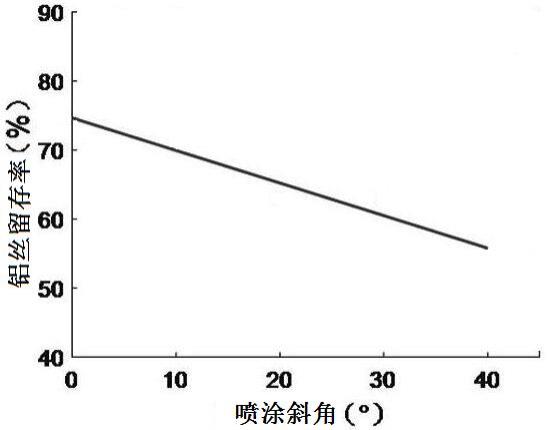
1.本发明涉及到飞机制造喷涂技术领域,尤其涉及一种自动火焰铝喷涂电阻的标定方法。
背景技术:2.先进复合材料主要指高性能纤维,如:硼纤维、碳纤维和芳纶这些增强的树脂基复合材料,以其耐高温、耐疲劳、阻尼减震性好、破损安全性好及性能可设计的优势,逐渐取代金属部件,在现代飞行器表面上取得重要应用。但复合材料具有导电性差、电阻率高的缺陷,在飞行过程中,飞机遭受雷击的事件在国内外时有发生。迄今复合材料雷击防护技术主要有四种,分别是网箔保护法、表面层保护法、复合胶膜保护法和添加导电材料保护法。火焰喷铝是最常用的表面层保护法之一。
3.火焰喷铝是通过乙炔气体燃烧产生的高温,将铝丝或铝粉熔融喷覆在零件表面形成铝层的一种表面处理工艺。质量指标为铝表面电阻的大小和均匀性。人工火焰喷铝需要通过经验来控制喷涂的厚度,厚度与电阻呈现一定的函数关系,喷涂后铝层电阻,如果铝层偏厚则进行打磨,如果铝层偏薄则进行补喷。
4.机器人自动化火焰喷铝能够精确控制各工艺参数,为保证涂层质量、取消打磨和补喷提供了可行性,有助于形成良好有效的闪电防护结构,保证飞机飞行的可靠性和安全性。
5.公开号为cn 112030093a,公开日为2020年12月04日的中国专利文献公开了一种机器人火焰喷铝最佳路径间距的获取方法,其特征在于,测量单条喷涂轨迹横截面厚度渐变值,拟合正态分布曲线,得到火焰喷铝单条喷涂横截面厚度渐变拟合曲线,并用正态分布标准差作为机器人自动火焰喷铝的路径间距。
6.该专利文献公开的机器人火焰喷铝最佳路径间距的获取方法,通过测量、推导和拟合计算得到参数,过程相对简单、准确,效率高。当火焰喷铝的路径间距等于单条喷涂横截面的正态分布标准差时,得到的涂层质量较佳。但是,参数的确定并不精确,影响电阻值的准确确定,从而影响实际喷涂质量和喷涂效果。
技术实现要素:7.本发明为了克服上述现有技术的缺陷,提供一种自动火焰铝喷涂电阻的标定方法,本发明通过合理的参数筛选确定,能够避免一遍遍地进行火焰喷铝,逐个调节参数测试才能得到目标涂层电阻,能够精准确定电阻值,保障实际喷涂质量和喷涂效果。
8.本发明通过下述技术方案实现:
9.一种自动火焰铝喷涂电阻的标定方法,其特征在于,包括以下步骤:
10.a、通过前期的工艺实验和数学推理,确定基础输入参数在送丝输入阶段、铝丝燃烧阶段和喷涂阶段的数学机理,建立数学模型;
11.b、通过建立的数学模型,解出数学模型中的数学关系式和数学拟合关系式;设点
火后喷涂时间为t,通过式1计算确定燃烧的铝丝长度l
s
;
12.l
s
=v
s
·
t
ꢀꢀꢀ
式1
13.其中,l
s
为燃烧的铝丝长度,v
s
为送丝速率,t为点火后喷涂时间;
14.设铝丝直径为d,铝丝密度为ρ,通过式2计算确定燃烧的铝丝重量w
s
;
[0015][0016]
其中,w
s
为燃烧的铝丝重量,d为铝丝直径,l
s
为燃烧的铝丝长度,ρ为铝丝密度;
[0017]
经实验测定喷涂高度h和喷涂斜角θ,通过式3计算确定铝丝留存率η,确定喷涂斜角θ与铝丝留存率η之间的拟合关系曲线;
[0018]
η=f1(θ,h)
ꢀꢀꢀ
式3
[0019]
其中,η为铝丝留存率,θ为喷涂斜角,h为喷涂高度,f1为喷涂斜角与喷涂高度交互影响对铝丝留存率的映射关系;
[0020]
通过式4计算留存在零件表面的铝重量w
c
,设铝层的密度为ρ',通过式5计算留存在零件表面的铝体积为v
c
,通过式6计算喷涂面积s,通过式7计算铝层厚度δ;
[0021]
w
c
=w
s
·
η
ꢀꢀꢀꢀ
式4
[0022]
其中,w
c
为留存在零件表面的铝重量,w
s
为燃烧的铝丝重量,η为铝丝留存率;
[0023][0024]
其中,v
c
为留存在零件表面的铝体积,w
c
为留存在零件表面的铝重量,ρ'为铝层的密度;
[0025]
s=av
m
t
ꢀꢀꢀꢀ
式6
[0026]
其中,s为喷涂面积,a为轨迹间距,v
m
为移动速率,t为点火后喷涂时间;
[0027][0028]
其中,δ为铝层厚度,v
c
为留存在零件表面的铝体积,s为喷涂面积;
[0029]
c、实验测量并拟合火焰喷铝的铝层电阻r与铝层厚度δ的关系曲线,代入基础输入参数,通过式8计算确定铝层电阻r;
[0030][0031]
其中,r为铝层电阻,f2为铝层厚度与铝层电阻之间的函数关系,δ为铝层厚度,d为铝丝直径,v
s
为送丝速率,ρ为铝丝密度,v
m
为移动速率,a为轨迹间距,ρ'为铝层的密度,f1为喷涂斜角与喷涂高度交互影响对铝丝留存率的映射关系,θ为喷涂斜角,h为喷涂高度。
[0032]
所述步骤a中,基础输入参数是指送丝速率v
s
、喷涂高度h、轨迹间距a、移动速率v
m
和喷涂斜角θ。
[0033]
所述步骤b中,确定喷涂斜角θ与铝丝留存率η之间的拟合关系曲线具体是指映射关系在以喷涂高度h为x轴,喷涂斜角θ为y轴,铝丝留存率η为z轴的三维坐标系下拟合为三维曲面。
[0034]
所述步骤c中,拟合火焰喷铝的铝层电阻r与铝层厚度δ的关系曲线具体是指将铝
层厚度δ与铝层电阻r之间的函数关系拟合为反比例函数。
[0035]
本发明的基本原理如下:
[0036]
通过前期的工艺实验和数学推理,总结出送丝速率vs、喷涂高度h、轨迹间距a、移动速率v
m
和喷涂斜角θ这五个基础输入参数在送丝输入阶段、铝丝燃烧阶段和喷涂阶段的数学机理,在一定设备的各参数许用值范围内,铝丝留存率η主要受喷涂斜角θ、喷涂高度h的影响,次要受移动速率v
m
、送丝速率vs、轨迹间距a和氧气乙炔气压的影响,本发明主要计算喷涂斜角θ与喷涂高度h对铝丝留存率η的影响,映射关系在以喷涂高度h为x轴,喷涂斜角θ为y轴,铝丝留存率η为z轴的三维坐标系下可以拟合为一个三维曲面,因火焰喷铝的铝层厚度δ一般低于0.1mm,厚度测量值受到接触式测量影响,采用磁力测厚仪、游标卡尺的方式测量拟合的关系曲线有一定不同,因此,将铝层厚度δ与铝层电阻r之间的函数关系拟合为反比例函数,然后建立数学模型,解出模型中的数学关系式和数学拟合关系式,最后通过基础输入参数能计算出涂层的理论电阻。对于自动化火焰喷铝机器人设备,能够避免一遍遍地进行火焰喷铝、逐个调节参数测试才能得到目标涂层电阻的问题,通过输入基础参数就能够计算得到涂层的理论电阻,进而为实际喷涂提供准确的数据支撑。
[0037]
本发明的有益效果主要表现在以下方面:
[0038]
1、本发明,a、通过前期的工艺实验和数学推理,确定基础输入参数在送丝输入阶段、铝丝燃烧阶段和喷涂阶段的数学机理,建立数学模型;b、通过建立的数学模型,解出数学模型中的数学关系式和数学拟合关系式;设点火后喷涂时间为t,通过式1计算确定燃烧的铝丝长度l
s
;设铝丝直径为d,铝丝密度为ρ,通过式2计算确定燃烧的铝丝重量w
s
;经实验测定喷涂高度h和喷涂斜角θ,通过式3计算确定铝丝留存率η,确定喷涂斜角θ与铝丝留存率η之间的拟合关系曲线;通过式4计算留存在零件表面的铝重量w
c
,设铝层的密度为ρ',通过式5计算留存在零件表面的铝体积为v
c
,通过式6计算喷涂面积s,通过式7计算铝层厚度δ;c、实验测量并拟合火焰喷铝的铝层电阻r与铝层厚度δ的关系曲线,代入基础输入参数,通过式8计算确定铝层电阻r。较现有技术而言,本发明通过合理的参数筛选确定,能够避免一遍遍地进行火焰喷铝,逐个调节参数测试才能得到目标涂层电阻,能够精准确定电阻值,保障实际喷涂质量和喷涂效果。
[0039]
2、本发明,步骤a中,基础输入参数是指送丝速率v
s
、喷涂高度h、轨迹间距a、移动速率v
m
和喷涂斜角θ,通过前期的工艺实验和数学推理,筛选确定得出的这五个基础参数,通过输入基础参数就能够计算得到涂层的理论电阻,进而为实际喷涂提供准确的数据支撑,整个过程简单、科学合理,且效率高。
附图说明
[0040]
下面将结合说明书附图和具体实施方式对本发明作进一步的具体说明:
[0041]
图1为本发明火焰喷铝的铝丝留存率与喷涂斜角的关系拟合图;
[0042]
图2为本发明火焰喷铝的铝层电阻与铝层厚度的关系拟合图。
具体实施方式
[0043]
实施例1
[0044]
参见图1和图2,一种自动火焰铝喷涂电阻的标定方法,包括以下步骤:
[0045]
a、通过前期的工艺实验和数学推理,确定基础输入参数在送丝输入阶段、铝丝燃烧阶段和喷涂阶段的数学机理,建立数学模型;
[0046]
b、通过建立的数学模型,解出数学模型中的数学关系式和数学拟合关系式;设点火后喷涂时间为t,通过式1计算确定燃烧的铝丝长度l
s
;
[0047]
l
s
=v
s
·
t
ꢀꢀꢀ
式1
[0048]
其中,l
s
为燃烧的铝丝长度,v
s
为送丝速率,t为点火后喷涂时间;
[0049]
设铝丝直径为d,铝丝密度为ρ,通过式2计算确定燃烧的铝丝重量w
s
;
[0050][0051]
其中,w
s
为燃烧的铝丝重量,d为铝丝直径,l
s
为燃烧的铝丝长度,ρ为铝丝密度;
[0052]
经实验测定喷涂高度h和喷涂斜角θ,通过式3计算确定铝丝留存率η,确定喷涂斜角θ与铝丝留存率η之间的拟合关系曲线;
[0053]
η=f1(θ,h)
ꢀꢀꢀ
式3
[0054]
其中,η为铝丝留存率,θ为喷涂斜角,h为喷涂高度,f1为喷涂斜角与喷涂高度交互影响对铝丝留存率的映射关系;
[0055]
通过式4计算留存在零件表面的铝重量w
c
,设铝层的密度为ρ',通过式5计算留存在零件表面的铝体积为v
c
,通过式6计算喷涂面积s,通过式7计算铝层厚度δ;
[0056]
w
c
=w
s
·
η
ꢀꢀꢀꢀ
式4
[0057]
其中,w
c
为留存在零件表面的铝重量,w
s
为燃烧的铝丝重量,η为铝丝留存率;
[0058][0059]
其中,v
c
为留存在零件表面的铝体积,w
c
为留存在零件表面的铝重量,ρ'为铝层的密度;
[0060]
s=av
m
t
ꢀꢀꢀꢀ
式6
[0061]
其中,s为喷涂面积,a为轨迹间距,v
m
为移动速率,t为点火后喷涂时间;
[0062][0063]
其中,δ为铝层厚度,v
c
为留存在零件表面的铝体积,s为喷涂面积;
[0064]
c、实验测量并拟合火焰喷铝的铝层电阻r与铝层厚度δ的关系曲线,代入基础输入参数,通过式8计算确定铝层电阻r;
[0065][0066]
其中,r为铝层电阻,f2为铝层厚度与铝层电阻之间的函数关系,δ为铝层厚度,d为铝丝直径,v
s
为送丝速率,ρ为铝丝密度,v
m
为移动速率,a为轨迹间距,ρ'为铝层的密度,f1为喷涂斜角与喷涂高度交互影响对铝丝留存率的映射关系,θ为喷涂斜角,h为喷涂高度。
[0067]
a、通过前期的工艺实验和数学推理,确定基础输入参数在送丝输入阶段、铝丝燃烧阶段和喷涂阶段的数学机理,建立数学模型;b、通过建立的数学模型,解出数学模型中的数学关系式和数学拟合关系式;设点火后喷涂时间为t,通过式1计算确定燃烧的铝丝长度
l
s
;设铝丝直径为d,铝丝密度为ρ,通过式2计算确定燃烧的铝丝重量w
s
;经实验测定喷涂高度h和喷涂斜角θ,通过式3计算确定铝丝留存率η,确定喷涂斜角θ与铝丝留存率η之间的拟合关系曲线;通过式4计算留存在零件表面的铝重量w
c
,设铝层的密度为ρ',通过式5计算留存在零件表面的铝体积为v
c
,通过式6计算喷涂面积s,通过式7计算铝层厚度δ;c、实验测量并拟合火焰喷铝的铝层电阻r与铝层厚度δ的关系曲线,代入基础输入参数,通过式8计算确定铝层电阻r。较现有技术而言,本发明通过合理的参数筛选确定,能够避免一遍遍地进行火焰喷铝,逐个调节参数测试才能得到目标涂层电阻,能够精准确定电阻值,保障实际喷涂质量和喷涂效果。
[0068]
实施例2
[0069]
参见图1和图2,一种自动火焰铝喷涂电阻的标定方法,包括以下步骤:
[0070]
a、通过前期的工艺实验和数学推理,确定基础输入参数在送丝输入阶段、铝丝燃烧阶段和喷涂阶段的数学机理,建立数学模型;
[0071]
b、通过建立的数学模型,解出数学模型中的数学关系式和数学拟合关系式;设点火后喷涂时间为t,通过式1计算确定燃烧的铝丝长度l
s
;
[0072]
l
s
=v
s
·
t
ꢀꢀꢀ
式1
[0073]
其中,l
s
为燃烧的铝丝长度,v
s
为送丝速率,t为点火后喷涂时间;
[0074]
设铝丝直径为d,铝丝密度为ρ,通过式2计算确定燃烧的铝丝重量w
s
;
[0075][0076]
其中,w
s
为燃烧的铝丝重量,d为铝丝直径,l
s
为燃烧的铝丝长度,ρ为铝丝密度;
[0077]
经实验测定喷涂高度h和喷涂斜角θ,通过式3计算确定铝丝留存率η,确定喷涂斜角θ与铝丝留存率η之间的拟合关系曲线;
[0078]
η=f1(θ,h)
ꢀꢀꢀ
式3
[0079]
其中,η为铝丝留存率,θ为喷涂斜角,h为喷涂高度,f1为喷涂斜角与喷涂高度交互影响对铝丝留存率的映射关系;
[0080]
通过式4计算留存在零件表面的铝重量w
c
,设铝层的密度为ρ',通过式5计算留存在零件表面的铝体积为v
c
,通过式6计算喷涂面积s,通过式7计算铝层厚度δ;
[0081]
w
c
=w
s
·
η
ꢀꢀꢀꢀ
式4
[0082]
其中,w
c
为留存在零件表面的铝重量,w
s
为燃烧的铝丝重量,η为铝丝留存率;
[0083][0084]
其中,v
c
为留存在零件表面的铝体积,w
c
为留存在零件表面的铝重量,ρ'为铝层的密度;
[0085]
s=av
m
t
ꢀꢀꢀꢀ
式6
[0086]
其中,s为喷涂面积,a为轨迹间距,v
m
为移动速率,t为点火后喷涂时间;
[0087][0088]
其中,δ为铝层厚度,v
c
为留存在零件表面的铝体积,s为喷涂面积;
[0089]
c、实验测量并拟合火焰喷铝的铝层电阻r与铝层厚度δ的关系曲线,代入基础输入
参数,通过式8计算确定铝层电阻r;
[0090][0091]
其中,r为铝层电阻,f2为铝层厚度与铝层电阻之间的函数关系,δ为铝层厚度,d为铝丝直径,v
s
为送丝速率,ρ为铝丝密度,v
m
为移动速率,a为轨迹间距,ρ'为铝层的密度,f1为喷涂斜角与喷涂高度交互影响对铝丝留存率的映射关系,θ为喷涂斜角,h为喷涂高度。
[0092]
所述步骤a中,基础输入参数是指送丝速率v
s
、喷涂高度h、轨迹间距a、移动速率v
m
和喷涂斜角θ。
[0093]
实施例3
[0094]
参见图1和图2,一种自动火焰铝喷涂电阻的标定方法,包括以下步骤:
[0095]
a、通过前期的工艺实验和数学推理,确定基础输入参数在送丝输入阶段、铝丝燃烧阶段和喷涂阶段的数学机理,建立数学模型;
[0096]
b、通过建立的数学模型,解出数学模型中的数学关系式和数学拟合关系式;设点火后喷涂时间为t,通过式1计算确定燃烧的铝丝长度l
s
;
[0097]
l
s
=v
s
·
t
ꢀꢀꢀ
式1
[0098]
其中,l
s
为燃烧的铝丝长度,v
s
为送丝速率,t为点火后喷涂时间;
[0099]
设铝丝直径为d,铝丝密度为ρ,通过式2计算确定燃烧的铝丝重量w
s
;
[0100][0101]
其中,w
s
为燃烧的铝丝重量,d为铝丝直径,l
s
为燃烧的铝丝长度,ρ为铝丝密度;
[0102]
经实验测定喷涂高度h和喷涂斜角θ,通过式3计算确定铝丝留存率η,确定喷涂斜角θ与铝丝留存率η之间的拟合关系曲线;
[0103]
η=f1(θ,h)
ꢀꢀꢀ
式3
[0104]
其中,η为铝丝留存率,θ为喷涂斜角,h为喷涂高度,f1为喷涂斜角与喷涂高度交互影响对铝丝留存率的映射关系;
[0105]
通过式4计算留存在零件表面的铝重量w
c
,设铝层的密度为ρ',通过式5计算留存在零件表面的铝体积为v
c
,通过式6计算喷涂面积s,通过式7计算铝层厚度δ;
[0106]
w
c
=w
s
·
η
ꢀꢀꢀꢀ
式4
[0107]
其中,w
c
为留存在零件表面的铝重量,w
s
为燃烧的铝丝重量,η为铝丝留存率;
[0108][0109]
其中,v
c
为留存在零件表面的铝体积,w
c
为留存在零件表面的铝重量,ρ'为铝层的密度;
[0110]
s=av
m
t
ꢀꢀꢀꢀ
式6
[0111]
其中,s为喷涂面积,a为轨迹间距,v
m
为移动速率,t为点火后喷涂时间;
[0112][0113]
其中,δ为铝层厚度,v
c
为留存在零件表面的铝体积,s为喷涂面积;
[0114]
c、实验测量并拟合火焰喷铝的铝层电阻r与铝层厚度δ的关系曲线,代入基础输入
参数,通过式8计算确定铝层电阻r;
[0115][0116]
其中,r为铝层电阻,f2为铝层厚度与铝层电阻之间的函数关系,δ为铝层厚度,d为铝丝直径,v
s
为送丝速率,ρ为铝丝密度,v
m
为移动速率,a为轨迹间距,ρ'为铝层的密度,f1为喷涂斜角与喷涂高度交互影响对铝丝留存率的映射关系,θ为喷涂斜角,h为喷涂高度。
[0117]
所述步骤a中,基础输入参数是指送丝速率v
s
、喷涂高度h、轨迹间距a、移动速率v
m
和喷涂斜角θ。
[0118]
所述步骤b中,确定喷涂斜角θ与铝丝留存率η之间的拟合关系曲线具体是指映射关系在以喷涂高度h为x轴,喷涂斜角θ为y轴,铝丝留存率η为z轴的三维坐标系下拟合为三维曲面。
[0119]
实施例4
[0120]
参见图1和图2,一种自动火焰铝喷涂电阻的标定方法,包括以下步骤:
[0121]
a、通过前期的工艺实验和数学推理,确定基础输入参数在送丝输入阶段、铝丝燃烧阶段和喷涂阶段的数学机理,建立数学模型;
[0122]
b、通过建立的数学模型,解出数学模型中的数学关系式和数学拟合关系式;设点火后喷涂时间为t,通过式1计算确定燃烧的铝丝长度l
s
;
[0123]
l
s
=v
s
·
t
ꢀꢀꢀ
式1
[0124]
其中,l
s
为燃烧的铝丝长度,v
s
为送丝速率,t为点火后喷涂时间;
[0125]
设铝丝直径为d,铝丝密度为ρ,通过式2计算确定燃烧的铝丝重量w
s
;
[0126][0127]
其中,w
s
为燃烧的铝丝重量,d为铝丝直径,l
s
为燃烧的铝丝长度,ρ为铝丝密度;
[0128]
经实验测定喷涂高度h和喷涂斜角θ,通过式3计算确定铝丝留存率η,确定喷涂斜角θ与铝丝留存率η之间的拟合关系曲线;
[0129]
η=f1(θ,h)
ꢀꢀꢀ
式3
[0130]
其中,η为铝丝留存率,θ为喷涂斜角,h为喷涂高度,f1为喷涂斜角与喷涂高度交互影响对铝丝留存率的映射关系;
[0131]
通过式4计算留存在零件表面的铝重量w
c
,设铝层的密度为ρ',通过式5计算留存在零件表面的铝体积为v
c
,通过式6计算喷涂面积s,通过式7计算铝层厚度δ;
[0132]
w
c
=w
s
·
η
ꢀꢀꢀꢀ
式4
[0133]
其中,w
c
为留存在零件表面的铝重量,w
s
为燃烧的铝丝重量,η为铝丝留存率;
[0134][0135]
其中,v
c
为留存在零件表面的铝体积,w
c
为留存在零件表面的铝重量,ρ'为铝层的密度;
[0136]
s=av
m
t
ꢀꢀꢀꢀ
式6
[0137]
其中,s为喷涂面积,a为轨迹间距,v
m
为移动速率,t为点火后喷涂时间;
[0138][0139]
其中,δ为铝层厚度,v
c
为留存在零件表面的铝体积,s为喷涂面积;
[0140]
c、实验测量并拟合火焰喷铝的铝层电阻r与铝层厚度δ的关系曲线,代入基础输入参数,通过式8计算确定铝层电阻r;
[0141][0142]
其中,r为铝层电阻,f2为铝层厚度与铝层电阻之间的函数关系,δ为铝层厚度,d为铝丝直径,v
s
为送丝速率,ρ为铝丝密度,v
m
为移动速率,a为轨迹间距,ρ'为铝层的密度,f1为喷涂斜角与喷涂高度交互影响对铝丝留存率的映射关系,θ为喷涂斜角,h为喷涂高度。
[0143]
所述步骤a中,基础输入参数是指送丝速率v
s
、喷涂高度h、轨迹间距a、移动速率v
m
和喷涂斜角θ。
[0144]
所述步骤b中,确定喷涂斜角θ与铝丝留存率η之间的拟合关系曲线具体是指映射关系在以喷涂高度h为x轴,喷涂斜角θ为y轴,铝丝留存率η为z轴的三维坐标系下拟合为三维曲面。
[0145]
所述步骤c中,拟合火焰喷铝的铝层电阻r与铝层厚度δ的关系曲线具体是指将铝层厚度δ与铝层电阻r之间的函数关系拟合为反比例函数。
[0146]
步骤a中,基础输入参数是指送丝速率v
s
、喷涂高度h、轨迹间距a、移动速率v
m
和喷涂斜角θ,通过前期的工艺实验和数学推理,筛选确定得出的这五个基础参数,通过输入基础参数就能够计算得到涂层的理论电阻,进而为实际喷涂提供准确的数据支撑,整个过程简单、科学合理,且效率高。