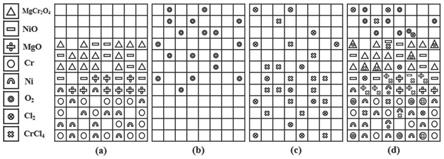
1.本发明属于元胞自动机演变研究技术领域,特别涉及一种基于元胞自动机的镍基合金腐蚀层动态演变分析方法。
技术背景
2.在聚光式太阳能发电厂中,传热以及储热系统是其主要的部分,直接影响了系统的工作效率和成本。氯化物熔盐因其热容大、粘度低、使用温度高、温度范围宽、热稳定性好且成本较低等优点,成为较为优秀的传热和储热材料。然而在高温下,氯化物熔盐对管道或容器等金属结构材料具有很高的腐蚀性。对氯化物熔盐腐蚀性的研究较为困难,实验周期较长并且难以研究腐蚀过程,因此部分学者选择使用先进的计算方法来对腐蚀过程进行模拟研究。元胞自动机法与其它模拟方法相比,计算方法简单、运行速度快、模拟准确度高,是常用的模拟方法。目前对于金属腐蚀过程的元胞自动机模拟方式主要有以下几种:
3.1、模拟表面形貌的元胞自动机法:利用元胞自动机法对粗糙金属与电解质的界面腐蚀表面形貌进行了模拟。该模型考虑了金属在实际腐蚀过程中不同区域的不同腐蚀方式,将顶部区域和底部区域分别讨论。而此模型是通过调整反应速率和每个区域的局部化程度,从而得到不同的腐蚀形貌,并没有考虑实际腐蚀过程中发生的具体的反应,腐蚀形貌虽然相近,但关键的腐蚀过程并不一致。
4.2、模拟腐蚀坑相互作用的元胞自动机法:利用元胞自动机和有限元方法对机械与化学作用下的不锈钢亚稳腐蚀坑的相互作用进行了预测。该模型不单单是从形貌上对腐蚀坑间的相互作用进行了模拟,还研究了腐蚀坑相互作用过程中的电流特性与坑稳定产物。但此模型并不适用镍基合金在氯化物熔盐中发生的腐蚀行为,不能反映出镍基合金在腐蚀过程中关键的腐蚀层形貌变化及元素流失情况,实用性低。
5.3、模拟晶内与晶界腐蚀的元胞自动机法:利用元胞自动机法研究了几何结构对晶间腐蚀以及晶间和晶内腐蚀的影响。该模型将传统的二维模型推广至了三维模型,较好地展示了各向异性或各向同性以及不同布局的各种晶粒的几何结构,以及在腐蚀过程中晶粒的几何变化与剥离过程。但该模型的实用性较低,定义的演化规则过于简单,与实际腐蚀行为中发生的一系列复杂过程吻合较差。
6.4、模拟腐蚀坑形貌的元胞自动机法:利用元胞自动机法计算了腐蚀坑的数量与深度,并模拟了腐蚀坑的萌生与长大过程。模拟结果较好地反映了腐蚀过程的随机性,模型的初始过程与生长过程与数学模型吻合良好。但此模型仅能预测短期内腐蚀坑的生长规律,不能对长期腐蚀行为进行预测。
技术实现要素:7.鉴于现有技术的缺陷,本发明旨在于提供一种基于元胞自动机的镍基合金腐蚀层动态演变分析方法,本发明的模拟结果与实际过程吻合度高,不仅可以获得清晰的腐蚀过程,还可以得知相应的元素含量变化情况。同时,还可以预测腐蚀层厚度的变化与质量损失
趋势,实用性强。
8.为了实现上述目的,本发明采用的技术方案如下:
9.一种基于元胞自动机的镍基合金腐蚀层动态演变分析方法,包括用于分析各个元胞,以及腐蚀实验中实际的合金样品,所述方法包括以下步骤:
10.步骤1:基于所述合金样品的实际形状,选取相应的坐标系,定义二维元胞空间,选取margolus型邻居,并确定周期性边界条件;
11.步骤2:根据氯化物熔盐及所述合金的组成,定义元胞空间中不同格位的属性;
12.步骤3:在元胞自动机空间中定义演化规则,实现元胞自动机空间中各个元胞间的相互转换,通过matlab软件将演化规则转化为程序语言;
13.步骤4:设置适当的模拟时间步长,利用二维元胞自动机方法,模拟镍基合金在氯化物熔盐中的腐蚀过程,获得截面腐蚀层形貌随模拟时间步长变化的动态演变过程的模拟结果;
14.步骤5:通过对模拟腐蚀形貌的分析,获得腐蚀层厚度随模拟时间步长增加的变化曲线,以及腐蚀层厚度变化趋势与实际腐蚀过程中的质量损失的关系。
15.需要说明的是,所述步骤3中,所述演化规则可通过对高温氯化物熔盐中腐蚀性物质的扩散规律、截面腐蚀层厚度的增长机理及腐蚀过程中发生的化学反应所获得。
16.需要说明的是,所述各个元胞包括腐蚀元胞、金属元胞、腐蚀层元胞和逃逸元胞;其中,腐蚀元胞包括o2和cl2,金属元胞包括cr和ni,腐蚀层元胞包括mgcr2o4、mgo和nio,逃逸元胞为crcl4。
17.需要说明的是,所述步骤3包括:
18.步骤3.1将元胞空间的左半部分定义为氯化物熔盐部分,腐蚀元胞以一定浓度存在于其中;右半部分定义为合金部分,由固定比例的金属元胞cr和ni组成,该元胞空间的状态用来模拟实际的腐蚀环境;
19.步骤3.2在每一个模拟时间步长下,处于格位(x,y)的中心腐蚀元胞以一定概率向其邻居元胞随机移动,该邻居元胞作为下一时间步长的目标元胞;
20.步骤3.3若步骤3.2中,中心腐蚀元胞的目标元胞为空,则在下一时间步长,该格位被腐蚀元胞占据;若目标元胞处已被其它腐蚀元胞占据,则下一时间步长,中心腐蚀元胞仍停留在格位(x,y);
21.步骤3.4若步骤3.2中,中心腐蚀元胞的目标元胞为金属元胞,则在下一时间步长,腐蚀元胞o2与金属元胞cr或ni、腐蚀元胞cl2与金属元胞cr以一定概率发生反应;
22.步骤3.5若步骤3.4中,腐蚀元胞o2与金属元胞cr的反应发生,则在下一时间步长,获得腐蚀层元胞mgo和逃逸元胞crcl4。金属元胞cr的格位被mgo格位代替;若反应不发生,金属元胞cr仍占据原格位,腐蚀元胞o2重复步骤3.2的过程;
23.步骤3.6若步骤3.4中腐蚀元胞o2与金属元胞ni的反应发生,则在下一时间步长,金属元胞ni的格位被nio格位代替;若反应不发生,金属元胞ni仍占据原格位,腐蚀元胞cl2重复步骤3.2的过程;
24.步骤3.7若步骤3.4中腐蚀元胞cl2与金属元胞cr的反应发生,则在下一时间步长,获得逃逸元胞crcl4,金属元胞cr的格位变为空格位。
25.步骤3.8步骤3.5和步骤3.7获得的逃逸元胞crcl4中,一部分以一定概率向熔盐部
分扩散,一部分与腐蚀层元胞mgo、腐蚀元胞o2以一定概率发生反应。若反应发生,则在下一时间步长,获得腐蚀层元胞mgcr2o4和腐蚀元胞cl2,逃逸元胞crcl4、腐蚀层元胞mgo、腐蚀元胞o2消失,腐蚀层元胞mgo的格位被腐蚀层元胞mgcr2o4格位代替。
26.步骤3.9步骤3.8中的腐蚀元胞cl2重复步骤3.2的过程。
27.需要说明的是,所述二维元胞空间的长和宽均为400个网格宽度。
28.需要说明的是,还包括对所述模拟结果进行验证,在600℃下的nacl
‑
cacl2‑
mgcl2熔盐中腐蚀21天的所述合金的腐蚀结果与模拟结果进行比较,对模拟结果进行验证。
29.本发明的有益效果在于:
30.首先,本发明模拟结果与实际过程吻合度高,不仅可以获得清晰的腐蚀过程,还可以得知相应的元素含量变化情况。同时,还可以预测腐蚀层厚度的变化与质量损失趋势,实用性强。
31.其次,本发明中的演化规则是按照实际腐蚀过程定义的,实际腐蚀机理与发生的化学反应已由实验得到验证。通过将每一步化学反应转化为对应的程序语言进行表达,使得模型与实际情况更符合。模拟的外腐蚀层与实际腐蚀情况下腐蚀产物积累而成的外腐蚀层的形貌与厚度一致,模拟的内腐蚀层与实际腐蚀情况下由于cr缺失而导致的内腐蚀层的形貌与厚度也一致。
32.最后,本发明通过调整模拟时间步长,可得到不同时间步长下的截面腐蚀层形貌变化过程,同时可以获得与之对应的元素含量变化情况,对研究腐蚀过程中合金形貌与元素含量的变化有很大意义。同时,还可以得到总腐蚀层、外腐蚀层和内腐蚀层厚度的变化曲线,预测合金在长期腐蚀下的腐蚀层厚度变化情况。同时,通过总腐蚀层厚度的变化趋势可以预测合金的质量损失趋势。将二者结合,可以达到预测金属结构管道和容器使用寿命的目的。
附图说明
33.图1为模型中元胞空间及不同属性的元胞示意图;
34.图2为模型的初始形貌;
35.图3为腐蚀层的生长过程(左)和含铬元胞的积累数量(右);
36.图4为截面腐蚀层模拟结果与实验结果sem照片的对比;
37.图5为实验结果中铬元素含量线扫结果(左)与模拟结果中含铬元胞积累数量(右)的对比;
38.图6为腐蚀层总厚度的模拟结果(左)和内外腐蚀层厚度的模拟结果(右);
39.图7为模拟的腐蚀层厚度增长曲线与实际腐蚀过程质量损失曲线的对比。
具体实施例
40.以下将结合附图对本发明作进一步的描述,需要说明的是,本实施例以本技术方案为前提,给出了详细的实施方式和具体的操作过程,但本发明的保护范围并不限于本实施例。
41.需要指出的是,本发明中的合金样本可为inconel 625合金样品。
42.需要指出的是,本发明中共包括4种元胞,分别为腐蚀元胞、金属元胞,腐蚀层元胞
和逃逸元胞,其中:
43.1、腐蚀元胞分别为o2和cl2,它们以一定浓度随机分布于高温氯化物熔盐中,可以把金属元胞腐蚀掉,在整个元胞自动机空间中,腐蚀元胞o2和cl2随着模拟时间步长的改变以一定概率随机运动;
44.2、金属元胞分别为cr和ni,它们以固定比例存在于元胞空间中,代表镍基inconel 625合金中的元素比例。并且金属元胞cr和ni的位置被认为是固定的,不发生改变;
45.3、腐蚀层元胞分别为mgcr2o4、mgo和nio,它们是由腐蚀元胞o2、cl2和金属元胞cr、ni发生反应后的产物,形成后位置保持不变,在二维元胞空间中共同组成了腐蚀层中的外腐蚀层;
46.4、逃逸元胞为crcl4,是由腐蚀元胞o2和cl2与金属元胞cr相互作用后的产物,但与腐蚀层元胞mgcr2o4、mgo和nio不同的是,crcl4一旦形成,一部分crcl4会与腐蚀元胞o2继续发生反应,一部分crcl4则会从金属部分逸出,逸出的crcl4的格位会变为空格位,即该处无任何物理意义。
47.实施例
48.本发明为一种基于元胞自动机的镍基合金腐蚀层动态演变分析方法,包括用于分析各个元胞,以及腐蚀实验中实际的合金样品,所述方法包括以下步骤:
49.步骤1:基于所述合金样品的实际形状,选取相应的坐标系,定义二维元胞空间,选取margolus型邻居,并确定周期性边界条件;
50.步骤2:根据氯化物熔盐及所述合金的组成,定义元胞空间中不同格位的属性;
51.步骤3:在元胞自动机空间中定义演化规则,实现元胞自动机空间中各个元胞间的相互转换,通过matlab软件将演化规则转化为程序语言;
52.步骤4:设置适当的模拟时间步长,利用二维元胞自动机方法,模拟镍基合金在氯化物熔盐中的腐蚀过程,获得截面腐蚀层形貌随模拟时间步长变化的动态演变过程的模拟结果;
53.步骤5:通过对模拟腐蚀形貌的分析,获得腐蚀层厚度随模拟时间步长增加的变化曲线,以及腐蚀层厚度变化趋势与实际腐蚀过程中的质量损失的关系。
54.需要说明的是,所述步骤3中,所述演化规则可通过对高温氯化物熔盐中腐蚀性物质的扩散规律、截面腐蚀层厚度的增长机理及腐蚀过程中发生的化学反应所获得。
55.需要说明的是,所述各个元胞包括腐蚀元胞、金属元胞、腐蚀层元胞和逃逸元胞;其中,腐蚀元胞包括o2和cl2,金属元胞包括cr和ni,腐蚀层元胞包括mgcr2o4、mgo和nio,逃逸元胞为crcl4。
56.需要说明的是,所述步骤3包括:
57.步骤3.1将元胞空间的左半部分定义为氯化物熔盐部分,腐蚀元胞以一定浓度存在于其中;右半部分定义为合金部分,由固定比例的金属元胞cr和ni组成,该元胞空间的状态用来模拟实际的腐蚀环境;
58.步骤3.2在每一个模拟时间步长下,处于格位(x,y)的中心腐蚀元胞以一定概率向其邻居元胞随机移动,该邻居元胞作为下一时间步长的目标元胞;
59.步骤3.3若步骤3.2中,中心腐蚀元胞的目标元胞为空,则在下一时间步长,该格位被腐蚀元胞占据;若目标元胞处已被其它腐蚀元胞占据,则下一时间步长,中心腐蚀元胞仍
停留在格位(x,y);
60.步骤3.4若步骤3.2中,中心腐蚀元胞的目标元胞为金属元胞,则在下一时间步长,腐蚀元胞o2与金属元胞cr或ni、腐蚀元胞cl2与金属元胞cr以一定概率发生反应;
61.步骤3.5若步骤3.4中,腐蚀元胞o2与金属元胞cr的反应发生,则在下一时间步长,获得腐蚀层元胞mgo和逃逸元胞crcl4。金属元胞cr的格位被mgo格位代替;若反应不发生,金属元胞cr仍占据原格位,腐蚀元胞o2重复步骤3.2的过程;
62.步骤3.6若步骤3.4中腐蚀元胞o2与金属元胞ni的反应发生,则在下一时间步长,金属元胞ni的格位被nio格位代替;若反应不发生,金属元胞ni仍占据原格位,腐蚀元胞cl2重复步骤3.2的过程;
63.步骤3.7若步骤3.4中腐蚀元胞cl2与金属元胞cr的反应发生,则在下一时间步长,获得逃逸元胞crcl4,金属元胞cr的格位变为空格位。
64.步骤3.8步骤3.5和步骤3.7获得的逃逸元胞crcl4中,一部分以一定概率向熔盐部分扩散,一部分与腐蚀层元胞mgo、腐蚀元胞o2以一定概率发生反应。若反应发生,则在下一时间步长,获得腐蚀层元胞mgcr2o4和腐蚀元胞cl2,逃逸元胞crcl4、腐蚀层元胞mgo、腐蚀元胞o2消失,腐蚀层元胞mgo的格位被腐蚀层元胞mgcr2o4格位代替。
65.步骤3.9步骤3.8中的腐蚀元胞cl2重复步骤3.2的过程。
66.需要说明的是,所述二维元胞空间的长和宽均为400个网格宽度。
67.需要说明的是,还包括对所述模拟结果进行验证,在600℃下的nacl
‑
cacl2‑
mgcl2熔盐中腐蚀21天的所述合金的腐蚀结果与模拟结果进行比较,对模拟结果进行验证。
68.如图1所示,为不同的元胞分散在图中三个平行的元胞空间中,其中cr、ni、mgo、mgcr2o4、nio格位被认为是固定的,并且使用元胞空间(a)。o2可以在熔盐中自由移动并扩散到外层腐蚀层,使用元胞空间(b)。cl2可以扩散到内部腐蚀层和金属基底,与crcl4共同使用元胞空间(c)。三个元胞空间叠加后形成元胞空间(d)。不同属性的元胞所处的元胞空间特性与实际腐蚀过程中各种物质的位置与扩散方式相同,能够反映真实的腐蚀状态。
69.如图2所示,图中左侧代表一定浓度的o2与cl2,在腐蚀还未开始时存在于熔盐中。右侧代表金属基体,由cr与ni组成。初始形貌符合实际环境中腐蚀还未开始的初始阶段。
70.如图3所示,随着模拟时间步长的增加,代表cr与ni的元胞随着反应的进行逐渐被腐蚀掉,mgcr2o4、mgo和nio元胞随之生成,逐渐积累在一起形成了模型中的外腐蚀层。生成的逃逸元胞crcl4逃逸出金属基体,原格位变成空格位,从而形成内腐蚀层。模型中的外腐蚀层与内腐蚀层的形成过程与形貌与实际腐蚀过程得到的腐蚀层形成过程与形貌一致。
71.在模拟的初始阶段,生成的腐蚀层元胞mgcr2o4积累在外腐蚀层中,因此含cr元胞的数量略微升高。随着模拟的进行,大量逃逸元胞crcl4逐渐生成,并离开金属基体,因此含cr元胞的数量逐渐降低。在金属基体的较深处,腐蚀行为并不严重,因此含cr元胞的数量逐渐升高。在金属基体的更深处,腐蚀行为并没有发生,含cr元胞的数量维持在较稳定的水平。
72.如图4所示,将截面腐蚀层模拟结果与实际腐蚀后的形貌进行对比后发现,二者的外腐蚀层和内腐蚀层的厚度基本一致,模拟结果能很好地反应出所述合金样品实际腐蚀后的结果。
73.如图5所示,将本发明的合金样品实际腐蚀后的铬元素含量变化曲线与模拟结果
中含cr元胞的积累数量进行对比,二者的变化趋势基本一致,模拟结果能很好地反应实际腐蚀过程中元素含量的变化趋势。
74.如图6所示,将模拟结果中腐蚀层厚度随模拟时间步长的变化情况绘制成曲线,反映出了总腐蚀层、外腐蚀层和内腐蚀层厚度的变化情况,而腐蚀层厚度的变化在实际腐蚀过程中是难以得到的,利用此二维元胞自动机方法可以为探究实际腐蚀过程中腐蚀层的厚度提供参考。
75.如图7所示,将模拟的腐蚀层厚度增长曲线与实际腐蚀过程中所述合金样品的质量损失曲线进行对比,二者的吻合度较好。在实际工况中,金属容器或管道的质量损失是衡量其使用寿命的重要依据,但通过传统的腐蚀实验对质量损失进行探究难度较大,周期性较长。利用此二维元胞自动机方法可以大幅度缩减研究时间,可以达到预测金属结构管道和容器使用寿命的目的,有着较为重要的意义。
76.对于本领域的技术人员来说,可以根据以上的技术方案和构思,给出各种相应的改变,而所有的这些改变,都应该包括在本发明权利要求的保护范围之内。