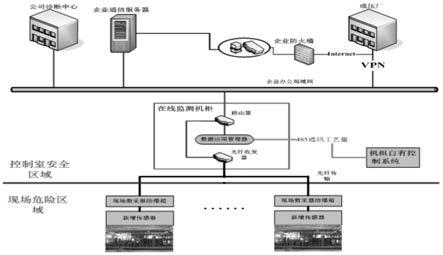
1.本发明属于故障诊断领域,涉及往复式天然气压缩机故障诊断系统以及诊断方法。
背景技术:2.从2007年ibm和google首次提出了云计算的概念开始,到如今随着信息化技术和工业化的深度融合,机械设备、信息化系统所产生的数据日益丰富。工业大数据具有体量大、类型多、价值密度低和处理速度快的特征,对数据进行实时有效的监测诊断,可以实现设备的预测性维护,发现生产、管理、调度流程中的决策问题。
3.同时,随着信号处理技术及人工智能技术的发展,越来越多的学者研究多传感器信息融合技术在故障诊断领域的应用。目前,已有学者将多传感器信息融合技术应用到电机,发动机及齿轮箱的故障诊断中并取得了一定的效果。但是,现有技术只针对监测设备的某些特定的故障进行检测判断,而无法对一个设备整体的、系统的状态进行比较和判断。
技术实现要素:4.本发明的目的在于:提供了往复式天然气压缩机故障诊断系统以及诊断方法,为往复式天然气压缩机设备提供监测、故障预警、维修决策及生产排程优化等业务功能,集设备运行状态感知、数据分析、数据决策等解决方案于一体的物联网应用平台,能够保障企业设备长周期、高效、节能、稳定的运行。解决了现有技术只针对监测设备的某些特定的故障进行检测判断,而无法对一个设备整体的、系统的状态进行比较和判断的问题。
5.本发明采用的技术方案如下:
6.往复式天然气压缩机故障诊断方法,包括上述故障诊断系统,包括以下步骤:
7.s1:将传感器等大数据采集工具安装在监测对象的各个关键部位,以采集监测对象不同工况运行状态下的特征参数;
8.s2:基于人工智能的计算网关实时处理、传输和存储上述特征参数,以及监测对象不同故障的波形和频谱分析经验,建立基于人工智能的智能预警模型和智能维修决策模型,根据实时采集的特征参数,植入到智能网关,实现监测对象故障的进场预警和处理;
9.s3:智能网关将关键数据实时上传至云平台,云平台通过对同一型号不同设备,以及不同型号不同设备的海量数据进行大数据分析和处理,利用时域频域等特征提取方法,建立仿真数学模型,并实时更新和优化仿真数学模型,并将优化后的模型下发到相应的智能网关,完成云端一体的智能阈值报警模型的优化和更新。
10.进一步地,步骤s3中所述的仿真数学模型的建立、优化方法步骤为:
11.s4:基于监测对象各个零部件的特性参数、监测对象的工艺信息数据、监测对象的实时运行状态数据,经滤波去除噪声后,建立监测对象的理想热力学方程、理想动力学方程和理想振动力学方程,得到监测对象的理想数学模型;
12.s5:监测对象运行阶段,向理想数学模型中输入由边缘层采集的数据,结合bp神经
网络方法和结构动力学修改,建立监测对象的仿真热力学模型、仿真动力学模型及仿真振动力学模型,得到监测对象的仿真数学模型,并将建立的仿真数学模型保存至故障诊断云平台;
13.s6:通过神经网络算法迭代改变仿真数学模型中有关故障部位参数,模拟监测对象不同部位的各种故障,获得故障数据特征,并将此故障数据特征保存至故障诊断云平台;
14.s7:当监测对象出现故障征兆时,现场通讯网络获取监测对象的实时运行状态数据作为待匹配的故障数据特征,根据一定的故障判定准则将待匹配的故障数据特征与故障诊断云平台中保存的故障数据特征进行比对;若比对成功,实现故障诊断,并将故障诊断结果传输至软件层;若比对失败,重复步骤s5,直到模拟出的故障数据特征与待匹配的故障数据特征能够对比成功。
15.进一步地,还包括故障知识库,当步骤s7实现故障诊断时,可根据故障诊断结果从故障知识库中调取相应的故障解决建议,并将此故障解决建议和故障诊断结果一并传输至软件层。
16.往复式天然气压缩机故障诊断系统,包括以边缘层、平台层和软件层三层结构为基本构架的故障诊断云平台,其中:
17.所述边缘层,通过设置在各类监测对象上的物联网感知技术和信息化系统的大数据采集工具,采集监测对象的运行状态和工艺信息的数据,并利用有线或无线的通讯网络将数据传输至智能网关或分布式服务器上;
18.所述平台层,利用云计算和大数据技术搭建故障诊断云平台,利用数据处理技术对边缘层采集的数据进行处理,利用大数据分析和机器学习技术,对边缘层采集的数据进行多方向分析,将数据的处理结果和分析结果发送至基于神经网络的故障诊断模块,完成故障诊断;
19.所述软件层,基于故障诊断云平台形成满足不同场景的故障诊断软件,通过用户终端设备向用户展示监测对象运行状态和故障诊断结果。
20.进一步地,所述边缘层的物联网感知技术通过各类传感器,结合rfid、视频监控和生产监测设备的手段,采集监测对象状态的常规物理量数据和工业现场环境数据,利用蜂窝网技术或局域网传输到边缘层;而大数据采集工具包括系统采集器,或是dcs系统、plc、第三方采集系统等,或是测试仪器类的离线采集设备。
21.进一步地,所述平台层的数据处理技术包括hdfs,或是spark,或是hive,或是kafka。
22.进一步地,所述平台层的多方向分析包括横向分析、纵向分析,其中:
23.横向分析,互相对比相同监测对象的实时状态数据;
24.纵向分析,将同一个监测对象的历史数据互相对比,精准分析不同环境和工况下的监控对象状态数据。
25.进一步地,所述故障诊断云平台包括状态监测模块、机组信息模块、运行管理模块、故障维修模块、维修保养模块、文件管理模块、管理报表模块、项目及合同管理模块、系统管理模块;
26.其中状态监测模块对工业常见的往复机械、发动机组等设备的振动、温度、压力、流量、电流、转速、电压等状态量和工艺量进行的在线监测、离线监测,以及针对不同的监测
对象设置专属的报警方式和分析诊断。
27.进一步地,所述故障诊断软件是基于ios系统或android系统的手机app,或是基于pc端的软件,用户可实时查看授权范围内的故障诊断云平台所提供的信息,动态了解监测对象当前运行状态和工况;出现报警时,故障诊断软件可实时推送报警信息,并提供故障诊断结果和故障解决建议,推送后续检维修待办事项提示。
28.对于压缩机类的设备,在线状态监测是实时了解和掌握机械装维运行状态与功能特性的必要手段之一,故障诊断是判断系统是否发生故障以及故障发生位置、故障损坏程度、故障类型的有效途径之一。本发明基于现有故障诊断系统成果,开发了以“边缘层、平台层和软件层”为基本架构的云平台,将ai算法植入边缘层计算网关,智能网关将关键数据实时上传至云端,在云端最终实现基于智能预警模型的预测性维护。云平台提供了针对工业数据的存储、分析和管理功能需求的众多服务,并满足工业安全的要求。与传统的故障诊断系统部署方式相比,云平台提供了数据库、高性能计算、工业数据分析等众多服务。同时,基于rcm原理构建的维修与安全保障信息化、智能化、专业化设备动态决策管理系统。对设备的检维修、维修优化、耗材记录以及剩余工作寿命等进行管理,在保证设备运行安全的前提下确定最小的维修任务需求,合理分配维修资源,实现设备长周期运转。
29.本发明故障诊断云平台服务功能实现流程如下:
30.平台边缘层的传感器安装在监测对象各关键部位,以采集机组不同工况运行状态下的振动与热工等特征参数。基于ai的智能边缘计算网关实时采集、处理、传输和存储数据,以及各类型设备不同故障的波形和频谱数据分析经验,研发应用了基于人工智能的智能预警模型和智能维修决策模型,根据实时采集的数据动态优化参数,现已植入到智能边缘计算网关,实现设备故障的近场预警和处理。智能网关将关键数据实时上传至云端,云端通过对同一型号不同设备,以及不同型号不同设备的海量数据进行大数据分析和处理。利用时域频域等特征提取方法,研究故障机理,采用参数化与非参数化方法相结合的手段提取故障特征,建立基于数据的机理知识规则和统计信息数据库,实时更新和优化模型,并将优化后的模型下发到相应的智能网关,完成云端一体的智能阈值报警模型的优化和更新。同时根据前期的技术积累,结合设备机理知识和数字双胞胎技术,把模型的颗粒度细化到具体的单台设备,实时建立从型号到具体设备的数字化模型,并关联设备实际工况,实现机组的智能化预测性维护。
31.本发明采用神经网络算法结合现场安装调试时实测数据对监测对象模型的热、动力学数学模型进行拟合优化,大幅度提高数学模型对监测对象的模拟精度。在故障诊断过程中,为准确判断故障原因和部位提供了参照标准。
32.综上所述,由于采用了上述技术方案,本发明的有益效果是:
33.1.本发明基于现有故障诊断系统成果,开发了以“边缘层、平台层和软件层”为基本架构的云平台,此故障诊断云平台为往复式天然气压缩机设备提供监测、故障预警、维修决策及生产排程优化等业务功能,集设备运行状态感知、数据分析、数据决策等解决方案于一体的物联网应用平台,旨在保障企业设备长周期、高效、节能、稳定的运行。
34.2.本发明的故障诊断方法为:将传感器等大数据采集工具安装在监测对象的各个关键部位,以采集监测对象不同工况运行状态下的特征参数;基于人工智能的计算网关实时处理、传输和存储上述特征参数,以及监测对象不同故障的波形和频谱分析经验,建立基
于人工智能的智能预警模型和智能维修决策模型,根据实时采集的特征参数,植入到智能网关,实现监测对象故障的进场预警和处理;智能网关将关键数据实时上传至云平台,云平台通过对同一型号不同设备,以及不同型号不同设备的海量数据进行大数据分析和处理,利用时域频域等特征提取方法,建立仿真数学模型,并实时更新和优化仿真数学模型,并将优化后的模型下发到相应的智能网关,完成云端一体的智能阈值报警模型的优化和更新。同时,采用神经网络算法结合现场安装调试时实测数据对监测对象模型的热、动力学数学模型进行拟合优化,大幅度提高数学模型对监测对象的模拟精度。在故障诊断过程中,为准确判断故障原因和部位提供了参照标准。
附图说明
35.为了更清楚地说明本发明实施例的技术方案,下面将对实施例中所需要使用的附图作简单地介绍,应当理解,以下附图仅示出了本发明的某些实施例,因此不应被看作是对范围的限定,对于本领域普通技术人员来讲,在不付出创造性劳动的前提下,还可以根据这些附图获得其他相关的附图,其中:
36.图1是故障诊断云平台示意图;
37.图2是“边缘层、平台层和软件层”的基本架构示意图。
具体实施方式
38.为了使本发明的目的、技术方案及优点更加清楚明白,以下结合附图及实施例,对本发明进行进一步详细说明。应当理解,此处所描述的具体实施例仅用以解释本发明,并不用于限定本发明,即所描述的实施例仅仅是本发明一部分实施例,而不是全部的实施例。通常在此处附图中描述和示出的本发明实施例的组件可以以各种不同的配置来布置和设计。
39.因此,以下对在附图中提供的本发明的实施例的详细描述并非旨在限制要求保护的本发明的范围,而是仅仅表示本发明的选定实施例。基于本发明的实施例,本领域技术人员在没有做出创造性劳动的前提下所获得的所有其他实施例,都属于本发明保护的范围。
40.需要说明的是,术语“第一”和“第二”等之类的关系术语仅仅用来将一个实体或者操作与另一个实体或操作区分开来,而不一定要求或者暗示这些实体或操作之间存在任何这种实际的关系或者顺序。而且,术语“包括”、“包含”或者其任何其他变体意在涵盖非排他性的包含,从而使得包括一系列要素的过程、方法、物品或者设备不仅包括那些要素,而且还包括没有明确列出的其他要素,或者是还包括为这种过程、方法、物品或者设备所固有的要素。在没有更多限制的情况下,由语句“包括一个
……”
限定的要素,并不排除在包括所述要素的过程、方法、物品或者设备中还存在另外的相同要素。
41.下面结合实施例对本发明的特征和性能作进一步的详细描述。
42.实施例一
43.往复式天然气压缩机故障诊断系统,如图2所示,包括以边缘层、平台层和软件层三层结构为基本构架的故障诊断云平台,其中:
44.所述边缘层,通过设置在各类监测对象上的物联网感知技术和信息化系统的大数据采集工具,采集监测对象的运行状态和工艺信息的数据,并利用有线或无线的通讯网络将数据传输至智能网关或分布式服务器上;所述物联网感知技术通过各类传感器,结合
rfid、视频监控和生产监测设备的手段,采集监测对象状态的常规物理量数据和工业现场环境数据,利用蜂窝网技术或局域网传输到边缘层;而大数据采集工具包括系统采集器,或是dcs系统、plc、第三方采集系统等,或是测试仪器类的离线采集设备。
45.所述平台层,利用云计算和大数据技术搭建故障诊断云平台,利用数据处理技术对边缘层采集的数据进行处理,利用大数据分析和机器学习技术,对边缘层采集的数据进行多方向分析,将数据的处理结果和分析结果发送至基于神经网络的故障诊断模块,完成故障诊断;所述数据处理技术包括hdfs,或是spark,或是hive,或是kafka。
46.所述软件层,基于故障诊断云平台形成满足不同场景的故障诊断软件,通过用户终端设备向用户展示监测对象运行状态和故障诊断结果。
47.实施例二
48.本实施例是实施例1的补充说明。
49.所述平台层的多方向分析包括横向分析、纵向分析,其中:
50.横向分析,互相对比相同监测对象的实时状态数据;
51.纵向分析,将同一个监测对象的历史数据互相对比,精准分析不同环境和工况下的监控对象状态数据。
52.平台层将来自边缘层的采集数据实时上传至云端平台,基于hdfs、spark、hive、kafka等数据处理技术,利用大数据分析和机器学习对实时上传至云端的数据作分析,横向对比同型号设备状态实时数据,纵向对比历史数据,精准定位不同环境和工况下的设备状态。同时,基于对实时数据和历史故障案例数据的动态训练和学习,优化智能维修决策模型和智能预警模型,并下发至软件层应用和边缘层智能网关,为企业设备提供诊断和维修决策支持。
53.实施例三
54.本实施例是实施例1的补充说明。
55.如图1所示,所述故障诊断云平台包括状态监测模块、机组信息模块、运行管理模块、故障维修模块、维修保养模块、文件管理模块、管理报表模块、项目及合同管理模块、系统管理模块;其中状态监测模块对工业常见的往复机械、发动机组等设备的振动、温度、压力、流量、电流、转速、电压等状态量和工艺量进行的在线监测、离线监测,以及针对不同的监测对象设置专属的报警方式和分析诊断。往复式天然气压缩机故障诊断系统云平台提供设备监/检测、预警、分析、诊断、检维修、维修决策、设备耗材等覆盖设备管理各个层次的服务。
56.进一步地,所述故障诊断软件是基于ios系统或android系统的手机app,或是基于pc端的软件,用户可实时查看授权范围内的故障诊断云平台所提供的信息,动态了解监测对象当前运行状态和工况;出现报警时,故障诊断软件可实时推送报警信息,并提供故障诊断结果和故障解决建议,推送后续检维修待办事项提示。
57.实施例四
58.往复式天然气压缩机故障诊断方法,包括上述的故障诊断系统,故障诊断方法包括以下步骤:
59.s1:将传感器等大数据采集工具安装在监测对象的各个关键部位,以采集监测对象不同工况运行状态下的特征参数;
60.s2:基于人工智能的计算网关实时处理、传输和存储上述特征参数,以及监测对象不同故障的波形和频谱分析经验,建立基于人工智能的智能预警模型和智能维修决策模型,根据实时采集的特征参数,植入到智能网关,实现监测对象故障的进场预警和处理;
61.s3:智能网关将关键数据实时上传至云平台,云平台通过对同一型号不同设备,以及不同型号不同设备的海量数据进行大数据分析和处理,利用时域频域等特征提取方法,建立仿真数学模型,并实时更新和优化仿真数学模型,并将优化后的模型下发到相应的智能网关,完成云端一体的智能阈值报警模型的优化和更新。
62.实施例五
63.本实施例是实施例4的补充说明。
64.步骤s3中所述的仿真数学模型的建立、优化方法步骤为:
65.s4:基于监测对象各个零部件的特性参数、监测对象的工艺信息数据、监测对象的实时运行状态数据,经滤波去除噪声后,建立监测对象的理想热力学方程、理想动力学方程和理想振动力学方程,得到监测对象的理想数学模型;
66.s5:监测对象运行阶段,向理想数学模型中输入由边缘层采集的数据,结合bp神经网络方法和结构动力学修改,建立监测对象的仿真热力学模型、仿真动力学模型及仿真振动力学模型,得到监测对象的仿真数学模型,并将建立的仿真数学模型保存至故障诊断云平台;
67.s6:通过神经网络算法迭代改变仿真数学模型中有关故障部位参数,模拟监测对象不同部位的各种故障,获得故障数据特征,并将此故障数据特征保存至故障诊断云平台;
68.s7:当监测对象出现故障征兆时,现场通讯网络获取监测对象的实时运行状态数据作为待匹配的故障数据特征,根据一定的故障判定准则将待匹配的故障数据特征与故障诊断云平台中保存的故障数据特征进行比对;若比对成功,实现故障诊断,并将故障诊断结果传输至软件层;若比对失败,重复步骤s5,直到模拟出的故障数据特征与待匹配的故障数据特征能够对比成功。
69.值得一提的是,还包括故障知识库,当步骤s7实现故障诊断时,可根据故障诊断结果从故障知识库中调取相应的故障解决建议,并将此故障解决建议和故障诊断结果一并传输至软件层。
70.以上所述仅为本发明的较佳实施例而已,并不用以限制本发明的保护范围,任何熟悉本领域的技术人员在本发明的精神和原则之内所作的任何修改、等同替换和改进等,均应包含在本发明的保护范围之内。