,利用多体动力学模型进行虚拟迭代分析,得到路面的疲劳载荷。
[0054]
具体的,所述采集路谱信号,利用多体动力学模型进行虚拟迭代分析的步骤包括:
[0055]
获取路面的白噪声信号并基于多体动力学模型得到白噪声响应,并根据白噪声信
号和白噪声响应生成传递函数及逆传递函数;
[0056]
向汽车车身多体动力学模型输入路面的目标信号,通过传递函数得到输入激励;
[0057]
将输入激励与目标信号进行比对,并修正输入激励,使得输入激励与目标信号的比值在预设区间,完成虚拟迭代;
[0058]
提取汽车车身系统的各个外连接点与路面的时域虚拟路谱载荷,即路面的疲劳载荷。
[0059]
需要说明的是,在模拟迭代分析中,通过传递函数计算得到轴头加速度与轮胎接地点的关系、减震器位移与轮胎接地点的关系,与此同时采集轮心六分力载荷、轴头加速度、减震器位移,对采集的道路谱数据进行检查、去毛刺、去漂移、滤波、转换、排序、压频等处理,将其输入至悬架多体动力学模型中,以此进行虚拟迭代计算,当目标信号与仿真信号的相对损伤值在0.5~2之间时,迭代工作结束。
[0060]
s3.根据汽车车身系统的三维模型,基于hypermesh建立汽车车身及焊点的有限元模型。
[0061]
具体的,所述根据汽车车身系统的三维模型,基于hypermesh建立汽车车身及焊点有限元模型的步骤包括:
[0062]
将车身的三维模型导入至前处理软件hypermesh中,采用midsurface功能项抽取各个车身零部件的中性面,对其表面进行几何特征清理和简化处理,采用尺寸为8mm的四边形单元对其进行网格划分,特殊的复杂结构区域采用部分三角形单元进行过渡。acm由弹性单元和连接模型两部分组成,由一个六面体单元和rbe3单元组成,能够准确模拟焊点的各项性能,因此基于nastran软中的spot功能项中类型为5mm的acm(shell gap)进行焊点模拟连接,建立相应的材料属性,以此建立车身及其焊点有限元模型。
[0063]
s4.根据汽车车身及焊点的有限元模型,采用惯性释放法进行单位载荷强度分析。
[0064]
具体的,所述采用惯性释放法进行单位载荷强度分析的方法包括::
[0065]
在汽车车身系统上增设虚拟反作用力,直到汽车车身达到静平衡,基于汽车车身及其焊点有限元模型分别在各个外连接点分别加载x、y、z方向的单位力和单位扭矩,获取在单位载荷激励下车身焊点的应力与应变状态,即单位载荷强度分析结果。
[0066]
可以理解的,由于汽车在路面行驶,存在刚体运动,属于静力不平衡状态,通常静力分析时,必须设置约束条件,否则会产生刚体位移,求解器不能计算,可采用惯性释放方法解决此类问题。
[0067]
s5.根据单位荷载强度分析的结果,以及路面的疲劳载荷,基于ncode对焊点疲劳分析,得到汽车车身的焊点疲劳损伤值。
[0068]
具体的,所述焊点疲劳损伤值的计算采用下列公式:
[0069][0070]
其中,d
i
为每级载荷下的损伤,n
i
为每级载荷的循环次数,n
i,f
为每级载荷对应的疲劳极限次数,∑n为总寿命。
[0071]
可以理解的,miner疲劳损伤累积理论是指结构或者材料在各个应力下的损伤是独立的,并且其总损伤是线性叠加的,当损伤叠加至某一边界值时将会产生破坏,本发明通
过上述计算公式对汽车车身的焊点疲劳度进行计算分析,相对全面的考虑到了焊点疲劳的因素,通过采用上述公式对焊点的疲劳进行计算分析,使得模拟计算值和实际的疲劳度更加贴近。
[0072]
本发明的优势在于,综合采用adams建立多体动力学模型、hypermesh建立有限元模型和ncode对焊点疲劳分析,得到汽车汽车车身的焊点疲劳损伤值,同时还配合虚拟迭代分析,大大提高了模拟精度,提升了模拟效果。
[0073]
本发明实施例还提出一种计算机可读存储介质,其上存储有计算机程序,该程序被处理器执行时实现如上述的车身焊点疲劳度评估方法。
[0074]
本领域技术人员可以理解,在流程图中表示或在此以其他方式描述的逻辑和/或步骤,例如,可以被认为是用于实现逻辑功能的可执行指令的定序列表,可以具体实现在任何计算机可读介质中,以供指令执行系统、装置或设备(如基于计算机的系统、包括处理器的系统或其他可以从指令执行系统、装置或设备取指令并执行指令的系统)使用,或结合这些指令执行系统、装置或设备而使用。就本说明书而言,“计算机可读介质”可以是任何可以包含、存储、通信、传播或传输程序以供指令执行系统、装置或设备或结合这些指令执行系统、装置或设备而使用的装置。
[0075]
计算机可读介质的更具体的示例(非穷尽性列表)包括以下:具有一个或多个布线的电连接部(电子装置),便携式计算机盘盒(磁装置),随机存取存储器(ram),只读存储器(rom),可擦除可编辑只读存储器(eprom或闪速存储器),光纤装置,以及便携式光盘只读存储器(cdrom)。另外,计算机可读介质甚至可以是可在其上打印所述程序的纸或其他合适的介质,因为可以例如通过对纸或其他介质进行光学扫描,接着进行编辑、解译或必要时以其他合适方式进行处理来以电子方式获得所述程序,然后将其存储在计算机存储器中。
[0076]
应当理解,本发明的各部分可以用硬件、软件、固件或它们的组合来实现。在上述实施方式中,多个步骤或方法可以用存储在存储器中且由合适的指令执行系统执行的软件或固件来实现。例如,如果用硬件来实现,和在另一实施方式中一样,可用本领域公知的下列技术中的任一项或它们的组合来实现:具有用于对数据信号实现逻辑功能的逻辑门电路的离散逻辑电路,具有合适的组合逻辑门电路的专用集成电路,可编程门阵列(pga),现场可编程门阵列(fpga)等。
[0077]
本发明另一方面还提出一种车身焊点疲劳度评估设备,请参阅图3,所示为本发明实施例三当中的车身焊点疲劳度评估设备,包括存储器20、处理器10以及存储在存储器上并可在处理器上运行的计算机程序30,所述处理器10执行所述程序30时实现如上述的车身焊点疲劳度评估方法。
[0078]
其中,所述车身焊点疲劳度评估设备具体可以为带有数据库的计算机设备,例如服务器等,处理器10在一些实施例中可以是中央处理器(central processing unit,cpu)、控制器、微控制器、微处理器或其他车身焊点疲劳度评估芯片,用于运行存储器20中存储的程序代码或处理数据,例如执行访问限制程序等。
[0079]
其中,存储器20至少包括一种类型的可读存储介质,所述可读存储介质包括闪存、硬盘、多媒体卡、卡型存储器(例如,sd或dx存储器等)、磁性存储器、磁盘、光盘等。存储器20在一些实施例中可以是车身焊点疲劳度评估设备的内部存储单元,例如该车身焊点疲劳度评估设备的硬盘。存储器20在另一些实施例中也可以是车身焊点疲劳度评估设备的外部存
储装置,例如车身焊点疲劳度评估设备上配备的插接式硬盘,智能存储卡(smart media card,smc),安全数字(secure digital,sd)卡,闪存卡(flash card)等。进一步地,存储器20还可以既包括车身焊点疲劳度评估设备的内部存储单元也包括外部存储装置。存储器20不仅可以用于存储安装于车身焊点疲劳度评估设备的应用软件及各类数据,还可以用于暂时地存储已经输出或者将要输出的数据。
[0080]
需要指出的是,图3示出的结构并不构成对车身焊点疲劳度评估设备的限定,在其它实施例当中,该车身焊点疲劳度评估设备可以包括比图示更少或者更多的部件,或者组合某些部件,或者不同的部件布置。
[0081]
在本说明书的描述中,参考术语“一个实施例”、“一些实施例”、“示例”、“具体示例”、或“一些示例”等的描述意指结合该实施例或示例描述的具体特征、结构、材料或者特点包含于本发明的至少一个实施例或示例中。在本说明书中,对上述术语的示意性表述不一定指的是相同的实施例或示例。而且,描述的具体特征、结构、材料或者特点可以在任何的一个或多个实施例或示例中以合适的方式结合。
[0082]
以上所述实施例仅表达了本发明的几种实施方式,其描述较为具体和详细,但并不能因此而理解为对本发明专利范围的限制。应当指出的是,对于本领域的普通技术人员来说,在不脱离本发明构思的前提下,还可以做出若干变形和改进,这些都属于本发明的保护范围。因此,本发明专利的保护范围应以所附权利要求为准。